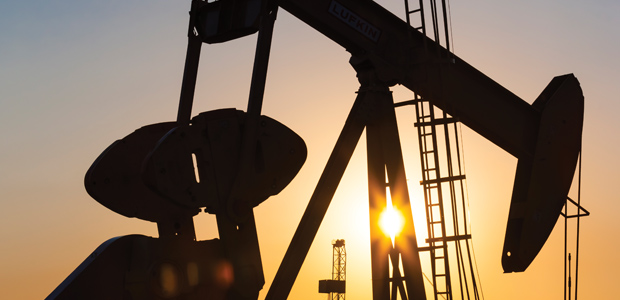
Developing Tools, Practices For Artificial Lift Applications Critical In Horizontal Wells
By Cleon Dunham and Cem Sarica
The vast majority of the wells being drilled for both oil and gas production in unconventional plays are horizontal. At some point, most of these wells will require artificial lift to produce the liquid hydrocarbons and/or dewater the gas wells, but artificial lift in horizontal wells is still an evolving science. It can be particularly challenging in shale assets, where wells are often deep with long horizontal sections.
Several methods of artificial lift have been deployed in these wells, from rod pumps to electric submersible pumps and gas lift. Some have proven more successful than others, depending on the application. All these lift methods are time proven to produce from vertical and deviated well bores, and companies are trying to extend the lessons learned from these experiences to produce horizontal wells.
What is the significance of artificial lift in producing horizontal wells? Simply put, half of the natural gas produced in the United States is expected to come from horizontal unconventional plays by 2030, including very tight sands and shales. On the oil side, new supplies from horizontal resource plays are growing rapidly, and have the potential to displace a significant percentage of oil imports in the domestic market.
In 2005, the majority of U.S. shale gas production came from four basins: the San Juan in New Mexico and Colorado (55 million cubic feet a day), the Antrim in Michigan (384 MMcf/d), Appalachian/Ohio shales (438 MMcf/d), and the Barnett in the Fort Worth Basin (1,233 MMcf/d). Today, the list of U.S. gas shale plays includes the Marcellus and Devonian in the Appalachian Basin, the Utica in Ohio and Pennsylvania, the Mowry in the Powder River Basin, the Mancos in the Uinta Basin, the Woodford in the Ardmore Basin, the Floyd/Neal in the Black Warrior Basin, the Bone Spring and Cline in the Permian Basin, the New Albany in the Illinois Basin, and of course, the Eagle Ford in south-central Texas.
Many more shale formations are being explored across North America and around the world, and several are demonstrating the capacity to hold significant reserves.
Production Challenges
After hydraulic fracturing in the lateral section to interconnect natural fractures with the well bore, only 20-25 percent of the total fracturing fluid volumes pumped during treatment normally are recovered at the surface as the well begins producing. The rest of the injected fluid spreads into the reservoir.
Experience in gas shale plays indicates wells may produce water long after a fracturing operation concludes. Moreover, the formations below or above the shale formations may have water. During fracturing operations, fractures may extend to water-bearing formations and result in continuous water production through the life of the well. Even worse, fracturing in one well may interfere with the production operations of neighboring wells by accelerating loading problems along the lateral sections.
In addition, water can be present naturally in oil and gas formations. In some shales, water is mixed with the gas and needs to be removed to produce the gas effectively. For instance, Barnett Shale gas wells can produce significant amounts of water. U.S. Geological Survey data indicate that some gas wells can produce up to 39 barrels of water per Mcf of gas. In Denton County, Tx., gas wells produce even more water (up to 53 bbl/Mcf). Devon Energy Corp. reports that in its Barnett Shale operations, some amount of water is produced over the life of the wells, with water volumes varying from trace amounts to 400-500 bbl/d.
One company producing gas from the New Albany shale in the Illinois Basin has reported that peak gas production is achieved after six to 12 months of dewatering. The Antrim Shale in Michigan also contains water that must be removed to achieve maximum gas production.
Oil production from tight sands and oil shale formations has been increasing significantly in recent years as producers transform their operations to focus on developing oil reserves. As with natural gas, most of the wells being drilled to produce oil are horizontals, and the challenges associated with tight oil horizontal wells resemble the issues associated with shale gas horizontal wells.
Horizontal Well Artificial Lift
Water in gas wells hinders production unless it is removed. Therefore, liquid unloading in gas wells is one of the most important production and artificial lift challenges. Unloading is especially challenging and not well understood in the horizontal portions of wells. There are several factors affecting water flow. Relatively low gas production rates make water flow difficult to maintain, and water may accumulate in the horizontal sections, resulting in back pressure on the formation. In some instances, it may even flow back into the formation.
Compounding the challenge is that horizontal wells often have undulating trajectories that create unintended low spots for water to accumulate that is then difficult, if not impossible, to remove (Figure 1). Moreover, the heel of horizontal wells sometimes can be shallower than the toe. This requires water to flow “uphill” in the horizontal portion of the well (Figure 2). For the low gas flow rates typically produced as the wells mature, water is inevitably expected to accumulate at the toe of the well. There is no reliable model or software tool to predict the unloading of horizontal wells. Developing such a tool requires an accurate understanding of the hydrodynamic interplay between the gas and the water.
For oil-dominated petroleum systems, there are unique operating issues that impact decisions concerning production operations and the choice of artificial lift method. Similar to gas-dominated systems, these systems require better characterization of the flow of various phases in the horizontal well. Some specific issues are:
- Determining horizontal well trajectory (i.e., whether to drill horizontal wells with a toe-up or toe-down trajectory);
- Identifying the existence of terrain induced slugging and its ramifications;
- Placing the artificial lift equipment in the well;
- Scale formation;
- Corrosion;
- Foaming;
- Asphaltene and paraffin deposition; and
- Frac sand/proppant production.
New Practices Needed
Artificial lift techniques for horizontal wells are based mostly on practices established in vertical wells, although often without acknowledging the fundamental differences. The pros and cons of various techniques in horizontals are not well established, and modeling tools for comparing the performance of different techniques are lacking for horizontal wells.
Moreover, there is no consensus within the industry as to whether lateral sections should be drilled with the toe up or down. Various artificial lift scenarios have been envisioned, including drilling sumps in the vertical section to place artificial lift equipment before the heel of the well; placing artificial lift equipment in the lateral section, and placing artificial lift equipment in the toe.
The type of artificial lift system employed in a well greatly influences its suitability for placement. In addition, the well design (casing size, hole angle build rate, dogleg severity, etc.), as well as reservoir performance, affects the choice and placement of artificial lift equipment. Industry trends include rod pumping, hydraulic pumping, progressing cavity pumping, electric submersible pumping, plunger lift, gas lift, and foam as the means for pumping or removing liquids from horizontal wells. Each form of artificial lift has associated constraints or limitations. These have been identified with screening criteria for vertical or near-vertical wells. Similar criteria are needed specifically for horizontal wells.
The placement of the end-of-tubing, the location of the artificial lift equipment (pump, gas lift), and casing size all influence the scope and success of artificial lift. Horizontal well trajectory impacts the flow regimes occurring along the well bore, the effectiveness and location of artificial lift equipment, and ultimately, the well’s capacity and ultimate recovery. In many cases, the horizontal well trajectory is dictated by drilling location and reservoir architecture. Any compromise between the two needs to be struck early on in field development, and requires clear qualification and quantification of the impact of trajectory on artificial lift success. One solution to optimize any trajectory is drilling a sump to locate artificial lift equipment.
Recommended practices for horizontal wells can be either experience-based or model-based. Model-based optimization starts with understanding the multiphase and transient flow phenomena that occur in horizontal wells. The critical rate in horizontal wells differs from the critical rate in vertical wells, and will impact the onset of liquid loading, among other things. Artificial lift techniques are intended to unload the liquids by changing the behavior of multiphase flow. Therefore, the flow behavior is a key to understanding and helping design the artificial lift techniques.
New Artificial Lift Consortium
An industry survey was conducted to determine interest in gaining a more thorough understanding of artificial lift in horizontal wells. Specifically, survey respondents expressed interests in:
- Helping select optimum method(s) of artificial lift for horizontal wells;
- Understanding flow regimes and critical rates in horizontal wells;
- Recommending optimum horizontal well geometry and well bore trajectory;
- Recommending placement of end-of-tubing, location for artificial lift, and casing size;
- Summarizing industry learnings and literature information;
- Recommending when to start artificial lift operations in horizontal wells; and
- Developing training materials and courses for engineers and operators associated with horizontal wells.
With this in mind, a new horizontal well artificial lift consortium, officially known as the Tulsa University Horizontal Well Artificial Lift Projects (TUHWALP), has been established with the purpose of developing an improved understanding of issues for producing horizontal oil and gas wells, especially where artificial lift is required. The research is conducted primarily at the University of Tulsa. The consortium has 17 member companies and the number is expected to grow (Table 1). The results of the research projects are provided to member companies.
The consortium has been formed to work cooperatively to advance the knowledge and effectiveness of the personnel who design and operate horizontal oil and gas wells, and to develop recommended practices for artificial lift of horizontal wells with objectives to:
- Improve design and operability of artificial lift for horizontal wells;
- Improve selection, deployment, operation, monitoring, control and maintenance of artificial lift systems; and
- Recommend artificial lift practices to optimize the recovery of oil, natural gas and associated liquids from horizontal wells.
TUHWALP is addressing these issues with three research projects to investigate multiphase flow behavior in horizontal wells; investigate artificial lift techniques in horizontal wells to help select optimum lift methods, place end-of-tubing and artificial lift equipment, determine casing size, design well construction, and assess the applicability of various artificial lift techniques; and develop guidelines and recommended practices for horizontal wells by summarizing industry learning/literature, and determine when to start artificial lift operations in horizontal wells.
Projects Overview
The project objectives of the multiphase flow behavior research are to investigate multiphase flow characteristics for horizontal oil and gas wells experimentally/theoretically and how they are affected by well geometry or trajectory, develop mechanistic liquid loading criteria for horizontal gas wells, develop a multiphase flow model that simulates multiphase flow in horizontal wells, and develop a predictive software tool that incorporates model development results.
Experimental study includes simulating operating conditions of horizontal wells using a facility consisting of a 17.6-meter long pipe connected to a 12.5-meter riser with a 2.0-inch diameter. The maximum allowable inclination angles are ±3 degrees. The facility includes at least two undulations (one undulation consists of one downward and one upward inclined pipe with a dip), both gas and liquid feeds along the test section to mimic horizontal well fractures, and both toe-up and toe-down configurations.
Tests will be performed for various gas and liquid flow rate combinations that are typical of horizontal well production to investigate flow behavior and liquid loading/unloading conditions. This will produce an experimental map of liquid loading. Toe-up, toe-down and flat configurations will be studied. A physics-based mechanistic model will be developed to characterize flow and predict liquid loading.
Project deliverables include understanding two-phase gas-liquid flow in horizontal wells, developing modeling and software tools to predict flow behavior, understanding liquid loading in horizontal wells and liquid loading criteria, generating experimental data, and providing guidance to determine optimum horizontal well geometry.
The objectives of the project to investigate artificial lift techniques in horizontal wells include experimentally and theoretically investigating the performance of various artificial lift techniques, developing performance evaluation tools based on flow dynamics and well construction profiles, and generating an artificial lift method selection criteria “road map,” based on field data as well as experimental and theoretical results.
The project will simulate operating conditions of horizontal wells using a large-scale facility. Liquids will be pumped from a storage tank and mixed with compressed air at the inlet of a 250-foot, 6.0-inch inside diameter lateral section. A 30-foot tall riser will follow the lateral section. Twelve supports will be spaced equally throughout the lateral section. These supports are 15 feet tall and are equipped with a pulley to facilitate modifying the well trajectory. This configuration allows the simulation of at least two undulations: toe-up and toe-down configurations with a maximum of 3.0 degrees of inclination. The facility will be able to incorporate and test various artificial lift methods.
Tests will be performed for various gas and liquid flow rate combinations that are typical of horizontal gas and oil wells, seeking to produce efficacy measures of various artificial lift methods. A detailed test matrix will be developed, based on the artificial lift methods investigated. Physics-based mechanistic models will be developed to predict the efficacy of various artificial lift methods.
Project deliverables include assessing the unloading performance of various artificial lift methods and their comparative analysis, tubing insert, surfactants, pumping systems, gas lift, the impact of slugging, generating experimental data, and analyzing setting locations for artificial lift equipment.
The third TUHWALP project seeks to develop guidelines and recommended practices for selecting artificial lift techniques. The project plan includes gathering data on field practices in horizontal well artificial lift, developing a database on the performance of various artificial lift practices, and testing the performance of various practices with the model simulations.
Deliverables include creating a database consisting of both field and experimental data, analyzing the data, and generating guidelines and recommended practices based on field and experimental data.
As part of the consortium’s research, there is interested in having an actual horizontal well to test and evaluate the project findings. There are a number of possibilities for implementing a horizontal test well. One being discussed is to drill a horizontal extension to the vertical Red Raider No. 1 test well at Texas Tech University. The university is willing, but the task now is to design the horizontal extension and find companies willing to contribute the drilling, completion and lift equipment.
Significant Strides
In spite of the many problems associated with using artificial lift systems in horizontal wells, the industry is making significant strides with many types of lift technology.
In regard to sucker rod pumping, despite the fact that conventional wisdom holds that sucker rod pumping only works in vertical or slightly deviated wells, it is being used in horizontal wells with the aid of innovations such as new types of rod guides and rod centralizers that allow pumps and associated sucker rods to operate in highly deviated and even horizontal wells, and improved packer-type gas separators that allow pumps to work when there is gas slugging in the horizontal sections.
Electric submersible pumps also can be used in highly deviated and horizontal wells, as long as the ESP system is installed in a straight section of pipe and gas interference can be addressed effectively with gas separators. Another approach is to install the pump in the vertical part of the well with an inverted shroud above the pump. Gas and liquid flow between the outside diameter of the shroud and the casing, with liquid flowing back down between the shroud’s inside diameter and the pump until it enters the pump. The motor is installed below the shroud so liquid and gas can flow past it for cooling.
New types of hydraulic pumping systems allow control of inflow along the entire horizontal section of a well, including in association with inflow from all hydraulically fractured locations. Progressing cavity pumps also are being used in horizontal wells with the aid of improved rod guides and centralizers, as long as temperature criteria are met and the wells are not allowed to “pump off” (which can cause overheating and swelling of pump elastomers).
Gas lift can be especially effective in horizontal wells, with the injected gas helping move liquids out of the horizontal section to avoid liquids buildup in low spots in the lateral. New gas lift designs use large tubes below the packer in deviated and horizontal wells to maintain critical flow rates in the smaller cross-sectional flow area. Special methods, including coiled tubing and well tractors, are used to install gas lift valves in highly deviated and horizontal wells, since wireline techniques are effective only in well bore deviations of less than 65-70 degrees.
Tubing plungers are being deployed in highly deviated wells as the fall of the plungers is better understood. Methods are being deployed to inject chemical agents for foaming into horizontal wells. Chemical cocktails are being formulated to address corrosion, scales, asphaltenes, etc., in addition to helping produce the wells.
Finally, in terms of well design, some companies are completing wells with sumps at the bottom of the vertical portion, before the turn to the horizontal section. Pumps are installed in the sumps to produce liquid while gas flows from the horizontal to the vertical section, above the location of the pump.
Editor’s Note: For detailed information on TUHWALP, visit http://tuhwalp.ens.utulsa.edu/index.html.
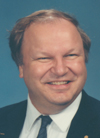
CLEON DUNHAM is president, chief executive officer and secretary of the Artificial Lift Research & Development Council. Dunham retired from Shell Oil Co. after a 36-year career in facility, reservoir, production and computer control engineering, with a primary focus on production automation and artificial lift. He spent the past five years of his career with Shell International E&P in The Hague, Netherlands, where he helped coordinate Shell’s worldwide production automation and artificial lift activities. He is a member of work groups of both the American Petroleum Institute and International Standards Organization for writing standards and recommended practices for gas lift. Dunham holds a B.S. in engineering from Cornell University.
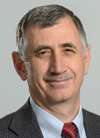
CEM SARICA is a professor of petroleum engineering and the F.H. “Mick” Merelli/Cimarex Energy Endowed Chair in the McDougall School of Petroleum Engineering at the University of Tulsa. He is also director of three industry-supported consortia at the University of Tulsa on horizontal well artificial lift, fluid flow, and paraffin deposition projects. Sarica was an associate professor of petroleum and natural gas engineering at Pennsylvania State University, and was an assistant professor at the Istanbul Technical University before joining Tulsa University. He was recognized as a Society of Petroleum Engineers Distinguished Member in 2012, and was the recipient of the 2010 SPE International Production and Operations Award. Sarica is a member of SPE’s Projects, Facilities & Construction Advisory Committee. He holds a B.S. and an M.S. in petroleum engineering from Istanbul Technical University, and a Ph.D. in petroleum engineering from the University of Tulsa.
For other great articles about exploration, drilling, completions and production, subscribe to The American Oil & Gas Reporter and bookmark www.aogr.com.