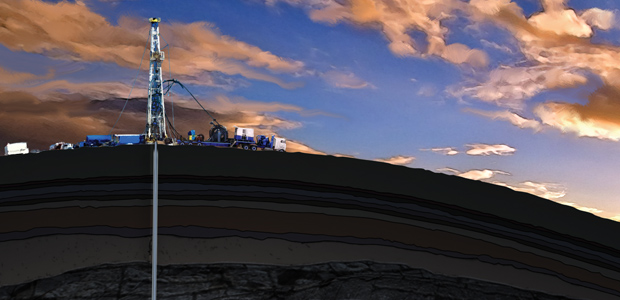
Well Intervention
Complex Wells Driving Advancements In Real-Time Measurements
By Teoman Altinkopru
HOUSTON–Looking at how hydrocarbon recovery has evolved over the past decade, it is striking to see how wells have become increasingly complex, with deeper boreholes and longer, more deviated laterals. This phenomenon has raised the bar for making continued improvements in well intervention technology.
Advances in coiled tubing and slick-line equipment, along with the development of downhole tools that convey critical data and measurements in real time, are helping operators move into new frontiers and develop challenging wells that once were inaccessible.
The changing nature of the overall well intervention business began in the North American land market, which has exploded as a result of the boom in unconventional resources. Previously, the North American and offshore well intervention markets were similar in that both relied on conventional, often remedial, CT or slick-line intervention services for well clean-outs resulting from nitrogen kickoffs, formation fill that restricted the flow of production, and other conditions.
However, unconventional activity clearly has changed the game in North America, and customers now are focused on drilling and producing from shale plays, starting with natural gas and then moving to the liquids-rich formations. Wells with extended-reach laterals completed with plug-and-perforation methods that require greater dependence on services, such as CT to mill plugs and clean out wells post-hydraulic fracturing, certainly have had profound implications for well interventions.
The growth of extended-reach wells in the offshore has resulted in development of 2 3⁄8- and 2 7⁄8-inch coiled tubing, which has become almost standard practice in the North Sea.
While the offshore market is still driven by oil production that requires conventional well intervention services, there is a growing tendency in this sector to drill more complex horizontal and highly-deviated wells where the horizontal displacement is so large that the measured depth is three times greater than the true vertical depth. This trend toward increasingly complex well profiles in both land and offshore wells has created a nice overlap in that similar well intervention technologies can be applied in both markets.
As the industry ventures into deeper waters and horizons that require horizontal well configurations, it has learned that Mother Nature is not very helpful in reaching total depth using wireline and slick line, despite significant developments in tractor technologies. Concurrently, spread rates and the daily cost of offshore operations are significantly higher than they were 10 years ago.
Such challenges have made operators’ tolerance for failure extremely tight in offshore developments. In that regard, efficiency has emerged as an important factor in how companies choose their service providers for all well intervention services, including CT and slick line. In this high-cost, high-risk environment, service companies must take a “do it right the first time” approach to delivering well intervention solutions that ensure customers achieve their objectives efficiently, cost-effectively and safely.
A Technology Evolution
The push for efficiency as wells grow in complexity has sparked an evolution in well intervention technology, starting with the hardware itself. Carbon steel CT, designed with properties to push and pull tubing into horizontal displacements, has been embraced by the industry as a viable well intervention tool for horizontal wells. However, conventional tubing sizes (13⁄4 to 2 inches) are no longer sufficient because they don’t have the physical properties to reach total depth in these wells. Therefore, there has been a decided move to larger, heavier and more capable surface units, such as 23⁄8 to 27⁄8 inches.
In the offshore market, with the shift to more extended-reach wells, we see a clear growth in CT capabilities, including the Middle East, where 23⁄8-inch CT has been used for the past few years. In the North Sea, it is now almost standard practice to run 27⁄8-inch CT, which was unheard of only a few years ago. This trend has had implications for the entire supply chain, from the pipe manufacturers to the service providers. Today, companies that provide the larger, more capable units typically are getting the lion’s share of the work as well intervention jobs become more demanding.
Even more significant in driving innovation is the need for accurate, real-time data in CT operations. Well servicing companies are focused on developing high-tech sensors that provide real-time downhole measurements for greater accuracy. Tools that deliver the capability to digitally operate key well intervention services and equipment are helping rig crews carry out well intervention services efficiently and safely. This is especially significant in light of the ongoing industry challenge to recruit and train skilled workers at the pace of technology development.
Downhole CT services use real-time measurements to optimize treatments while the operation is ongoing. These packages include plug-and-play tools that deliver pressure, temperature and depth correlation data, as well as downhole load and torque.
For an offshore well intervention greater than 20,000 feet, for example, it typically takes two days to run in and out of the hole to conduct a stimulation operation to increase the productivity index of a well with lower drawdowns on the reservoir. In this situation, surface measurements provide little control over what the CT is doing down hole, meaning we can only infer the depth from length measurements. In a horizontal environment, those assumptions can very easily lead to a discrepancy in measurements and inaccurate decision making.
Therefore, downhole tools that can provide real-time information on depth, pressures, temperatures, and depth correlation are critically important, and represent a significant change from what was required 10 or 20 years ago in shallow, vertical wells where a 2 percent discrepancy was acceptable. That 2 percent variance in a 20,000-foot horizontal well is unacceptable because the need for absolute numbers is so important, and is significantly different from what industry was used to doing. Companies now require better resolution and better accuracy in terms of the critical parameters of executing a well intervention such as depth, pressure, and what the CT is doing in a customer’s well.
Fiber-Optic Telemetry
The development of real-time downhole measurements began even before 2000 with temperature and pressure data, and casing collar locators. Today, with fiber-optic telemetry, we have the ability to conduct distributed temperature sensing along the entire length of the well with three-foot resolution and a high degree of accuracy, and not only point pressure and temperature measurements. This has given the industry the capability to gain a comprehensive understanding of what is going on in the zone of interest (where the customer lands the horizontal section of the well).
Operators need to know where treatment fluids are going and how the formation is responding to the treatment in real time so they can fine-tune pumping schedules based on how the well actually is behaving, and not on a past job, lessons learned, or best practices that were applied to design the job. This ability to respond to the well during the operation is completely changing the game in well intervention, and is a step change we could not have dreamed of as recently as 10 years ago.
Real-time pipe inspection systems use magnetic flux leakage sensors, probes, and depth encoders to monitor the physical and mechanical properties of coiled tubing pipe, and to provide early warning of defects while a job is under way.
There now exist downhole CT services that use real-time measurements to optimize treatments while the operation is ongoing. The portfolio includes plug-and-play tools that deliver pressure, temperature and depth correlation data, distributed temperature surveys, and casing collar locator capability. Tension and compression sensors measure downhole overpull and load in deviated and horizontal wells, and gamma ray tools record naturally occurring gamma rays in formations adjacent to the wellbore.
While CT has become a critical tool in moving well intervention forward, it is by far the most used and abused piece of equipment in the oil field. In a live well intervention, where stimulation fluids and treatments are being pumped downhole continually, the CT pipe is being exposed to chemicals, high pressures and temperatures, hydrocarbons, sour gas, and carbon dioxide in harsh environments, all of which can cause deterioration and induce fatigue. Because CT is considered a pressure barrier, any weakening of the pipe can lead to wellbore integrity issues, which the industry takes very seriously.
In response to this, well servicing companies have developed real-time CT pipe inspection systems that use magnetic flux leakage sensors, probes, and depth encoders to monitor the physical and mechanical properties of the CT pipe, and provide early warning of defects while a job is under way.
Keeping Pace With Advances
As CT technologies and applications have matured, customers have gained the confidence to embrace these tools as viable well intervention conveyance methods. This growing technology uptake has led to a rapid increase in the number of well interventions and job counts.
Digital, downhole, adjustable jars allow operators to pretension slick-line cable, then stop the winch and send a surface command telling the jar to fire, bringing greater control and efficiency to jarring operations.
Unfortunately, what the service sector cannot do as quickly as the industry is growing, is recruit and train people. This bottleneck has created additional challenges in delivering “seasoned” crews for customers. So, while we are continuing to aggressively recruit and train new workers, we are counting on some of our latest technological enhancements to assist our less experienced crews to get the job done right, the first time.
The same is true for slick-line operations. Service companies are building new slick-line units every year and are working on improving their utilization of those units, but there is a limit to how much companies can do to increase their utilization of experienced crews to operate those units. By developing technologies that don’t require the expertise of a seasoned slick-line operator, we have a better chance to provide the services our customers need, while continuing to build our crews.
For example, one digital slick-line mechanical service portfolio digitally enables all conventional slick-line services, such as gauge cutter runs, drift runs, and pulling and setting subsurface safety valves. This means the service company does not need to rely strictly on human experience and skill to ensure delicate slick-line operations such as fishing are carried out with consistent precision.
Strategically located operations centers enable on-demand analysis of data from all over the world to streamline well site intervention workflows.
Improved Fishing Capability
One of the most common uses of slick-line intervention is to fish and jar a downhole restriction in the wellbore. Typically, the slick-line operator runs a tensioned slick line and mechanical jar into the hole in an attempt to latch onto the fish and, very quickly, start pulling it out of the well so it can be retrieved. This requires a high level of skill. If a less experienced operator doesn’t pull out of the hole fast enough, he may risk parting the slick-line cable, which can worsen the problem exponentially because now the cable must also be fished out of the well.
A digital, downhole, adjustable jar allows the operator to pretension the slick-line cable, then stop the winch and send a surface command telling the jar to fire. This method brings greater control and efficiency to jarring operations, and is a good example of how smart use of technology is overcoming gaps in field experience.
There is always the risk of becoming stuck with all slick-line and CT well intervention applications. A digitally controlled release (DCR) tool is a battery-operated tool positioned atop the bottom-hole assembly that allows the operator to send a surface command to the BHA to disconnect. This is especially advantageous for applications using slick line, which, unlike wireline, doesn’t have a weak point that allows it to break and be retrieved if the jar can’t be dislodged. If the slick line is continually pulled to free a fish, it often breaks at the surface, where the tension is the highest.
The DCR tool is a fail-safe mechanism that, if it does not receive a disconnect command from the surface, automatically disconnects in 24 hours. The operator can either send a command to disconnect, or, in case of a communication malfunction, the device will disconnect automatically.
This technology sounds simple, but it gives companies a way out, especially in remote offshore environments. It gives crew members the comfort of knowing that if things don’t go according to plan, the technology they have deployed down hole will assist in resolving the problem.
Support For Crews
As another example of how technology is making the crew member’s job easier, well servicing providers are developing tension limiters for slick line, similar to features becoming standard on CT fleets. The tool can preset tension specifications, depending on the size of the slick-line cable, preventing the operator from inadvertently exceeding the tension limit and parting the slick-line cable.
Advanced downhole tools also are providing greater efficiency and safety in perforation operations, which are conveyed on both CT and slick line. For perforating in long horizontals, we typically deploy charges and guns on CT. For wells that are vertical or less than 65 degrees in deviation, perforating guns are deployed on slick line. Regardless which conveyance is used, well servicing companies rely on the downhole firing head to behave the way it was designed.
Historically, industry had no surface verification that the guns actually had detonated, which posed significant safety risks to the crew. Today, sudden and dramatic increases in temperature and pressure captured and reported by downhole sensors provide a positive indication at the surface that perforation guns have fired.
Real-time data capabilities have opened opportunities for remote monitoring of well intervention operations by experts consolidated in a central facility. Strategically located operational centers provide engineering support and monitoring of ongoing well intervention operations that stream live data from sites all over the world.
Engineers with the expertise to interpret complex data on distributed temperature and pressure, and other key parameters, ensure that operations are being executed as designed, and intervene to address unplanned events and problems.
Looking ahead, the engineering pipeline is full, with some very exciting concepts in development. Among them is a technology for select perforation using CT. Today, the industry can perforate only by firing all the guns at the same time, regardless of length. With the new tool, an operator will be able to selectively perforate up to 10 zones in one CT run. This will enhance greater efficiency by eliminating multiple runs and bringing the well on production a few days earlier than we can currently.
As E&P companies place a priority on maximizing production from evermore challenging reservoirs, they rely on technology development to drive opportunity and success. Over the past decade, improvements in slick line and coiled tubing, along with breakthrough advances in real-time monitoring and data delivery, have brought significant step changes to the well intervention market, enabling operators to produce from wells that once were inaccessible. As the industry looks ahead to the next decade, continued innovation will be the key to producing complex wells with improved efficiency and safety.
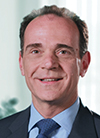
TEOMAN ALTINKOPRU is vice president, well intervention marketing and technology, at Schlumberger. Prior to attaining this position, Altinkopru held several managerial posts at Schlumberger, including marketing manager and marketing & technology manager for coiled tubing services, and later vice president for coiled tubing services. He has overseen operational activities in various Schlumberger markets as manager of recruiting, training and development in Paris; oil field services GeoMarket manager in the United Arab Emirates, Pakistan, Oman and Yemen; and GeoMarket operations manager in Azerbaijan, Kazakhstan, Georgia, Turkey, India, United Arab Emirates, Oman, Yemen and Qatar. Altinkopru holds a bachelor’s in electrical engineering from Middle East Technical University in Turkey.
For other great articles about exploration, drilling, completions and production, subscribe to The American Oil & Gas Reporter and bookmark www.aogr.com.