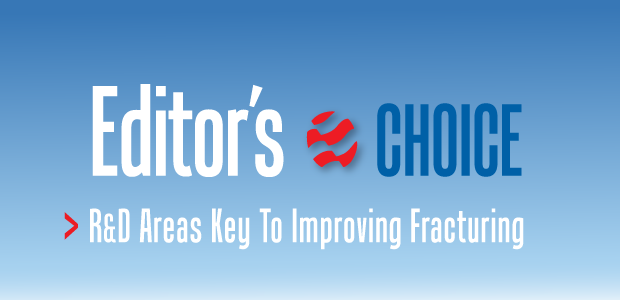
Natural Gas White Papers
R&D Areas Key To Improving Fracturing
By Guy Lewis and Kent Perry
DES PLAINES, IL.–Along with horizontal drilling, enhanced 3-D seismic imaging and other technological advancements, the hydraulic fracturing of gas shale and tight gas sands have transformed the U.S. energy picture and hold the potential to have a similar impact globally.
In ultralow-permeability shale and tight sand reservoirs, hydraulic fracturing is critical to creating permeability to enable commercial flow rates. Since the first commercial use of the technology in 1947, it has been used in more than 1 million wells and has helped to produce more than 600 trillion cubic feet of natural gas and 7 billion barrels of oil. The payoff to developing hydraulic fracturing advances has been extraordinary in bringing new life to old wells and unlocking the potential of oil and gas resources from reservoirs with low permeability.
Today’s research focuses on continuing to fine-tune the approach with more precise sizing and placement through multistage fracturing. Improvements will enable further reductions in the environmental footprint and enhanced productivity per application. While different well sites require different mixes of frac fluids depending on the composition of the rock bed and other factors, almost all mixtures are comprised of more than 95 percent water.
Environmental Footprint
Many concerns have been raised associated with the environmental footprint of hydraulic fracturing. In part, this is the result of significant activity taking place in populated areas that have little experience with natural gas exploration, drilling and production. The vast majority of applications are performed without incident, but good news is not news. For the most part, hydraulic fracturing is an invisible process with high visibility put on certain activities that support it.
These include water delivery trucks (50 or more per well) that bring traffic, noise, dust and local water requirements. Produced water handling then requires lined pits, disposal trucks, “chemical handling,” and on-site treatment/recycling, and all of these activities provide the potential for spills. The potential is there for environmental impact and the industry is becoming increasingly proactive in reaching out to affected communities. Part of the challenge is that several potential concerns get combined under the heading of “hydraulic fracturing.” These include the volume of water required, the potential for groundwater contamination, and the potential for spills of water at the surface. The solution for the industry is doing good science and providing transparency to fracturing activities, both of which the industry is actively engaged in.
Beyond the environmental issues, more research and development will enable the effectiveness of hydraulic fracturing to improve. Today, it is an expensive process with only 50 percent of fractured stages reaching their full potential based on logs. Causes of nonproductive fracture stages include inadequate design, wrong proppant loadings, poor fluid selection, proppant embedment, poor fracture fluid cleanup, water blockage of permeability, and poorly understood reservoir compartmentalization.
Much progress has been made to date, but opportunities remain to improve the effectiveness of fracturing through improved diagnostics, leading to improved fracture design, better understanding of fracture fluid migration, optimizing proppant loadings, ensuring the right fluids are used, considering alternatives to hydraulic fracturing, risk modeling to quantify potential negative impacts, and improving rock mechanics models for assessing impacts of well construction and completion techniques.
Technological Evolution
Today, the evolution of lateral and horizontal drilling technology is beginning to allow the development of unconventional resources through the placement of smaller well bores into exactly the area and location required for optimum production. Figure 1 illustrates the evolution of the technology over the past four decades, with horizontal drilling and multistage fracturing combining to allow operators to stimulate substantially more reservoir volume yet achieve ever-more precise placement and treatment size.
In order to continue this trend in efficiency, a large portion of the formation containing the hydrocarbons has to be exposed to the well bore and stimulated to enhance permeability. This can only be achieved if the well bore follows the bedding plane of the formation for long distances, which requires long-lateral horizontal wells completed in multiple stages along the entire length of the lateral.
The effectiveness of horizontal wells can be directly measured by production performance, which is dependent on well spacing, lateral length and orientation of the lateral well bore relative to the minimum in situ stress of the formation. Optimal spacing of horizontal wells will enable maximum recovery of hydrocarbons between two wells and reduce the hydrocarbons left behind to be recovered by future infill wells. The horizontal well bore must be positioned in such a way that when fracturing operations are performed, the hydraulic fractures emanating from the well bore create a network of hydraulically induced fractures coupled with natural fractures, thus enhancing production.
Transverse Fractures
A horizontal well bore positioned normal to the maximum in situ stress provides the most complex network of hydraulic fractures (as shown in Figure 2), because it promotes a series of transverse fractures along the horizontal lateral. The complex fracture network increases the effective permeability of the reservoir, thereby enhancing production.
Post-fracture stimulation diagnostics are used to determine the overall position of induced hydraulic fractures and to ascertain the amount of the reservoir that was stimulated, or the stimulated reservoir volume (SRV), as shown in Figures 3A and 3B. Technologies that enable the determination of one or both of these parameters include net pressure matching, tiltmeter mapping, bore hole microseismic, temperature, chemical and radioactive tracer surveys.
Net pressure matching was refined in vertical well bores with single fracture treatments and provides insight into the geometry of the created fracture by matching the pressure response. In order for net pressure matching to be reliable, geomechanical reservoir properties have to be accurately modeled in a fracture simulator. Tiltmeter surveys utilize tiltmeters positioned either in the well bore or on the surface and measure the shift of the rock induced by hydraulic fractures. This technology is best for determining fracture azimuth. Additionally, depending on the location of the tools, fracture height and length can be inferred.
Bore hole microseismic surveys utilize an array of geophones positioned in an offset well near the stimulated well. The geophones record microseismic signals (compressional and shear wave arrivals) generated by the propagation of the hydraulic fractures. This technology can measure the spatial and temporal changes of hydraulic fractures. Determining the position of the microseismic source greatly depends on the accuracy of the velocity model used to describe the rock strata through which the signal propagates. Various methods are used to generate the velocity model, including seismic profile surveys, acoustic logs and check shots.
In addition to enhanced diagnostic technologies, the capability to detect sweet spots in real time while drilling is under development. Combined with fracture steering and orientation control, there is the promise of a future where drilling and completion technologies can be optimized to match the characteristics of a reservoir and tailor the approach to the specific circumstance.
Great Strides
Operators also continue to make great strides to manage environmental challenges. One of the most important emerging developments has been the practice of reusing the flow-back water from one well for part of the volume required for the next well’s hydraulic fracturing effort. Typically, about 25 percent of the water injected flows back over the first few weeks after hydraulic fracturing and the well is turned to production. As a result, this reuse reduces the potential for environmental impact, reduces ton-miles required in water transportation, decreases air emissions, decreases carbon footprint, lowers truck traffic densities, reduces road wear and generally leads to greater stakeholder acceptance.
Even in the best case scenario, fracturing support is still transportation-intensive, with the 1 million gallons of water flowing back from one well requiring more than 200 truckloads and four times that typically needed in total for the next well.
In addition to reuse of the flow-back water, operators sometimes dispose of flow back and produced water by deep well injection at Class II wells, but this option only is available in regions where the geology is suitable for deep injection and the wells have been drilled. Reintroducing the water from hydraulic fracturing into surface or ground water can be environmentally safe if the water is sufficiently treated, but these treatment technologies can be very expensive. Developments continue within the industry to reduce the cost of these treatment technologies.
In the meantime, some water treatment is important for reuse to protect equipment and the shale formation from damage. This portfolio of options allows operators to be flexible and allow for the freshwater requirements for shale gas development to be minimized. More research is required to quantify the impact of varying water quality on formation quality.
Fracturing fluid migration into freshwater aquifers has not been observed. Although it is not demonstrated that fractures can reach fresh groundwater, there is the potential for spills at the surface and leaks and ruptures in surface casing if cementing jobs are not performed properly. As a result, it is important to understand what is put into fracturing fluids and promote sustainable operating practices that minimize the risk of surface contamination. Strides have been made to develop more environmentally benign fracturing fluids and alternatives to the use of water in enhancing permeability, and this is another area of ongoing research efforts.
Future Research Areas
Hydraulic fracturing has evolved from the performance of a single treatment in a vertical well to multiple treatments in a horizontal well. The technology to adequately characterize and evaluate the hydraulic fracturing process has been eclipsed by the ability to drill the horizontal well and pump the fracture treatments. A collaborative industry project to conduct field research experiments on the hydraulic fracturing process would enhance the understanding of the dimensions and productivity of hydraulically created fractures in long horizontal well completions aiming to develop improved procedures that will be reflected in better well productivity.
Additional research that should be performed includes novel ideas for creating permeability beyond the hydraulic fracturing process, such as explosives, cryogenic fluids and novel heating techniques. The potential for improvement is large enough to set goals of future research such as:
- Developing the technology and techniques to increase horizontal well performance by up to 100 percent. The benefits could include adding 500 million cubic feet of reserves (across 1,000 wells), increasing revenue up to $2 billion even at a U.S. gas price of $4.00 an MMBtu, and reducing the environmental footprint by 50 percent because of increased productivity.
- Mitigating air, land and water environmental issues associated with well drilling and completion. Multipad drilling will minimize surface footprint. Reducing fugitive methane emissions and converting field fleets to operate on natural gas will reduce greenhouse gas emissions. Further enhancements to produced and flow-back water treatment technology and developing alternatives to using water will reduce net water consumption.
While theoretical and modeling efforts have advanced significantly, the needed next step is to conduct comprehensive and transparent field experiments to verify new theories to explain the productivity responses from multiple and modified treatments in horizontal well bore geometries. A carefully planned field-based research experiment similar to what the industry has conducted in past years is overdue. A comprehensive research experiment could lead to significantly improved hydraulic fracturing efficiencies. The set of research topics might include:
- Drilling, logging, coring and well completions;
- Sidetracking and coring through the fracture domain;
- Fracture injection operations;
- Direct observation of induced fractures and cuttings in core;
- Injection of radioactive solid and fluid tracers/spectral gamma ray logging;
- Bore hole imaging using formation micro imager (FMI) tools;
- Downhole hydraulic fracturing seismic characterization and ground truth as to the true meaning of signals received;
- Surface seismic evaluations;
- Hydraulic fracturing seismic model verification and calibration (including directly measuring the exact time of the seismic signals reaching observation wells, and how those measurements compare to modeled predictions);
- The effectiveness of downhole perforating techniques;
- Evaluating directional changes in hydraulically induced fractures (e.g., where does the fracture intercept observation wells versus the initiation point?);
- Evaluating fracturing fluid and proppant placement;
- Assessing the created conductivity as measured with flow between two wells connected by a hydraulic fracture;
- Evaluating flow effectiveness and stimulated reservoir volumes; and
- Conducting formation evaluation experiments to determine optimum well log suites.
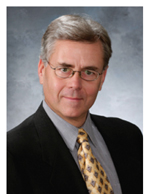
GUY LEWIS is executive director for strategic growth initiatives at the Gas Technology Institute, responsible for developing new growth opportunities for GTI and developing key strategic global relationships. Previously, Lewis was responsible for GTI’s unconventional gas technology development and collaborative research and development programs. He has extensive experience in strategic planning, performance management and operational leadership in the energy industry, with a proven track record of developing and implementing innovative strategies and leading transformation initiatives. Before joining GTI, Lewis held leadership positions at BP and Amoco. He serves on the board of directors of the Research Partnership to Secure Energy for America (RPSEA) and is president of the GTI Catoosa test drilling facility in Tulsa. Lewis holds a degree in chemical engineering from Northwestern University and an M.B.A. from the University of Chicago.
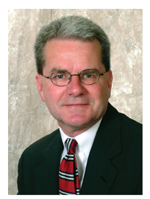
KENT PERRY is director, exploration and production research, at the Gas Technology Institute in Des Plaines, Il. At GTI, he has responsibility for planning and managing a research program for recovering unconventional natural gas in the United States. He also serves as team leader, unconventional gas, for RPSEA. Perry’s experience includes 30 years of natural gas engineering and gas production responsibilities, including gas storage engineering for Northern Illinois Gas Co., production engineering with Kansas-Nebraska Natural Gas Co., and exploration and production for Michigan Energy Resources Co. He is a past Society of Petroleum Engineers’ distinguished lecturer on tight gas sands, and has participated in National Petroleum Council studies on domestic natural gas potential. Perry holds a B.S. in petroleum engineering from Colorado School of Mines.
For other great articles about exploration, drilling, completions and production, subscribe to The American Oil & Gas Reporter and bookmark www.aogr.com.