
High-Performance WBM Optimizes Drilling Efficiency In Demanding Vicksburg Wells
By Erik Hoover and John Trenery
AUSTIN, TX.–Drilling operations continue to get more complex as fields mature and operators search for new oil and gas reservoirs. Not only are oil and gas companies drilling more advanced well designs such as extended-reach and long-lateral horizontal wells, but they also are targeting challenging formations such as deep and high-pressure/high-temperature zones in ever-more complex geology. Because of the technical difficulties associated with these wells, exploratory and developmental drilling has become increasingly risky.
A case in point is the Vicksburg natural gas play in South Texas, which is characterized by extensive structural faulting that creates hydrocarbon traps within deep, tight, geopressured sandstones. The subsurface is complex, with rollover anticlines and major fault systems cutting through the pressured Vicksburg sands interval, compartmentalizing the reservoir and further complicating the structural setting.
In this operational environment, 3-D seismic is critical to understanding the structural evolution of the formation and trapping mechanisms that are key to delineating prospective exploratory targets and optimizing the locations of development wells. And at drilling depths to 14,000-plus feet in highly-pressured, complex geology, drilling is always a challenge, especially when cutting through depleted zones intermingled with higher-pressure intervals.
As wells become more challenging in onshore areas such as South Texas, operators are finding it difficult to drill efficiently to total depth using conventional water-based mud (WBM) systems and often have to rely on oil-based mud (OBM) to reach their drilling objectives. Although there are definite technical benefits associated with OBM, these fluids are often a costly solution with regard to disposal costs, lost circulation issues and regulatory/environmental considerations. As a result, operators are constantly challenged to balance performance requirements with environmental, waste disposal, economic and logistical drivers.
In response, new high-performance WBM (HPWBM) solutions have been developed to fill the performance gap between conventional water-based and oil-based muds for onshore and inland water drilling applications. The newest generation of HPWBM systems is designed to provide superior performance and environmental compliance while maintaining cost competitiveness compared with conventional WBMs.
An HPWBM was used to successfully drill three wells in a South Texas Vicksburg field where differential sticking, losses, twist offs and catastrophic well bore stability problems were experienced in previous wells drilled with conventional WBM and OBM. HPWBM set new performance benchmarks for the field area, and saved the operator an average $500,000 on each of the three wells. The system minimized losses and eliminated stuck pipe events while reducing environmental impact. No formation damage occurred and minimal washouts were experienced during drilling, resulting in good cement bonds and allowing the operator to obtain high-quality image logs.
Key Attributes
The key attributes that make OBM effective in difficult wells are improved shale stability by reducing pore pressure transmission, controlling reactive clays, controlling differential sticking tendencies, achieving high rates of penetration, better lubricity to minimize torque and drag, and ease of engineering. However, since not all of these attributes are necessary for a given well or particular interval, HPWBM technology is designed to provide any combination of these specific characteristics in a water-based fluid that can be customized to fit a particular application.
Roughly three-quarters of formations drilled onshore contain reactive shale, and more than 90 percent of well bore stability problems are related to the drilling fluid’s inability to control reactive shales. The most important variable in maintaining shale stability is preventing pore pressure invasion into the shale matrix. Pressure invasion alters the near-well bore stress state and can induce failure. Shale stability is achieved when pressure invasion is reduced and differential pressure support is maintained.
Incorporating a micronized deformable sealing polymer (MDSP) in the HPWBM system allows shale micro pores, micro fractures and bedding planes to be to mechanically bridged to create an effective barrier that prevents destabilizing pressure transmission into the shale. Figure 1 shows how MDSP seals micro fractures to reduce pore pressure transmission and promote well bore stability.
In addition, an aluminum complex is used that precipitates out in the pore throats of shale matrix on the lowering of pH or contact with multivalent cations. The aluminum complex forms a semipermeable membrane to provide an additional barrier to pore pressure transmission.
The inability to suppress hydration in reactive clays leads to complications such as bit balling, accretion, poor solids removal efficiency, high dilution rates, filtration control and the control of rheological properties. Reactive clay swelling, along with pore pressure transmission, is a leading cause of shale instability.
Clay hydration occurs from surface hydration, bonding of water molecules to oxygen on the surface of the clay, and ionic hydration, which is the hydration of interlayer cations with surrounding shells of water molecules. Surface and osmotic absorption leads to two distinctly different problems: swelling (clay expansion after water uptake) and dispersion (the disintegration of the clay fabric after hydration).
Clay inhibition is more difficult to achieve with water-based systems because of the similarity of the wetting characteristics between the drilling fluid and formation. HPWBM uses an environmentally acceptable water-soluble clay hydration suppressant to stabilize highly reactive clays through a cation exchange mechanism. The suppressant effectively inhibits reactive clays from hydrating to control problems associated with reactive shales.
Well Bore Strengthening
Stuck pipe caused by differential pressures in pressure-depleted zones is problematic with both WBM and OBM. When used with the proper lost circulation material (LCM), the MDSP developed for HPWBM reduces differential sticking tendencies in depleted zones. The MDSP will bridge at the bore hole interface of low-permeability formations, such as tight gas sands. This bridging creates an external as well as an internal filter cake that effectively controls differential sticking.
In addition, the internal filter cake enhances the effective rock strength for increased formation fracture resistance. This increase in rock strength allows depleted sands to be drilled with the appropriate mud weight required to control pressured shales and/or pressured production sands while reducing mud losses to the depleted formation.
Conventional WBMs often exhibit low penetration rates compared with OBMs. Drilling soft, reactive formations can present issues in regard to bit balling and reduced penetration rates. Bit balling is caused by reactive clay accretion on a water-wet bit and bottom-hole-assembly, which effectively prevents the bit from contacting the formation. A penetration rate enhancer can be added to HPWBM to preferentially “oil wet” the bit, drill string and other metal components with environmentally friendly base fluids and surfactants to render metal surfaces hydrophobic, reducing the tendency of reactive clays to adhere to the bit and BHA surfaces.
Contacting the bit with a continuous, nonemulsified stream of additive during drilling provides a step change in performance by minimizing mechanical emulsification and reducing product concentrations. A secondary function of the penetration rate-enhancing additive is reduced frictional forces arising from contact between the drilling assembly, tubulars and open hole. Friction factors are representatives of the true friction coefficient of a drilling fluid, and HPWBM technology exhibits friction factor values approaching those of OBM.
The newest-generation HPWBM system is designed to provide well bore stability in a freshwater or low-salinity environment. This presents a considerable advantage for waste treatment in land environments, particularly where chloride discharge is restricted. In a multiwell campaign, the system can be recycled and reused to save the operator valuable mixing and rig time. In addition, mud reclamation reduces the total amount of fluid required, ultimately lowering the overall environmental impact of drilling operations.
HPWBM also exhibits reduced dilution rates compared with conventional water-based systems. Field studies have demonstrated that HPWBM averages dilution rates of less than 0.7 barrel/foot, whereas typical WBM systems average more than 1.0 barrel/foot, translating into lowered waste disposal costs and reduced chemical consumption.
Other positive attributes associated with HPWBM technology include enhanced image log quality, efficient cementing operations, reduced logistical and HS&E concerns, reduced barite sag, early gas kick detection, full-gauge well bore, and inherent flexibility in meeting specific performance objectives.
Severe Depletion
Gas production has been occurring in South Texas for decades, resulting in severe reservoir depletion. The level and presence of depletion is difficult to determine because of production commingling, complex geology and the low permeability of the formations. The inability to accurately predict reservoir pressures led some operators to redesign well programs. In the early 1990s, for example, some operators began using larger casing sizes with a contingency liner set before drilling into a potentially depleted zone. More recently, underbalanced drilling with casing has been adopted in South Texas to avoid associated problems with depleted zones.
Although a growing number of operators are now drilling underbalanced with casing, most (including Brigham Oil & Gas) are still using standard casing programs and relying on the drilling fluid to provide the means to control severe circulation losses in depleted zones. A long-time South Texas operator, Brigham has drilled Vicksburg wells with conventional WBMs, OBMs, and now HPWBM.
In Brooks County, Tx., Vicksburg wells are typically drilled to 11,700-14,200 feet total depth at bottom hole temperatures ranging from 270 to 320 degrees Fahrenheit. Surface pipe is usually set at ±2,000 feet and intermediate pipe is set between 9,500 and 11,000 feet near or just below the top of the Vicksburg formation. Vicksburg sands can extend for hundreds of feet in multiple sand packages. The laminated character of the Vicksburg typically consists of shale/sand sequences with productive intervals varying in permeability from 0.01 to 10.0 milliDarcy.
Over the past decade, Brigham drilled 29 wells in Brooks County, 24 of them using WBM and five using OBM. More than half of the wells experienced one or more problems, including lost circulation, stuck pipe, carbon dioxide contamination, poor cement jobs or excessive gas influx. Six of the wells using WBM experienced problems where the wells had to be either sidetracked or abandoned.
The average mud weight used to drill the 24 wells was 17.5-18.5 pounds per gallon, and each well required an average of 35-40 days to drill. Fluid losses exceeded hundreds of barrels of fluid using WBM and thousands of barrels using OBM. The small differential between pore pressure and fracture initiation pressure, along with the fracturing nature of oil-based fluids, led the operator to prefer conventional WBM.
However, the problems associated with drilling the Vicksburg with WBM included low penetration rates and excessive hole enlargement. Partial or total casing collapses were documented on a number of wells, and it was believed that excessive washout contributed to inadequate primary cementing. In early 2007, the operator made the decision to apply HPWBM technology in its Brooks County drilling program in hopes of minimizing the issues encountered when drilling with conventional WBMs while increasing drilling performance in the South Texas Vicksburg trend.
Customized Formulation
Based on the formations encountered and the problems on offset wells, the HPWBM formulation was customized to balance fluid costs and performance, and consisted of the micronized deformable sealing polymer, aluminum complex and penetration rate enhancer. The combination of these components was designed to reduce pore pressure transmission and subsequent fluid invasion into the lower-pressure sand zones. The MSDP was selected because its particle size distribution is ideal to seal and bridge the tight permeabilities found in Vicksburg sand sections.
The first well utilizing HPWBM was a vertical hole with a total depth of 13,600 feet. Conventional WBM was used to drill the 171/2-inch section to 2,000 feet, at which point 133/8-inch casing was set and a 121/4-inch hole was drilled using conventional WBM to 10,250 feet. After setting 95/8-inch casing, HPWBM was then used to drill the 81/2-inch production interval to 13,600 feet. This section is difficult to manage because of highly-depleted sands, a pressure transition requiring mud weights between 15 and 17 pounds/gallon within the first 150 feet, and a bottom-hole temperature of 320 degrees F. The mud weight at total depth for the 81/2-inch interval was 18.3 pounds/gallon.
No losses, well control events or stuck pipe were encountered drilling the interval. A 7-inch contingency liner was planned while drilling the 81/2-inch hole section in preparation for potential severe problems (seepage, lost circulation, well control, stuck pipe, etc.) while drilling the section. The upper and lower Vicksburg sands are severely depleted or highly pressured with a pore pressure of 17.5-18.5 pounds/gallon. However, using HPWBM in the 81/2-inch section resulted in successful drilling to total depth, eliminating the need for the liner.
The well was drilled to total depth in 26 days, compared with an estimated time of 35 days. The nine days saved in rig time netted the operator an estimated $500,000 in savings. When drilling was complete, the HPWBM was treated with a biocide and stored for use on the next well. Retaining the mud not only lowered fluid-related costs, but also eliminated the need to mix new mud on the rig, saving even more rig costs.
An after-action review was conducted after drilling the first well to evaluate the fluid system’s performance. It was ultimately decided to adjust the formulation to reduce costs, including using mineral oil instead of the penetration rate enhancer, and optimize bit hydraulics to improve penetration rates and reduce washouts.
Even Better Performance
Drilling performance on the second and third wells was even better. The second well was a vertical hole offset to the first well with a total depth of 13,811 feet. Conventional WBM was again used to drill the 171/2-inch hole section to 2,030 feet and the 121/4-inch hole to 10,680 feet. HPWBM was then used to drill the 81/2-inch interval to 13,811 feet using the mud from the previous well. The HPWBM was brought to the rig and cut back to 16.0 pounds/gallon. The ending mud weight was 17.8 pounds/gallon with no losses, seepage or stuck pipe, again eliminating the need for a contingency liner.
The well was drilled to total depth in 24 days, saving 11 days and $600,000 of rig time. As with the first well, the HPWBM was treated and stored for use on the third well.
An after-action review was again conducted to further improve the performance of the mud system. Excessive hole enlargement was noted on the second well, despite modifying the bit hydraulics. The main recommendation was to use potassium hydroxide instead of caustic soda for pH control to provide additional shale inhibition to the mud system and prevent washouts.
The third and final well in the Brooks County campaign was a vertical hole with a total depth of 13,600 feet. As on the first two wells, conventional WBM was used to drill the 17½-inch section to 2,011 feet and the 121/4-inch section to 10,833 feet. After setting 91/4-inch casing, the HPWBM was used to drill the 81/2-inch production interval to 13,600 feet at a bottom-hole temperature of 310 degrees F.
The potassium hydroxide helped reduce the washouts observed in the first two wells (Table 1), which led to a better primary cement job. The ending mud weight for the 81/2-inch interval was 18.4 pounds/gallon. The well was drilled to total depth with no losses, seepage or stuck pipe, and the 7-inch contingency liner was not needed.
This well was drilled in only 20 days–a record for Brooks County–saving 15 days and more than $700,000 in rig time (Figure 2).
The operator considers the three-well campaign using HPWBM highly successful, with all three wells completed ahead of schedule and the last well achieving record performance. Figure 3 shows the days versus depth curve for the three wells drilled with HPWBM compared with offset wells drilled with conventional WBM systems. The wells drilled with HPWBM were completed an average of 23 days faster than those drilled with conventional systems.
All three wells were also drilled to total depth with lower mud weights than the offset wells. The reduced final mud weights helped eliminate losses and reduce chemical consumption. Figure 4 shows mud weight versus depth for the three HPWBM wells compared with offset wells drilled with conventional WBM systems. The wells drilled with HPWBM reached total depth with an average mud weight of 0.5 pound/gallon less than the wells drilled with conventional systems. Table 2 shows the average fluid properties for each of the three wells drilled with HPWBM.
The faster drilling rates, reduced mud weights and ability to recycle the mud from well to well saved the operator a combined $1.5 million on the three Brooks County Vicksburg wells.
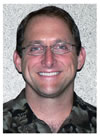
ERIK HOOVER is the operations manager for Brigham Oil & Gas LP in Austin, Tx. His responsibilities include managing daily drilling, completion and production operations for Brigham’s Gulf Coast region and other high-impact areas. Before joining Brigham in 1997, Hoover worked for nine years as an operations engineer for Mewbourne Oil Company in Texas, Oklahoma and New Mexico. He holds a B.S. in petroleum engineering from Texas A&M University.
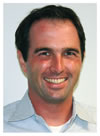
JOHN TRENERY is the product line manager for water-based fluids for Baker Hughes Drilling Fluids in Houston. His responsibilities include developing new water-based products, as well as marketing support for existing products. Trenery has worked for Baker Hughes for seven years. He holds a B.S. in chemical engineering with a minor in chemistry from the University of Houston.
For other great articles about exploration, drilling, completions and production, subscribe to The American Oil & Gas Reporter and bookmark www.aogr.com.