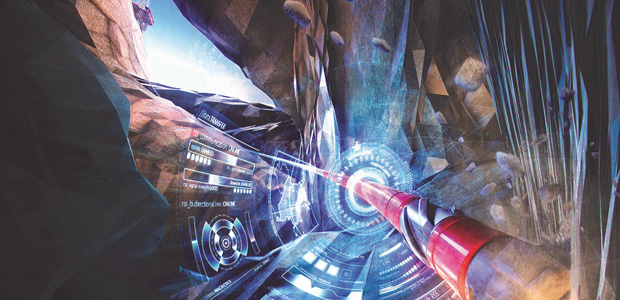
Drilling Innovations
RSS, MWD Technologies Optimize Performance In Challenging Environment
By Brian Jansky, Ricardo Arias, Ali Rodriguez and Stephen Forrester
HOUSTON–The volatility of oil and gas commodity pricing continues to drive titanic shifts in the way the industry does business. Five years ago, the primary performance metric for drilling–especially horizontal operations in unconventional assets–was the amount of time required to reach total depth and then to rig down and move onto the next location. However, when these wells were revisited for completion and production operations, many operators discovered that the quality of the wellbore was lacking. This problem, combined with a stringent focus on capital efficiency, has been a key factor driving the rise in drilled but uncompleted wells in U.S. shale basins.
These issues have come together to cause a collective rethinking of the way the industry drills wells, with far more focus put on wellbore quality and well placement. Drilling costs remain crucial, of course, but the primary concern today is constructing a completion-ready wellbore instead of simply maximizing penetration rates. One way of accomplishing these goals is to use a rotary steerable system to drill a smoother, less-tortuous borehole that is geosteered precisely into and through the targeted production zone.
A case in point is a project onshore Mexico that incorporated an advanced point-the-bit RSS with a rugged measurement-while-drilling system to help the operator drill a very challenging well through several extremely hard formations while achieving directional drilling and wellbore placement objectives. Even with the overall emphasis on wellbore quality, the drilling portion of the project was completed ahead of schedule and below planned cost. The well was the area’s first horizontal application. It targeted a Middle Cretaceous formation, and the geologic conditions mirror those in some U.S. resource plays with abrasive interbedded formations.
Advanced RSS System
Recognizing that the well’s lithology would prove difficult to drill, the operator decided to implement a fully automated closed-loop, point-the-bit RSS to achieve highly accurate steering in the complex downhole environment. Another objective for using RSS was to help reach the drilling target and producing zone more effectively while adhering, at minimum, to planned drilling days. The RSS system features a functionality whereby it can be programmed at surface to hit a drilling target and then effectively left on “cruise control” until the target changes.
In this project, if the well path deviated from the targeted zone, the system was set to autocorrect its course without driller input, automatically recalculating the trajectory every 96 seconds. This eliminates the need for data downlinking to change course or enter a cruise control mode, which takes additional time.
In addition, incorporating an RSS with an onboard guidance system enabled the operator to control inclination and azimuth via closed-loop communications with surface and real-time feedback, enhancing the ability to geosteer and place the well correctly. The point-the-bit system proved ideal for this application, where it was crucial to drill a wellbore devoid of tortuosity and drilling dysfunctions.
The operator incorporated a rugged MWD system into the BHA design to provide real-time directional guidance and geological information through the problematic curve and lateral sections. One major challenge in the project was the hardness of the rock, as well as the variety of rock types throughout the well. By incorporating an MWD system that could take resistivity logs while enabling real-time monitoring of drilling parameters, the operator sought to overcome the complex downhole drilling environment while obtaining the information necessary to effectively place the well as the RSS geosteered through the lateral.
Optimizing ROP and extending equipment life by having this information were secondary benefits that further reduced drilling cost in line with the optimized BHA design developed by the well planning and engineering analysis team.
Case History
Figure 1 shows the well plan, including the various formations and casing sizes. The yellow line indicates the operator’s planned trajectory, while the red line is the actual well. Despite the difficult formations, the trajectory aligned almost perfectly with the original plan.
Because of the formation’s hardness, conventional tools were not an option for drilling the curve and lateral. The operator had encountered extremely poor hole conditions, which were leading to increased drag on the BHA, wellbore instability and fluid loss. This was compromising directional drilling efficiency as well as persistently decreasing penetration rates, which were affecting the well’s cost versus the authority for expenditure.
The project began with a comprehensive engineering analysis by teams in both Houston and Mexico. The teams examined the well plan, modeled and determined the influence of torque and drag on the drill string, and analyzed the design and configuration of the BHA and hydraulics systems.
The well’s lithology was the main cause of the operator’s poor drilling performance and the driving factor behind the search for a better directional drilling solution. The operator’s wellbore objective required drilling the curve section in geology that transitioned between multiple interbedded formation layers that consist of a wide variety of multistratigraphic rock types, including marls, bentonite shale, shale loam, mudstone and wackestone with microfractures presenting pyrite.
The landing zone and lateral targeted a Middle Cretaceous formation made up of mudstone, wackestone, pyrite, black shale and fragmented flint. The well path called for a catenary curve building from 3.5 degrees per 100 feet and landing at an inclination of 90 degrees before extending into a 1,640-foot lateral. The operator set the expectation that this project would entail approximately 45 days of drilling time, given the formation issues and equipment-related limitations.
The engineering analysis revealed that an optimized BHA configuration for this project would consist of a 4¾-inch RSS, MWD tools, and a multifrequency resistivity tool with gamma ray capabilities and extended-life batteries. Running such a configuration with RSS was the only feasible option for drilling this well, since slide drilling was impossible using a conventional mud motor with a bent housing. The operator chose an RSS to address several other issues as well, including wellbore quality, hole cleaning, and directional drilling efficiencies.
The nature of a directional wellbore drilled with RSS lends itself to a smoother well profile, with the RSS using autonomous near-bit sensors to update wellbore trajectory in real time. A combination of 100% rotary drilling and full rotation stabilizers allowed cuttings agitation, while a through-bore internal diameter of the system accommodated optimal flow rates. With projected slide drilling rates as low as 3.28 feet/hour and rotary drilling rates better than 32.8 feet/hour, the team recognized that eliminating the need for slide drilling would increase actual daily footage drastically compared with projections.
The MWD tool was incorporated into the BHA design to provide real-time gamma and resistivity measurements. The data was transmitted to surface through mud-pulse telemetry and cyphered by a surface transducer integrated onto the rig’s pressure system along with an MWD data visualization platform. The MWD system helped the operator to better understand wellbore geology and downhole location. Additionally, the system also provided a higher tolerance for lost circulation materials, as the operator expressed concerns for losing drilling fluid volume for the duration of this operation.
Drilling Road Map
After selecting the suite of technologies and designing the BHA that best met the operator’s needs for this application, the operational planning phase began. This included an extensive examination of the well’s drilling parameter requirements and analysis of the BHA for directional tendencies to provide a base for output expectations. Further analysis of the combination of drilling parameters and BHA configuration allowed a drilling “road map” to be developed that more formally advised of expected conditions.
Importantly, the road map also distributed responsibilities between the operator and service provider so that both parties would know exactly what to do in case of a technical issue or HS&E event. By incorporating the drilling road map moving forward, the operator also expected to limit the opportunity for defects within the required drilling parameter range.
The rig site team was deployed and operations began. The initial phase consisted of drilling the wellbore’s curve section. The BHA was picked up at 5,906 feet at an inclination of 20 degrees/100 feet and a direction of 320 degrees. The operator achieved the curve rate of 3.5 degrees/100 feet without difficulty, given the capability of the RSS to build up to 12 degrees/100 feet.
The RSS was programed to complete this task with virtually no input from the driller and onsite team. The system used an uploaded well plan and well plan targets to automatically geosteer the drill bit in accordance with the plan. This allowed the rig site team to focus more closely on monitoring downhole conditions via the MWD system while using the selection of optimal drilling parameters as outlined in the drilling road map. The gamma ray and resistivity logs provided by the MWD system also were vital to this phase of the operation; onsite and remote office-based geologists used this information to ensure accurate landing within the target zone. Per the plan, the operator landed the well successfully at 8,386 feet TVD at an inclination of 90 degrees.
Once the curve section landed, the rig site team entered the second phase, which consisted of drilling the lateral to TD. In today’s market, a lateral of only 1,640 feet would be considered relatively short, but this was the operator’s first attempt at an unconventional well profile in this formation lens. While drilling the lateral, the operator encountered stringers of chert in concentrations of 10%-15% or more, but the BHAs performed as expected, limiting downtime. A total of four successful BHAs were deployed with no tool failures, consistent ROP, and excellent wellbore guidance to mitigate wellbore tortuosity. The MWD system collected logging information for 100% of the formation, providing the operator critical insight to complete the lateral in zone and on target, reaching TD at 9,580 feet TVD.
Notable Achievements
The operator had several notable achievements on this well. It was the first well to reach the Middle Cretaceous formation, the area’s first horizontal application and the fastest well drilled in the area when compared with all relevant offsets. Most importantly, the drilling phases were completed in only 25 days versus the operator’s plan of 45 days, representing nearly a 45% reduction. The drilling AFE came in significantly lower than budgeted, saving the operator resources and capital for use on the next project phase.
The Mexican project is relevant to some U.S. plays featuring hard and abrasive interbedded formations. This list includes the Bakken/Three Forks in the Williston Basin and the Wolfcamp and Spraberry in the Midland Basin. Although ROP is not as limited in plays such as the Spraberry, for example, where complex layers of sandstone, mudstone and siltstone are interbedded with shale, the concern for geosteering to hit the target zone is highly relevant–particularly in areas such as the Spraberry, where low porosity and permeability and naturally fractured rocks further complicate hydrocarbon flow and recovery. Other plays in the Permian Basin and the Granite Wash face similar challenges.
Run histories from projects such as the one in Mexico have been compiled to build a drilling plan for areas in the United States with hard formations and interbedded lithologies. Such projects pose a similar challenge in that they require a precisely tailored combination of tools and technologies in the BHA to drill ahead appropriately while maintaining an extremely straight wellbore.
In one Granite Wash project, for example, an operator was dealing with a complex geology of shale, chert and sandstone with a hard, granitic basement. In this situation, log analysis also was more difficult. Using the run history of a similar project in Mexico, Gyrodata advised on exact BHA configuration and modeled the potential drilling path that could be programmed into the RSS at surface to obtain comparable results. This type of work continues throughout North American basins, with previous projects informing the engineering analysis and execution phases of new projects to improve each time.
The oil and gas industry is entering a phase where business success depends on calculated decision making and prudence when drilling wells that may not be economical or returns fall short of expectations. In this environment, it will be critical for operators to continue to push their projects’ operational and performance limits. To achieve the dual goals of drilling better wells faster into hydrocarbon reservoirs that also produce at higher rates for longer, implementing directional technology packages that enable enhanced geosteering and real-time data collection is a proven way of transforming an average prospect into something extraordinary.
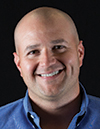
BRIAN JANSKY is an operations technical support (OTS) supervisor at Gyrodata, where he works with other members of the OTS group to develop solutions to customer problems and find ways of increasing directional drilling efficiencies. Jansky brings 20 years of oil and gas experience to the company, and has specialized knowledge in drilling optimization, BHA design and rotary steerable technology.
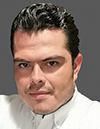
RICARDO ARIAS is an operations supervisor for Gyrodata based in Villahermosa, Mexico, where he oversees regional field operations for the company’s directional drilling services group. Arias has 13 years of previous experience, including previously working as a gyro surveyor and field engineer at Gyrodata, a logging-while-drilling engineer at Weatherford, a directional driller and southern region coordinator for Halliburton/Sperry Drilling.
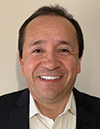
ALI RODRIGUEZ is vice president of drilling services operations at Gyrodata. He began his career in Colombia as a rig site supervisor and drilling engineer for Hocol Colombia. Rodriguez moved to Canada in the late 1990s to work as an operations manager for Weatherford’s drilling services division. His career took him to Houston in 2010 to manage the Northeast and Mid-Continent areas for Weatherford’s directional drilling division before he started at Gyrodata. He holds a degree in petroleum engineering.
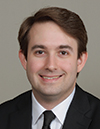
STEPHEN FORRESTER is content development manager at Gyrodata, where he oversees technical writing and strategic communications initiatives for the company’s gyroscopic surveying, drilling services, and wireline product lines. He previously worked at National Oilwell Varco in technical writing roles. Prior to that, Forrester worked in the oil and gas division of Lloyd’s Register, where he was a technical editor for reports on inspections and certifications of subsea blowout preventors.
For other great articles about exploration, drilling, completions and production, subscribe to The American Oil & Gas Reporter and bookmark www.aogr.com.