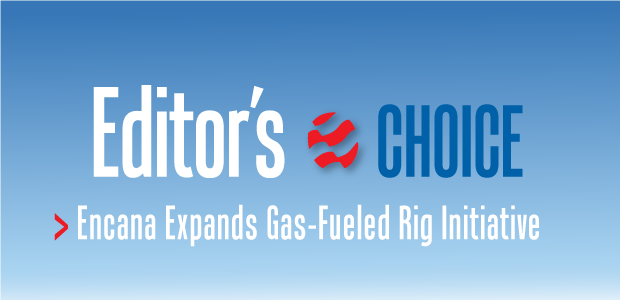
Natural Gas Rigs
Encana Initiative Underscores Environmental, Economic Benefits Of Powering Rigs On Natural Gas
By David Hill
DENVER–The North American natural gas industry is in search of an environmental and economic solution to address significant fuel use. Because natural gas has potential for widespread applications, it is critical that early adopters within the industry help trigger greater use.
With testing and improvements, growing infrastructure and industrywide collaboration regarding natural gas viability, powering rig operations with natural gas is becoming a reality for several operators–paralleling broader trends in the U.S. transportation sector and the growing movement to convert over-the-road trucks and fleet vehicles from diesel and gasoline to natural gas.
By using this engine technology to fuel drilling rigs, we have the opportunity to make an enormous impact on overall fuel consumption across the United States and on a global level. Encana tested its first natural gas-powered rig in the United States in 2005. With the success of that initial test, we have expanded our portfolio, both in the United States and Canada, with 16 natural gas-powered rigs running this summer in Encana’s field operating areas. Two additional gas-fired rigs are planned by year’s end.
There are two main types of engine technology used to implement natural gas into our operations. Among the natural gas-powered rigs Encana is operating, six use dual-fuel technology and 10 have dedicated natural gas engines. The source or type of natural gas used as a fuel also varies. Twelve of the rigs use field gas produced from the fields in which they are drilling. Four use liquefied natural gas because of limited natural gas distribution availability in the field, or the need to supply fuel that is highly mobile because of frequent rig moves or short drilling cycles. LNG offers the ability to move rigs outside of an area that is using field gas and provides a high-quality and reliable source of fuel.
With each technology and fuel type, we are working with other operators and evaluating our sites to address operational challenges and increase efficiencies.
Significant Benefits
The most significant benefit to substituting natural gas for conventional diesel is the impact on our environmental footprint. Not only are we seeing improvements to regional air quality, but a significant reduction in carbon dioxide, volatile organic compounds and nitrogen oxide emissions (Figure 1). An Encana rig tested in the Jonah Field in Wyoming over four years showed a reduction of more than 4,000 tons of VOC and 600 tons of NOx emissions per year, even with increased drilling activity. Additionally, natural gas engines run quieter than their diesel counterparts, are less visually polluting and are odorless.
It is also economically beneficial, turning rig fuel into revenue, which we hope will promote rapid expansion in operations industrywide. At a much lower cost than diesel, natural gas-powered rigs are lowering transportation and refining costs, particularly in the case of field gas where the natural gas rig fuel is utilized from the wellhead and omits the need to transport fuel to the rig site.
There are some challenges that we are working to overcome. Depending on the region, the availability of natural gas supply and its quality and content can be variable, and as with any new technology, unfamiliarity with natural gas engines and engine maintenance can be a problem, including higher engine costs than for conventional diesel on a horsepower basis, potential power loss and durability (this is more of an issue since natural gas requires spark ignition versus compression ignition with diesel engines). Dedicated natural gas engines also experience a slower response under variable loads, can be more temperamental, and are associated with higher maintenance costs.
Even with these obstacles, however, Encana sees the benefits as outweighing the costs.
Two Engine Types
While dedicated natural gas engines use only one fuel system and require spark ignition for combustion, dual-fuel engines incorporate two independent fuel systems–one natural gas and the other diesel–and run on both fuels simultaneously. The engine, which requires compression ignition for combustion, can run on diesel alone if needed. This technology can be applied on most engines.
Currently, engine manufacturers do not have dual-fuel engine solutions for the engine types used in drilling operations, so the conversions are done with aftermarket companies that offer dual-fuel systems. Because the system is installed aftermarket, the engine manufacturer warranty should be reviewed for any implications.
Depending on the natural gas source used and diesel substitution, dual-fuel systems save more than 660 gallons of diesel fuel a day, reduce CO2 and NOx emissions up to 10 percent compared with diesel, and reduce operating costs by $600,000 a year. This translates to a fuel savings of $500-$1,500 a day per dual-fuel rig, with savings varying according to the natural gas fuel source, the price of diesel and the diesel substitution rate. Dual-fuel systems also offer flexibility when challenged with inconsistent natural gas availability. Similar to dedicated natural gas engines, dual-fuel systems can utilize field gas, compressed natural gas delivered to location in tube trailers, or LNG delivered to location and vaporized prior to introduction into the fuel system on the engine.
A challenge faced when using dual-fuel is that retrofits are unable to maximize substitution and handle high transient loading commonly found on rigs. “Stray” gas in the engine, caused by block unloading, creates instability. Also, the maximum substitution rate is about 70 percent for natural gas, but only with the fuel at its highest quality and at high stable load conditions on the engine. As the methane percentage in the natural gas decreases, the substitution rate is limited.
While cost savings are not as high as other technologies and the integrity of the gas has been an issue, the important distinction with dual-fuel systems is the flexibility to use both natural gas and diesel–a critical component in instances where natural gas supply is inconsistent.
At present, dedicated natural gas engines are being used on drilling rigs with electric drives. Diesel-electric generator sets are replaced with natural gas as part of a new rig build or as a retrofit on a rig that is fully operational. Since natural gas is the primary fuel, field gas, LNG or CNG must be delivered to the site.
Switching from diesel to natural gas engines presents challenges. There is a power loss resulting from efficiency reduction when going from compression ignition (diesel) to spark ignition (natural gas), which can require larger engine sizes to obtain equivalent horsepower. Dedicated natural gas engines have a slower torque response that requires rig crew training. Gas quality also can inhibit efficiency, and field gas must be free of all liquids, requiring some processing and dew point control.
The benefits of using dedicated natural gas engines over diesel are significant. Engine emissions (NOx, sulfur oxides, VOCs, carbon monoxide, particulate matter and CO2) are reduced. Dedicated natural gas engines can meet 2010 U.S. Environmental Protection Agency emission requirements for on-road engines with less after-combustion treatment than diesel engines. By reducing traffic, we also see reduced road wear and tear, and reductions in dust, mud tracking on hard-top roads, noise and light pollution. Dedicated natural gas engines provide maximum displacement of diesel, allowing maximum fuel savings.
Field Gas
Field gas can be implemented in two ways: wellhead or raw field gas, which typically is gathered from in-field gathering lines and piped to location, requiring limited treating; or plant tailgate (treated) gas, brought from the gas plant and piped back to location or supplied by gas lift lines, and requiring no treating.
The greatest benefit to field gas is cost. Comparing natural gas with diesel for an Encana rig in the Jonah Field that uses conditioned wellhead gas with backup diesel costs, hookup and fuel gas unit costs, the natural gas rig costs $26,710 per well, saving $115,040 in fuel costs on every well drilled compared with the diesel-powered rig. The savings can be significant when multiplied over multiwell programs and a multiyear deployment of a rig in a field.
After initially testing mobile LNG technology in the Haynesville Shale, Encana is implementing the system to fuel gas-fired rigs in other operating areas. LNG is purer, cleaner and maintains more consistent quality than unprocessed field gas. It is not explosive or flammable in its liquid state, and because it is vaporized, LNG is highly mobile and requires no natural gas infrastructure. LNG is more expensive than field gas because of liquefaction, transportation and regasification costs, but Encana is averaging $500-$1,000 a day in fuel cost savings with LNG compared with diesel engine rigs.
While Encana has realized tremendous fuel benefits from field gas, less refining and a reduction in truck trips, we have experienced issues that we are working to address to increase performance. Initially, we saw a high frequency of “blackouts,” with rig crews unaccustomed to the torque response. In addition, the effect of elevation is greater, resulting in a higher “deration” factor (14 percent versus 6 percent) with a rig located at an altitude of 7,200 feet. Tuning the engines to help achieve higher power also gave us spikes in NOx numbers, an inconsistent fuel supply from our central distribution point (leading to pressure and volume issues), and a higher-than-anticipated amount of backup diesel burned.
Changes to natural gas delivery and our quick-move design for vertical wells have caused additional gas consistency and reliability challenges. The initial delivery design produced large temperature swings, resulting in a liquid knockout, slugging of engines with condensate, freezing issues with delivery lines, and general inconsistencies in fuel delivery.
Encana has addressed some of these issues with early field gas testing. Load bank installation on generators has helped moderate load swings and has allowed us retune our engines. We also are obtaining gas samples from different central distribution points to help tune engines accurately. Finally, we developed a system to educate crews to operate the rig effectively.
To solve delivery issues, we have created a dedicated fuel gas team responsible for the initial setup of our fuel lines and desiccant system (designed to condition gas), troubleshooting problems during drilling, and performing routine blow-downs of our lines. We also increased the size of delivery lines to two to three inches, which has limited pressure drop at the engine regulators.
Going forward, we plan to eliminate the three lines to location concept (fuel gas, hydraulic fracturing and sales lines) in the Jonah Field, implement a robust fuel gas delivery conditioning system that is engineered for wider use, and expand technologies to other fields.
Liquefied Natural Gas
LNG, liquefied through refrigeration (-260 degrees Fahrenheit), is stored as liquid in insulated vessels and transported to the site. The LNG is vaporized on site with a LNG fuel handling system and is delivered to the engine in a gas state at approximately 60 degrees F. This unique application of technology, initially tested by Encana in the Haynesville Shale for five months and representing the first such test of its kind, has been successful and is now being implemented elsewhere.
LNG is purer, cleaner and maintains a more consistent quality (97-98 percent methane), performing better in engines than field gas. In addition, LNG implementation requires no natural gas infrastructure, and because it is vaporized, it is highly mobile, giving us the ability to use it in most locations.
Another key benefit is safety. Since LNG is not stored under pressure, it is not explosive or flammable in its liquid state; it disperses and evaporates quickly, and therefore, cannot “spill.” Also, additional safeguards can be added to an interface, including a methane detector and instrumentation that shuts down the system if a flame is detected.
Encana is running 16 natural gas-powered drilling rigs in its U.S. and Canadian field operations, and plans to add two more gas-fired rigs by the end of the year. Six of the rigs have dual-fuel engines and 10 have dedicated natural gas engines, such as the Caterpillar engine shown here. Powering rigs with field gas or LNG provides both cost savings and environmental benefits, with dedicated natural gas engines saving 1,500 gallons of diesel fuel a day, reducing CO2 and NOx emissions up to 20 percent, and reducing operating costs by up to $2,000 a day.
One challenge is the risk of fuel depletion on site. We work closely with our teams to set delivery schedules to help manage this. LNG also requires more labor and equipment costs, which Encana has helped limit with an automated interface for the driver to use on location, so that the pressure no longer has to be controlled manually. Finally, there is a loss associated with transfer to the gas phase as a result of the pressure requirement for transfer.
Tests in extreme weather have shown that this system performs in extreme cold, but it is important to monitor issues specific to high humidity and low temperature. Significant ice buildup on vaporizer coils can reduce the efficiency of LNG transfer to the vapor phase, and needs to be monitored.
As with dual-fuel technology and field gas, LNG continues to produce significant cost savings. LNG has higher cost than field gas because of liquefaction, transportation and the LNG regasification system required on site. The largest fuel cost savings will be in dedicated natural gas engine applications that completely eliminate diesel use. Today, we are experiencing savings of $500-$1,000 a day. The variability is caused by daily fuel use, cost of LNG delivered to location, and the price of diesel in the area. Cost savings can be higher with LNG sources located close to drilling operations.
Promising Future
The cost savings and positive environmental impacts that Encana and other early adopters are experiencing have been significant, with dedicated natural gas engines saving in excess of 1,500 gallons of diesel fuel a day, reducing CO2 and NOx emissions up to 20 percent, and reducing operating costs from $500 to more than $2,000 a day in some locations. Dual-fuel engines also look promising in terms of cost and environmental impact, while providing flexibility during operation. The fact that operators are recording similar cost savings and fuel use is promising.
Extensive use of natural gas in our operations builds additional domestic energy security and has implications for rail, mining, military, construction services, freight transportation, airport and port authorities, and more. Light-duty uses within the transportation sector (personal vehicles, municipal level, etc.) present the largest opportunity, while medium- and heavy-duty uses (freight and goods transportation, rail, mining, military and construction) are the most commercially ready.
At a summit hosted by America’s Natural Gas Alliance and member operators, participants discussed the next steps for collaborative evolution. Our immediate challenges are a lack of familiarity and convincing rig contractors to make the investment in gas-fired engines. We need to identify strategies to overcome these challenges, convert existing rigs and implement natural gas engines on new rigs, as well as build new LNG plants and expand infrastructure to make natural gas a reliable fuel source for North America’s rig fleet.
If early adopters can collaborate and bring others along, best practices can continue to be established that will have a significant impact on overall fuel consumption.
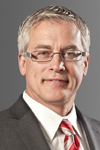
DAVID HILL is vice president, natural gas economy operations, at Encana, responsible for working both internally and externally to increase the use of natural gas in the power generation and transportation sectors through advocacy, strategic partnerships and building infrastructure to enable market development and acceptance. He is also the Colorado Natural Gas Vehicle Drive Project champion at the company. Hill has 25 years of industry experience. He joined Encana in 2002, and previously served as team lead for the Denver-Julesburg, Paradox and West Texas basins. Before joining Encana, Hill was president of TICORA Geosciences, and prior to that, served for 11 years in various management positions at the Gas Technology Institute, including working in GTI’s gas shale, coalbed methane and tight gas sand programs. He started his career as a field engineer at Halliburton Energy Services. Hill holds a B.S. in petroleum engineering from Marietta College and an M.B.A. from Northwestern University.
For other great articles about exploration, drilling, completions and production, subscribe to The American Oil & Gas Reporter and bookmark www.aogr.com.