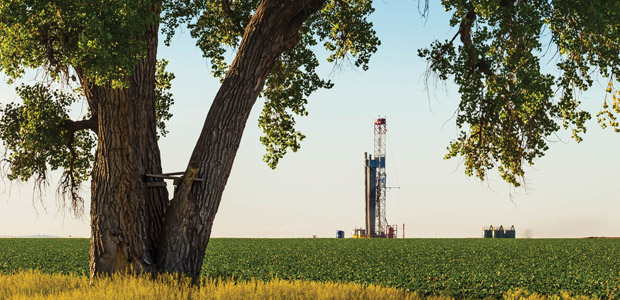
Horizontal Wellbore Construction
Drilling Strategies, Technologies Improve Performance In High-Yield Resource Plays
By Allen Gilmer and Phillip Dunning
AUSTIN, TX.–As the industry has wrestled with the “new normal” of lower commodity prices and uncertainties regarding long-term forward pricing, it is hugely important to identify some of the improvements in processes and technologies that both operators and service companies are embedding into their operations.
Learning best practices, lowering authorization for expenditure and operating costs, and improving per-well productivities are all foundational drivers of stay-in-the-game business practices that will improve margins when prices do finally recover.
Every financial analyst call or 10Q quarterly report from publicly traded oil and gas companies states that operators have reduced their drilling costs. A large part of the savings has come from the pricing discounts that oil field service companies have made, in many cases simply to keep the lights on and their workforces in place.
However, it is not only pricing concessions that have helped improve margins. Whereas the industry became monomaniacal in its focus on reducing costs, the smartest operators have focused on the entire equation and the metric of dollars they spend producing each barrel of oil or Mcf of natural gas. The range of solutions that operators and service companies have brought to the table run the gamut from enterprise-level decisions to tactics to reduce the operating costs associated with a particular asset.
On an enterprise level, perhaps the most significant improvement has been the happy coincidence that great geology has allowed oil and gas companies to focus on new high-yield resource plays in mature basins with solid supply chains and well-developed infrastructure. The most obvious example, of course, is the Permian Basin, which accounted for roughly half of all active U.S. oil rigs as summer began. Mature basins have a hidden value multiplier since there are usually up-hole “stacked” targets that operators can plug back to later and complete without incurring the cost of acreage (the acreage is held by production, unless there are Pugh clause complications), surface infrastructure or initial vertical wellbore drilling costs.
Figure 1 displays a map of Texas Railroad Commission districts 7C and 8. It illustrates very clearly how many different reservoirs produce in the Midland and Delaware sub-basins as well as on the Central Basin Platform. The multiple stacked productive zones can total in excess of 4,500 gross feet and give operators a dozen or more potential reservoir targets.
Focusing On Efficiency
On a tactical level, drilling companies have begun to do more mobilization/demobilization work at night when the roads are less crowded, and rigs can get on and off site more efficiently, trimming downtime.
In another example, service companies of all stripes have been evaluating operational efficiencies in the search for margin, including the process automation of certain aspects of the drilling operation. A case in point is automated pipe connection systems, which are improving overall drilling speed efficiencies as much as 10-15 percent. Even smaller drillers can achieve these efficiency gains easily through connection time optimization.
Containerized solutions for handling proppant on location are a good example of a technology that is improving efficiency in well completion and stimulation. These systems deliver proppant to the job site in containers that can be emptied easily and quickly, reducing costs, operational footprints, truck traffic and proppant loss while also decreasing site personnel’s silica dust exposure.
However, the biggest operational improvements have come from fracturing a much smaller volume of rock much more thoroughly. The use of an old technology, chemical diverter agents, to focus frac intensity around the wellbore and create a complex, interwoven frac network is increasing recoverabilities significantly in horizontal tight oil and shale gas plays.
A number of new diverting agents are being brought to the market. Some are designed to provide temporary zonal isolation and fluid diversion to newly stimulated perforation clusters to reduce the number of required perforating runs and plugs. Others create a “webbing” effect to help prevent proppant flowback or temporarily block existing fractures to complete untreated sections of laterals and increase stimulated reservoir volumes.
Proppant makeup also has changed in the past few years, with pure sand applications increasing as a result of its lower cost. However, operators are undertaking a variety of experiments using tails of ceramic and resin-coated proppants, which are designed to help maintain near-wellbore conductivity over time by reducing proppant flowback. The use of mixed proppant in frac jobs also has allowed smaller fractures to be stimulated and kept open by pushing fine-grained (100-plus mesh) sand first and then using 40/70 mesh or other coarser proppants later. The finer mesh is supposed to flow easier in the presence of natural fractures, allowing for a more complex fracture network and opening reservoir volume to flow.
The increase in “zipper” fracs (fracturing adjacent multistage horizontal wells in sequence, with one well holding pressure while the adjacent well is fractured) is helping develop a more robust wellbore-to-wellbore fracture network, increasing individual well returns 5-15 percent in some cases.
Staying In Zone
With newer logging-while-drilling and geosteering tools, bottom-hole drilling assemblies are able to stay in the target zone and more accurately steer laterals to planned depth. In some instances, this is allowing frac treatments to stimulate more of the reservoir, resulting in higher production. Even when not in zone, completion crews are able to engineer completions with the net effect of minimizing fracturing in non-prospective zones. For instance, if the wellbore has been steered high in the target zone, completion crews can orient perforating guns downward to focus all the frac energy in the direction of the target reservoir. The real-time tower data provided by the drillers also can be used to create synthetic logs that can help completion engineers understand stress regimes in real time to better plan perf clusters.
As operators seek to extract maximum value from the reservoir rock in their lease inventories, many have experimented with and implemented downspacing strategies. In other words, they are drilling more densely on their leases by reducing well spacing in an attempt to effectively stimulate the rock volume between lateral sections. In more mature basins such as the Eagle Ford in South Texas and Niobrara in the Denver-Julesburg, it is not uncommon to see spacing of 80 acres or less. Nevertheless, some cases show signs of diminishing returns with downspacing in certain areas and plays.
The major issue is wellbore connectivity. Zipper fracs work best when the original wellbores are drilled in a proximate time frame. Exposing a wellbore exhibiting high pressure to an older one exhibiting low pressure can hurt overall productivity, while intercalating the frac networks of two higher-pressure wells can result in “positive interference” (producing more hydrocarbon than originally expected). Unfortunately, in many older plays, this means significant resources will be left behind, because fracturing new wells mostly will reactivate older fracs rather than break new rock.
In newer resource plays such as the Delaware Basin, where operators are still delineating proven zones, it will take a while before negative downspacing issues arise, and hopefully, lessons learned will boost recoveries considerably. But such a play also will raise the most questions. With multiple major formations and multiple subformations, initial well placement and spacing will play a big role in where future wells will be drilled.
For companies to book the highest proved undeveloped reserves, they will need to prove not only the economic reservoir benches, but also the most efficient spacing plans to show that the wells can be placed to yield the highest dollar return. New well/pad planning and reservoir characterization tools will allow companies to better produce these stacked plays and optimally produce the existing resource.
Big Data And Best Practices
Big data and analytics technologies have helped operators zero in on best practices, and importantly, learn from one anothers’ experiences. For example, total proppant volumes in Bone Spring reservoirs in the Delaware Basin look to have normalized to around 1,500 pounds per foot of perforated interval (Figure 2).
In the meantime, Bone Spring estimated ultimate recovery values per foot of perforated interval appear to be best maximized at lateral lengths of 4,500-5,000 feet (normalized by perforated interval feet), with the highest values in Lea County, N.M., and Loving County, Tx. (Figure 3)
The insights available from big data allow operators to focus their investment dollars on completion and drilling practices that deliver results, and avoid overspending on techniques and practices that waste money without bringing in added revenue from increased production.
This is critical, because the point of having access to big data is to find previously unknown drivers that illuminate how operations deliver bottom-line dollars. The ability to effectively learn from not only internal operations, but from competitors’ experiences, differentiates best-of-breed companies from average companies. Now, operators easily can discover who is learning (and optimizing) the fastest over time, and emulate their completion practices.
For example, the graph in Figure 4 shows the net production added over time for three operators in the Delaware Basin. Note that for one of the operators, production volumes by well increased markedly (the red circle defines the behavior inflection point) at around well number 85. Determining what changes this company has made before and after that well can pay huge dividends to other operators that are willing to learn from their peers.
Optimizing Operations
In most cases, these impacts are geology-specific and nonlinear. What does that mean? First, it means that rocks matter, and the formula that optimizes production in one location may not be the same two sections away. Acquiring 3-D seismic data is a very small cost to incur in order to squeeze out an extra 150,000 barrels of production from each location.
Second, it means that operators run the risk of spending too much or too little. In a study of several plays, we observed that the very best operators were around 80 percent optimized relative to criteria that actually could be examined. The average operators got about half right, and the lowest performers were only 10-20 percent optimized.
In one particular case in the Eagle Ford that involved roughly 100 wells, it was possible to show where operators overspent by an average of $500,000-$600,000 a well by applying various stimulation parameters far beyond the return breakeven. On top of this, had they reallocated $150,000 a well of that to another part of the equation that still offered return-on-investment gains for each dollar spent, they could have produced significant incremental oil at a cost below $2 a barrel.
Such insights derivable from big data allow operators to focus their dollars on completion and drilling practices that deliver results, and not overspend on techniques and practices that mar well economics by failing to yield incremental production gains. Operators that rely on a formulaic “cookbook” for drilling and completion procedures destroy value and condemn acreage by their bad practices.
Unconventional oil and gas is certainly the planet’s oyster, and companies that avoid the 10, or 100 or even 1,000 well cookbook will be certain winners. Operators that are nimble and quick to learn from their results, and that can adapt quickly to changing cost conditions–or maybe more importantly, to subtle geological and petrophysical variabilities in their acreage blocks–will be the most important companies in the world.
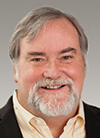
ALLEN GILMER is co-founder and chairman of Drillinginfo. He is active in all aspects of Drillinginfo’s new product development and is recognized widely for his industry leadership and vision. Gilmer holds several patents in multicomponent seismology. He received a B.A. in geology from Rice University and an M.S. in geology from The University of Texas at El Paso.
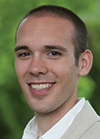
PHILLIP DUNNING is a technical adviser at Drillinginfo and an engineering officer in the U.S. Army. He also is a partner in PD Drilling & Exploration. Dunning holds a B.S. in civil engineering from Ohio State University and an M.S. in petroleum engineering from the University of Louisiana at Lafayette.
For other great articles about exploration, drilling, completions and production, subscribe to The American Oil & Gas Reporter and bookmark www.aogr.com.