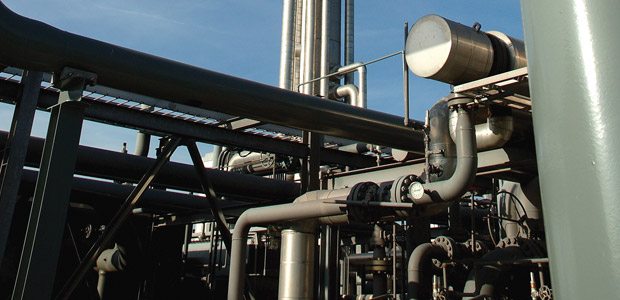
Natural Gas Processing
Processing Solutions Enable Economic Development Of Highly Variable Shale Plays
By Guy Lewis, Tom Russell and Neil Eckersley
DES PLAINES, IL.–Natural gas is cleaner burning and more flexible than other fuels, and is available in abundant supply, thanks to shale plays. It delivers clear economic as well as environmental advantages. As a result, the unconventional revolution is enabling a transformation of the U.S. energy mix, and the revolution has begun to spread to other parts of the world. However, each new supply source brings challenges for treating, gas quality standards, and distribution infrastructure.
This is particularly true of shale gas, which has compositions that are likely to vary significantly from one development area to another. In addition, the gas resources often are in remote regions challenged by limited water, infrastructure and other logistical problems that require innovative processing solutions. Operators need solutions that assure they can monetize their resources. Success often hinges on executing gas projects quickly and reliably, as well as ensuring the projects can maximize recovery of high-value natural gas liquids products at low production costs and downtime.
It is challenging to design a gas processing facility based on gas quality information from a few initial wells, while remaining flexible enough to deal with variations that might come as more wells are drilled in the same area. In addition, operators often want to start designing gas processing plants before they have detailed gas compositions from pilot wells. This uncertainty in future gas quality adds to the risks of any shale gas field development.
Unconventional Processing
Fortunate operators find that their gas is relatively clean. However, unconventional gas often is contaminated with “acid gas” and requires removing carbon dioxide when the produced gas contains higher CO2 levels than the downstream pipeline will accept. In addition, when cryogenic operations are used to recover NGLs or generate liquefied natural gas, CO2 concentrations above 0.5-1.0 percent (depending on the richness of the gas) will cause CO2 to freeze out at normal operating temperatures below -125 degrees Fahrenheit.
Y-Grade NGL (propane, isobutene, butane, pentane, hexane and other heavier C7+ components) specifications for cryogenic liquid production normally limits CO2 to 0.35 liquids volume percent CO2/ethane (C2), or 1,000 parts per million. The right technology for removing acid gas depends on the amount in the feed and the desired contaminant level in the product. The most common processes for removing carbon dioxide are amine treating, membranes and molecular sieves.
Removing water vapor also is required for a variety of reasons. Residue gas specifications normally limit water content to about five pounds per million cubic feet of gas. That gas will have a water dew point of about 20 degrees at a pipeline pressure of 800 psig. Mechanical refrigeration plants that chill the gas to temperatures of 0 to -30 degrees will form hydrates if the water content of the gas is one to two pounds/MMcf. Cryogenic liquid recovery plants will freeze up (form hydrates) if the gas water content is above 100 parts per million by volume (ppmv).
The most prevalent solutions for each case are contacting the gas with 99 percent triethylene glycol to dry the gas to below 7 pounds/MMcf, injecting 80 percent ethylene glycol (EG) into the mechanical refrigeration unit to prevent hydrate formation and dry the gas to below 1 pound/MMcf, and processing the gas in a molecular sieve unit upstream of the cryogenic plant to dry the gas to below 100 ppmv.
In addition to removing contaminants, shale gas often is produced with NGLs that bring higher value if they are recovered for petrochemical or other uses that exceed their Btu value when left in the natural gas stream. Depending on the inlet gas conditions (gas richness, pressure and temperature, product specs, etc.), the optimum liquid recovery process will be selected.
For a production situation that anticipates fairly rich gas and propane-plus recovery, and normally smaller volumes, the best choice would be mechanical refrigeration with EG injection. This process gets fairly high propane recovery when the gas has five gallons of liquid hydrocarbons per Mcf (GPM) or better. In situations with lean or rich gas and little to no ethane recovery with smaller gas volumes (e.g., 20 MMcf/d), a Joule-Thomson process with molecular sieve dehydration is a sensible solution. Finally, situations expecting lean or rich gas, high propane or ethane recovery, and medium to large gas volumes (30-200+ MMcf/d) should choose a cryogenic process.
Modular Plant Solutions
The traditional model of a “stick-built” NGL recovery plant that requires two or more years to implement creates costly delays, forming a barrier to developing vital shale and other unconventional resources.
Just as specialty horizontal drilling and multistage hydraulic fracturing techniques and technologies have emerged to optimize the economics of developing shale gas resources, so, too, have processing solutions designed to speed implementation in these plays. A new processing model that provides pre-engineered, factory-built modular plants enables the delivery and installation of NGL recovery plants at least six months faster than the traditional stick-built alternatives (Figure 1).
In addition, the approach does not require the operator to know upfront exactly how rich the gas stream will be. Much of the plant fabrication can occur before the gas composition is known. For operators developing new resources, these new capabilities are critical. This “fast gas” rapid NGL recovery model has helped to enable the shale gas revolution.
Speed remains of the essence in the NGL business. As mentioned, the typical timeline for a traditional NGL recovery plant can run 24 months from placing the order to startup. In part, this is because a sequential process is required. Once gas analysis is complete, equipment design starts with front-end engineering design (FEED). After FEED ends, procurement can start with ordering equipment. FEED and procurement are sequential steps in stick-built projects.
In contrast, modular plants provide a faster alternative by integrating FEED and procurement activities to optimize overall project scheduling and profitability (Figure 2). Some equipment is pre-engineered to start procurement from day one, and even before gas analysis is necessarily available. Once gas analysis is known, key value-added equipment is optimized for the project. Efficient value-added optimization allows FEED and procurement to be integrated in a single, seamless process. These modular plant project innovations enable getting to first gas much faster than with traditional NGL recovery solutions.
The skid-mounted aspect of the equipment ensures greater mobility and the ability to plug into challenging locations, providing quick system startup. Ideal candidates for modularization are packaged units sized for volumes to 200 MMcf/d. Larger plants can be accommodated with multiple trains (Figure 3). These skids are fit tested in a factory setting before being shipped to the production site to ensure that everything will flange up properly at the field site for a smooth startup.
Modular units have been developed to simultaneously reduce engineering time and have the ability to process a range of gas compositions. For example, a modular cryogenic facility design allows customers to preorder a plant before the final composition of the gas to be treated is known. The equipment can be engineered in the latter stages of manufacturing with comparatively small adjustments in order to ensure that final performance specifications are met. When the equipment is delivered to site, standard plants result in a vastly reduced field construction timetable.
In this way, the approach can recover NGL rapidly and enable customers to quickly monetize the widest possible range of natural gas compositions at the lowest installed cost.
The faster NGL recovery is quite valuable. A typical example of a 200 MMcf/d plant with a moderate NGL content (three GPM) will generate $10,000 in additional value each month in recovering the NGLs at current prices versus leaving them in the gas and receiving heating value for them. So earlier delivery of six months could potentially be worth $60,000, which can equate to 50 percent of the total installed cost of the full plant. Rapid NGL recovery is vital in improving the overall process economics of the shale gas/liquid hydrocarbon value stream.
Case Study Applications
Some of the real-life applications in U.S. shale basins over the past few years showcase the unique challenges customers face. For example, flat topography in the Eagle Ford Shale play might be replaced by more mountainous terrain in the Marcellus Shale. High altitude areas such as the San Juan Basin can be contrasted with lower-lying areas in Louisiana. Some areas produce lean gas with low to moderate levels of NGLs, while others have high levels of NGLs and demand more recovery with more associated equipment.
In the Marcellus Shale play, an operator acquired a 120 MMcf/d cryogenic unit with a refrigeration package to process natural gas containing six-seven GPM. After startup, the operator determined that he had higher gas rates than anticipated. The equipment supplier worked with the producer to find a solution, designing a flexible system that would meet the gas specifications. The customer then was able to push gas volume throughput to 115 percent of design and process 138 MMcf/d, enabling the company to secure more gas contracts.
Since the installation of the first plant, the site has increased from 138 MMcf/d capacity to 660 MMcf/d by adding two 200 MMcf/d cryogenic units with refrigeration and a 120 MMcf/d cryogenic unit with refrigeration. This has enabled the customer to go from breaking ground in a green field site to expanding into a major gas processing hub for the Marcellus area. Because of the success of this installation, the customer has returned to modular solutions for additional gas processing needs.
In the Eagle Ford Shale, an operator was aware that he had to process up to 600 MMcf/d of gas within two years (Figure 4). The operator partnered with the equipment supplier to make certain he could achieve this without consuming the time it would take to construct a stick-built plant. Adopting a modular approach saved time in project timeline execution and made rapid NGL extraction a reality.
The first 200 MMcf/d cryogenic plant installation was finalized in the third quarter of 2012, and the second 200 MMcf/d cryo installation was finalized in the first quarter of 2013. The final 200 MMcf/d plant installation is expected to be finalized in the first quarter of 2014.
A benefit that only a modular approach could provide was the ability to install the additional equipment and capacity in step with increasing gas production. Another benefit was to enable the operator to have three identical plants with the same list of common spare parts, which meant greater maintenance familiarity as more plants came on line. The operator was able to purchase common compression for each train, leading to a more homogenous operation.
When delivered by an experienced solution provider, solutions for CO2 removal, dew pointing and NGL recovery can be delivered as prefabricated, skid-mounted modules that provide feed composition flexibility and rapid NGL recovery. This lowers fabrication costs, speeds installation, and provides high on-stream efficiency.
Modular prefabricated solutions enable economic development of shale gas resources that otherwise pose daunting processing challenges and risks, given their inherent variability in gas composition. Operators using this approach benefit with more efficient operations and optimal monetization.
GUY LEWIS is strategic marketing director for the gas processing and hydrogen business of Honeywell’s UOP, which has focused on pioneering gas processing solutions for more than 60 years. With the acquisition of the Thomas Russell Co., UOP offers a range of technologies and modularized, packaged plants to enable shale and conventional natural gas producers to remove contaminants and recover high-value NGLs. Before joining Honeywell’s UOP in 2012, Lewis served as managing director for unconventional gas at the Gas Technology Institute. Prior to GTI, he was vice president for U.S. retail strategy and planning, vice president for commercial business solutions, and vice president for U.S. marketing fuel supply at BP.
TOM RUSSELL is founder of Thomas Russell Co. UOP, a Honeywell company, purchased a majority stake in the company in 2012, and its name was changed to UOP Russell. He formed Thomas Russell Co. in 2004, and his pre-engineered modular designs have been groundbreaking in gas liquid recovery plant design to reduce project schedule time and cost. Before pioneering new processing models at Thomas Russell Co., he manufactured processing equipment at T.H. Russell Co., which he founded in 1972. Russell holds a B.S. in chemical engineering from the University of Tulsa.
NEIL ECKERSLEY serves as business director and integration leader for the UOP Russell business of Honeywell’s UOP. He is responsible for integrating all aspects of Thomas Russell Co. into UOP, and has responsibility for the business’s profit and loss. Originally a catalyst and adsorbent development chemist, Eckersley has more than 20 years of experience in this field. He holds a bachelor’s in applied chemistry from Sheffield Hallam University in England.
For other great articles about exploration, drilling, completions and production, subscribe to The American Oil & Gas Reporter and bookmark www.aogr.com.