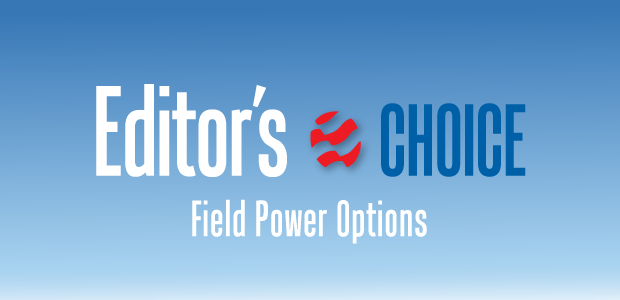
Fracturing Fleets Apply Expertise And Tools To Expand Natural Gas Use
By Colter Cookson
Pumping completion fluids downhole at high volumes and rates requires a significant amount of power. Whether that power comes from old but reliable diesel engines, dual-fuel engines that blend diesel with natural gas, or turbines or reciprocating engines that rely entirely on natural gas, it takes care to keep these prime movers running as efficiently as possible.
That care extends beyond maintenance. How engines are operated can influence how effectively they transform fuel into energy, which impacts completion costs and emissions.
Dual-fuel engines illustrate the benefit of paying attention to detail, says Jason Burger, chief innovation officer for Rolfson Oil. He says natural gas substitution rates often fall short of their potential. “With new Tier IV engines that should be able to run on 60% or 70% natural gas, we still see customers happy with diesel displacement rates around 40% or 45% because they think that is the ceiling in field conditions,” he reports.
Those fleets can often achieve much higher substitution rates, Burger stresses. By bringing more flexible fuel distribution equipment, sharing best practices and working with frac crews during the job to optimize fuel delivery, Burger says Rolfson has helped fleets increase substitution rates from 40% to 70% without any capital investment.
“As dual-fuel engines came on the scene, we started to see opportunities for improvement,” Burger recalls. “Initially, dual-fuel fleets would bring us on site to supply the diesel, a CNG vendor to provide the CNG, and a separate manifold company to distribute the gas to the engines. Most of the manifolds would be daisy chain-style systems where it’s all or nothing. The gas is either on or off, and the pump on the end is not getting as much gas as the pump at the front.”
Such manifolds are a poor fit for frac applications, Burger says. “Even in the best case, they lead to suboptimal diesel displacement because only some of the engines get all the gas they could use,” he says. “If something happens and a pump needs to be pulled off line, a daisy chain-style manifold has to stop sending gas to all the pumps until that pump is replaced.”
To address these shortcomings, Burger says Rolfson has adapted its automated diesel delivery system to handle both diesel and gas. “By doing that, we eliminated the need for a separate manifold vendor,” he says. “We also designed our system with the ability to isolate each gas line so the crews can pull a pump out without turning off gas to the other pumps.”
Tailoring Pressures
Rolfson’s system also allows the fuel delivery pressure to be adjusted for an individual pump, adds Francis Noble, vice president of engineering and compliance at Rolfson Oil. To explain why that matters, he points out that some fleets use a mix of Tier II and Tier IV dual-fuel engines.
“There are different pressures that should be delivered to a Tier II engine and a Tier IV one,” he says. “We base the initial fuel delivery pressures on what the crew requests, but we frequently need to make adjustments throughout the job.”
To help customers get the most out of dual-fuel fleets, Noble says Rolfson trains its equipment operators to communicate with frac teams. “If it looks like a pump’s low substitution rate is the result of the pump not receiving enough gas, our operator might suggest increasing the gas pressure to that pump by 10 psi for the next stage to see if that helps. Frequently, it does.”
Before and during each job, Noble says Rolfson works with the operator and frac crew to identify any issues that could limit substitution rates or create safety concerns. “We had one location where the CNG provider planned to send gas to our distribution system using a three-inch poly line that, after de-rating, only had a pressure rating of around 200 psi. This pressure would then be split across 28 two-inch lines to get the fuel into the pumps,” he relates. “In that scenario, it would have been impossible to deliver fuel to each pump at the target pressure of 125 psi.
“We talked with the crew and brought out a three-inch, braided stainless steel line that had a much higher pressure rating,” Noble continues. “Before working with us, the crew had substitution rates around 45%. On this job, we averaged close to 68%.”
Even with the right fueling equipment, maintaining high substitution rates requires buy-in from the crew, Noble emphasizes. “One of the biggest concerns is horsepower optimization,” he says. “Engines usually achieve the best blending ratios around 60% to 75% of their maximum load.”
When crews focus on keeping the engine load in that range and following other best practices, they can provide customers with significant fuel savings and emissions reductions, Noble reasons. To illustrate, he compares two recent jobs that involved similar equipment and completion designs. “One spread burned almost 1,700 gallons of diesel a stage,” he says. “The other, which had a crew that took optimizing fuel usage more seriously, only needed around 900 gallons per stage.”
Broad Appeal
Given the benefits of maximizing substitution rates, Burger says that most crews do what they can to help. “In many cases, their operator customers have made substitution a key performance indicator that can lead to bonuses,” he says.
To magnify the cost savings associated with burning natural gas rather than diesel, operators will often use conditioned field gas rather than compressed or liquefied natural gas. To support field gas use, Burger says Rolfson developed an upgrade to its dual-fuel distribution system that allows it to blend field gas with CNG. “The goal is to keep the fuel quality high enough that the engines can maximize diesel displacement while burning as much field gas as possible,” he outlines.
Noble says a gas’s methane number, which is a measure of its resistance to autoignition, or knock, is the key metric for determining its quality as a fuel. “Typically, CNG has a methane number around 77,” Noble says. “Conditioned field gas varies depending on the basin, site and conditioning method, but it is usually around 64. The higher the methane number, the better the substitution rate, so we target a midpoint between 70 and 77.”
While field gas is almost always the most affordable fuel available, it needs to be treated before it is sent to the engine. “There are two main methods for conditioning field gas on location: mechanical refrigeration units and membrane systems,” Noble describes. “With the necessary infrastructure in place, membrane systems will generally outperform MRUs, but they are less common because many frac sites lack that infrastructure.”
Membranes work by using a pressure differential to separate high-quality gas from low-quality gas. For the membranes to be deployed, the site needs a low-pressure line that can return the rejected low-quality gas stream to a tank battery or carry it to market, Noble elaborates. “As a result, we typically see membrane systems on sites operated by large companies that are developing fields with existing infrastructure,” he explains. “For most sites, MRUs are a more practical choice.”
Regardless of the conditioning method, Noble says it’s vital to watch for changes in the quality of conditioned field gas during a completion. “We take daily gas samples and get them tested at a local lab,” he says. “Between those tests, we can still often spot quality declines by monitoring operating conditions and the volume of gas consumed for each stage. If usage drops 30% from one stage to the next and there’s been no major operational changes downstream of our blending unit, that can indicate a change in gas composition and tell us we need to blend more CNG to compensate.”
Burger mentions that some gas providers now use gas spectrometers to analyze gas composition in seconds. Although these systems are expensive and need to be recalibrated ahead of every job, he predicts they will become more common. “As we educate companies and they see how much paying attention to details helps them reach high substitution rates, they are investing more resources in managing fuel,” he explains.
Electric Vision
For many companies, Burger says the quest to minimize fuel costs and emissions will lead to electric equipment. “Rolfson already uses natural gas to provide electricity for equipment that once ran off our diesel,” he divulges.
In a frac fleet application, the necessary scale can present a challenge, Burger says. “When it’s humming, an electric fleet can require as much as 35 megawatts of power, which is what some large cities use,” he comments.
It’s possible to supply that power with turbines or with generators powered by reciprocating natural gas engines, but Burger cautions that traditional designs for both types of equipment struggle with rapid load increases that occur as pumps ramp up, down and up again. It can help to idle equipment so it’s ready when the load jumps, but he says that increases fuel consumption significantly.
Fortunately, he reflects, the oil and gas industry is not the only sector that seeks responsive and efficient power generators rugged enough to endure travel down bumpy terrain. “We have some products coming to market based on small, five-megawatt turbines that have performed well in military applications,” Burger says. “There is one fleet already using them with good results. They have proven to be more resilient to changing load demands, and they can burn lower-quality field gas that would be difficult to condition in the field.”
The Case for Natural Gas
The fuel savings from running entirely on natural gas can be tremendous, says Madison Hollaway, low emissions and sustainability lead for Liberty Energy. “Diesel and natural gas prices fluctuate, but if a customer goes from pumping 100% diesel to 100% natural gas on a dedicated spread that works throughout the year, they can generally expect to save upwards of $10 million when using CNG as the natural gas source,” she estimates.
The savings grow when field gas is available and remain significant even for companies that are transitioning from dual-fuel to natural gas, Hollaway says. Assuming diesel costs $2.50 a gallon and natural gas capable of producing an equivalent amount of energy costs $1.50, a natural gas fleet that uses reciprocating engines to generate power for electric pumps would cut fuel costs by 29%.
The price disparity between diesel and natural gas accounts for most of those savings, but natural gas engines also convert fuel to energy more efficiently than their diesel counterparts, Hollaway says.
In general, frac fleets use 100% natural gas engines in two ways. In the first approach, engines generate electricity that is shared with several electric pumps. The second approach, called direct drive, involves connecting engines to individual pumps using traditional frac transmissions.
Direct-drive fleets are more efficient because they minimize the number of energy conversions, Hollaway explains. On an electric fleet, the engines combust fuel to transform chemical energy into mechanical energy, which generators turn into electric energy. When this electric energy reaches a pump’s power end, it is converted back into mechanical energy and sent to the fluid end, which translates the mechanical energy into hydraulic energy. That is four conversions.
On a direct drive fleet, Hollaway contrasts, there are only two conversions. The engine still needs to combust fuel to create mechanical energy, and the pump still needs to turn mechanical energy into its hydraulic counterpart. However, the mechanical energy that the engine produces goes to the pump immediately, skipping any conversion to electricity.
Using the same fuel cost assumptions mentioned earlier, Hollaway says moving from electric to direct-drive fleets reduces the cost per hydraulic kilowatt hour from $0.12 to $0.10. For comparison, a Tier II diesel fleet would need $0.24 per kilowatt hour, or twice as much as either natural gas approach. Dual-fuel fleets do better at $0.17, but direct-drive ones still cut fuel costs by 40%.
These numbers come from “Evaluating the Transition to Natural Gas-Powered Equipment in Hydraulic Fracturing: Challenges, Benefits and Feasibility Analysis,” a paper that Hollaway and Liberty Energy’s Roy Aune presented at the SPE Hydraulic Fracturing Technology Conference, which was held Feb. 4-6 in The Woodlands, Tx.
The paper, which drew on data collected during Permian Basin field trials, also compares emissions from electric and direct drive fleets with those from diesel and dual-fuel fleets. Both natural gas-powered fleet types demonstrated lower greenhouse gas and nitrous oxide emissions. Overall, Liberty found that electric fleets have about 19% lower emissions than Tier IV dual-fuel fleets. For direct drive spreads, the reduction jumps to 28%.
“Our main goal with the paper and the other information we have put out is to make sure the industry has publicly available data that matches the results we see in the field rather than idealized scenarios,” she says. “It’s important to show the verified benefits of natural gas-powered fleets, because the more that story gets out, the more we will see a drive to build natural gas infrastructure.”
Infrastructure’s Importance
Running on natural gas alone requires confidence in its availability, Hollaway suggests. With diesel, whether enough can get to site is rarely a concern. “Frac has used diesel for 70-plus years now, so the supply chain is robust and well-known,” she says. “When we transitioned to dual-fuel engines, we began using natural gas, but losing it wasn’t critical because we could simply switch to diesel.”
But if an electric or direct-drive fleet stops receiving natural gas in the necessary volumes or qualities, the job halts. “Before we deploy a natural gas spread, we run a model to predict how much gas it will need and what quality that gas needs to be,” Hollaway says. “The amount varies heavily based on job design parameters, such as how many hours the pumps will be active and the pressures and rates they need to be at.
“Once we have the amount locked down, we work with our customers or Liberty Power Innovations, our dispatchable power and natural gas fuel services subsidiary, to make sure we will have enough,” Hollaway continues. “If the answer is a confident yes, we can use a direct drive fleet to maximize fuel savings and emissions reductions. If there is some uncertainty, we will ask if the site has access to a power grid. If so, and if that grid can deliver enough power to flush the well if the gas supply falters, we may recommend an electric fleet. But if we think the gas supply will be interrupted, we will fall back on a dual-fuel fleet.”
Hollaway says access to gas is expanding. “It will take time for natural gas infrastructure to catch up to diesel, but it is going to do that relatively quickly because the benefits of burning natural gas are big enough that people are pushing for it,” she assesses.
Reliable Delivery
Today, Liberty Power Innovations has robust infrastructure for delivering natural gas in the Permian and the Denver-Julesburg basins, says Richard Bradsby, the company’s president. “We entered the DJ last year in response to customer demand,” he relates. “The producers we work with wanted us to help minimize the risk of disruptions to pump time as they began to use more natural gas-powered equipment.”
Reliable gas delivery starts with compression, Bradsby says, noting that the company works for Liberty Energy’s frac customers and other firms. “At the gas source, we invest in redundant compression or contract with another party to supplement our capacity. That way, we can keep gas moving when compressors require maintenance,” he assures.
To transport most of the gas to site, LPI employs internal drivers, Bradsby continues. “The logistics team optimizes dispatching and routing with a platform that Liberty originally developed to handle sand logistics,” he says. “It is a great backbone that helps our team use resources efficiently and manage risk.”
To control loading and unloading, the company has equipped its CNG trailers with sensors and telemetry for monitoring temperatures. “When gas is compressed during loading, it heats up. As it decompresses during unloading, it cools,” Bradsby observes. “The gas storage cylinders can only tolerate so much heat or cold, so we cannot fill or empty an individual trailer too quickly.”
As a result, achieving the rates necessary for higher-volume applications requires multiple trailers to connect and transfer fuel simultaneously. “There is only so much space on the pad, and we want to use the trailers efficiently, so we do some math to figure out how quickly each trailer can unload without getting too cold,” he says. “The telemetry will allow us to manage the process from a central location.”
To make sure gas arrives, Bradsby says fuel companies need to track driver hours to stay in compliance with Department of Transportation limits. They also need to account for flat tires, storms and maintenance issues, as well as health or family situations that could render drivers unavailable. “We have the experience to estimate how often these situations occur and keep our staffing levels a skosh above our theoretical limit so we can adapt to unanticipated changes,” he assures. “If necessary, we occasionally call in strategic third parties to supplement our drivers.”
Unlocking Field Gas
While pure natural gas engines have many advantages, they tend to be less tolerant of field gas than dual-fuel engines, Bradsby shares. “With newer nonroad-mobile permitted engines, it can be difficult to stay in compliance with emissions limits if the heating value of the gas is volatile or too high,” he clarifies. “For now, field gas is mainly concentrated around dual-fuel applications and a little less common, at least in oil basins, in natural gas direct-drive pumps or natural gas power generators.”
Natural gas liquids transportation physics limit how well field gas conditioning equipment can compensate for rich gas, Bradsby says. “A portable processing plant can cool the gas to condense and remove the liquids, but some of those liquids have a high vapor pressure. If a site has a pipeline to return the liquids to, that pressure is not a concern. However, if the liquids will need to be hauled away by a liquefied petroleum gas or propane trailer, the conditioning equipment often needs to leave ethane in the field gas because those trailers can only take so much pressure.”
Bradsby mentions that Liberty Energy has partnered with Cummins to adapt a variable speed, large displacement natural gas engine as a power source for direct-drive pumps. He says the collaboration, along with other strategic partnerships, will continue to drive innovations in natural gas reciprocating technology that will boost the frequency at which field gas can be used.
Liberty’s work with Cummins is enhancing the versatility of directly driven natural gas pumps by allowing for variable speeds. “The original version of the engine was designed for fixed-speed operations, which has historically limited how we can reach full rate on the frac. With the newly announced variable speed capabilities, this engine stands out as the most fuel-efficient way to deliver horsepower while maintaining some operational flexibility,” he comments.
Electric pumps complement the historically constant speed direct drive system’s strengths with their own, Bradsby advises. “Electric pumps have an extremely flexible load curve,” he explains. “We are combining electric pumps that provide increased flexibility with direct drive pumps that stay close to their ideal loads, increasing overall efficiency.”
For other great articles about exploration, drilling, completions and production, subscribe to The American Oil & Gas Reporter and bookmark www.aogr.com.