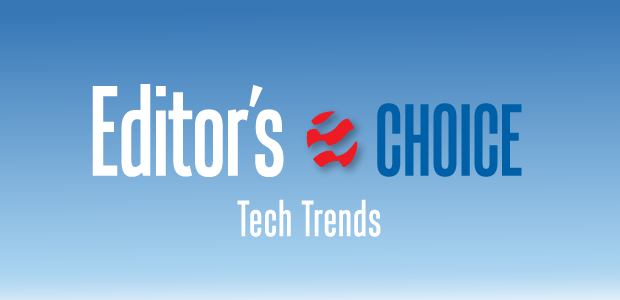
Advanced Technologies Drive Ongoing Innovation In Horizontal Resource Plays
By Danny Boyd, Special Correspondent
Unparalleled technological advancement has driven every step in the maturation of the U.S unconventional oil and gas industry during the past two decades. Tight oil and shale gas plays are producing more than 8 million barrels of oil and nearly 80 billion cubic feet of dry gas a day, but with such a significant role in the energy supply mix, it is easy to overlook the simple fact that horizontal resource play development is still a relatively young science that has lots of growing room ahead of it.
So while multiwell pad operations, long-lateral wellbores, and high-rate hydraulic fracturing designs with large fluid and sand volumes have quickly become the norm, innovation very much remains the watchword of the day. Operators are continuing to evolve drilling and completion practices in all the major shale basins, including optimizing well siting, lateral spacing, completion engineering, well site operations, and production processes–the blocking and tackling of any horizontal well success.
Operational innovations have boosted the effectiveness and reach of tried-and-true technologies such as microseismic, logging-while-tripping (LWT), and downhole pressure and temperature monitoring, among others. All of these solutions are driving gains in well performance and bottom-line economics. In addition to downhole improvements, however, operators are implementing next-generation technologies and strategies for reducing emissions and managing water resources to demonstrate to environmentally conscious end users and investors that the industry is fully committed to elevating ESG performance.
Holistic Approach
HighPeak Energy Inc. uses a holistic approach to deploying the latest technologies in a continual quest for ways to improve completions and water handling on its oil-weighted Permian Basin acreage in Howard County, Tx.
This comprehensive approach includes deployment of microseismic enhanced in recent years by the advance of real-time event observation (RTO), which has made the technology an essential element of completion optimization and execution instead of a “nice to have” to be shelved during tight times, says Chief Technology Officer Alan R. Huffman.
HighPeak Energy is using microseismic monitoring with real-time event observation and 3-D subsurface velocity modeling to gauge stimulation treatment effectiveness and make adjustments on the fly. HighPeak also is deploying fiber optic sensors to create a grid of permanent monitoring wells to monitor stimulation operations, and analyzing cuttings to evaluate rock/fluid interactions. At its Flat Top project in Howard County, Tx., the company has installed a 20-inch flowline to transport produced water to active frac locations.
Microseismic using only a single monitoring well is typically insufficient to obtain accurate event location data during stimulation, so in 2021 the company deployed it on three triangulated vertical wells that monitored a four-well pad, accessing data multidirectionally via vertical arrays of geophones, he reveals.
RTO–available for review within a minute or two during operations–was combined with comprehensive 3-D subsurface velocity modeling to pinpoint within 10-20 feet the location of acoustic events during stimulation, allowing the company to immediately gauge treatment effectiveness and make near-real-time adjustments, Huffman explains. The technology helped determine how varying stage sequencing, pump rates and diverter use led to different stimulation results.
“All of the adjustments we made improved our well performance because we did a properly integrated microseismic program with the correct acquisition geometry coupled with a robust 3-D earth model for location of the events, monitoring diagnostics as they occurred and setting up the experiment properly to learn from it,” Huffman says. “We looked at things holistically with a group of technologies, as opposed to using one technology. From this experiment, we determined the best approach to stimulating the specific reservoir targets in our leasehold.”
Downhole Fiber Optics
To contribute to the long-range goal of achieving the electric oil field concept, HighPeak is working with a Boston company developing a low-cost fiber optic technology which, when commercialized, will allow sensors to be cemented permanently in place behind the casing. Huffman explains that this will create a grid of permanent monitoring wells that provides near-field monitoring of active stimulation operations, far-field monitoring for earthquakes, and also enables passive listening for long-term production signals in the reservoirs.
“The goal of this integrated technology approach to seismic monitoring will be to better understand and discriminate between acoustic emissions that are due to stimulation operations and those that are unintended such as the recent earthquakes that are believed to be related to deep disposal wells,” Huffman comments. “When fully implemented, this approach will complement the existing TexNet seismic monitoring program that relies primarily on surface seismograph stations.”
Fluid/Rock Interactions
Completion improvements also are coming from a greater understanding of how fluids are interacting, in some cases negatively, with unconventional reservoirs, Huffman offers. Freshwater or frac water that is out of chemical equilibrium with a reservoir–and that fails to more closely match that of produced water from a formation–can diminish hydrocarbon yields because of clay swelling and other negative interactions between reservoir rock and fluids, he says.
HighPeak now uses almost 100% produced water for its fracturing operations. At its Flat Top acreage north of the city of Big Spring, the company has installed a 20-inch flowline to move produced water to any locations where it is needed for stimulation operations, Huffman points out.
The company also routinely collects wellbore cuttings to monitor rock/fluid interactions and better understand chemical reactivity in individual reservoirs with evaluations necessary zone-by-zone because of chemical differences, he says.
Advancing Stimulation Design
Civitas Resources is Colorado’s largest pure-play operator in the Denver-Julesburg Basin. It was formed in 2021 from the merger of Bonanza Creek Energy and Extraction Oil & Gas, with additions before and after of HighPoint Resources and Crestone Peak Resources. The new company is relying on advanced stimulation designs coupled with legacy drilling and completion expertise as it works to consolidate operations across 525,000 net acres, says Chief Operating Officer Matt Owens.
Civitas has done several tests with technology that logs while tripping pipe out of the hole to specifically identify and target areas with more brittle rock and focus less on stimulating more ductile rock, Owens explains.
“It is too early to draw anything definitive, but it appears in this very brief time to be showing some benefit, so it is something we are going to continue experimenting with,” he says.
Civitas Resources is in the process or repermitting and respacing planned drilling locations across its consolidated 525,000-net-acre D-J Basin leasehold to drill longer laterals with fewer wells, including two-, three-, and eventually four-mile laterals instead of the parallel one-mile wells typically drilled in the past. Each two-mile lateral replaces two, one-mile laterals, and each three- and four-mile lateral essentially replaces three or four one-mile lateral wells.
The company also is placing a major emphasis on extreme limited-entry perforating, which maximizes the amount of pressure drop across each perforation to ensure that as much sand as possible can move throughout the stage and that frac fluid does not leak off into one particular set of perforations during stimulations of Codell and Niobrara benches, Owens explains.
Assessments are ongoing of the number of perforations being shot, perforation diameter, and horsepower at the surface as part of an undertaking to mathematically model the erosion on perforations from sand and fluid movement, based on friction pressure at the surface, and how to make necessary adjustments, he continues.
Longer Laterals, Fewer Wells
Legacy expertise drilling step-outs from fewer pads to tap into distant minerals in more urban areas in the west are helping make the permitting process easier as Civitas consolidates locations and extends laterals across its position. Owens says changes have involved about 100 wells with pads now designed for between eight and 20 wells.
“Everywhere where two, one-mile wells in parallel were planned we have converted to one two-mile well,” he explains. “If there was a third one-mile well planned, we turned that into one three-mile well. We are also looking at four-mile laterals in the future. We are in the process right now of repermitting and respacing units to be one longer lateral rather than multiple pads with shorter laterals.”
The company continues to assess frac designs that vary across its position, depending on geological depths, reservoir pressures and hydrocarbon makeup. In the east, oil has a lower API gravity. In the west, deeper targets include more rock anisotropy and higher pressures with a gassier mix and higher API gravity oil, Owens points out.
In the south, where oil is heavier, Civitas is testing larger spacing intervals and bigger frac designs similar to the east, Owens details. The company is pumping up to 60 barrels of fluid and 1,800 pounds of northern white sand per lateral foot to determine whether the rock will produce more like the eastern area, which responds well to more intense completions, or the western area, where Civitas can pump slightly smaller jobs and still maximize economics, he says. In the west, the standard frac design is predominantly 20-30 barrels of fluid and 1,000 pounds of sand per foot.
Frac stages in the Niobrara average 180-200 feet. For the Codell, stages typically range from 200 to 250 feet. After reviewing results and science, Owens notes Civitas is leaning more toward slickwater fracs, but is considering a gel fluid in the event of stimulation challenges.
To reduce the chances of screen-out on future planned four-mile laterals, the company is testing a new technology from Disruptive Downhole Technologies on shorter laterals that eliminates frac plugs by running a ball seat instead of a frac plug, he explains.
On all its new drilling sites, from pad construction into the production phase, Civitas is using real-time air monitoring and assessing development of technology that involves using grid power coupled with portions of field gas to produce electricity on site, Owens concludes.
Pushing Boundaries
Armed with 14-years of unconventional technical expertise concentrated in the Marcellus Shale, the operations team at Greylock Energy LLC is not afraid to push the boundaries of completion engineering as part of its ongoing research to identify the most efficient design, says Chief Operating Officer Ryan Deaderick.
Earlier, Marcellus operators reduced stimulation volumes for various reasons, but Greylock has continued to experiment and realize increased recoverability by pumping larger frac volumes, he says. While weighing results from various frac stage spacings, lateral spacings and stage concentrations, the company’s completions are now done in 200-foot stages with 3,000 pounds of northern white sand per lateral foot, Deaderick details.
The team will stimulate with five or six clusters per stage and occasionally “goes against the academic grain” and adds clusters to push all the sand into the shale, he adds. “We’re not restricted here to the limited-entry philosophy of hydraulic fracturing,” Deaderick notes.
Using five-year estimated recovery rather than a standard EUR calculation as its metric, Greylock Energy is realizing increased recoverability as it has pushed the boundaries of completion engineering in its Marcellus development program through pumping larger frac volumes, various frac stage spacings, lateral spacings and stage concentrations. The company’s typical design is now 16-well pads with 10,000-foot laterals spaced 600-1,200 feet apart, with 200-foot stages with five or six clusters per stage, and 3,000 pounds of northern white sand pumped per lateral foot.
Geosteering logs on adjacent wells and ample 3-D seismic are helping make the most of economies of scale on pad configurations and well siting. Currently, 16-well pads are being used on acreage where two different pads were planned initially, reducing surface disturbance while allowing for 10,000-foot laterals, Deaderick states.
Lateral spacing is now up to about 1,000 feet on average, although wells have been down-spaced to 600 feet and up-spaced to around 1,200 feet at times, he adds, with the company routinely conducting chemical tracer programs to characterize any communication between laterals.
Although rare, Greylock will skip a stage or two around a fault or other feature, but designs its program in Greene County, Pa., largely to drill between faults, he says. The company has experimented with various logging technologies, but treats the Marcellus for what it largely is in Greene County: a thick homogeneous rock formation.
Through all its metrics for success, Greylock has adopted a “5-ER” standard, representing the five-year estimated recovery of a well, rather than a standard EUR calculation, Deaderick points out.
“We have found that EUR lacks precision because it looks at total recovery from a well without considering the economic component very well,” he remarks. “With 5-ER, we are looking at what making a change operationally does to five-year recoveries, because that is driving the financial engine and helping us understand if we are maximizing the recoverable potential from a well.”
With solid ESG performance imperative, the company is deploying new technologies to reduce its environmental impact, Deaderick adds. On one recent Greylock project, Energy Water Solutions’ VOX™ evaporation technology enabled the company to reduce flowback water handling from 5,000 to 4,200 bbl/d, he reports.
The company continues to benefit from cost reductions from drilling and frac fleet automation, Deaderick says, including automated systems with both diesel and natural gas distribution for dual-fuel pumps that keep systems going during stimulation and eliminate a diesel truck constantly traversing locations to fill fuel tanks.
Emissions Detection Program
With downhole success, Jonah Energy LLC continues to add technologies to its emissions detection program as it works to influence a shift to reporting real emissions levels over calculated ones to demonstrate that natural gas is a clean, reliable energy source for end-users, says Paul Ulrich, vice president of government and regulatory affairs.
“One thing we are very cognizant about and appreciate is that the West Coast is demanding cleaner energy resources,” says Ulrich. “We feel in order to respond to the market, customers, regulators and policymakers, we have been pushing and continue to push the envelope on providing the cleanest natural gas in the system.”
More than a decade ago, the company first deployed forward-looking infrared cameras throughout its operations in the Jonah Field of Wyoming’s Green River Basin. Since then, the company has added fixed monitors in the field for 24-hour surveillance. Inspections are done monthly, over and above state requirements for quarterly inspections and federal requirements for biannual reviews.
Jonah Energy is contracting with vendors Scientific Aviation, Bridger Photonics, and other companies to conduct drone flyovers and airborne gas mapping LiDAR analysis. Practical operational innovations include the use of natural-gas-powered drilling rigs and consolidation of pad locations, he says.
Jonah Energy LLC is applying a number of technologies to demonstrate that natural gas is a clean, reliable energy source–from natural-gas-powered rigs to drone flyovers and fixed infrared field monitors for 24-hour emissions surveillance. But a key innovation is its work to measure and report actual emissions levels instead of calculated levels, which in November, helped it become the first U.S. company to achieve a gold standard rating for emissions data submitted to the United Nations Oil and Gas Methane Partnership 2.0.
But a key, forward-looking innovation includes its work to identify actual emissions levels instead of relying on mandated calculations based on engine size, leak factors and other measures that make calculations highly variable, Ulrich says.
“Actual measurement is the path that needs to be taken for the customer and others to have confidence in what we are reporting versus calculations,” he says. “In our mind, it’s really that simple. We want to be able to provide that confidence and transparency to the marketplace.”
To that end, in November Jonah Energy became the first U.S. company to achieve a gold standard rating for emissions data submitted to the United Nations-sponsored Oil and Gas Methane Partnership 2.0. Ulrich points out.
Jonah Energy reported 85% of all emission sources from operated assets using actual measurement and detailed engineering calculations rather than generic emission factors, Ulrich reports. Independent analyses came up with a path to direct measurement and all information was verified by a third party, he adds.
“It is a strong signal to the market, to customers, policymakers and others that we take emission reductions very seriously; serious enough that we have charted a path to direct measurement and we are the first in the country to do so,” Ulrich comments.
The concept of responsibly produced gas is in its infancy, he says, but the company is involved in discussions with other business partners throughout the supply chain on how transparent and credible the company’s numbers are and what the pathway to gold standard means to the industry as a whole.
“We want to be able to demonstrate what’s possible and how natural gas can play an ongoing foundational role in our energy needs in this country,” Ulrich says. “But in order for us to do that, we need to produce natural gas cleaner and demonstrate that we are doing that.”
For other great articles about exploration, drilling, completions and production, subscribe to The American Oil & Gas Reporter and bookmark www.aogr.com.