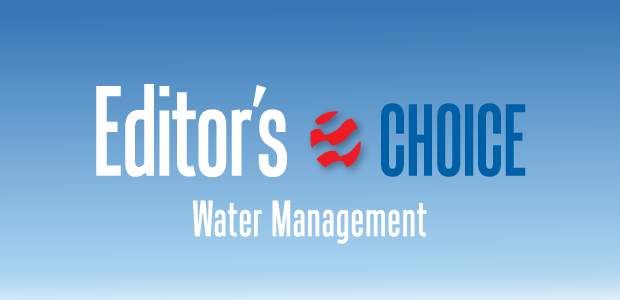
Climbing Water Cuts, Produced Water Volumes Create Challenges In Permian
By Gregory DL Morris
It was not long ago that Permian Basin producers were scrambling to identify enough water resources to sufficiently supply hydraulic fracturing operations. To “feed the beast,” some large operators were even working jointly with municipalities to upgrade wastewater treatment plants and secure direct access to treated wastewater. It is amazing how quickly the tide has turned over the past few years as the industry has developed Permian tight oil plays and as horizontal wells spud over the past decade have matured to the mid and late stages of the lifecycle.
As the wells age, water cuts tend to climb, especially in the Delaware Basin. Suddenly, water is no longer difficult to come by. In fact, the situation has so completely reversed that the chief concern of oil and gas operators has flipped from “where are we going to find enough water to fracture our wells?” to “what are we going to do with all the co-produced water coming from our wells?”
Since 2017, produced water volumes are up more than 350% in the Permian, with the average well now lifting nearly 3.5 barrels of water to surface for every one barrel of oil. According to data from B3 Insight, the Permian is forecast to produce 22.3 million barrels of water a day on average in 2025–enough to fill some 925 million one-gallon jugs every 24 hours. The Delaware is projected to average 13.6 MMbbl/d and the Midland 8.4 MMbbl/d, with 16 MMbbl/d of that total going to disposal and the remainder recycled and reused.
Aligning with B3 Insight’s 2025 forecast numbers, 21 MMbbl/d was produced across the Permian in the third quarter of 2024, according to Robert Crain, executive vice president of Texas Pacific Water Resources, and chair of the Permian Basin Water In Energy Conference. Prior to TPWR, Crain led water resource development efforts for EOG Resources across multiple basins, including in the Permian and Eagle Ford.
Although treating and recycling has emerged as a best practice, Crain estimates that 25-30% of produced water is currently being recycled. He points out that recycled volumes vary greatly from one development area to another. Even so, in many areas, producers utilize as much as 90% produced water for their hydraulic fracturing volume demand.
“But there is just so much water,” Crain avers. “And because water cuts are now approaching 4-to-1 in the Delaware and close to 3-to-1 in the Midland, there is no way to frac our way out of the water situation.”
Finding The Answers
Out-of-basin disposal and beneficial reuse are part of the answer, “and we were early to the game in those,” says Crain. Applying produced water to enhanced oil recovery projects is one use, he adds, “but waterfloods tend to be in the vertical zones, outside the fairway for unconventional development. And the volumes needed for vertical well EOR pale in comparison to what is being produced from horizontal wells.”
Who pays whom for what is highly variable, as produced water swings through the value proposition, at times representing a value-adding resource and at other times little more than a waste stream with an associated management cost. “We do it 10 different ways every day,” Crain remarks. “That is one of the great things about the Permian. There are a lot of options for managing produced water.”
TPWR has the only land-application permit for beneficial reuse as part of research projects with Texas Tech University and New Mexico State University. Potential applications include agriculture irrigation and livestock watering. However, Crain acknowledges that beneficial reuse is challenging on a commercial scale.
“Not counting field trials, there are zero beneficial reuse volumes currently,” he details. Salinity and dissolved minerals are much higher than seawater, so conventional desalination using reverse osmosis does not work well in many cases. “And thermal treatment applications are very expensive,” Crain explains.
TPWR is a subsidiary of Texas Pacific Land Trust Corp., which traces its legacy to the eponymous railroad founded in 1871. “TPL started the water subsidiary in 2017,” Crain recalls. “The focus is on post-frac flowback and produced water. We do not own nor operate any disposal wells; we have a variety of contractual structures with water midstream companies for transportation.”
The Permian Basin Water in Energy Conference is a program of The University of Texas Permian Basin, and will be held March 4-6 in Midland. “The conference touches on the technical but focuses on the functional. Beneficial reuse is the future of produced water. We have a whole panel on that,” Crain says. The program also focuses on developments on the regulatory, legislative and operational fronts.
Thirty years ago, when a considerable percentage of total U.S. oil production came from mature onshore vertical wells, the president of one independent operating company liked to quip, “We are a water company that moonlights in the oil business.” It was a memorable line, but as tight oil plays mature, it reminds that increasing water cuts are no joke to bottom-line profitability.
“Water management is only going to become more and more critical in the Permian Basin as the industry reimagines its product as both oil and water,” Crain suggests.
Sustainable Solution
Five Point Energy manages more than 4 MMbbl/d of produced water through its two portfolio operating companies, WaterBridge in the Delaware Basin (3 MMbbl/d), and Deep Blue, a joint venture with Diamondback in the Midland Basin (1 MMbbl/d).
“In terms of beneficial reuse, recycling and reuse are very important pieces to the puzzle,” says David Capobianco, chief executive officer and managing partner at Five Point. “Diamondback has indicated it seeks to use 65% recycled water and Devon Energy has said it targets 50% recycled water for fracturing operations. Other operators have set goals as well to reduce freshwater usage. But current water production from producing wells significantly outpaces fracturing needs. That is why beneficial reuse is so important, including enhanced evaporation and desalination methods.”
Capobianco is frank about the cost factors in water management, especially beneficial reuse. “What does ‘sustainable’ really mean? How much should sustainability take away from producers’ profit margins? Are the outcomes of beneficial reuse worth the input expense? Are approaches actually cost-competitive to implement in real-world field operations?”
Reinjecting produced water in disposal wells costs about $0.75/barrel on average across the Permian. “We believe we have an enhanced evaporation technology that is competitive with that at perhaps a $0.05-$0.10 premium,” Capobianco reveals. “And for that, there is the benefit of adding water to the environment. Evaporation has not reached its moment in the sun, so people do not yet realize its potential.”
Five Point is building what Capobianco calls “super pilot plants” for desalination at scale. Pilot scale is 15,000-20,000 bbl/d, while a super pilot is 60,000-100,000 bbl/d. “For costs, we are looking at $1.50-$1.75/bbl,” he reports. “Those are good numbers. If we can average that cost level, desalination is going to be adopted rapidly. A good target for us would be handling 20%-30% of our total volumes with a combination of desalination and evaporation, more if possible.”
In developing the technology with an eye on cost, there is great interest in potential commercial minerals that can be extracted from the concentrated byproduct of desalination. “Our focus is on the lithium and ammonia that can be mined from the concentrate,” Capobianco notes. “No one has done much of that, so we do not really know the ideal density, process or logistics. But mineral extraction will continually advance.”
Broadly, Capobianco agrees that gathering, storage and distribution infrastructure is important. “But even more important is maintaining a network of producers so that we can manage enough water to serve the end use. It would be great to use water in contiguous acreage, but that is not often an option. Reality is drilling in one area and then producing for many years. That is why the network is so important.”
Maximizing The Resource
Martin Water Midstream is the fourth business that Steve Johnson has helped start, but rather than name the company after the founders, it was named after the Texas county in which the company operates.
“We chose a Martin County focus because it is the second most active county for drilling and completion permits in the United States,” explains Johnson, the company’s co-chief executive officer and chief sustainability officer. “The Midland Basin is much more mature than the Delaware, and the land ownership is more fragmented. Many producers are on one to three or maybe five sections, not the giant leases like in the Delaware.”
That affects the size and volume of frac campaigns and whether recycled produced water is reused by the same producer or becomes a shared resource with other operators.
While traditional midstream operators and energy service providers figure large in water management, Johnson notes a fundamental difference from hydrocarbon midstream operations. “The crude oil and gas pass through the midstream infrastructure but then exit to the downstream. Raw produced and recycled water comes back, so it is a velocity play,” he states. “When you reuse the same barrel over and over, the question becomes how fast you can handle it.”
Relatively smaller leases do not mean smaller players. “We have most of the big public companies all around us,” Johnson says. “That includes Diamondback, Oxy, ExxonMobil and Chevron, as well as several of the large privately held producers.”
Martin routinely lays parallel twin pipe systems. “One is for raw produced water, and the other is for cleaned, recycled water. The pipe has risers, essentially hydrants, spaced periodically. From those, the operator can use lay-flat pipe to run from our large-diameter lines to the completion pad or job site,” Johnson describes. “We are not a traditional services company and we are not into water transfer for the last mile. We are a traditional midstream company in the water management and transportation business.”
The last mile is very labor intensive, Johnson explains. “We take raw produced water and provide recycled water for reuse, and the cash register rings for us each time a barrel goes in or out of our system.”
Martin also operates four disposal wells for volume management. “We don’t like it, but we have to have them,” he says. “If the ponds get full, we cannot tell an operator not to flow water to us.”
The balance challenge for water midstream is exacerbated by the burgeoning size of fracs. “There has been an evolution in water demand,” Johnson observes. “It used to be 75,000-100,000 bbl/d for a frac. Today, with longer laterals, zippers, and trimul-fracs, that can reach 250,000 bbl/d. It is hard for anyone to marshal that much water at one time. Operators are fracturing two and three wells on the same pad at a time with double or triple the number of stages in 24 hours, a huge increase in efficiency.”
At the same time, Martin is also exploring beneficial reuse in many manifestations. That includes pilot development for evaporation, carbon capture and sequestration, reuse of solids, and even power generation using the kinetic force and temperature of produced water.
“We view the water as a resource,” Johnson states. “But how can we use all of it: the water, the solids, the pressure, and the temperature? If you are having to step down the pressure, that is a waste of energy. Most of the focus is on what to do with the water itself, but when you do the arithmetic on the solids, how many tons are going to landfills to never be used again?”
Water Banking
Chad Lavender, vice president of water at Mustang Extreme Environmental Services, says satisfying the water demand for fracturing in the Permian comes down to a few simple questions. “What water is available and in what volumes, what is in it, and what is it going to be used for? We do not try to find a magic box because there is a huge difference in each shale play, and even from well to well,” he comments.
Given the demand level associated with “hyperfrac” designs that pump hundreds of thousands of barrels a day, Lavender says water banking is the map of the future. “Ideally, it would be like the power grid. You flip a switch and you get instant power. If there is a pipeline grid all over the basin, you could flip a switch and get water on demand,” he explains.
Lavender acknowledges that the last mile of connection can be a challenge but notes that there is pipe installed all over the Permian. “All I can say for sure is that there is much more water pipe capacity today than there was last year, and next year there will be even more,” he states.
The company is the largest installer of geosynthetic liners for pits, ponds and impoundments. It also designs, builds and operates storage facilities. “The assets and operations are specific to each producer,” Lavender explains. “We can build it and they can staff it, or we can operate their facilities. Or we can just treat the water.”
Mustang focuses on remote sensing to monitor water volumes and qualities, not only at production, but also over time. “Water quality degrades over time in open storage pits,” Lavender points out. “Every time the wind blows, you get more contamination, and over time, bacteria and other organics can grow. It is important to have data points to understand the current quality of the water. That has an effect on frac chemistries. You need good data on the left side of the equation.”
The custody of the water, as well as payment transactions, also varies. “There is not much anyone can do about the water that comes up,” Lavender says. “You can put some biocides and scale inhibitors into the frac water, but even those have limited effect on the flowback. Then everyone has variations of what they need or what they can treat before using produced water for the next frac because operational conditions change so much.”
He adds that hydrogen sulfide, iron and high salinity in particular can be difficult to manage in produced water.
“Our objective is to recycle as much water as possible,” Lavender remarks. “We would rather have you use one barrel 100 times than 100 barrels once.”
For other great articles about exploration, drilling, completions and production, subscribe to The American Oil & Gas Reporter and bookmark www.aogr.com.