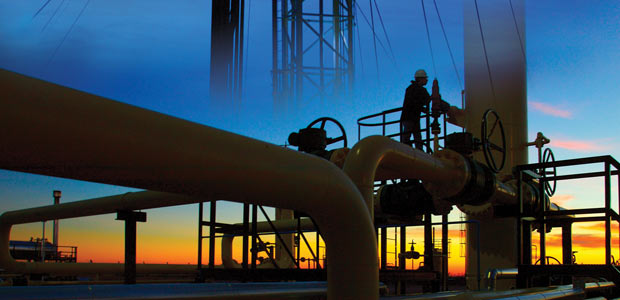
Applying Right Technologies Drives Value Creation Process Across Asset’s Full Life Cycle
By Mike Bahorich
HOUSTON–Technology has become the name of the game in upstream operations, even though business success always is measured by the bottom-line financial numbers. But in an industry in which the “state of the art” is being redefined almost by the project–particularly in evolving plays such as onshore unconventional gas and offshore ultradeep water–technology has very much become the business of oil and gas.
Whether drilling an ultralow-permeability gas shale formation in North America or testing a deep oil prospect in the Egyptian desert, having the right tools can be the key difference in being able to bring a project in on time and budget. But technical success is no guarantee of economic success. Fortunately, a range of technologies–from complex 3-D seismic imaging to multistage hydraulic fracturing and time-lapse reservoir monitoring–can create value along the exploration, drilling and production chain to enhance economic performance throughout an asset’s full life cycle.
Although investing in technology may seem easier to justify during periods of high commodity prices, the truth is technology may be even more critical at lower prices, when the economic margins become tighter, fewer dollars are available to generate returns, and operational inefficiencies and cost overruns can destroy profitability. If a given technology can help a company complete a project faster and at less cost with better results–be it subsurface imaging or hydraulic fracturing–it generally makes sense to deploy that technology regardless of the prevailing commodity price environment.
The value creation process begins with exploration, and more specifically, the acquisition of seismic data. With imaging environments becoming more complex, less conventional and deeper, the trends in seismic acquisition are toward ever-higher channel counts for increased density and greater numbers of receivers and sources for higher-resolution surveying. The high-channel acquisition systems seismic contractors are deploying in the field today are similar to computer “networks,” in that receivers are being connected in large arrays to achieve much higher-resolution sampling for a more detailed final image.
Wireless receivers that acquire data without cables also are beginning to take hold. These receivers generally have a battery, flash memory, a geophone and recording software in a very small, lightweight package that can function autonomously in the field.
Apache has used fully wireless systems as well as hybrid systems that combine wired and wireless receivers. In a survey shot on the border between Argentina and Chile, a conventional cabled system was deployed in Chile while passive wireless recorders were used in Argentina to acquire data continuously until data acquisition was finished. The survey design effectively created a continuous area of coverage in Argentina and Chile without any cables, sources or even a wireless signal crossing the border. When the survey was complete, the data were reconstructed and merged to create a single data set.
Building A Better Image
Improved imaging is always an issue, particularly as the industry targets deeper structures and more complex imaging environments. For years, seismic imaging has adhered to a process of continual improvement similar to Moore’s Law governing the increased speed/reduced cost of computing, and the incremental improvements in the ability to obtain a more accurate subsurface image will only increase. Every time the industry improves the level of imaging quality, more light is shed on the subsurface, revealing new features and details that ultimately lead to new discoveries. As seismic imaging moves to the next level over the next couple years, it will once again open the way for even more reserves and fields to be found.
One of the drivers behind the steady incremental gains in imaging quality is 3-D data migration. The geophysical industry has evolved from running fairly simple time migrations to highly sophisticated depth migrations that require massive computational horsepower. For example, reverse-time migration (RTM) is a more accurate implementation of wave equation imaging that enables multiple ray path tracing through dramatically different velocity bodies. Geoscientists have known about RTM for some time, but it was impractical to utilize because of historic limitations in computing capability. With affordable, yet powerful clustered supercomputers as well as new RTM algorithms, the technology now is being deployed on an almost routine basis to obtain much more accurate velocity models and processed images.
Multicomponent seismic is another technology whose time is coming. Multicomponent adds the shear (s) wave component to the compressional (p) wave energy in a 3-D data set. As one of the earliest adopters of multicomponent 3-D, Apache utilizes the technology to help solve a number of imaging problems and better predict reservoir quality from surface seismic data. There is a definite role for multicomponent in unconventional resource plays (one of the main applications, for example, is characterizing naturally fractured reservoirs), but we also have examined the use of multicomponent 3-D with ocean-bottom cables as a direct hydrocarbon indicator in soft rocks by comparing s- and p-wave data contrasts.
Wide-azimuth (WAZ) 3-D imaging has become almost synonymous with the Lower Tertiary play in the Gulf, where marine WAZ techniques are a relatively new development. However, wide-azimuth has been used onshore for some time. In fact, Apache has shot a number of WAZ surveys on land, including large surveys in the Western Desert of Egypt, and has found it to be extremely useful, particularly in imaging deeper targets.
One objective that Apache specifically attempts to accomplish in its geophysical operations is the ability to shoot very large seismic surveys extremely cost effectively and with very high image quality. We pride ourselves in understanding how to design very large (multithousand square-kilometer) land surveys to maximize efficiency while getting better data and better image quality at less cost. Achieving this competitive advantage boils down to a combination of having the right technical proficiencies to optimize survey design and field operations as well as leveraging the right technologies.
One such technology is independent “slip-sweep” vibroseis systems for land acquisition. Slip sweep techniques using high-density single vibrator operations improve wavefield sampling without source array effects for high-resolution imaging and better structural delineation. Apache was the first operator to conduct a production survey using single-vibrator slip-sweep technology and acquired a shot every five seconds (more than 700 an hour), which established a world record at the time. The technology is ideal for high-density and wide-azimuth data, enabling data to be acquired from simultaneous sources and sorted out during processing for increased resolution and better subsurface illumination with reduced acquisition cycle times.
Shifting The Paradigm
Of course, the value-adding impact of technology extends well beyond geophysics. In drilling, for instance, coiled tubing techniques can significantly reduce drilling time and cost. One operator was able to drill a Barnett Shale well to total depth with coiled tubing in only four days. Obviously, that kind of dramatic reduction in rig time can transform drilling economics, but the small-diameter hole size and logistical issues present limitations that still have to be overcome before CT drilling can reach its full potential.
Horizontal drilling is another high-impact technology. More horizontal rigs are active in the United States today than vertical rigs–372 horizontal rigs versus 345 vertical rigs during the first week of June, according the Baker Hughes Weekly Rig Count. This trend actually is related as much to completion as drilling technology, specifically the ability to complete multiple stages in long horizontal laterals. In fact, I believe the greatest single innovation in the industry in the past decade in North America has been the refinement of multistage completions. Oil and gas companies are completing 4,000-foot and longer laterals with a dozen or more stages, which dramatically increase production rates and improves recovery efficiencies.
The industry is in the middle of a huge paradigm shift with multistage completions. The state of the art in multistage completions quickly has evolved from three to six frac stages per horizontal well to the point where 12-15 stages are becoming routine. That number will increase even more going forward. Considering that there are typically three to four perforation clusters between each frac stage, it could be argued that operators are already putting 50 stages in a horizontal well with a 12-stage completion if each perforation cluster is counted. Of course, at this point, not each perforation cluster is effective, but new innovations surely will provide improvements.
Within the next decade, the industry will figure out how to inexpensively go from 15 frac stages to tens of stages per lateral. The additional stages, specifically in ultralow-permeability shales, will have a corresponding increase in production rates. Considering that a horizontal well completed with 15 frac stages can produce up to 15 times as much gas as a vertical well drilled in the same location with a single frac, it is not hard to imagine how doubling or tripling that number of frac stages could further impact initial production rates in some ultralow-permeability shales.
The efficiency gains with horizontal drilling and multistage completions are even more pronounced with pad drilling operations. A series of horizontal wells drilled on a single pad might have more than 100 total frac stages, as opposed to putting one vertical well with one or two fracs on a pad. In a very impermeable reservoir such as a shale or tight sand, each frac stage functions as almost a completely separate entity. On a multiwell pad it is possible to have nearly continuous fracturing operations, moving back and forth between wells and zones to complete each stage with optimal efficiency.
The bottom-line issue here is the cost per frac stage. If there are more fracs per lateral and more wells per pad, it is possible to get to the point where fracturing operations are conducted around the clock for an extended period to achieve tremendous efficiencies and economic savings.
It is true that with more frac stages and more proppant pumped into the reservoir to open conduits for hydrocarbons to flow to the well bore, the faster the reserves will deplete. However, it is important to remember that multistage fracs ultimately improve recovery. That is a big part of what is driving the technology’s growth in ultralow-permeability tight sands and shales, where steeper decline rates are offset by high initial flush production.
Monitoring Performance
One example of the expanding role geophysics is playing in nonexploration workflows is microseismic, which is not only one of the most interesting technologies to come along in recent years, but also ranks as one of the most important advances because it directly supports the single most critical invention: the multistage horizontal completion.
There is no question that microseismic monitoring has helped refine and optimize multistage frac technology to better exploit unconventional reservoirs. Looking forward, what the industry perhaps requires more than anything else are better real-time tools to change frac designs on the fly as multistage jobs are being pumped. I expect a series of technologies to be introduced within the next few years that will bring game-changing real-time analytical capabilities to multistage hydraulic fracturing.
One potential solution is permanently embedded microseismic sensor arrays to monitor frac jobs throughout a field’s development, and ultimately, perhaps even assess recovery efficiency. There are a handful of early applications of this technique to assess the feasibility of using embedded microseismic to monitor the effectiveness of frac jobs in an unconventional reservoir setting.
Regarding 4-D seismic, there is certainly a place at the table for this technology as the world’s oil fields mature and as more enhanced recovery projects are implemented. Time-lapsed seismic surveying actually started in onshore enhanced oil recovery operations to monitor steamfloods, and subsequently migrated offshore. Although not every reservoir is amenable to 4-D, it will be applied in areas with appropriate rock properties. In these environments, 4-D can help operators maximize production and recovery rates.
A case in point is the Apache-operated Forties Field, the largest oil field in the North Sea. As a giant field (roughly equal to the area encircled by the 610 Loop around Houston) in the most mature province for 4-D technology, it could be argued that Apache is deploying 4-D very much in the “sweet spot” for the technology, but there is no arguing with the results. Production from the Forties Field effectively has doubled since 4-D monitoring began, ramping from 35,000 to more than 70,000 barrels a day.
Given the field’s size, there are numerous opportunities to identify bypassed pay and drill infill wells in areas that have not been adequately swept. The two main tools we use to accomplish that are 3-D and 4-D seismic, using 3-D data to obtain a snapshot of areas of the reservoir that could have bypassed pay, and then applying 4-D monitoring to determine if any changes occur in those areas over time (indicating whether those sections of the reservoir are being swept).
In terms of the overall impact, the prize is so huge that improving recovery technology likely will prove far more significant than advancing exploration technology. For that reason, the task with technology will increasingly shift to figuring out how to get more resource out of the ground, especially as the industry targets more poorer-quality unconventional reservoirs.
In fact, I envision growing demand for all types of enhanced recovery techniques in the future, in addition to recompletions of older wells using multistage fracturing wherever feasible and the nearly ubiquitous application of nonexploration geophysics such as 4-D and microseismic monitoring. Even a relatively mature EOR technology such as waterflooding will see advances that lead to more effective recovery. For instance, new waterflood modeling algorithms have been developed that analyze the performance of producing and injection wells on a systems level without a full geologic model.
Single “game-changing” technological advances may come few and far between, but leveraging the right sets of technologies in the right applications can have no less dramatic impact on the ability of oil and gas companies to create value and enhance economic performance, regardless of whether commodity prices are trending up or down.
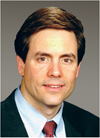
MIKE BAHORICH is executive vice president and technology officer at Apache Corp. He joined the company as chief geophysicist in 1996 after serving several years at Amoco working in prospect generation and development, research and management. Bahorich is a past president of the Society of Exploration Geophysicists and received SEG’s Virgil Kauffman Gold Medal. He is a graduate of the University of Missouri at Columbia and received a master’s in geophysics from Virginia Tech. Bahorich serves on advisory boards at Stanford and Yale and holds eight patents.
For other great articles about exploration, drilling, completions and production, subscribe to The American Oil & Gas Reporter and bookmark www.aogr.com.