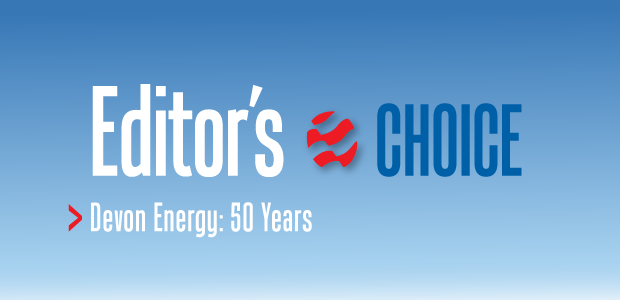
Half Century Of Innovation Underpins Devon’s Legacy, Fuels Its Future
OKLAHOMA CITY–Figuring out how to make shale formations commercially productive took heroic effort from a lot of individuals and organizations over the course of decades. It was not a single giant leap forward by a few, but countless small steps by many that progressed the science of shale gas and tight oil.
Devon Energy Corp. was built in much the same manner: a half century of deals, discoveries, diligence and the occasional lucky break. With full acknowledgement to the many who helped pioneer shale technology, there is no doubt that one of the milestones in the unconventional play timeline occurred in 2002 when Devon Energy–fresh off its acquisition of Mitchell Energy Corp. and its Barnett Shale leasehold–combined the simple horizontal well architectures it had experimented with off shore with the basic slickwater hydraulic fracturing recipe Mitchell Energy had developed for Barnett vertical wells.
Although its first horizontal well, the Blakely Estate No. D2, paled in comparison to modern well designs in terms of lateral length and frac treatment size, it was apparent from the get-go that Devon was onto something big. Applying horizontal drilling to expose large volumes of rock and multistage fracturing to create a complex network of multiple transverse fractures intersecting the lateral would open one shale basin after another on short order, allowing operators to recover the vast liquids and gas reserves locked in low-permeability rock from West Texas to West Virginia.
It was a fine moment for Devon, ranking among its crowning technical achievements. But it was nothing new for a company with a long lineage of innovation across all aspects of its operations: from introducing new financing structures to proving up coalbed methane.
Back in 2002, Trey Lowe was a young completions engineer getting his start right as the shale revolution was starting to roll. He joined Devon in 2006 at about the time it completed a $2.2 billion acquisition to expand its Barnett operation. It was going all-in on shale.
Maintaining An Edge
Today, Lowe serves as vice president of technology. He has a guiding hand in maintaining the technical proficiencies that for so long have given Devon a sharp competitive edge, and views technology from a business-end perspective. “For us, innovation is the means to achieve our business objectives, which include targeted financial and operational metrics, but also environmental, social and governance goals,” Lowe states.
Much as John and Larry Nichols scarcely could have recognized when they founded the company in 1971 what Devon ultimately would become, Lowe concedes that it is next to impossible to envision what the company’s operations may look like in another 50 years. But whatever tomorrow has in store–be it in five quarters or five decades–he says the concerted investment the company has made to implement a data-centric digital platform spanning its entire business will be helping foster technical breakthroughs across its entire portfolio of assets.
“I am excited about how the digital platform creates long-term opportunities for our field operators, engineers and geoscientists to innovate. They are going to come up with new inventions and ideas for operating and designing wells in ways we cannot fathom today,” he remarks. “I know it is coming. I have seen innovations start to happen over the past couple years and they are coming at a faster and faster pace all the time. Our future will be driven by our employees’ discoveries.”
According to Lowe, the next-generation capabilities spinning out of its enterprise-scale digital backbone are likely to evolve around the three core operational domains that have fueled technological advances in resource plays since the days of the Blakely Estate D2: well construction, completion and production. Going forward, he says digital solutions encompassing cloud computing, the Internet of Things, machine learning, artificial intelligence and automation not only will reshape how Devon builds and operates wells, but can lead the company into new frontiers as global energy markets gradually transition toward renewables.
Streaming Real-Time Data
Devon was an early adopter of live data analysis in its drilling and completions operations. In fact, Lowe says, it started streaming real-time, high-frequency data from drilling rigs and frac spreads in 2012.
“That has laid the foundation for where we are today in well construction,” he states. “The breakthrough today is that we are able to join a lot of the sensor data that comes from the well site with subsurface characterization information. That enables us to continually improve at a much faster and more effective pace.”
The results have been transformative during the past five years, propelling Devon to the top of its peer group for well performance and operational execution metrics. “We went from being an underperforming operator in the lower half of our peer group all the way up to the very top,” he reports. “A lot of that was the result of hard work by our engineering staff, but it was also because of the foundation that we laid with our digital platform to collect high-quality data and make it readily accessible in real time.”
In its early iteration, the platform streamed data to a real-time operations center in Devon’s Oklahoma City headquarters. “We have matured beyond that now, to where algorithms perform much of the role of the real-time operations center,” he comments. “We still use an operations center for geosteering operations but drilling and completion engineering are largely automated.”
Algorithms continually analyze real-time data feeds, providing usable information around the clock to help field personnel make sense of what they are seeing and empower them to take decisive action. “I do not think we could have gotten to this point without going through the step of having a real-time operations center. We learned a lot from that,” Lowe remarks. “It is almost like going back to a distributed model. All the data flows into a centralized place, but analysis is decentralized so that engineers and field personnel can make decisions very quickly.”
Lowe emphasizes that Devon is not focused on acquiring novel or unique types of data, but instead on extracting novel and unique insights by integrating all available information in a powerful new way. “We do not have a new prototype sensor,” he assures. “The magic we are experiencing comes from aggregating disparate datasets, such as joining live streamed drilling data with subsurface and geologic data to make well spacing decisions. In the past, that would have been really hard to do.”
Moving The Needle
Through better and more timely data analysis, Devon has been able to move the needle on casing design and sizing, in-zone drilling times, lateral length optimization, etc. Going forward, digital technology increasingly is making it possible to automatically control the mechanical drilling processes themselves using machine learning protocols, according to Lowe.
“There is an opportunity in the near future to do more calculations and control at the edge of the rig site with a computer. Whether managing hook loads, sliding at the right time or rotating at the optimal speed, we will ultimately teach a computer to automatically maintain the correct setpoints,” he reveals. “We are starting to experiment with a trial project using some of those machine learning models and edge computing technologies.”
In its simplest terms, the technology allows Devon to operationalize on all its rigs in all its operating areas the parameters and practices applied on its top-performing wells/rigs using a “best driller” algorithm. The algorithm is trained to automatically optimize drilling operations from spud to total depth. “That will definitely help us tighten up consistency across all our drilling programs, and make step changes from there,” Lowe details, adding that for Devon, rig days is still the primary yardstick for measuring drilling performance.
However, keeping the wellbore in the planned target zone is critical to maximizing completion quality and overall well productivity, Lowe points out. “Geosteering windows will get tighter and we are going to see a much more dynamic geosteering interpretation based on data acquired while drilling,” he states. “Not only will we adjust formations up and down based on what we see as drilling proceeds, but we will also adjust more complex measurements, such as porosity and rock stress, while drilling to make better decisions.
“The industry has become so good at throwing the lateral dart right on the bull’s eye two miles away. It is really amazing,” Lowe goes on. “But if we can improve the real-time interpretation of what the bit is encountering down hole, we will be able to make even more fine-tuned adjustments to landing and steering laterals.”
Changing The Game
Real-time adjustments is also the operative term for completion design, according to Lowe. At present, the industry makes real-time decisions on frac jobs based on operational data, such as pump rates and proppant densities. Devon’s objective is to apply information from offset wells to make those same types of optimization decisions in real time based on the actual geometry of the fracture being created. “No one in the industry is doing that yet, but we are really close,” he enthuses.
The company took a major step toward realizing that objective when it developed a patented low-cost, nonintrusive method to evaluate and quantify fracture growth rates and fracture-driven interactions during stimulation using only a surface pressure gauge on a monitor well (see “Breakthrough Technology uses Pressure Monitoring to Monitor Cluster Efficiency,” by Kyle Haustveit, Wolfgang Deeg, Brendan Elliott and Jackson Haffener, in AOGR’s April 2020 issue).
“We think sealed wellbore pressure monitoring will allow us to use offset well information to make live fracturing decisions that dramatically improve completion quality and cost,” Lowe relates. “The ability to make operational decisions based on a subsurface understanding of the fractures in real time is one of the things we are most excited about. It could be a game changer.”
An early adopter of real-time data analysis in its drilling and completions operations, Devon began streaming high-frequency live data from rigs and frac spreads in 2012. This approach has been instrumental to the company’s rise during the past five years to the top of its peer group for drilling performance and operational execution metrics. One of the next big steps for Devon is automating drilling operations using machine learning and edge computing based on “best driller” practices from top-performing wells.
Here again, machine learning is the enabling technology behind Devon’s ambitious vision of the future completion operation. Most adjustments to fracturing parameters are today made between stages, typically after something has occurred to cause the completion design to be changed before pumping the next stage.
“We are not far from being able to teach a machine to make interpretations on the fly so that we can make decisions during a stage,” he says. “That is the next big leap for us with respect to optimizing fracturing designs, cutting costs and making better wells.”
How would the ability to modify completion design parameters in-stage using subsurface fracture geometries open the possibility of not only changing operational variables such as pump rates and pressures, but also more dynamic factors such as proppant density, fluid viscosity, chemical additive concentrations, and even proppant grain size during a stage treatment?
“All of these things are coming. We will step into it one piece at a time,” Lowe responds. “Down the road, I expect it will become fairly routine for us to use real-time measurements to optimize fracture geometry and fracture lengths by making on-the-fly adjustments to proppant volume and size or fluid viscosity.”
That kind of value-adding capability has obvious and profound bottom-line implications for Devon across its unconventional asset base. “Real-time digital solutions to optimize drilling and fracturing may allow us to increase rates of return by adjusting well spacing to drill fewer wells with larger frac designs, or by placing more wells closer together but with smaller frac sizes. Either way, these are the types of decisions that could ultimately result in hundreds of millions of dollars to Devon’s bottom line. That is the big win. We make investments for that type of return on our capital program.”
And high-frequency data is not confined to only measuring and adjusting what happens when the frac pumps are on; it also is being used to optimize efficiency when the pumps are off. “We have seen a 100%-120% improvement in pump times, going from pumping about 40% of the day five years ago to pumping more than 80% of the day on average.” Lowe reports. “We recently set a record of 22.7 hours of continual pumping operations in a 24-hour period on one of our wells in the Rocky Mountain region.
Layering In Video Data
Even before it entered the Barnett Shale nearly 20 years ago, Devon systematically applied technology to its producing assets to maximize run times and improve productivities and efficiencies. But even after decades of investing in automation and remote monitoring systems, Lowe says production is still the operating domain with the biggest upside for digital solutions.
“Honestly, production is where I am most excited about the application of technology. We are seeing huge improvements by continuing to modernize field operations,” he says. “Even with all the automation we have done over the years, we are making huge leaps using technology in the production space. It is flattening the decline curve, lowering lease operating expenses (LOE), and reducing our environmental footprint.”
Devon was an early adopter of remote surveillance of its well sites and tank batteries using high-definition video and infrared imaging cameras. It has now adopted remote surveillance as a standard operating practice throughout its operating areas and integrated video imagery with a machine learning algorithm and automated controls to monitor production operations and emissions on a 24/7 basis.
“Video data is layered into all the automation and sensor data that streams in from the well site,” he explains. “it is not just imagery; it is a rich new dataset that is organized and integrated with other types of data for analysis.”
The surveillance initiative began in the Powder River Basin, where well sites are remote and isolated enough to justify the ability to have a real-time camera view of every location. “Since then, we started using AI to teach a computer to watch and analyze the imagery,” Lowe continues. “The computer always knows that state of the flare on a site, for example, and constantly looks for any type of anomaly on location and alerts a foreman when an action is needed.”
The company is deploying both infrared imaging and high-resolution RGB video cameras with pan, tilt and zoom functions. Although the cameras are “pretty high-end,” Lowe says the cost of the technology has come down so much that Devon can apply video and infrared cameras at scale and still achieve significant LOE, operational, and environmental benefits.
“This is a cutting-edge approach,” he emphasizes. “We do not know of any commercial models nor any another companies doing anything like this on the scope we are today.”
Devon has been a pioneer in using high-definition video and infrared imaging cameras as a standard operating practice for remote surveillance of well pads, tank batteries and other sites. Integrating video imagery with a machine learning algorithm and automated controls is allowing it to optimize the management of production operations and emissions on a 24/7 basis, driving significant LOE, operational and environmental benefits.
High-resolution video is obviously a very different type of data source than what oil and gas companies are accustomed to dealing with. How can video be monitored, analyzed and integrated with the other types of data collected on a producing well?
“This is one of the benefits of cloud computing, IoT and AI,” Lowe responds. “These technologies have opened this space up. IoT creates the opportunity to convert rich video into data. Once the state of equipment has been converted from a video image to a data point, it can be rolled into the datasets along with SCADA and other sensor data. It basically looks and feels very similar, and it can be streamed in the same way.”
Around-the-clock video surveillance allows well operators to visually visit sites at any time they need to check the status of a well or piece of equipment without having to physically travel to location.
“Instead of making a three-hour drive, the operator can bring up the camera and with the level of zoom available, can check out everything from very small nuts and bolts on a pump all the way up to the big picture of what is happening on a well site. We have seen a tremendous reduction in the amount of miles driven across our operations,” Lowe comments. “Reducing traffic is obviously an ESG benefit, but fewer highway miles also means increased safety for our people.”
Driving Positive Change
Lowe suggests that the enterprise-level digital solutions Devon now has in place will continue to generate economic, operational, ESG and safety dividends for decades to come. Looking at how far Devon has come with digital technology during the past decade, he says it is nearly impossible to fathom the kinds of capabilities it may unleash in another 10 years’ time.
“I think sensors will be on almost everything, with data streamed into a cloud environment, where it will all be accessible in real time so people can create and learn from it. I also see an open environment between Devon and vendors, where we share data in new ways. But I cannot begin to predict what innovations will come out of the digital platform,” he says. “The only thing I know for sure is that we will have a lot of smart people figuring out new ways to use information to drive innovation and positive change across all areas of our business.”
What its business may look like a decade down the road is anyone’s guess. Ten years–let alone 50–is a long time in a volatile industry where change is practically the only constant. However, Lowe ventures to guess that an energy transition of some sort will begin to take root during the next decade.
“I do not know where exactly Devon will be 10 years from now, but I am excited about the potential to play a role in energy markets adjacent to oil and gas. The skills and tools Devon has developed in advancing digital solutions are applicable to geothermal, carbon capture, solar and other areas. Our digital experience, and the corporate culture we have built to innovate based on data, will serve us well no matter what the future holds.”
For other great articles about exploration, drilling, completions and production, subscribe to The American Oil & Gas Reporter and bookmark www.aogr.com.