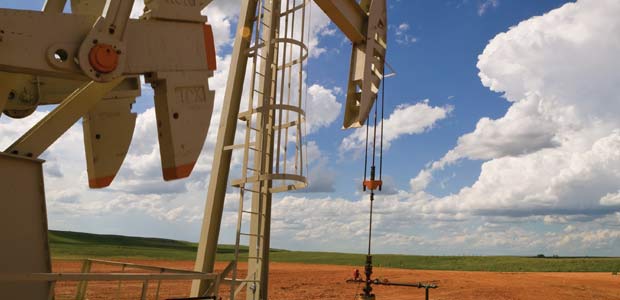
Advanced Technologies Optimize Artificial Lift, Production Operations
By Brian Dickson
PLANO, TX.–The main value proposition of production automation traditionally has been the ability to monitor artificial lift, separation, compression and other well site processes to streamline efficiencies and avoid unnecessary downtime. That is changing, however, with advances in hardware and software. The value-adding drivers behind automation are evolving rapidly from keeping individual wells and equipment on line to optimizing the operation of entire fields and maximizing the performance of the reservoir over its complete life cycle.
More than 95 percent of all U.S. oil wells require some form of artificial lift from the start of production, whether beam/sucker rod pumps, gas lift, plunger lift, electric submersible pumps, progressing cavity pumps, or subsurface hydraulic pumps. Increasing numbers of natural gas wells also are being equipped with various forms of artificial lift systems to produce liquids-rich gas and deliquify waterlogged formations.
Moreover, the proliferation of enhanced recovery projects and heavy oil production is creating new challenges when it comes to understanding the complex behavior of reservoirs subjected to water, steam or carbon dioxide injection, and determining how to optimize injection and production processes to optimize recovery.
While monitoring production processes such as artificial lift and injection certainly is not new, the ability to analyze flow measurements, operational data and other parameters in real time to continually optimize performance at the field- and reservoir-scale is a major step forward that can introduce game-changing capabilities for producers.
Optimizing even a relatively simple form of artificial lift such as plunger lift can be difficult. Installing plunger lift is usually the first solution for gas wells that are beginning to make water to prevent gas flow from being choked off. Removing water lowers bottom-hole pressure and increases production and reserves recovery. But every time the plunger cycles, it essentially shuts the well in and stops production. If the time between plunger cycles can be doubled from, say, six to 12 hours, it can make a material impact on well economics.
Multiply the economic benefits over multiple wells in a field and the results can be dramatic. Of course, determining each well’s optimal run time between plunger cycles requires having the necessary information on which to base the decisions and compare alternatives.
More complex artificial lift systems require more complex analytical capabilities. In one U.S. oil field, an operator was struggling with gas locking in ESPs. To avoid gas lock, the company intentionally undersized the pumps, but it was far from an ideal solution because it meant the wells were underproducing. By equipping the wells with real-time measurement technology and modeling the data to optimize performance, the operator was able to adjust pump operations to avoid gas locking while boosting production without having to change the pumps.
Creating Value
Optimization’s potential value increases proportionately with increasing operational scope and complexity–whether dealing with large numbers of wells, multiphase production flows, or both. Consider gas lift (Figure 1), the second most common form of artificial lift in the United States behind sucker rod pumping. To optimize production, the producer has to accurately measure how much gas is being injected into each well and how much is being produced.
With gas lift, the first challenge is lifting off the formation to get production started. The challenge then becomes determining the amount of lift agent that needs to be injected to maintain optimum production rates. The third challenge is measuring and allocating production, which is complicated by multiphase flow. Anytime a lift agent is used, it generally means a two-phase flow, often with fluids and gases in different phases.
Whether an oil well with associated gas, or a gas well that is producing condensate or water, production is rarely ever 100 percent gas or 100 percent liquid. It is comparatively simple to handle a production stream that is in an all-gas or all-liquid phase. Unfortunately, probably 90 percent of all oil and gas wells have multiphase production that makes optimizing measurement and artificial lift much more complicated.
The traditional method of measuring multiphase flows uses a test separator to periodically sample each well to get 24-hour average liquid and gas rates. Depending on how many wells are in a field, each producing well may be tested only once a month. Essentially, if a field has 40 wells, 39 are producing to the field’s production separator and one is producing to the test separator at any given time.
The problem is that the operator simply cannot make sound reservoir management decisions based on sparse test measurements averaged over 24 hours at a sampling interval of three to four weeks. Such data cannot tell the operator whether a well is liquid loading or gas locking at any particular point in the production cycle. Furthermore, once a test separator is introduced, it puts a huge filter at the front end of being able to allocate and measure production to know how much each well is contributing.
An alternative solution is to use meters that continuously measure both injection and production in real time. In a gas lift operation, for example, a vortex meter can measure and control the amount of lift agent injected, while a multiphase digital Coriolis meter can measure the two-phase production. An order-of-magnitude improvement over orifice plates and other conventional measurement devices, vortex meters can tolerate high pressures and have huge turndowns to accurately measure both very low rates as a well is being lifted off and very high rates as it reaches full production. Figure 2 shows vortex flow meters mounted on skids for use in gas lift operations.
While Coriolis meters historically have performed poorly in conditions that combine gas and liquid masses, the latest generation of digital Coriolis meters incorporates new signal processing techniques that accurately measure mass flow and density in two-phase environments. Figure 3 shows a Coriolis meter deployed to measure a two-phase flow in a CO2 flood to enhance oil recovery and improve reservoir pressure management. With multiphase data acquired continuously on each well, field operations staff can see what is happening minute by minute to accurately allocate production and optimize performance fieldwide.
Full-Field Optimization
Imagine a field with 50 wells on artificial lift. How can the operator optimally produce all the wells when they are interrelated and interact? Making a change to optimize the performance of one well might negatively impact the performance of others. The only way to understand the interaction between wells and optimize full-field performance is to have the right data along with the right analytical tools.
A key piece of the optimization puzzle is powerful new modeling software based on integrating nonlinear sequential quadratic programming algorithms with comprehensive multiphase flow simulators. With this technology, operators can analyze field performance and quickly run multiple “what if” modeling scenarios on individual wells to determine how changes could impact other points in the network of wells.
Applications include designing surface facilities in production networks, integrating reservoir simulators and full-field simulation, field matching with model parameters, allocating lift gas, designing pipelines and compressor/pump installations, and field planning.
By delineating the optimum allocation of injection rates to maximize production in the network and determining the optimum size and location of pumping and compression facilities, the technology maximizes fieldwide production, optimizes capital expenditures over the economic life of an asset, minimizes daily operating costs, and provides integrated reservoir and surface modeling/simulation.
The last point is significant. The same information used to optimize production can be applied to reservoir engineering to make business decisions such as where to drill the next well or what completion method is most effective. To make good reservoir decisions, engineers need good data to understand subsurface conditions and determine what steps to take to better manage the reservoir. Getting production data in real time is fundamental to optimizing production, but it is also a huge benefit to reservoir engineers, who can use the information to see how the overall reservoir is performing. And, of course, from the corporate perspective, optimizing production and reservoir management is directly related to share value.
IT Backbone
A comprehensive optimization solution includes hardware components such as vortex and Coriolis meters, remote terminal units, supervisory control and data acquisition systems, etc. But the information technology backbone for optimization functionality is software that monitors, manages and enhances the performance of wells and fields, and shows real-time production data at a glance on a single computer screen. Designed as a single-point tool to measure the operations of producing assets, the technology helps operators maximize performance by integrating real-time information from hardware and software networks to improve the overall productivity of their operations.
Advanced software packages not only provide reports, alarms, call-outs, data storage and process data management on wells and fields, but they support higher-order management capabilities that look deep into the operation of each well to extract detailed production information that can be used to identify underperforming assets and optimize each asset in the network. Any process variable–flow rate, pressure, volume, etc.–can be measured and analyzed to identify assets that are performing below expectations.
State-of-the-art human/machine interfacing (HMI) solutions are an important enabling feature. Once a production company has drilled a well, it needs to move quickly to complete it and get the production on line. Because the applications are data driven with fully automatic mapping, users can easily configure assets, wells, operator responsibilities and other data, saving engineering and programming costs. Operators can quickly add hundreds of wells at a time to the configuration, and the solution contains proven templates to integrate real-time automation and information systems as well as SCADA hardware. This is particularly valuable for older fields that have multiple generations of automation equipment.
So instead of requiring 60 man-hours to set up an individual well with the type of artificial lift, RTU and SCADA equipment, the user can configure a well in only an hour or two on a single configuration page. For companies with lots of wells or “manufacturing mode” plays such as shales, the ability to quickly put the field management/optimization HMI on top of the automation capabilities for each new well or piece of equipment as it is added is critical.
As shown in Figure 4, the specific needs of field operations are met by SCADA, reporting, configuration and system health features provided by advanced software packages with state-of-the-art interfacing solutions.
With all the pieces in place, the producer can begin to optimize operations by taking advantage of real-time, continuous production and allocation data from all wells in a field. Systems can include thousands of wells, with all the information delivered to central control and reporting systems as well as reservoir management systems.
In addition to optimizing production and reservoir performance, the information captured by these systems provides the framework to enhance business value. A company can assess such issues as energy consumption and maintenance expenditures to see where it is allocating limited capital and personnel resources versus where it should be allocating them to achieve the highest return.
The benefits of optimization resonate differently within different departments in an organization, but the “magic” is in exposing real-time information to professionals who never before have had access to it. As mentioned, giving reservoir engineers real-time production information gives them powerful new decision-making tools that can have a dramatic impact on drilling and development programs. On the other hand, managers focused on the bottom line will appreciate the business value of optimization. They now have the information to assess production performance and manage costs.
It is worth noting that focusing only on maximizing production will not necessarily make the most money. Neither will focusing only on cutting energy or maintenance/materials costs. Optimizing all these variables at the same time, however, can greatly enhance economics. It sounds simple, but it is very difficult to attain in a production operation, given all the dynamic variables.
Modeling And Simulation
Innovations around how the information acquired by automation and field management systems is used are driving the step change in automation capabilities. Optimizing an individual well is much more complicated than merely ramping up production and involves numerous variables. And again, because each well is interconnected to a larger network within the field, any change to one well can influence the behavior of other wells. That is where modeling and simulation come in.
The modeling software capabilities used in conjunction with real-time optimization allow the user to see in the virtual world what would happen across a field if a given parameter–say, increasing pumping frequency–at one well was changed. By modeling the various outcomes at different points in the field, the user quickly can evaluate available options and determine what changes to which wells would optimize production from the network of wells. It could take months or even years, and would be cost-prohibitive to run all the various permutations in the field and analyze the feedback. In fact, by the time that task was completed, the field’s production profile would have changed completely.
These kinds of optimization tools go far beyond managing physical assets and controlling costs. Adding real-time data measurement and analysis capabilities to automation moves a production operation up the value chain by giving operators the ability to continually optimize field and reservoir performance. Layering modeling/simulation and other value-adding capabilities on top of it generates even more incremental return on the investment.
For example, the latest optimization software technologies provide the tools to improve human resource functions. Many companies have a few key individuals with the experience and technical proficiencies to understand how to optimize producing wells. With the right software, such “pockets of excellence” can be distributed across the organization by identifying and capturing best practices, and by developing training methods using summaries and comparisons that can be organized by area, team, artificial lift type and custom group.
These types of knowledge capture efforts are taking place in shale plays across the country as companies search for the optimal ways to develop and produce fields. Optimization is only beginning in many shales because the wells are so new. However, even in emerging plays, real-time production information is proving invaluable to reservoir management by helping identify best practices, guide drilling decisions, and generally get the most bang for the investment buck. In shale plays, whoever can produce the most gas or oil the quickest, wins. The key is getting information to the right people to plan the next phase of field development.
Large numbers of wells and high depletion rates with rapidly changing production profiles also are major factors in shale plays. In addition to deciding where to drill or how to complete and produce wells, real-time production data can help companies manage equipment inventories in the field. For instance, managers may decide to keep a specific well on line that has depleted to 20-25 percent of its original production output, or they may choose to redeploy that well’s production equipment to a new well making much higher rates.
Compression And EOR
Like artificial lift, compression is an integral part of the equation when it comes to optimizing all the interacting elements in a field. As with artificial lift, changing compression/gathering line pressure in one part of a field can impact other parts. In fact, it can be very difficult without real-time data and some type of optimization modeling for field operators to see that gathering pressures at one area are choking off production in another area. By analyzing data in real time, operators can make certain that line pressures are continuously maintained at optimum levels.
Some of today’s most demanding production operations involve enhanced recovery projects. The need to control and manage steam injection, injection temperature, soak time, water and oil production, etc., make huff-n-puff cyclic steam injection and steam-assisted gravity drainage extremely complex from an optimization standpoint.
Carbon-dioxide miscible flooding also requires sophisticated measurement and modeling capabilities since the CO2 is in both a gas and liquid phase. Two-phase digital Coriolis meters are proving very successful for one operator in a West Texas CO2 flood to measure the volumes of CO2 being injected and recovered, while real-time optimization is assisting with reservoir management issues such as determining the optimum level of CO2 injection, analyzing sweep efficiency and avoiding channeling.
In northern Alberta, new software technology is being field tested in a particularly challenging application that has a single process stream containing CO2 in both liquid and gas phases, hydrogen sulfide in both liquid and gas phases, oil, water, and condensate. One allocation device is measuring the multiphase flow, and the data are being compared with data from a test separator with very promising results. The operator is planning to bring hundreds of wells on line, all of them equipped with automation and real-time measurement capabilities.
No matter the form of artificial lift or the type of production operation, the ability to optimize each piece in a production network using technology that brings it all together–automation, remote monitoring, real-time data capture, information analysis, and simulation and modeling–is the key to enhancing oil and gas production economics.
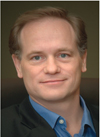
BRIAN DICKSON is vice president, field devices, at Invensys Operations Management in Plano, Tx. With 20 years of experience related to plant and field automation, Dickson focuses on creating and delivering high-value solutions. His career includes work in measurement, control and optimization, with a current emphasis on business value created through innovative application of various technologies. Dickson began his career with Foxboro Canada in Edmonton. After a three-year assignment in Abu Dhabi as country manager for the United Arab Emirates and Oman, he returned to North America as a manager in Western Canada, where he spent eight years. He also served as a director of sales in Singapore before assuming his current assignment. Dickson is a graduate of the University of Alberta.
For other great articles about exploration, drilling, completions and production, subscribe to The American Oil & Gas Reporter and bookmark www.aogr.com.