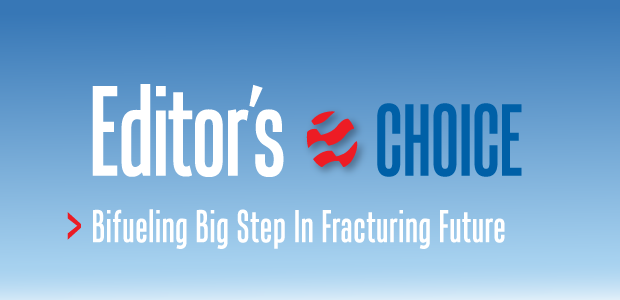
Bifueling Big Step In Fracturing Future
By David G. Gallagher
HOUSTON–Thanks in large part to the entrepreneurial spirit of U.S. independent oil and gas producers, the great “shale gas and tight oil boom” is fueling a tangible rise in domestic oil production, a surplus in natural gas supplies, and for the first time in decades, a more secure energy future for the United States. However, given the cyclical nature of the oil and gas industry throughout its long history, the question has to be asked, “Is this sustainable?”
It can be. But that is only possible if the industry and the nation at large continue to pursue and adopt ongoing technology innovations that promote more sustainable solutions in terms of efficiency, effectiveness and environmental stewardship.
There is no doubt that the upstream industry is making strides in efficiency and resource usage to maximize the production potential of prolific wells. The lessons learned in the early days of Barnett Shale development have evolved into a litany of proven best practices being deployed in shale gas and tight oil plays all across North America. The result is that the industry is delivering wells with optimal lateral lengths, drilled from highly efficient multiple-well pads and using completion techniques that drive ever-rising reserves recovery.
In terms of effectiveness, the industry also is moving to embrace a more disciplined approach to asset development that maximizes recovery across entire fields. This starts with an improved understanding of shale and unconventional reservoirs and extends through optimal well and fracture placement. This, combined with specialized fracturing fluids designed to maximize regained conductivity in ultralow-permeability reservoirs, slows decline curves that tend to be significantly steeper than in conventional reservoirs, and is one of the key reasons that domestic hydrocarbon production continues to rise.
Finally, the oil and gas industry has taken great strides in the area of environmental stewardship. The industry has undertaken a number of key initiatives around well bore integrity, chemical disclosure, groundwater protection and emission reductions, to name only a few. As a result, there has been a reduction in the environmental impact of shale and tight oil development operations and improved transparency in all phases of drilling, completion and production operations.
Of course, to ensure a sustainable future, the industry should be the first to embrace those innovations that promote better efficiency, increased effectiveness, and environmental stewardship–specifically those technologies that facilitate the efficient use of the very energy resources oil and gas companies produce, while simultaneously pushing the envelope on environmental performance.
One solution to help the industry move forward in closing the loop for a more sustainable energy future is bifuel hydraulic fracturing technology.
Paradigm Shift
For decades, diesel fuel has been the fuel of choice to power the high-horsepower pumps employed in hydraulic fracturing operations around the globe. While effective, this method is inefficient in terms of emissions, supply chain and risk reduction. The millions of gallons of diesel fuel used in hydraulically fracturing tens of thousands of wells each year require multiple modes of transportation and treatment to first undergo the conversion from crude oil to diesel, and then be transported back to well sites to fuel the pumps and generate hydraulic horsepower.
Burning a mixture of natural gas and diesel, bifuel pressure pumping systems are capable of operating with no reduction in hydraulic horsepower generation. Replacing a significant percentage of diesel with LNG or CNG not only slashes emissions from the engines driving stimulation pumps during hydraulic fracturing, but also provides important economic, safety and operational benefits.
The exclusive use of diesel fuel generates emissions that impact an operation’s carbon footprint, while adding safety risks and potential nonproductive time because of the complexity of diesel refueling operations. Is there a better way to fuel the enormous amount of horsepower amassed on a well site to facilitate hydraulic fracturing operations? Can a paradigm shift to natural gas help the industry optimize not only with respect to the environmental impact, but also in terms of the overall economics of hydraulic fracturing without sacrificing the operational performance of traditional diesel-fired equipment?
The answer to these million-dollar questions is decidedly yes. A method for using natural gas to help power frac operations was envisioned and tested early in this decade using producers’ “line gas” as the immediate fuel replacement. While the initial experiment was successful, the necessary investments required by major service providers in this fuel-swapping concept did not occur until a few years later, when higher diesel prices, increased gas availability, and growing horsepower demand combined to make this approach more economically viable for both service providers and their customers.
The first steps toward a more sustainable approach to horsepower generation were seen late last year as service companies began introducing a new breed of hybrid pumps capable of replacing a significant percentage of diesel fuel with cleaner-burning natural gas. These pumps, typically referred to as bifuel or dual-fuel, have moved from the white board to the field in record time.
All types of heavy-duty fleet trucks–from long-haul tractor-trailers to municipal garbage trucks–and growing numbers of light-duty commercial and private-use vehicles are making the switch to natural gas. Even marine vessels ranging from giant cargo ships to tug boats and ferries are being designed with gas-driven power systems.
Win-Win Proposition
Building on the trend toward using cleaner-burning and cost-efficient natural gas in land and offshore transportation, the rationale for converting hydraulic fracturing horsepower to natural gas is highly compelling for the oil and gas industry. Not only does it improve operational efficiency, lower costs, and reduce health, safety and environmental impacts, but it also capitalizes on the availability of the natural gas supplies operators have unlocked in unconventional resource plays across the country.
The newest and most advanced models of bifuel pumps for hydraulic fracturing burn a mixture of natural gas and diesel, reducing diesel use by up to 70 percent. They are capable of operating efficiently with no reduction in the hydraulic horsepower generated. The ability to maintain the equivalent horsepower performance of a traditional diesel system, using instead a bifuel mixture, is of critical importance in hydraulic fracturing operations.
The environmental benefits are significant. Converted bifuel fleets are designed to meet all relevant U.S. Environmental Protection Agency emissions standards, and to reduce nitrogen oxides, carbon dioxide, particulate matter and other emissions. Plus, bifueling not only reduces emissions from the engines driving the stimulation pumps, but also less fuel is needed to keep the pumps operating. By substituting natural gas into a converted diesel engine, the bifuel alternative can operate twice as long as engines running solely with onboard diesel. In addition, it has the added value of improving job site safety by eliminating refueling demands during operations.
Most of the early applications for these bifuel pumps have successfully used either liquefied natural gas or compressed natural gas as a replacement for a high percentage of a project’s normal diesel usage.
One of the initial applications of bifuel pumping technology was a hydraulic fracturing job conducted in the Eagle Ford Shale on a well operated by Cheyenne Petroleum Co. The operator was interested in using converted bifuel units because of the potential savings by cutting diesel consumption, as well as the potential for long-term emissions reductions.
In all, 35 stages were pumped using three of the converted units during each stage. During the job, the operation reached a 65 percent substitution rate (i.e., 65 percent of diesel fuel was replaced with LNG) with no loss of horsepower. The job basically pumped the same as a 100 percent diesel job, but with the added economic and environmental benefits.
Shortening The Supply Chain
However, while yielding significant benefits, the bifuel approach has so far done little to address an inefficient supply chain model. Even using LNG, the model frequently requires natural gas to travel hundreds of miles and go through extensive energy-consuming processes in order to fuel an operation that literally could be located less than one mile from the wellhead where the methane was produced originally.
As shown in Figure 1, when fueling a diesel-powered frac operation today, the fuel supply chain is long and complex, with costs added every step along the way. In the near future, bifuel operations will be optimized routinely by tapping wellhead or line gas in the field to simplify logistics and maximize efficiency.
The industry is doing itself a disservice if it lets LNG-powered fracturing operations become the final destination on the road to an energy optimized model. The LNG-powered bifuel pump should be a bridge to a future where the natural gas production from the initial well (or from a previous pad) in a shale development program powers the stimulation treatments for subsequent wells. In fact, the model for this new paradigm is taking shape already as a handful of forward-thinking oil and gas producing companies have initiated strategies to power drilling rigs with field gas.
The genie is out of the bottle. The most likely scenario envisions natural gas as the prime mover for hydraulic fracturing horsepower before the end of this decade. Ultimately, full commercialization will require enhanced technologies, processes and logistics to efficiently, safely and effectively capture, scrub and transfer wellhead gas. Over time, this incremental advance in technology will lead us to consider the economic and energy benefits of using 100 percent natural gas-fueled or perhaps even electric pumps.
This transition need not be long, arduous or restrained by paradigms. If managed properly, line gas-powered pumps should quickly become the industry norm, yielding a number of environmental and operational benefits, including fewer flaring activities, reduced transportation requirements and lower total energy consumption.
Ultimately, the industry will close the loop on shale gas operations to ensure a long, safe and profitable future while creating a clear vision of long-term sustainability that other industries will strive to emulate.
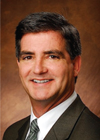
DAVID G. GALLAGHER is vice president of production enhancement at Baker Hughes. He is responsible for leading the global stimulation strategy for the company’s pressure pumping business. He has more than 30 years of experience in oil field services, starting his career as a field fracturing engineer, and since serving in various senior management roles in the areas of strategy, marketing, operations, sales and stimulation technology development. Gallagher has extensive domestic and international business management experience and worked for more than 10 years in Latin America. He holds a bachelor’s of engineering from the University of New Mexico.
For other great articles about exploration, drilling, completions and production, subscribe to The American Oil & Gas Reporter and bookmark www.aogr.com.