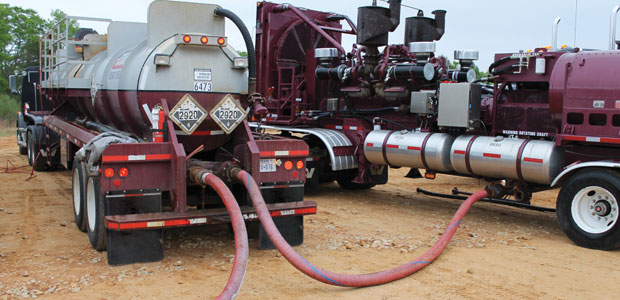
Production Restarts
Fiscal, Technical Issues Define Operator Strategies In Restarting Shut-In Wells
By Doug Walser
TOMBALL, TX.–U.S. producers of all sizes responded to the economic shutdown and sub-breakeven commodity prices by dramatically cutting back budgets for drilling and completing new wells, and by shutting in or restricting flow from producing wells. The large number of wells that were shut in from mid-March through early May ranged from marginal vertical producers to higher-rate horizontals. However, uncertainty with respect to the ability to restore comparable production in a higher-price environment resulted in some degree of hesitation to shut in older horizontal wells.
Mid-sized and larger operators with multiple acreage positions have the luxury of choice in the production restoration triage process as commodity prices recover. The most active operators have impacted a large percentage of their total production cuts by working exclusively with drilling and completion curtailment and newer producing wells, leaving midlife and legacy producers untouched, or at most, implementing slowdowns in those wells. Smaller operators and others with limited acreage and play coverage simply have few options in assuring minimal loss of reserves when commodity prices reach the point where economics warrant well restarts.
During the initial triage process, separating technical risk from purely financial risk is a reasonably straightforward process. The purely fiscal decisions that are made regarding the choice of wells to shut in (or from which to restrict flow) are well known, and include the aggressiveness and terms of hedging programs in place, the degree and nature of offset competitive activity, held by production (HBP) issues, and contractual lease and midstream obligations. Other issues also taken into consideration are of varying degrees of importance.
For example, some regulatory entities have momentarily relaxed restrictions on temporary abandonment, active well definitions and reporting requirements. The operator’s capital funding source, under some circumstances, can impose an overriding (and even debilitating) set of restrictions on the various options available. Royalty owners can cause difficulties if the lease does not have a shut-in royalty provision or amendment. Occasionally, even public perception issues can become enablers for decisions on shut-ins and slowdowns.
Technical Considerations
The technical issues that an operator faces in well shut-in and production restoration are not as clear cut as the purely fiscal drivers, and nice, clean net present value calculations are not really possible for each and every branch of a given decision tree. Large operators with several active operations and multiple plays can slash budgets for their development drilling and completion programs, but not indiscriminately.
Undrilled proved-but-undeveloped (PUD) and drilled-but-uncompleted (DUC) locations that are located immediately adjacent to existing producers are at substantial risk of pressure-related, asymmetric-induced fracturing in the future as new wells are hydraulically stimulated. The asymmetric fracturing results in the sharing of reserves between the DUC (child) and the existing parent producer as well as a statistical loss of reserves, typically on the order of 10-25% of expected estimated ultimate recoveries. In addition, intense competitive activity along lease line borders can be a very real issue in “rule of capture” scenarios, especially when shutdowns and restarts do not occur in parallel time frames.
Recently stimulated completions in many plays demonstrate a marked resilience when it comes to retained productivity after extended shutdowns. The Bakken, in particular, has experienced multiple midstream related production interruptions with negligible reported degradation in production decline curve character after re-opening. Public data on Wolfcamp and Spraberry production is often difficult to interpret, but individual testimonies suggest that newer wells have their production restored after shut ins with no negative repercussions, as long as immediate offsets undergo the same shut ins over the same period.
Recently completed oil wells face an operational hazard that is unique to their age and to the means of applying artificial lift. Electric submersible pumps generally are deployed in a wellbore after the bottom-hole producing pressure drops close to the hydrostatic head (weight) of the column of produced fluids. Even after several years of continuous improvement to ESP design and engineering, these pumps can be finicky if they suddenly are asked to start again after a prolonged shutdown. In addition, ESPs typically operate within a relatively tight band of production rates, and therefore slowdowns can be problematic.
It is well known that conventional vertical wells perforated in multiple stacked reservoirs almost always will experience crossflow between reservoirs of differing pore pressure gradients during every shut-in period, and the transfer of fluids back to the wellbore after production restoration is not usually very efficient or complete. The degree to which reserves are permanently lost depends on permeability in each reservoir, the reservoirs’ thicknesses, and the pore pressure differential between them. Crossflow is also an issue in horizontal well drainage volumes, but it is not usually between separate reservoirs.
In a horizontal drainage volume in a single stratigraphic reservoir, there are usually wide variations in permeability, most often caused by variable natural fracturing density and differences in the placement and degree of propped stimulation. Along a given horizontal wellbore, therefore, the wellbore drains some portions of the reservoir substantially more efficiently than others during its early history. When the wellbore is shut in, pressure tends to equalize. Upon restoring production, a substantial period of time is sometimes required for the wellbore pressure distribution to return to its former character. Unfortunately, it is not clear where this will be a real issue, or how it can be measured, mitigated or forecasted.
Some researchers have highlighted the negative impact of cyclical shut-ins and restarts on the stability of proppant packs and subsequent decreased production tied to the proppant damage. It is probable that these concerns are valid in more conventional wells when the reservoirs of interest have moderate to high permeability, and the proppant is not of sufficient quality to withstand the closure stress imposed upon it. However, most North American unconventional production scenarios are not deeply dependent on high fracture conductivity for success, and an extended shut-in followed by resumption of production should not be expected to have substantial geomechanical stress-related issues.
Midlife Wells
The vast majority of unconventional producers decline in a semi-predicable manner because of pressure depletion. Within a few short years (or even months), these wells become subject to their own class of unique challenges. Among those changes is a potential change in reservoir rock wettability in and near propped fractures. From a statistical point of view, it appears that connate (bound) water often decreases and free water increases. The result is that in several plays across North America, water-to-oil ratios and water-to-gas ratios increase upon restoration of production after extended shut-in periods. The degree to which this is a problem appears to be localized to plays where wettability is easily altered or reversed.
Operators often utilize a mandatory shutdown initiated by midstream or surface facilities as an excuse to perform needed subsurface repair, so it could be difficult to attribute increased water to this specific phenomenon from public data alone.
Midlife producing wells also can suffer from surface facilities degradation, and in a little-appreciated twist, that rate of degradation can accelerate during prolonged shut-in periods as a result of exposure to oxygen inside equipment that was not present during active production and a number of minor, but additive factors.
High-rate gas wells that produce water are healthy and happy, as long as they are lifting produced water in what is known as “mist flow.” As pore pressures decrease, production rates decrease, and at some time in middle or late life, there comes a point where the mist becomes a slug. Liquid loading from that point forward is the bane of the producer. For these wells, a slowdown or shut-in must eventually lead to some sort of artificial lift expenditure to kick-off the well once prices sufficiently improve.
Both oil and gas wells in the midlife production period face the same parent-child risk of EUR loss due to asymmetric fracturing of a DUC or PUD offset–except that in this case, the loss is in the future when the offset is stimulated. There is no evidence to support a generalization that simply shutting in a midlife well helps to prevent the asymmetric fracturing and loss of recoverable reserves.
Legacy Wells
As production curves for both oil and gas wells flatten out at just barely commercial rates, there are a multitude of events that can trigger an end-of-life scenario. For legacy stripper oil wells, artificial lift (rods, pump or tubular failure) is the most frequent cause of permanent production cessation. However, the nature of rod-pumped completions is such that they are built for intermittent pumping, so this class of wells may not be particularly impacted by extended shut-ins and subsequent restarts. A fiscal consideration stemming from this is that a well just barely inside the definition of a stripper for tax purposes might be bumped out of that classification if the transient bump in production after restarting increases the annual average to outside that classification range.
As with midlife wells, further degradation of surface facilities can become an issue with older wells. An extended shutdown followed by a restart often brings to light mechanical issues that may have been present during the later stages of production, but were not detected. These may include leaks, corrosion, erosion or even functionality of the measurement devices themselves.
For a legacy gas well, the endpoint of life is most often severe liquid loading, scale, sanding up or a hole in the vertical portion of tubulars. The trigger for such events is typically an extended shut-in due to unforeseen circumstances. Like the midlife gas well scenario, a legacy gas well is statistically subject to watering out. Although the root or contributing causes could be mechanical in nature, changes in wettability are possible, largely because of various interventions over the years, many of which contain a plethora of surface active agents.
Several operators with large inventories of legacy gas wells have developed decision trees that assist in accelerating the decision making process by “databasing” and updating costs of various remedial actions–including plugging–in order to obtain a quick look at NPV and/or cash flow associated with end-of-life action steps. In this case, remedial work is almost always a negative NPV proposition. Consequently, most operators have elected to completely avoid shut-ins or slowdowns of this classification of wells.
Older oil and gas legacy wells also can face the same issues with respect to crossflow, and with respect to interaction with offset producers during shut-in periods, but usually to a lesser degree than they would have earlier in their life cycles. Most geomechanical experts agree that stress effects likely have minimal impact on legacy producers, even with repeated cycling of production.
Miscellaneous Issues
There are a few other miscellaneous subsurface equipment issues that may pop up as a result of extended shut-in periods followed by restarts, namely tubular corrosion at the fluid interface and seal failures.
In regard to tubular corrosion, nearly all unconventional and conventional wells alike produce at least two phases (gas and water/oil and water/gas and oil) and sometimes three (oil, gas and water). When a well is shut in, the fluids in the wellbore do not immediately cease their movement. Phase separation begins, and pressure equalization continues for some time.
Eventually, however, fluid movement is negligible, and the interface between oil and water or between gas and water can promote steel tubular goods corrosion. Anaerobic bacteria, or the presence of even minute amounts of dissolved oxygen or carbon dioxide, can initiate corrosion that ends up impacting tubular integrity upon restarting a well.
Occasionally, engineered seals are placed in downhole equipment to facilitate the isolation of different pressure environments. Over the years, dramatic improvements in sealing material technologies have resulted in outstanding performance over long service periods in hostile temperature and pressure differentials. However, the enemy of these products is not the extreme pressure or temperature or movement, but changes in extreme temperature or pressure or movement. A prolonged shut-in, followed by a restart with wild temperature, pressure and movement can be the trigger that initiates failure.
Key Takeaways
The COVID-19 lockdown and commodity price slide produced a completely unforeseen and unexpected result: an avalanche of webinars and online workshops for industry professionals, along with the free time required to participate in them. One of the subject matters covered by several of these online events was the impact of slowdowns and shutdowns on both production rates and EURs. There were several key takeaways from the information presented, and quite a few concepts were systemically noted.
For instance, when considering wells that have not yet been drilled, DUCs and new producers, the primary drivers for the well triage process are purely fiscal, as opposed to technical. A slowdown is generally preferable to a shutdown in relatively new wells, since choking back high-rate producers is a relatively simple operation with low technical risk from a recoverable reserves standpoint.
A few large and mid-size operators were reportedly comfortable with simply adjusting their active drilling and completions operations in the downward direction, as opposed to a strong emphasis on working with existing producers. The various reasoning provided for this was not uniform. Some claimed lack of manpower, and some cited an inability to quantify the risks associated with restarts. Others said that the contractual and regulatory complexities associated with shutting in existing producers were overwhelming.
The parent-child well interaction dilemma was the single biggest technical obstacle to executing new undrilled PUD and DUC decisions. This is understandable, given that reserves lost to asymmetric fracturing from a child development well toward an existing producer at its midlife point can meet the definition of “fiscally material” if repeated over dozens or hundreds of drainage areas.
From a technical perspective, it is clear that legacy and midlife wells are the most difficult scenarios to work. Operators in states that have provided regulatory relief by extending allowable shut-in periods for this class of wells may have more options available as commodity prices improve. As noted, unconventional gas wells face more technical restart issues at midlife than do unconventional oil, primarily because of liquid loading.
Smaller operators without significant drilling and completion programs need to assess the technical risks associated with restarts of midlife and mature wells, even if it means that the assessment is partly qualitative. If there are multiple reservoir types, fluids and well construction practices, then the assessment should look at each of the potential parameters that could impact the recovery rates and EURs of the wells in question.
The domestic industry already has demonstrated to the rest of the world that restricting flow from unconventional wells is best enabled by restricting the rate of drilling, stimulation and completion. The primary drivers are fiscal, as opposed to technical. However, for the large number of wells that have been shut in, operators will have to evaluate both technical and financial considerations as they start bringing assets back on line and restoring productivity.
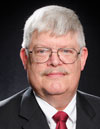
DOUG WALSER is a subsurface asset valuation acceleration specialist with Hydraulic Fracturing Group LLC. Walser has 40 years of experience in the Permian Basin, Mid-Continent, Appalachian Basin, Rocky Mountains and South Texas. He has specialized in calibrating 3-D fracture modeling using a number of methods, including historical production transient analysis and calibration by various fracture mapping processes. Most recently, Walser has specialized in methods to quantify the potential to improve the recovery factors of North American resource plays. He holds a B.S. in natural gas engineering from Texas A&I University.
For other great articles about exploration, drilling, completions and production, subscribe to The American Oil & Gas Reporter and bookmark www.aogr.com.