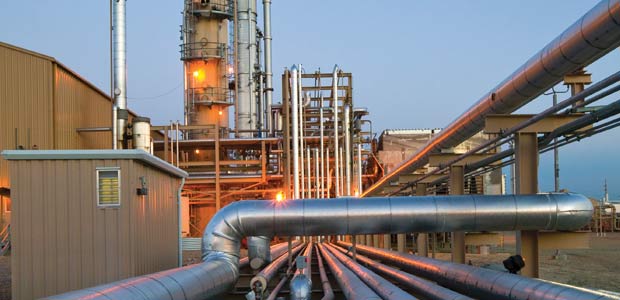
Natural Gas Processors Respond To Rapid Growth In Shale Gas Production
By Kari Johnson, Special Correspondent
After almost a decade of no net growth, natural gas production began rising again in 2007. According to the U.S. Energy Information Administration, that upward trend showed 3 percent growth between first-quarter 2006 and first-quarter 2007, and accelerated to 9 percent between first-quarter 2007 and first-quarter 2008.
This growth was in no small part attributed to unconventional gases found in shales and tight gas sands. As of a June 2008 report, for example, the EIA figured gas from one Barnett Shale field alone contributed more than 6 percent of total lower-48 production.
This rapid growth in unconventional gas has implications for gas processing, according to James Tobin, natural gas industry analyst for EIA, who notes that the number of plant additions outstrips plant closures. “Extensive natural gas development in the Barnett Shale and Bossier Sand formations of East Texas, as well as in western Colorado and Wyoming, has resulted in the construction of several large processing plants, as well as the expansion of several existing plants,” Tobin says.
Tobin further says the plants that have been closed tend to be low-volume processing plants, while the new plants tend to be large-volume operations, increasing overall daily processing capacity. It also appears, he says, that more gas treatment plants are being built because many unconventional gas wells yield fewer natural gas liquids. This leads Tobin to conclude that the gas-treating market is growing faster than the processing segment.
The Treatment Chain
Shale gas is certainly not the same everywhere, says Keith Bullin, senior consulting engineer for Bryan Research & Engineering. The Antrim Shale, for example, has high nitrogen concentration, as does at least one well tested in the Barnett Shale, Bullin observes. New Albany wells show high carbon dioxide concentrations, he points out, while several wells in the Marcellus Shale have tested up to 16 percent ethane content.
Economically treating and processing these gases requires all the same techniques as conventional gas, concludes Bullin, plus the ability to handle a great deal of variability in the same field.
Treatment often begins at the wellhead, offers Bob Dunn, president of the Gas Processors Association. Condensates and free water usually are separated at the wellhead using mechanical separators, he observes. Gas, condensate and water are separated in the field separator, he details. Extracted condensate and free water are directed to separate storage tanks and the gas flows to a gathering system. After the free water has been removed, the gas is still saturated with water vapor, and depending on the temperature and pressure of the gas stream, may need to be dehydrated or treated with methanol to prevent hydrates as the temperature drops.
Contaminants such as carbon dioxide and hydrogen sulfide are removed at a treatment facility near the field or at a gas processing plant. “Removing the CO2 near the field is often done for pipeline protection,” he remarks.
He says this typically is achieved using a physical solvent called an amine solution. Dunn says that CO2 and H2S are both highly corrosive, and for some, the risk of corrosion is outweighed by the economies of scale achieved by central processing. If the gas is treated using an amine solution, it later must be dehydrated to pipeline quality. Dehydration, says Dunn, can be accomplished through absorption or adsorption methods. These separation and dehydration steps are similar for all gases.
If nitrogen is present in significant amounts, it must be removed at a cryogenic plant with supercooling equipment so that the gas meets the minimum heating value required by the pipeline, Bullin adds.
Meeting Pipeline Specs
Pipeline quality standards limit the amount of CO2, nitrogen, oxygen and water vapor that can be in the gas stream, notes Tobin, and also set a heating value limit of 1,035 Btu per cubic foot, plus or minus 50 Btu.
In some cases, when plants are not yet available, waivers are granted for a limited time, according to Dunn. This enables producers to begin marketing gas from new fields as the processing plant is built.
If the gas is not pipeline quality, it typically is processed at a refrigeration or cryogenic plant. In refrigeration units, the gas is cooled and the NGLs precipitate out, explains Bullin, removing more than 90 percent of the propane and about 40 percent of the ethane. Other heavier components are almost entirely removed.
In cryogenic units, gas temperature is reduced to -120 to -150 degrees Fahrenheit, he explains. The temperature drop causes the ethane and other heavier hydrocarbons to condense, removing more of the natural gas liquids and 90-95 percent of the ethane.
Dunn says natural gas liquids removed in the cryogenic units may be trucked or are piped to a fractionation unit, where ethane, propane, and the heavier hydrocarbon liquids are separated. The fractionation process is accomplished basically because each hydrocarbon component has a unique boiling point, he adds. When NGL prices are low, Dunn says extraction will be minimized. Some gas liquids, and particularly ethane, will be left in the gas because they may not be economic to separate.
There were more than 500 gas processing plants in the United States in 2004. Most of these, according to Tobin, were in the Southwest and the Rocky Mountains. Since that time, additional plants have been added at least in part to address demand in unconventional gas plays. He says growth in tight-gas production has increased capacity in Wyoming, Colorado and Utah.
In the past few years, Bullin interjects, processing activity also has grown in proximity to the developing Barnett, Woodford and Marcellus shales. Tobin points out that although there was a net decrease in natural gas plant capacity in Texas between 1995 and 2004, several new plants were added and more are being planned as a result of increased development in the Barnett Shale.
Unconventional Gas Challenges
As unconventional gas production has become attractive, gathering and processing capacity has come under pressure. Horizontal drilling has turned slow- to low-producing shales into extraordinary assets, reflects Randy Albert, senior vice president of emerging business units for CNX Gas.
Randy Nickerson, chief commercial officer at MarkWest Energy Partners, agrees. “When a horizontally drilled shale gas well starts flowing, there often is a tremendous increase in volume, making it critical that infrastructure is in place to process the gas and move it to market,” he says.
Prior to the 1990s, most processing operations were owned by the pipeline or gas production companies. When a producer planned to develop new fields, the processors were fully informed and could build capacity to match production.
Now there are many independent midstream processors, which relieves pipelines and/or producers of the capital requirements for processing, but also raises coordination issues. To be successful, Nickerson says producers and processors must work closely together to ensure that production levels, and gathering and processing capacity are as well matched as possible. This, he opines, is a very big challenge for emerging shale plays. “It is very important to make sure service providers are in lock step with producers,” he reflects. “It has to be a joint effort where risk and reward are shared.”
Another challenge is in plant location. The ideal site often is close to city limits, and therefore may come under tight local regulations, says Bullin. For example, the town of Flower Mound, Tx., has rules for noise levels, fence height and color, size of shrubs and trees to hide the equipment, and the amount of lighting permitted. The rule book, says Bullin, is 100 pages long.
Ethane is an issue for Eastern shales. When NGL prices are down, there is little attraction to separating the feedstock because there are no extraction economics, according to Dunn. To address this issue and NGL pricing in general, he says some processors are embracing contracts that revert to a fee for services when the fractionation spread is unfavorable. During the run-up in prices in 2007 and 2008, processing gas and gas liquids was quite profitable, but now, he says, fee-based contracts are more reliable.
Developments In Appalachia
Exciting things are going on in Appalachia, and particularly in the Marcellus Shale, where Nickerson says MarkWest is the largest natural gas processor in the region. He says the company has moved aggressively into the Marcellus play, building an initial refrigeration plant last year in Houston, Pa., and making plans to bring additional plants on line over the next 24 months.
Nickerson says MarkWest has operated in the Appalachian Basin for more than 20 years, and has gas processing plants and NGL fractionation facilities in West Virginia, Kentucky and Ohio. The new plants move the company into the midst of the Marcellus production in Pennsylvania. He reports MarkWest has an agreement with Range Resources to process Range’s rich gas in the southwestern part of the state. The company also has a financial partnership with NGP Midstream & Resources for joint funding of its Marcellus activities.
The initial Pennsylvania refrigeration plant has a capacity of approximately 30 million cubic feet a day, which can be easily expanded. Nickerson says planned processing additions this year include a 35 MMcf/d cryogenic unit and a second cryogenic plant with 120 MMcf/d of processing capacity. Another cryogenic plant is planned in 2010 near Majorsville, Pa., with a planned capacity of 120 MMcf/d, he adds.
By the end of this year, Nickerson sums, MarkWest should have as much as 200 MMcf/d of processing capability in the Marcellus. A 20,000 barrel a day fractionation facility also is possible for Houston in 2010, he says.
According to Nickerson, it appears that the Marcellus is similar to the Barnett and Woodford shales in that parts are quite dry, with gas in the 1,000-1,050 Btu per cubic foot range or less.
Marcellus gas, Nickerson continues, also is higher in ethane content in areas, which often is not recovered in Appalachia because there is not a significant market for ethane in the East.
Appalachian Producer
Horizontal drilling has enabled unconventional gas wells to be economic, and they can be large producers. CNX learned this first hand as its initial wells in the Marcellus Shale quickly became the company’s biggest producers, says Albert. He reports the peak rate on CNX’s first well after producing the first 100 million cubic feet was 6.7 MMcf/d, and the well still is producing around 3 MMcf/d. If the well had been allowed to flow at full rate, Albert says he believes initial production would have been more than 10 MMcf/d.
CNX is the leading Appalachian gas producer at 76 billion cubic feet in 2008, according to Albert. He says the company controls more than 4 million acres and has a strong coalbed methane program. CNX dehydrates the gas at a membrane plant.
“Thanks to our CBM program, we have been able to avoid processing our shale gas so far,” Albert says.
He notes that CNX’s shale gas is averaging 1,100 Btu, which is blended with 910 Btu CBM gas. The benefit works both ways, Albert adds, because the shale gas enables CNX to avoid removing CO2 from its CBM stream, since the blended gas meets pipeline quality standards.
CNX is focusing its Marcellus activity in southern Green County in the southwestern corner of Pennsylvania. Through February the company had drilled three horizontal wells and four vertical wells, which Albert notes are sometimes the only option because of land area, lease and mining constraints.
CNX also has drilled 20 wells to the Chattanooga formation. Here the gas is wet, so the company is partnering for the processing, which is scheduled for midyear, Albert says. In the meantime, he reveals, the company has a waiver to ship unprocessed gas.
CNX has five wells in the Huron, Albert continues. These wells are yielding 1,150 Btu gas in Tennessee and 1,120 Btu gas in Kentucky. At present, he allows, CNX has no outlet for its Kentucky gas, and the Tennessee gas is shipping hot. Even with these issues, Albert says he doesn’t see a long-term problem getting shale gas to market.
The bigger issue, Albert says, is ethane. CNX’s strategy is to remove all the higher-ranked hydrocarbons so that the ethane can remain in the gas. Sometimes the gas is still not pipeline quality, he allows, so the ethane must be removed even though that is not economic in itself.
The company is doing initial work in the New Albany Shale as well. Here there seems to be a nitrogen issue, Albert reveals, with 8-10 percent saturation. This will have to be addressed before the gas can be successfully produced and marketed, he acknowledges.
Rockies And Southwest
Tight gas sands are going strong in the Rocky Mountain region, where Questar Gas Management processes some of the gas in Wyoming and eastern Utah, according to Vice President Perry Richards. He says Questar’s processing complex in the Green River Basin has a capacity of 540 MMcf/d, and its center in the Uinta Basin has another 330 MMcf/d. No hydrogen sulfide or nitrogen has been encountered, and the gas generally is fairly dry, he mentions. Most of the gas comes from the Pinedale Anticline.
MarkWest Energy Partners also is a major player in the Southwest as the largest gatherer and processor in the Woodford Shale, according to Nickerson. Gas volumes are a challenge, he says, and it is not unusual for a producer to bring four wells on at one time.
For example, Nickerson cites, in only two and a half years, Newfield Exploration Co. went from producing a few million cubic feet to more than 350 MMcf/d. He says this dramatic upswing makes it imperative that producers and processors work together so that surprises are minimized.
Similarly, Nickerson continues, shale gas wells have fairly steep decline rates, so new wells must come on line regularly to generate any kind of steady flow. As fields mature, this is less of an issue.
He says MarkWest has been processing gas from vertical wells in the Woodford Shale for some time, and has 320 MMcf/d of throughput capacity, and both cryogenic and fractionation capability. Now with new horizontal drilling, the wells are highly productive. The gas ranges from 1,000 to 1,350 Btu, so the company designed and operates separate wet and dry gathering systems, Nickerson reports, saying that so far the company has not encountered much H2S and no nitrogen.
In the nearby Haynesville Shale, Dunn says it is still too early to draw conclusions. Some wells are producing near pipeline quality while others have some CO2 and H2S, and high liquid content. Although there are few processing facilities in the region, Dunn says he does not see a problem in meeting capacity demands, given that it only takes 12 months to get a plant up and running.
Even though producers often do not control the processing, both parties have an interest in working together to ensure a good match between supply and demand. If anything, according to Dunn, there is a greater move to independence as a result of financial constraints. If forced to choose, he says, producers will invest in drilling rather than processing.
This goes against the desire for greater control, but is mitigated by the close relationship developed by necessity. “It’s hard to be the best at both,” Albert concludes.
Because of the low level of natural gas liquids in the Haynesville, it appears fractionation will not be required, Dunn says. Given that NGL supply now exceeds demand, Dunn says he believes the liquids in Haynesville gas will remain in the gas wherever possible.
Meanwhile, the grandfather of all shale plays–the Barnett–continues to produce high volumes, says Bullin. Hundreds of thousands of acres are leased to producers in the Barnett, and there are hundreds of active wells. Bullin says the gas to the east tends to be dry, while the gas to the west is richer. These wetter gases need to be processed and fractionated, and local facilities are available for this.
For other great articles about exploration, drilling, completions and production, subscribe to The American Oil & Gas Reporter and bookmark www.aogr.com.