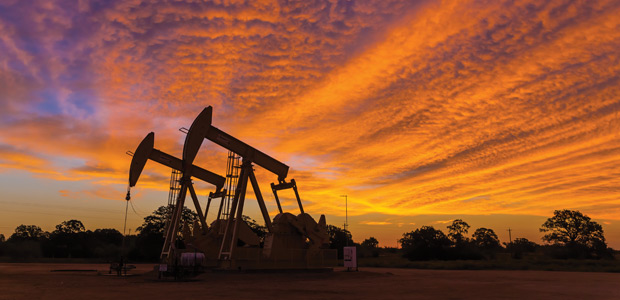
Going Digital
Intelligent Well Pad Program Optimizes Operation And Production Of Eagle Ford Shale Wells
By Jon Krome, Mike Bloom, Alex Swanson, David Anthony, Shaun Derise and Lauren Rightmire
HOUSTON–Retrofitting producing assets in U.S. shale plays with digital oil field-type automation, information technology, and best-in-class work practices has revealed significant benefits to BHP Billiton in the Eagle Ford Shale play.
After entering the Eagle Ford five years ago through an acquisition that included more than 1 million net acres in the play, BHP Billiton’s operations and engineering team identified the need for a digital oil field solution to improve safety and operating efficiency while optimizing production. The company selected well pads in its Blackhawk Field in Karnes County, Tx., to use as a demonstration area for an intelligent well pad program (IWPP). The goals were to:
- Reduce health, safety and environmental (HS&E) risk exposure;
- Increase productivity for operations personnel; and
- Minimize production downtime.
A multidisciplined team evaluated the opportunities and implemented a comprehensive program that included facility redesign, well-site automation, IT and telecommunications, and a round-the-clock surveillance center. A detailed assessment with all key stakeholders yielded a fit-for-purpose program, detailed and tailored for the specific application.
The IWPP has been deployed fully, including 24/7 operation of the surveillance center since October 2014. It delivers state-of-the-art automation, telecommunications and information systems to acquire real-time data and video, and has demonstrated the ability to improve HS&E, lower operating costs, and enhance production performance. The surveillance center supports centralized well and pad monitoring to enable exception-based interventions in the field. Surveillance software, notifications and exception-based reporting also support work processes to minimize driving time for field technicians and well downtime on pads.
Based on the positive results in the Eagle Ford pilot program, BHP Billiton now is developing and tailoring its IWPP solutions and work practices to well pads on all its shale assets.
Redesigning Pad Operations
The early well pad automation design was extremely limited for both new and legacy pads. In some cases, the data included only gas rate measurements. All surveillance data (pressures, temperatures, and vessel/tank levels) were collected manually by operations technicians during daily inspections, limiting the usefulness of the data and exposing technicians to unnecessary risk. The operations and engineering teams attributed a portion of unfavorable well performance and downtime to limited use of surveillance data. Additionally, pad shutdowns could not be triggered remotely for emergencies such as flash flooding or vandalism.
Remedial work was required to bring the legacy pads up to BHP Billiton’s standards for safety, integrity, reliability and surveillance. In addition to installing advanced automation, the sites also required modifying the pneumatic safety system and piping to commingle tank batteries, and installing additional electrical grounding, temperature safety element loops, and liquid allocation metering.
BHP Billiton’s Eagle Ford production unit also faced challenges with telecommunications. A remote Wi-Fi service was installed on each pad prior to operations to connect drilling and completions teams to the Internet as well as to BHP Billiton’s business voice, video and data networks. However, this service was disabled following completion, leaving well pads with no Internet connectivity.
After production startup, point-to-multipoint radios were used to transmit the limited data collected from each pad site. In this configuration, bandwidth restrictions created an excessive length of time between data polling periods.
The operations team identified several HS&E and productivity challenges resulting from the limited data available from the pads. Technicians spent up to four hours each day driving on remote roads to perform daily inspections. Regulatory inspections also demanded regular visits to pads to meet compliance requirements. In addition to manual data collection and keyed data entry, operations technicians spent additional hours on site for higher-rate wells that needed more frequent tank level monitoring.
Once on location, technicians spent large amounts of time in safety-sensitive areas performing manual data collection tasks. Moreover, operations technicians and administrative staff spent one to two hours a day capturing non-automated process values and entering them into a historian database.
Guiding Principles
The team developed a set of guiding principles to drive program design and implementation, with an eye on tangible results that included:
- Improving productivity by 25 percent by allowing each technician to operate more wells;
- Reducing road miles by 25 percent per technician by eliminating daily site visits to collect data;
- Reducing downtime by 10 percent of unscheduled facility breakdowns and well loading by fully adopting remote surveillance practices;
- Leveraging existing applications in BHP Billiton’s IT portfolio to avoid having to develop new software;
- Using off-the-shelf components to limit custom builds, costs, and supply cycle times; and
- Leveraging downtime during implementation by “hiding behind” other non-IWPP downtime to perform tasks such as installing tubing or upgrading facilities.
The team determined during the selection phase that the IWPP would require a holistic implementation approach supported by a cross-functional project team. Each of the five “layers” shown in Figure 1 was identified as critical for a comprehensive program. Without this complete view, solutions were likely to be partial or suboptimal.
Work streams were established to support the IWPP framework (Figures 2A and 2B). The automation and piping work streams implemented data collection and well control. The IT and telecommunications work stream delivered the video cameras and radio infrastructure to move the collected data off well pads, while the surveillance center work stream provided the tools and infrastructure to manage and view collected data. The applications and business processes work streams managed the required changes to the existing application tool set, established standardized processes and procedures, and defined roles and responsibilities.
Stakeholder Engagement
Project engagement with a cross section of the operations team was instrumental to the program’s success. In addition to the increased level of automation and instrumentation on the well pads, the IWPP impacted operational processes, roles, responsibilities, and IT applications. Production and process engineers worked closely with operations personnel to define key metrics and performance criteria to promote improved data analytics and reporting capabilities. Process engineers worked to create a tank commingling design and identify opportunities to reduce the level of instrumentation.
The automation team was responsible for changes to production surveillance requirements in the supervisory control and data acquisition tool, and for designing programmable logic controller functionality at the pads. By engaging the end-users (operations technicians) early in design phases, buy-in and innovation of these activities were improved simultaneously.
The IT team assessed the requirements for designing and deploying high-speed telecommunications. Improved polling rates and bandwidth were required to increase the availability of near-real-time data. Increasing the number of process values and data tags collected, and adding three live streaming closed-caption television cameras per pad, further increased bandwidth requirements.
The IT team also updated surveillance software applications, whereby the video management software notified users of deviations from a predefined “normal” condition. The application tool set was enhanced as updated screens and reports were developed to analyze the richer set of information.
A separate design team was responsible for developing new well pads, while the Karnes IWPP focused on retrofitting existing pads. As the program expanded to include additional production units, design team members incorporated the IWPP design into new pads. The facilities team selected the surveillance center location, including evaluating various use cases and safety studies, and selecting vendors for constructing and implementing the center. The HS&E team translated permitting requirements for modifying well pads and the surveillance building.
Defining Project Scope
A series of design workshops with the project team and the various stakeholders established the project scope and future operating philosophy. These early workshops also established guidelines for reporting requirements, design, and tools or technology used for each task.
All activities requiring daily site visits were to be automated. The design needed to include remote shut-in and tank switching to efficiently manage wells from the surveillance center. The goal of adding remote control capabilities was to reduce the likelihood of shutdowns, improve reaction times, and reduce mileage.
The team determined that many human inspections could be eliminated by installing three video cameras on each pad to observe flares continuously, and process trains, wellheads, etc., especially at high-priority locations. However, the large data volumes required video management software to high grade events such as leaks or pad entries, and to notify technicians. Figures 3A and 3B show the application tool set selected and detailed application scoping.
Site surveys were performed for each well pad to determine the level of automation and instrumentation. The automation team compiled a list of required materials, labor, and associated cost, leading to additional engagement with the eventual users in the operations team. Based on this collaboration, several process values were identified that could remain inferred from other automatically collected data points, reducing project cost.
Following completion of these initial surveys, the project team realized an opportunity to reduce costs by minimizing the amount of instrumented process equipment. The initial production trains were sized to handle 1,000 barrels of condensate a day, but rates had fallen by the time the IWPP was installed. With lower forecasted production rates, the amount of processing and storage equipment could be reduced greatly, along with related instrumentation.
The project team determined that commingling liquids production from all wells downstream of the high-pressure separators into one production train was possible and cost effective. The team planned to install oil and water meters on the liquid lines of each high-pressure separator to meter the liquid production of each well for operational allocation, essentially using the separators as individual test separators for each well.
Gas measurement was accomplished already through individual gas meters on the high-pressure gas outlet piping. On the initial pad, commingling production into one train allowed the equipment needed to be reduced by:
- 14 oil tanks;
- Two water tanks;
- Two low-pressure separators;
- Two heater-treaters;
- Two vapor recovery towers;
- Two fuel gas systems (scrubbers, filter and pots);
- Two recycle pumps;
- One flare stack; and
- Two flare knockout drums.
This same approach was adopted to install the IWPP solution on all subsequent well pads.
Dynamic Operating Model
The IT and telecommunications team performed surveys to precisely define each site’s location, topography, and distance to other pads. An initial engineering design was performed to identify possible radio solutions, leading to a “mesh” radio solution to increase telecommunications coverage, reliability at the remote pads, and expanded bandwidth to support the increased process values and live streaming video.
Wi-Fi access at each pad became a part of the final solution, giving operations technicians complete access to all new data captured. The low-power, multifrequency mesh radios use nodes to create a fully redundant network. All telecommunications equipment on the pad is powered by a central solar/battery source.
A BHP Billiton-owned site that housed a gas processing facility was selected to construct the surveillance center. It was an ideal location in the center of the field with access to all pads. The operations team was relocated approximately 50 miles from an office in Cuero, Tx., to the new surveillance center near Karnes.
The building includes a control room, meeting space, supervisors’ offices, and an open seating workroom for technicians. The surveillance room contains four wall-mounted, 65-inch monitors, and is secured behind controlled-access doors. A video matrix can display any PC source on any of the monitors, allowing technicians to monitor well pad operations and production, vehicle locations, and closed-circuit-television video feeds 24 hours a day.
Implementing the IWPP solution drove key changes to operations technicians’ normal routines. By instrumenting all the process values required for manual daily data collection, the IWPP solution eliminated the multiple hours technicians had spent collecting data and manually entering values into the field data capture system.
Several field operations technicians, selected based on their previous experience working in control room environments, were shifted to permanent positions in the surveillance center. Capabilities were developed through the IWPP solution to not only enable surveillance technicians to provide centralized support by monitoring asset performance continuously, but also by optimizing scheduling and dispatching operations, and improving data reporting.
For example, since inception, the IWPP system’s alarm features have greatly enabled faster reaction times and increased the speed of resolution, preventing unfavorable occurrences and the duration of downtime events. The team is able to use real-time data and vehicle location information to perform dynamic dispatch, rerouting the closest, most appropriate personnel. Consequently, the operations team has evolved from static inspection routes to a more dynamic model in which well sites were visited on an exception basis only.
SCADA and data historian training was provided to all operations technicians, both in the field and in the surveillance center, and all technicians are provided the same tool set to monitor field conditions. Shift supervisors went to a four days on/four days off pattern, mirroring that of operations technicians, and were officed at the surveillance center to provide additional support and foster more rapid issue triage.
Several other initiatives were formed in conjunction with the IWPP to help drive change. Teams worked to enable an electronic run ticket process to eliminate the need for operations technicians to travel to sites to collect daily run tickets or manually measure tank levels. Additionally, a reporting project was developed to help collect key data and automatically generate a daily production report, eliminating the need for manual collection. These projects have proven to have more universal application than merely in the Karnes area.
Project Results
The surveillance center was commissioned in July 2014, and moved to 24/7 operations in October 2014 to provide full-time field support. The IWPP solution has increased collaboration between operations and engineering teams, with both now using common surveillance tools, and end-users continue to identify opportunities for continuous improvement.
Teams attend morning meetings and connect remotely to review upcoming operations activities and field issues requiring attention. The operations team in the field continues to manage real-time issue resolution, while petroleum engineers use the surveillance tools to review historical data and develop action plans for resolving issues with problem wells. The teams use IWPP surveillance solutions to share well trends and discuss any well performance issues on an exception basis.
The IWPP solution was implemented on 35 pads with 105 wells in Karnes County as part of BHP Billiton’s pilot program. As a result, the well-to-technician ratio and overall operator efficiency improved by more than 400 percent, far exceeding the pilot program’s targeted 25 percent (Figure 4). Improvements to data gathering and management are the greatest contributing factors.
With global positioning system tracking of each vehicle, dynamic routing and dispatching processes have optimized the necessary routes. Both data management and driving/routing optimization will continue to improve efficiencies, allowing additional wells to come on line without requiring additional resources.
Recognizing that decreasing road miles would lead to reduced HS&E risks as well as improved productive time for operations technicians, the pilot targeted a 25 percent reduction in travel. The projected mileage based on well count would have been in excess of 4,500 miles each month without the IWPP. The project is reporting a monthly mileage reduction of more than 50 percent (Figure 5A).
The dramatic decrease in driving time reduced costs and HS&E risks, while also directly impacting productivity, freeing approximately 40 hours a month for each technician.
The average number of downtime events per well each month has decreased from nine to five. Again, this 44 percent improvement far exceeds the pilot project’s 10 percent target objective. The duration of the average unscheduled downtime event has improved by 25 percent (from 20 to 15 hours), as shown in Figure 5B.
Surveillance center technicians receive data in real time, speeding reaction and resolution time. In some instances, technicians can identify an imminent shut-in event and prevent downtime.
BHP Billiton continues to see measureable and successful productivity gains in its Karnes County operations, and the company now plans to implement intelligent well pad functionality across its North American shale production units, using the lessons learned from the Eagle Ford project. To meet the specific demands of each production environment, each production unit is to be equipped with varying levels of automation and instrumentation.
Some of the more mature production units already are equipped with an advanced level of automation and connectivity. Adding real-time surveillance centers in other production units will achieve the goals of improving productivity and reducing downtime. Less instrumented areas will receive the full intelligent well pad scope, including automation, piping and telecommunications. For these projects, the team will work directly with operations and engineering to complete the design workshops and select the appropriate level of instrumentation for each field.
Editor’s Note: For additional information on the Karnes County IWPP project, see SPE 174826, a technical paper presented at the Society of Petroleum Engineers Annual Technical Conference & Exhibition, held Sept. 28-30, 2015, in Houston. The preceding article was adapted from that presentation.
JON KROME is head of operations, maintenance and integrity at BHP Billiton Petroleum in Houston. He joined the company in 2009 as an operations and production unit manager in Trinidad and the United Kingdom, and began working with BHP Billiton’s Eagle Ford assets in 2013. Krome began his career in 1988 in well operations and completions assignments with Mobil Oil, and subsequently served as an operations manager at Aera Energy, a senior manager at Accenture, an associate partner at IBM, and a senior manager at Capgemini Consulting. He holds a B.A. in earth and planetary sciences from Johns Hopkins University, and an M.S. in petroleum engineering from the University of Southern California.
MIKE BLOOM is principal of H2R Consulting LLC in Houston, providing drilling, completions, engineering and management consulting services. He previously served as a field manager at BHP Billiton in the Eagle Ford Shale, managing upstream and midstream assets in DeWitt, Karnes and Bee counties, Tx. Bloom’s eight years of service at BHP Billiton included drilling and completion-related assignments in the Eagle Ford, Fayetteville Shale, deepwater Gulf of Mexico, and international projects. He began his career in 2001 as an operations engineer at Chevron. Bloom holds a B.S. in petroleum engineering from the University of Tulsa.
ALEX SWANSON is information systems manager, planning, design and modification, at BHP Billiton in Houston, where he leads a team of business analysts and solution architects providing technology detail design. Notable projects include the intelligent wells pad production program in the company’s North American shale plays. With more than 40 years of industry experience, Swanson joined BHP Billiton in 1994 and has held a number of IT management positions for both onshore and offshore assets in the United Kingdom, Trinidad and the United States, including deepwater and onshore shale field developments.
DAVID ANTHONY is senior information systems manager, strategy, compliance and projects, at BHP Billiton. He joined the company in 1995 as a principal analyst, standards and technology, and subsequently served as information systems lead, business systems manager in Algeria, manager of development and production information technology, and senior information systems manager for BHP Billiton’s North American shale assets. Anthony holds a B.S. in mathematics and computing from Swinburne University of Technology, and completed the business school graduate management program at the University of Melbourne.
SHAUN DERISE is shale automation supervisor at BHP Billiton. He joined the company in 2013 as an electrical and instrumentation engineer, central engineering. Derise previously served as technical professional leader of instrumentation and controls at KBR Inc., a technical adviser at Universal Pegasus International, a subsidiary of Huntington Ingalls Industries, and as a PLC programmer at Jelec USA Inc. He holds a B.S. in electrical engineering from the University of Louisiana at Lafayette.
LAUREN RIGHTMIRE is industry solutions and services manager, North American resources, at Accenture in Houston. She joined Accenture as a consultant, North American resources, in 2013 after serving as a land technician at EXCO Resources Inc. and as a landman at Carla Petroleum. Rightmire holds a B.B.A. in energy commerce and petroleum land management from Texas Tech University.
For other great articles about exploration, drilling, completions and production, subscribe to The American Oil & Gas Reporter and bookmark www.aogr.com.