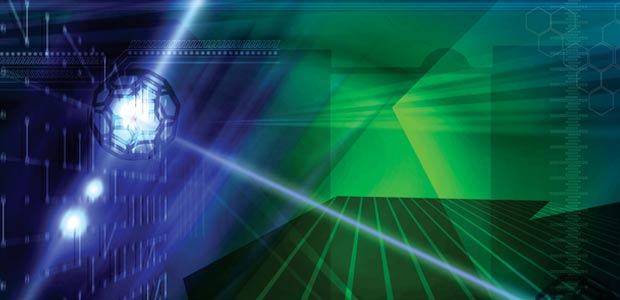
Advances In Nanotechnology Hold Huge Potential Promise In Upstream Applications
By Kari Johnson, Special Correspondent
Incredibly small by definition, nanotechnology is making big leaps in potential applications in the oil and gas industry.
“Nanoscale technology has moved from science fiction into really hard engineering,” says Wade Adams, director of the Richard E. Smalley Institute for Nanoscale Science and Technology at Rice University.
Adams notes that companies are bringing to market commercial nanoscale products such as anti-corrosives and smart proppants, and nanotubes–once the province of research labs–now are manufactured on the tonnage scale in Belgium, Germany and Asia.
The evidence, according to Adams, is in the inclusion of nanoscience in a wide cross section of disciplines, including physics, chemistry and material science. Nanotechnology is also the focus of research projects at universities across the country. Oil and gas service companies also are getting involved, hiring nanotechnology specialists and supporting basic research. Moreover, Adams notes that new companies are bringing commercial nanoscale products to market.
Nanoscale technologies are very small, typically 1-100 nanometers. At this scale, research shows that well established chemical and physical properties do not hold. Instead, the nanoparticles may exhibit extraordinary magnetism or other changes in their micro and macro properties, Adams explains.
“The combination of reduced size and special properties make nanotechnology intriguing. Super strong, ultralightweight materials could be developed based on nanoscale technology, for example,” he states. “Laboratory measurements have made it clear that you can take a multiwall carbon nanotube and get what amounts to 100-gigapascal tensile strength, which is 20 times stronger than the strongest carbon fiber made today. Now that would be a revolution.”
Carbon bonding at the nanoscale level gives the Buckminster-fullerene–dubbed the “Buckyball”–a tremendously strong structure. The Buckyball forms the elemental components of other nanotechnologies, including nanotubes and nanocars.
Nanotechnology is the focus of research projects at universities across the country and is working its way into primary, secondary and continuing education. Rice offers a nanotechnology 101 course for business people. In the fall, a short course will be offered on the history of the Buckyball (Buckminsterfullerene), which turns 25 in October. The Buckyball, which won a Nobel Prize in chemistry for Richard E. Smalley and his associates, measures only a single nanometer in diameter, yet its 60 carbon atom structure is tremendously strong, relying entirely on carbon-carbon bonds, which Adams says is the strongest of all possible elemental bonds. The single-walled carbon nanotube is essentially a continuous Buckyball.
Once little more than a novelty, nanoscience is projected to be a fast growing and highly profitable business during the next decade. “The financial wizards think nanotechnology will be a $1 trillion-$3 trillion industry by 2020,” Adams relates. “In any case, there will be lots of little companies focusing on developing a range of nanotechnologies, and lots of larger companies figuring out ways to incorporate them into their products.”
Adams recognizes that achieving that kind of breakthrough in a lab is one thing and consistently engineering it in a manufacturing facility is another, but he says it gives him hope that it is possible to make a fiber strong and light enough to make a space elevator, or revolutionize the construction options for deepwater oil and gas production facilities, or perhaps totally revamp the transportation system.
“Imagine, for instance, designing a sport utility vehicle that weighs one-third as much as an SUV today, but is much stronger and safer. That would cut fuel consumption as much as 80 percent and extend the lifetime of a precious petroleum resource base quite a bit,” Adams says. “To me, petroleum is too precious to be burning at such a high rate in cars and trucks.”
Industry-Specific Research
A key development in nanoscale technology specifically for the oil and gas industry was the formation of the Advanced Energy Consortium, says Scott Tinker, who originated the concept of the AEC and serves as its director. The AEC, which took Tinker and his colleagues more than three years to develop before the doors opened officially in January 2008, is managed by the Bureau of Economic Geology at the University of Texas at Austin.
“The Bureau has a long history of bridging between academia and industry,” Tinker says. “That is the primary reason the industrial members of the AEC felt comfortable placing management with us rather than a specific company, as is common in more traditional joint industry partnerships.”
The AEC funds research projects of particular value to the industry at universities, labs and companies around the world. Projects can involve university research staff and industry representatives, explains Tinker, noting that the AEC will provide some 25 different research entities with funding this year.
In addition to workshops hosted by the consortium in Austin, which were some of the first to bring oil and gas industry representatives together with university nanotechnology researchers, the upstream petroleum industry is buying into the potential of nanotechnology, with oil and gas companies hiring college graduates with nanotechnology backgrounds, according to Tinker.
The Society of Petroleum Engineers and the Society of Exploration Geophysicists both have hosted several global forums and workshops, and companies such as ExxonMobil are hosting workshops to spread the word about nanotechnology, Tinker notes. At the same time, he adds, major oil and gas conferences have begun to integrate nanotechnology into their technical programs.
Carbon nanotubes are essentially continuous Buckyballs, allotropes of carbon with a cylindrical nanostructure. Nanotubes can be single- or multiple-walled, and have been constructed with a length-to-diameter ratio of up to 132 million-to-1, significantly larger than any other material. The carbon-to-carbon bond is the strongest of all possible elemental bonds, with nanotubes exhibiting tensile strengths 100 times that of steel. In addition to their extraordinary strength, nanotubes have novel electrical and thermal conductive properties that give them potential value in a range of oil and gas applications. A single-wall, 1-nanometer carbon nanotube is shown at left, with a large number of aligned carbon nanotubes shown at right.
Governments are becoming interested as well, according to Adams. The state of Texas, Rice University (Smalley Institute) and the province of Alberta have signed an agreement to work cooperatively on a variety of projects related to oil sands. The list of top projects is under development, but is likely to address issues such as reducing the use of water in enhanced oil recovery, better catalysts, cleaning waste water and increasing the efficiency of flowing fluids through long pipelines, Adams relates.
He observes that ExxonMobil held a workshop to spread the word about nanotechnology, and the Society of Exploration Geophysics has also held several workshops internationally. “The cross-fertilization that is needed has started to happen to facilitate the uptake of nanotechnology in the oil and gas industry. I like to think that we have had something to do with that here at Rice,” says Adams.
Cooperative Program
Six years ago, AEC was nothing more than an idea. Tinker, who also serves as director of the Bureau of Economic Geology and a professor in the Jackson School of Geosciences at the University of Texas at Austin, says he thought it would be beneficial to organize a group of companies working cooperatively to fund basic research that could yield significant advances in enhanced recovery of oil and natural gas, along the lines of the DeepStar consortium for developing deepwater exploration, drilling and production technology.
“The AEC’s formation was anything but simple, given the players involved,” explains Tinker. “It benefitted greatly from patient legal and contractual work by Jay Kipper, associate director of the AEC. Forming a consortium of this magnitude is not for someone who is in a hurry,” he laughs.
After three years of organizational development, the consortium converged on subsurface nanotechnology as its primary focus, and in January 2008 opened its doors and began to develop a strategy to interest leading researchers from other fields in the oil and gas space, recalls Tinker.
The consortium consists of 10 companies (BP America Inc., Baker Hughes Inc., ConocoPhillips, Halliburton Energy Services Inc., Marathon Oil Corp., Occidental Oil and Gas, Petrobras, Schlumberger, Shell, and Total) that provide equal funding and have equal input on projects and organizational guidance, explains Tinker. They also have equal access to intellectual property through royalty-free, nonexclusive licensing. Each project typically has six to 10 industry personnel that actively engage in project tracking and reviews. “It is in their best interests to be actively involved in projects,” Tinker says. “Then they are in a good position to leverage the research for their own use.”
The AEC focuses on precompetitive research. While commercial applications will certainly come out of the research, commercialization will not be done by the AEC itself, Tinker explains. “This makes it easier for companies to collaborate, drives projects that are fairly broad, and for now makes the AEC quite different from the biomedical and other fields, in which faculty often form startup companies to commercialize their academic research findings,” he observes.
During the startup phase, the consortium defined its mission to develop nanoscale sensors that could provide previously unattainable information about the interwell oil and gas reservoir space, and then began an educational process to bridge the divide between petroleum and nanotechnology specialists, according to Tinker.
“Our member companies had limited experience with nanotechnology and really did not understand its potential in the oil field,” says Sean Murphy, program manager at AEC. “At the same time, many of the nanotech researchers never had considered the extreme conditions that are common in the subsurface. The downhole environment is hot and chemically intense with high pressures.”
“There is just a whole lot going on in the earth that does not happen, for example, in the human body, where small sensors have been deployed for medical purposes,” adds Tinker.
A request for proposals was issued at the end of the first six months, and 21 projects were selected for funding. Another 13 projects were funded in the second round, filling in the gaps from the first. “We are starting to see results from the early projects,” Murphy reports.
A recent annual project review held in Boston hosted about 150 attendees representing member companies and more than 20 funded universities. “The advances made in only one year are astounding,” says Tinker.
Four Project Classes
Research is being conducted at universities and labs around the world, with research grouped into two broad classes: mobility (including experimental studies, modeling and simulation), and sensors (including contrast agents, nanomaterials and microfabricated), according to Murphy. “Nanotechnology is still young enough that more research is needed to understand the basic interactions of nanoparticles and fluid flow,” he explains. “Our projects are exploring how these particles behave in simple to complex rock and fluid systems, how nanoparticle types, shapes and coatings influence retention, and how different rock types and pore geometries impact particle transport."
Nanofluids are designed by adding nanoscale particles in low volumetric fractions to a fluid to enhance its rheological, mechanical, optical and thermal properties. The liquid phase can be oil, water, ethylene glycol or conventional fluid mixtures and the nanoparticles are carbon, metals and metal oxides, and inorganic materials with properties of no dissolution or aggregation in a liquid environment. These photographs show a nanofluid containing cation-exchanged laponite. When metal powders are mixed with the laponite suspensions, they have no effect on suspension viscosity and the resulting solutions remain free-flowing liquids. When these metals are intercalated into the interlayer of the laponite disks, however, viscosity increases several hundred times and the solution turns into a gel strong enough to hold its own weight. Such gel strengths can suspend barite and other weighting materials used in drilling fluids. Courtesy of the National Energy Technology Laboratory.
Projects focus on specific applications of nanotechnology, such as contrast agents that may be able to better illuminate the reservoir. For instance, Murphy says nanomaterials may be able to leverage existing seismic, electromagnetic, and electrical remote sensing technologies by “lighting up” the reservoir to detect various geophysical and petrophysical properties at higher resolutions.
Research into the use of passive sensors may yield nanoparticles that change their states when they experience a target substance or environmental condition in the reservoir. For example, they might fluoresce or their molecular bonds may change to reflect peak reservoir temperature, or pressure or pH conditions. “These sensors may ultimately be injected into wells, retrieved and then interrogated to determine what they encountered in their travels,” Murphy comments.
Another line of research centers on the miniaturization of electronics to the nanoscale level for use as injectable sensors. “Such micro-sized sensors may allow us to get beyond the well bore a few feet, into the interwell space that is unaffected by drilling,” explains Murphy. “Our research teams are looking at the tough problems of building, powering and communicating with these devices.”
Because the research is at such an early stage and nanotechnology remains so new, Tinker says it is difficult to envision exactly what types of advances could come out of AEC’s initial efforts. “But it is fun to try,” he laughs.
“Nanotechnology projects often bring together researchers in physics, chemistry, chemical engineering, electrical engineering, material science and nanotechnology,” Tinker observes. “The best discoveries are often made at the margins of disciplines. An example is geomicrobiology, where research combines geology, chemistry and biology to study the ‘DNA’ of rocks. That will happen in nanotechnology as well. The importance of nanotechnology as an agent for revolutionary change was so compelling that it made sense for industry to collaborate and support basic research. The industry is to be recognized for its foresight and willingness to come together to tackle this challenging new field. The opportunities are limited only by our imagination, and a few laws of physics,” he quips.
Nanomaterial Membranes
Given its potential for improving the production and recovery process throughout the lifecycle of oil and gas assets, nanotechnology has become a significant focus for research at the University of Wyoming, according to Brian Towler, professor and fellow for hydrocarbon energy resources at the university.
Separation technologies are among many applications for nanotechnology. Historically, amine technology has been used to separate hydrogen sulfide and carbon dioxide, but all sorts of new membranes now are being developed, according to Towler.
“Gas separation membranes rely on differences in chemical or physical interaction between the components present in the gas mixture and the membrane material,” Towler explains. “Gas absorption membranes are used as contacting devices between a gas flow and a liquid flow. The absorption liquid on one side of the membrane causes the separation by selectively removing certain components from the gas stream on the other side of the membrane.”
Nanomaterial membranes are stronger, less brittle and more temperature resistant than ceramic materials. These membranes can be impregnated with nanoparticles, which plug the intercrystalline pores and make the membrane selective toward a specific gas, says Towler. “One of the exciting lines of research here at Wyoming is in the area of adsorbents that remove carbon dioxide from natural gas and flue gas, and could be used in recovery and sequestration,” he remarks. “This work is garnering national attention for its potential in reducing CO2 emissions.”
Adsorbents relate to purification in particular, adsorbing impurities to treat oil and gas flows. They can also be applied in remediation projects to clean contaminated sites, according to Towler. “The adsorbents capture the impurities and then release them off the material in a controlled environment,” he states. “Wyoming is interested in the possibility of carbon sequestration, because the state is a strong candidate for storing CO2.”
More Effective Proppants
The industry’s march into the unconventional resource play frontier has been enabled largely by another microscopic agent of change: proppants pumped into ultratight rock formations during hydraulic fracturing treatments to create pathways for oil and gas to flow into the well bore. But given the steep decline curve on most shale and tight sands wells, the industry continues to focus on developing stronger, yet lighter-weight proppants capable of being carried deeper into the formation without being crushed or settling out. That is where nanoscience is entering the picture, according to Andrew R. Barron, the Welch Chair in the chemistry department and a professor of materials science at Rice University and an AEC-funded researcher.
“Typically, proppants can only travel 100-130 feet in shale and tight sands reservoirs,” explains Barron. “What is needed is a more buoyant proppant that is light enough to go 180 feet or more into the reservoir, but strong enough to withstand high closure stresses.”
Designing a better frac job could double recovery, according to Barron, and a more buoyant proppant system would require much less pressure and fluid, both reducing cost and easing the need for large volumes of water. A case in point is the ceramic proppant technology originally developed in his laboratory. Unlike conventional sand proppants, the manufacturing process of ceramics can be controlled at the molecular level to create perfectly spherical proppants hundreds of microns in size that are hollow to add buoyancy, Barron points out.
“As a result of using this inherently simple molecular design, ceramic proppants are very lightweight with a specific gravity and strength curve similar to more conventional proppants,” he remarks.
According to Barron, ceramic proppant research initiatives at Rice University have culminated in the commercialization of a product by a new company spun off from Rice, Oxane Materials, which he says has started commercial proppant production operations at a large manufacturing facility in Van Buren, Ar.
The next logical step, Barron contends, is improved diagnostics to determine the exact location of pumped proppants. “If we can precisely track where proppants go, then we can tell if a frac job worked as designed,” Barron states. “The trick is in the detection.”
Magnetic Sensing
To address this challenge, Barron says he is collaborating with David Potter at the University of Alberta on one of the AEC-funded projects, to develop an initial methodology that incorporates magnetic nanoparticles in the structure of the proppant that could be sensed during a frac job to assess the effectiveness of a treatment, or perhaps even during production or waterflooding operations to identify proppant flow back.
Nanotechnology is rapidly moving into mainstream oil and gas operations. One example is lighter and more buoyant proppants capable of migrating deeper into the formation than conventional proppant materials, yet strong enough to withstand high closure stresses without being crushed or settling out to improve recovery rates–particularly in unconventional shale and tight gas sand formations. Ceramic proppant research initiatives at Rice University culminated in the commercialization of OxFrac™ and OxBall™ as well as a new company, Oxane Materials, spun out of the Rice R&D effort. The company has commenced proppant production operations at its manufacturing facility in Van Buren, Ar. Modeling indicates the nano-based proppants can increase initial production by up to 50 percent while slowing the steep production declines that characterize many unconventional reservoirs.
Within the next couple years, Barron reports that it will be possible to see in three-dimensional space where proppants are going. Initially, the sensors will need to be in close proximity, providing an indication of porosity and permeability based on the flow rate of the proppants. “If the flow is fast, then there is good porosity and permeability, because the proppants have some place to go and a pathway to get there,” he explains. “Using this information, a 3-D image can be constructed, showing how porous and permeable the structure of the rock is and how well a treatment is working in real time.”
The next goals would be to achieve understandings of porosity, permeability and chemistry as well. “We already have a material that changes on contact with sulfur, for example,” Barron observes. “Potentially, the proppant would be detected using chemical composition and physical properties.”
The sensors likely would be mixed in the proppant as a low-percentage additive, which would add to the cost. “But the benefits in additional information should outweigh the incremental cost,” Barron holds. “Plus, the technology should help reduce pumping and fluids costs. There are three failure points for any research: the laws of physics and chemistry, the inability to engineer, and economics. We keep all three in mind as we define projects so that our research has the best chance of reaching commercialization.”
Potter, director of the integrated petroleum geosciences master’s program at the University of Alberta, says the magnetic properties of nanoscale materials are of particular interest to him. As a professor of petrophysics and geophysics, Potter is exploring the possibilities of using magnetic properties for sensing in several applications.
To achieve the goal of using nanoparticle magnetic sensing to track the pathways of proppants, Potter reports that he is working on sensing particles (developed by Barron’s group) with a high magnetic susceptibility at reservoir conditions that can be detectable above the noise level of the rock matrix surrounding the bore hole. “Once this is done, it is likely to be deployed on a large scale to discover where the proppants are and how far they have traveled,” he states.
On a smaller scale, there has been interest in using magnetic properties to estimate the permeability anisotropy of core samples. “In the 1990s, some researchers injected a ferro fluid into core samples to see where the particles went over time,” explains Potter. “They were trying to determine the pore fabric and relate this to permeability anisotropy with this technique. Extending this type of research using nanoparticles specifically designed for downhole conditions and sensing on the larger scale could yield far more detail and dramatically improve our understanding of permeability anisotropy and fracture anisotropy in an active well.”
Nanostructured steel surface technologies are enhancing the physical properties of oil field tubulars, piping and other equipment. Nanostructured alloys for thermal spray coating and weld overlay for hardfacing and wear plate applications combine high hardness and toughness properties for exceptional resistance to corrosion, erosion, impact and wear. As shown in the figure at left, nanostructured steel alloys provide a new class of steel, with hardness fracture toughness exceeding conventional alloys. NOV Grant Prideco’s Platinum® HB, developed in partnership with The NanoSteel Co. using its Super Hard Steel® technology, is engineered for drill string hardbanding applications to provide high strength for minimum casing wear performance and tool joint protection as well as high toughness to resist cracking and spalling in severe downhole applications.
A third area of investigation focuses on in situ nanoparticles. “The formation rocks themselves have nanoparticles such as magnetite and hematite embedded within them,” Potter notes. “Some of the larger nanoparticles, or aggregates of nanoparticles, may sometimes block pore connections in intrinsically ‘tight’ reservoirs, which may influence permeability.”
Because these particles have a higher magnetic susceptibility than the formation rocks, logging tools potentially could be used to find in situ nanoparticles to identify formation layers where they could be problematic. To determine how these particles migrate within the formation, and whether the particles can be flushed with production processes, Potter says his group is performing flow experiments that simulate waterflooding and other fluid flow procedures and tracking the particle migrations with magnetic sensors.
Other Research Areas
One area of research being funded by the AEC is to use chemical “nanoreporters” to gain insights on downhole reservoir conditions. In essence, nanotechnology chemical sensors are pumped into the well bore to report back on what they encounter down hole, explains James Tour, professor of chemistry at Rice University.
“Ultimately, nanoreporters could replace tracers, which can be pumped down hole and then identified when they come up elsewhere. While tracers can tell you where they entered and exited, nanoreporters also can tell you about the journey in between,” he says.
To be useful, nanoreporters must be smaller than 100 nanometers so they do not plug pore spaces in the reservoir. “The tiny sensors are infused with chemicals that diffuse in the presence of oil, for example, with the rate of diffusion revealing the volume of oil encountered,” Tour relates.
Rice University has created nanocars using four Buckyballs for wheels, an axle and a central chassis made from basic molecules. The first incarnation was propelled by applying temperature, and the second was driven by light. Variations of the nanocar include a nanodragster, nanotruck, nanobackhoe and nanotrain.
A graph of what is encountered then can be made for visual analysis. “Chemical nanoreporters can fluoresce so they are easily identified as they surface,” Tour adds. “They can be so sensitive that even a single molecule can be readily seen.”
Several years ago, Tour and his students at Rice University created a nanocar, a nanotruck and a nanotrain using Buckyball wheels, axles and a tiny chassis. These nanovehicles were powered using a molecular motor that produced 1.8 rotations a minute. “The thinking behind the nanocar was that complex structures can be built from simple components,” Tour observes. “By developing and powering the nanocar, we took a big step toward defining the basic building blocks.”
In 2009, Tour and his team completed a nanodragster. Other modifications have permitted a light-powered motor that produces 3 million rotations a minute. “And we have another version of a nanocar that is chemically driven using hydrogen and ethylene. And a third version involves a polymer spitting out the back end as the car moves. From these developments, we have learned a great deal about bottom-up assembly and controlling motion,” explains Tour.
Graphene, single-layer sheets of graphite that are one-atom thick, may find a new role down hole in plugging pores during the drilling process, according to Tour, who entered a partnership with M-I SWACO. Rice University and M-I SWACO are working on a graphene additive that would protect the reservoir pores from becoming clogged with drilling mud. Forced by fluid pressure, Tour explains, the additive would form a thin filter cake that could be easily removed by formation pressure during the production phase. He says graphene also could be used in other drilling products and completion fluids in the future.
“The potential applications for nanoscale technology are endless,” Tour concludes.
For other great articles about exploration, drilling, completions and production, subscribe to The American Oil & Gas Reporter and bookmark www.aogr.com.