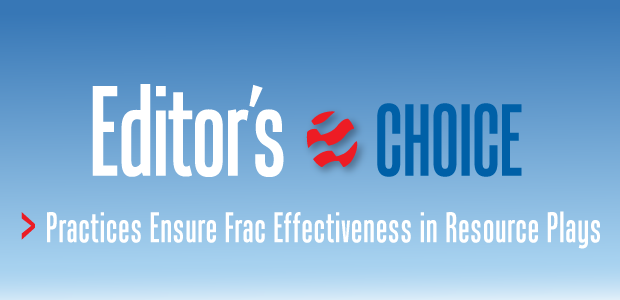
Emerging Best Practices Ensure Fracture Effectiveness Over Time In Resource Plays
By Mike C. Vincent and Monte R. Besler
DENVER–The objective in creating hydraulic fractures is to provide durable, highly conductive flow paths that remain effective throughout the created extent over decades of production. However, a growing body of evidence demonstrates that a number of mechanisms can cause fractures to lose effectiveness over time.
A study of fracture effectiveness in onshore resource plays has identified a number of examples that demonstrate convincingly that fractures have lost propped conductivity, surface area and hydraulic continuity over time. These field examples range from wells interconnected during a frac treatment that have no sustained interference during production, to production that is highly sensitive to lateral depth (indicating that fractures fail to drain reserves from the entire pay section) and adjacent wells improved by offset well “bashing” (permanent stimulation when an offset well is fracture stimulated).
The results indicate that greater focus should be placed on fracture effectiveness, rather than initial fracture length or extent. The field results are encouraging, and suggest that improved practices are emerging in all resource plays that can improve frac effectiveness and durability.
Productivity Mechanisms
A number of mechanisms can cause fractures to become ineffective and lose conductivity. Operators are working to address some of these concerns, but there are a number of design and operational factors to consider. For example, lateral landing depth can influence well productivity significantly in the Bakken/Three Forks, Barnett, Niobrara, Woodford, Montney, Eagle Ford, and other resource plays.
Managing drawdown also seems to improve ultimate recoveries in some reservoirs, suggesting that typical operational practices may be accelerating fracture degradation. While this degradation possibly could be attributed to stress-dependent permeability of the reservoir, it likely suggests that traditional frac treatments are insufficiently durable to withstand common drawdown or standard operating practices (shut-ins, cyclic stress loading, etc.). In fact, data suggest that aggressive drawdown can cause premature damage to the completion in some plays, resulting in lost reserves. In other reservoirs, aggressive drawdown can be safely conducted only when using sufficiently strong proppant at adequate concentrations.
Tremendous degradation of conductivity over time has been documented even under ideal laboratory testing conditions. While some proppants are more durable than others, all proppant packs experience continued crush and compaction over time, causing fractures to lose conductivity. Fracture complexity also challenges the goal to place a sufficiently durable frac. Hydraulic fractures are not simple, wide planar features, and stress on proppant is magnified greatly in irregularly propped fractures, or in horizontal fracture “stair steps” in which proppant must support the entire overburden.
Another challenge when designing hydraulic fracturing treatments is to ensure a sufficient stimulated volume without detrimentally interfering with offset wells. There are numerous instances where hydraulic fractures clearly have connected two offset wellbores, including pumping proppant-laden slurry through the entire frac length into adjacent wells completed at exactly the same depth, filling the adjacent wellbore and surface equipment with sand.
However, even in these cases, diagnostic tests frequently indicate ineffective retained hydraulic continuity, and often show no indication of a sustained hydraulic connection. The frac treatments either provide exceedingly low conductivity on initial placement, or the continuity collapses at some point between the wellbores. There are a number of encouraging examples that display some modest level of sustained hydraulic continuity, but even in these cases, large pressure losses are apparent in the fracture network, suggesting opportunities to improve fracture design and implementation.
There are also cases where stacked laterals demonstrate the ability to initially create a fracture connecting wellbores completed within 100-foot depths, such as the Bakken and Three Forks. However, after being brought into production, these stacked laterals often show little or no sustained continuity, and commonly produce distinctly differing water cuts, indicating that the wells are draining unique reserves. The hydraulic continuity/conductivity within the fractures is evidently compromised during drawdown and production. There is clearly a large pressure loss within whatever fracture network connects the two laterals, unlike what most frac models predict.
In some situations, adjacent wells have been stimulated permanently by fracturing operations on an offset well. While “bashing” can either improve or damage production on adjacent wells, a positive influence of specific well pairs has been observed in the Haynesville, Bakken, Eagle Ford, Niobrara and Barnett. If fractures were infinitely conductive conduits as many envision, a newly drilled offset would consistently steal reserves from nearby wells. However, documentation of positive interference allows us to improve our understanding of frac performance, unambiguously demonstrating that created fractures do not reliably perform as highly conductive conduits between wells in a wide range of rock types and stress conditions.
Decline Curves
Production decline curves are often steeper in resource plays than initially anticipated. These steep declines could be attributed partially to insufficient conductivity, collapse of fracture conductivity over time, or loss of surface area contacted by the treatment. Evidence that fractures are not recovering hydrocarbons as effectively as anticipated includes cases where new infill wells drilled through microseismic “swarms” in resource plays encounter near-virgin reservoir pressures and recover a high percentage of the EURs of parent wells drilled in virgin rock (suggesting that parent wells do not thoroughly deplete the rock volume covered with microseismic events).
Traditional techniques to analyze production declines from individual wells are increasingly ambiguous for horizontal wells with multistage completions, making it impossible to uniquely determine whether a steep decline rate should be attributed to insufficient reservoir quality or deficiencies in the stimulation design. Steep decline curves in ultratight reservoirs have been blamed on a number of mechanisms, ranging from low reservoir permeabilities, to frac stage spacing and proppant/fluid selection issues, to failing to place sufficient proppant concentrations throughout the created network.
Another obvious indictor is the restimulation of horizontal wells. The fact that wells have been restimulated successfully in most resource plays shows that initial frac treatments were insufficient to drain the recoverable reserves.
While no single frac design is optimal for all resource plays, there are a number of controllable design variables that can improve fracture effectiveness to provide superior sustained production in transversely fractured horizontal wells. One example is increasing the number of stages, which clearly increases production in most plays. This is in contrast to what is predicted with production models, which incorrectly forecast that placing more, but smaller stages (reduced frac lengths) will reduce long-term productivity.
The relationship between high stage counts and productivity strongly suggests that at least one of the following is true:
- Pressure losses are high within transverse fracs, and dividing the hydrocarbons between multiple entry points is advantageous.
- Fractures lose hydraulic continuity at some location within the fracture, so putting the investment nearer the wellbore increases the proportion that remains productive over time.
- The connection between the wellbore and fracture is tenuous, and increasing the number of connections (fractures) increases the durability.
- Overflushing or flowing back proppant jeopardizes well productivity, and increasing the number of stages somewhat compensates for completion practices.
Some reservoirs appear to be tolerant of overflushing and can be developed economically with standard industry practices that require flushing the wellbore clean between stages, typically resulting in overflushing proppant in the created fractures some distance away from the wellbore. Other formations appear to be damaged by overflushing. Several operators have disclosed efforts to reduce or eliminate overflushing, and some are choosing to screen out specific stages to evaluate the production benefits from improving connections between the wellbore and fractures.
In wells susceptible to proppant flow back, using curable resins near the wellbore has been beneficial in some plays, while uncoated ceramic proppants have eliminated proppant flow back in fields such as the Bakken, which is prone to flowing back less durable frac sand. In general, field results demonstrate that sufficiently strong, larger-diameter proppants are more resistant to proppant flow back than smaller-diameter, weaker sand.
Proppant Placement
There is growing recognition that placing proppants in diffuse concentrations in cross-linked fluids is yielding discontinuous proppant packs after closure. Some operators are switching to low-viscosity banking fluids (slickwater) that build a continuous proppant bank through the mechanism of saltation. The retained fracture width and conductivity is insensitive to proppant concentration in a slickwater duning/banking placement strategy. Stages placed in slickwater also appear to be less damaged by overflushing.
Other operators are trying to improve continuity by specifying high proppant concentrations in cross-linked fluids to place a sufficient volume of proppant grains to improve hydraulic continuity. Additional efforts to reduce or eliminate overflush in gelled treatments have proven effective in some plays. It appears either approach can improve the continuity of created fracs, compared with traditional treatments.
A number of operators also are reporting using detectable proppants to locate proppant near the wellbore and indicate which fracturing stages contact offset wells. Additionally, oil- and water-soluble chemical tracers can indicate which injected fluids reach adjacent wells, and document the relative productivity of stages using tracer recovery as proxies for load recovery and hydrocarbon productivity.
Efforts to integrate the interpretation of these diagnostics with other data such as seismic attributes, microseismic mapping, mud logging, production logs, and distributed temperature and acoustic sensing (DTS/DAS) data from fiber optic monitoring are improving the understanding of which parameters most directly correlate with sustained fracture productivity.
All proppants are not equal. Vast variations in proppant quality and durability have been documented for both white sand and ceramics. Given these quality variations, operators should not accept generic proppant identifiers without careful documentation of their performance. Several operating companies are beginning to specify the exact materials and qualities they will accept, and are keeping careful records so that wells stimulated with lower-quality proppants can be identified for restimulation.
Refracs appear to be required and profitable in most resource plays, again indicating the opportunity to improve the quality and durability of initial stimulation treatments. It would be more cost effective and profitable to improve the initial treatment, if possible, to avoid the need for subsequent restimulation efforts.
Hydraulic Continuity
As noted, there are wells in numerous oil and gas resource plays in which diagnostics have conclusively proven excellent communication of fracturing pressure between two adjacent horizontal wellbores during treatment. In some cases, it is evident that liquid chemical tracers, solid tracers and even full wellbore volumes of frac sand have been conveyed during treatment into adjacent wellbores.
It is irrefutable that a propped fracture connecting two wells has been established in a large number of fields. These unique well pairs provide tremendous opportunities to interrogate the conductivity and durability of fracs. Unfortunately, the news is sobering. The majority of these wells appear to have essentially zero hydraulic continuity six months after frac treatment. It appears that drawdown causes some portions of the fracture to collapse as the wells are produced.
A case in point is the Eagle Ford Shale, where data demonstrated connection during stimulation of three parallel laterals at 500-600 foot spacing. Chemical tracers and solid radioactive proppant were observed in most stages in adjacent horizontal wells. Soon after cleanup and initial flow back, pressure communication testing was performed by bringing the center well onto production while parallel laterals remained shut in with pressure gauges recording the pressure influence. Lag times of 43 and 55 minutes elapsed before any pressure influences were documented in the offset wells. However, when a similar interference test was conducted three months later, the lag times increased to 76 and 81 minutes.
While this may be attributed partly to compressibility changes, it also suggests the “flow path length” between wells had increased, indicating deterioration of the fracture network. It is interesting to note that if the connecting fractures were envisioned to behave as an infinitely conductive pipe, a pressure pulse in one well could be observed at 500 feet with a lag time of less than one second. Furthermore, the pressures would equilibrate through this infinitely conductive pipe, and there would be no difference in the wells’ bottom-hole pressures. Clearly, it is incorrect to envision these fractures as infinitely conductive, open channels.
More sophisticated efforts to evaluate pressure pulse movement through narrow fractures are ongoing, but to date, the data remain a challenge to the industry’s description of hydraulic fractures.
It also is compelling that when testing was repeated three months after initial stimulation, despite production from the central well, the bottom-hole pressure in offset wells continued to increase, showing that the reservoir was capable of supplying hydrocarbons to those wellbores much more rapidly than the hydraulic fractures connecting the wells could deplete the pressure. It is surprising to most in the industry that the ultralow-permeability Eagle Ford rock could supply hydrocarbons to a well more rapidly than it could be drained through a number of interconnected fractures.
Wellbores stacked vertically have shown similar loss of hydraulic connection over time. It has been repeatedly documented that it is possible to inject fracturing fluids through the Lower Bakken Shale, apparently creating fractures connecting stacked laterals landed in the overlying Middle Bakken and underlying Three Forks. The vertical separation of these wellbores is often less than 100 feet.
Frac fluid, chemical tracers, solid radioactive tracers and full wellbores of sand have been recovered from offsets, corroborating pressure monitoring and microseismic data demonstrating that it is possible to initially create fractures connecting Middle Bakken and Three Forks laterals. However, wells frequently appear to operate independently, with little sustained production interference. Many Three Forks wells produce distinctly different water cuts and gas-to-oil ratios than adjacent Middle Bakken completions, illustrating that the wells are draining unique reserves and that the connecting fractures are not infinitely conductive.
At least five Bakken operators have announced plans to evaluate “high density,” “vertical down spacing,” or “array fracturing” to land laterals in multiple horizons, in recognition that fractures are insufficiently capturing resources throughout the section. A conceptual image is shown in Figure 1. Similar efforts are under way in the Niobrara, Woodford, Montney and several Permian Basin plays. That fact that operators are electing to invest considerable capital to vertically down space wells in these formations is evidence that conventionally executed fractures fail to adequately drain vertical sections in many laminated plays.
Frac Conductivity
It is estimated that more than 90 percent of all transverse fractures have been overflushed because it is operationally necessary to sweep the wellbore clean of proppant before dropping balls or pumping plugs to isolate stages. In some plays, there is no evidence that overflushing causes any well productivity problems (in fact, it may actually result in superior production in some formations), but overflushing may not be appropriate in many reservoirs.
Stages initiated in more brittle (highly siliceous) rock often are reported to be more productive than those in more ductile rock. The standard explanation is that more complex fracturing develops in brittle rock. But can an alternative explanation be that this result is an artifact of the way wells are overflushed? Is it possible that more rigid, competent rock better accommodates the unpropped or poorly propped void caused by overflushing? Can treatments be designed to achieve high productivity, even in stages initiated in more ductile rock?
Numerous operators and service companies have reported large percentages of perforation clusters failing to produce measurable hydrocarbons. In many cases, tracer logs indicate minimal or no proppant in some perforations. There are numerous explanations for this, but can some of this be attributed to overflushing between stages? Is it possible that overflushing may leave the area of highest drawdown near the wellbore (connecting the wellbore with the fractures) inadequately propped and vulnerable to collapse? Does overflushing proppant partly explain why initial frac treatments fail to capture reserves accessible to the well in so many cases, and why successful restimulation treatments have been performed in nearly all of the resource plays?
Rather than overflushing all stages, we recommend experimenting with completion strategies, including intentionally screening out stages to compare results to overflushed stages. Although far from an optimal experiment, Figure 2 shows production logging results from a 15-stage horizontal well in which three stages achieved screen out (green bars). Those three stages had approximately twice the productivity of overflushed stages at the time the log was run. Coupled with previous wells in this formation, in which intentionally screened out heel stages had higher productivities, these results could compel an operator to focus on the conductivity of the fracture in the near-wellbore area in this particular play.
There is an understandable reluctance to intentionally screen out stages, since it is operationally impractical to perform multiple flow backs or well cleanouts. There are both advantages and disadvantages to intentional screen outs, but in one of the most statistically significant published field trials, screen outs in the Pinedale Anticline using ceramic proppant consistently resulted in superior productivity and superior apparent fracture length, while stages that screened out using lower-strength sand or resin-coated sand had consistently poor productivity. This demonstrates that careful evaluation may be necessary to determine the best strategy in a specific field.
FIGURE 4
Production Performance of Seven Wells Completed Emphasizing Proppant Transport (Blue) And 27 Wells Completed Emphasizing Near-Wellbore Conductivity (Red)
One relatively inexpensive strategy is to test the result of intentionally screening out using strong proppant in the heel-most stage. If production logs indicate improved productivity, steps can be taken to capture part of the benefits of screen-outs while avoiding the cost and delay of multiple flow backs or cleanouts.
Bakken Strategy
In an effort to improve fracture conductivity, a strategy has been implemented in the Bakken/Three Forks to use high-conductivity ceramic proppants to maximize flow capacity throughout the fracture, commonly reaching six pounds of proppant added per gallon of fluid (ppa) in the majority of treatments. At the end of each stage, a high-concentration proppant slug (12-20 ppa) is introduced. Stages are flushed only to the top perforation, with efforts to “call flush” aggressively to underdisplace each stage with the goal of ensuring that high-concentration slurry remains near the perforations and is not overflushed into the fractures.
Aggressive quality control is performed to ensure water quality and cleanliness, fluid rheology, breakers, pH, scale inhibition, and proppant quality to help maximize fracture conductivity and connection between the wellbore and fractures.
This strategy cannot guarantee that a highly concentrated slurry will remain near the wellbore in all perforation clusters, and some damage likely occurs during subsequent work to pump the required plug and perforation gun assembly before treating the next stage. However, this strategy provides an operational compromise that increases the likelihood of retaining a durable, conductive connection in the near-wellbore area while minimizing expensive and time-consuming flow back/cleanout following screen outs.
One Bakken operator completed 34 horizontal wells in close proximity in McKenzie and Dunn counties in North Dakota with two primary strategies, shown as blue and red dots in Figure 3. Both categories of wells utilized ceramic proppant throughout the entire pump schedule, with small amounts of Ottawa sand used in portions of five red wells. The offset wells shown as green dots were completed using less expensive frac sand.
The completion strategy on the blue wells focused on proppant transport to ensure superior fracture lengths using greater fluid volumes, higher gel concentrations and reduced breaker concentrations. These wells had greater spacing between stages to delay production competition between adjacent stages.
The wells in red focused on improving near-wellbore conductivity by placing high-concentration proppant slugs and taking precautions to reduce or eliminate proppant overflushing. The majority of the treatments were plug-and-perf completions in uncemented laterals isolated with swellable elements in the casing/bore hole annulus to compartmentalize frac stages. In the most recent wells, the design specified 24-30 stages per 9,500-foot lateral, draining 1,280-acre spacing units. Over time, these wells had longer lateral lengths and much higher stage counts with more closely spaced swell packers.
Production Results
Figure 4 shows total well production rates without correcting for stage count. The seven blue wells completed to enhance proppant transport underperform the 27 red wells completed to emphasize near-wellbore conductivity. The blue wells typically were treated in five or six stages, while the red wells averaged 28 stages. Adjacent operators have completed 23 wells in the surrounding area with frac sand (green dots). The cumulative production trends are shown in Figure 5. These wells were completed with 20 frac stages, on average.
While it is challenging to compare wells with differing completion strategies and numbers of stages, Figure 6 shows the cumulative production trends after normalizing for stage count, with an inset table showing the average parameters of each category. When normalized for stage count, both ceramic strategies outperformed offset wells completed with frac sand, despite greater proppant mass utilized in the sand stages.
Furthermore, ceramic stages focusing on near-wellbore conductivity appear to have superior sustained production, despite shorter presumed fracture lengths and greater competition from more closely spaced fractures. The incremental oil recovered through this approach provides a significant return on the investment to upgrade fracture conductivity.
In the Middle Bakken and Three Forks formations, efforts to place more durable ceramic proppants in increased concentration in the near-wellbore area appear to result in superior sustained production. It is evident that more durable proppants and attention to the near-wellbore connection generates significant increases in well production and profitability in the study area. There is not yet any production evidence to suggest that closely spaced stages cause competition detrimental to production in this study area. On the contrary, an increased number of initiation points improves the extent of the connections between the wellbore and fractures, which appears to enhance sustained productivity.
While this approach has not addressed all the potential mechanisms that may jeopardize fracture continuity and durability, it is clear that relatively modest design changes can improve the profitability of wells in a large number of resource plays.
Editor’s Note: For more detailed information, the authors recommend reviewing URTeC 1579008, a technical paper that assesses evidence of propped fractures losing effectiveness over time in resource plays. The paper was presented at the Unconventional Resources Technology Conference, held Aug. 12-14 in Denver.
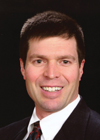
MIKE C. VINCENT is a consulting engineer based in Colorado, specializing in fracture optimization and training. After completing his degree at the Colorado School of Mines, he worked with Amoco, ARCO and CARBO prior to establishing Insight Consulting and becoming an independent consultant in 1996. He has 25 years of experience in optimizing hydraulic fractures, and has analyzed frac treatments in reservoirs around the world. An active member of the Society of Petroleum Engineers, Vincent has authored more than 30 SPE papers and serves as a technical editor for three SPE journals. He presents fracturing schools to numerous companies and universities, and served as an SPE distinguished lecturer in 2009-2010, and as an SPE distinguished author in 2012.
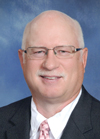
MONTE R. BESLER is a consultant and owner of FRACN8R Consulting LLC, providing primarily completion consulting and supervision services for oil and gas operators. With three decades of experience, he has worked in 20+ distinct producing intervals in the Williston Basin, including the Bakken/Three Forks. Before establishing FRACN8R, Besler was a senior consulting engineer at Hohn Engineering, production engineer at Hess Corporation, district engineer at Halliburton, and district engineer at The Western Company of North America. He has served in various leadership positions with the American Petroleum Institute’s Williston Basin Chapter and the Society of Petroleum Engineers’ Williston Basin section, and is a member of the North Dakota Petroleum Council and technical adviser to the North Dakota Oil & Gas Research Council. Besler has a B.S. in geological engineering from South Dakota School of Mines and Technology.
For other great articles about exploration, drilling, completions and production, subscribe to The American Oil & Gas Reporter and bookmark www.aogr.com.