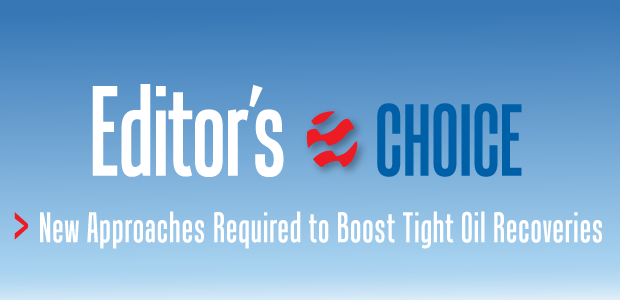
Maximizing Recovery Factors
Improving Recovery Factors In Liquids-Rich Resource Plays Requires New Approaches
By George E. King
HOUSTON–Even with the unprecedented and ongoing success of plays such as the Bakken, Eagle Ford, Marcellus and Wolfcamp, the industry has only scratched the surface of the tremendous potential of liquids-rich unconventional formations. Production from tight oil and liquids-rich gas shales may double or even triple with purpose-engineered methods aimed squarely at the local geological characteristics and properties of the formation fluids.
But therein is the industry’s challenge. Using standard drilling and completion approaches, recovery factors in unconventional liquids-rich formations tend to be measured in the single digits, or only a fraction of typical recovery rates during the primary production phase in conventional reservoirs.
Related to these low recovery rates, both gas and liquids-rich shale production declines rapidly in shale formations, with production often declining by half or more of initial production rate within the first six to 12 months. The rapid declines are caused by flush production from the natural fractures, and slow recharge from the microfissures and the few larger pores in the matrix. Success of refracturing on wells that have suffered sharp production declines indicates that advances in the initial fracture stimulation are required.
Figuring out how recoveries can be improved to flatten decline curves and add incremental production over the life cycles of horizontal wells in ultralow-permeability reservoirs is a complex and multifaceted issue, but the potential reward is substantial. Improving well performance to increase per-well recovery rates by only a few percentage points would have enormous positive implications on development economics, and may not be that difficult if the mechanics of fluid flow and the stability of propped and unpropped fractures within these shales are better understood.
Initial Step
The initial step toward accomplishing this objective is acknowledging that resource plays must be treated unconventionally. That may seem obvious, but many operators continue to use methods designed for permeable matrix flow that shales simply do not support. Highly variable production results from one well to the next are typical in resource play developments, and that variability offers proof that many conventional methods, from completion design to fracturing application, are not effective in unconventional reservoirs.
The best acreage usually represents a relatively small area of a total play. Even within the core area of the Barnett Shale, there are localized areas with very highly productive wells and others areas with very poor wells. In the Eagle Ford Shale, the highest production rates were concentrated initially within one long, relatively narrow area in the wet gas window.
Even with the recognition that gas and gas condensates will flow easier than oils, there are other clues that suggest what specific actions are needed for different parts of the shales. Understanding subtle geologic variations and how they impact completion design considerations is critical to optimizing the performance of individual wells and the overall recovery factor across a development area.
Most critically, what is being produced at the surface is not always representative of what is in the reservoir itself. Unlike conventional reservoirs that produce near-consistent flow composition, unconventional formations seem to produce lots of gas and light liquids. The production streams contain ethane, butane and propane, but often not a lot of the heavier oils. Liquid-rich flow from shales is usually leaner than conventional reservoirs with the same in situ components.
The problem is that when the gas and gas condensate liquids are drained, both the drive energy and the solvents that could otherwise be used to produce the heavier oils are removed.
Options with current technology are limited. Operators can apply more brute force by increasing the number of fracture stages, or better use of brute force through optimized placement of fracture stages and clusters within each stage. These incremental changes will yield only incremental improvements. For a step change in production and field economics, new techniques are needed to preserve flow capacity of fractures and mobilize the oil.
The industry needs to start thinking about how fluid flows in unconventional formations and develop unconventional technologies for these unconventional reservoirs. That means thinking in terms of unconventional methods, and employing advanced petrophysics and chemical methods that are suited to modifying the flowing surfaces of the reservoir and the actual character of the connate fluids.
This could open liquids production in liquids-rich reservoirs that are not yet economically productive. They could even offer new life to abandoned unconventional and even conventional wells that still hold residual oil.
Using More Science
Historically, about a third of all shale wells drilled in the United States have not been economic (including the majority of early trial-and-error shale wells), and another one-third are economic only at moderately high gas prices. However, the wells in the top one-third perform so well and have such favorable economics that they may be able to carry the rest of the wells in a development project. Operators must use more science to predict better drilling locations and improve production in all areas.
Even with all the mechanical advances made in developing shale, including longer laterals, increased frac densities, stronger proppant and cleaner breaking fluids, the industry is still recovering only an estimated 5-8 percent of the hydrocarbons in place in liquid-rich shales.
In contrast, conventional reservoirs yield 15-30+ percent in primary production, and as much as another 30 percent in secondary and tertiary enhanced recovery operations.
Enhanced oil recovery has not been widely considered in unconventional plays, but with the well and frac density in unconventional plays, the ability to use EOR methods that incorporate repressuring, fluid density decreases, flowing surface modification and flow path enlargement cannot be economically ignored.
Clearly, more needs to be done to understand where the oil and gas are, how they flow, where they are stored, and how they are stored. To accomplish that, we need the rock and logs, and then time for scientists to analyze the data and determine the optimal approaches. Every shale play is unique, and every well within a play is different. Before any operator locks in a standardized design, he must do the basic scientific work to find out what approach is optimal. Economics are critical, but shales are not all alike.
Gas and liquids flow through natural fractures and fissures in shales. The pores within shales are simply too small to be much benefit during the short time that a shale well is in economic operation. The matrix does not yield much out of the interstitial space. Instead, flow must come from areas that are accessed by linking natural fractures and microfissures with the hydraulic fractures propagated during stimulation treatment.
In liquids production there is much higher viscosity, much more resistance to flowing in small cracks and natural fractures, and a lot of capillary resistance to that flow. Wetting, adsorption and emulsions also impact flow in low-permeability reservoirs.
So instead of losing, say, 100 psi in drawdown pressure through the fracture system in a gas producing shale, liquids-rich flow in a tight oil reservoir may require overcoming several thousand psi of capillary blocking pressure with drawdown pressure before liquids will move. If the pressure is too low from initial production losses, then injecting cheap natural gas and/or waste carbon dioxide into an offset well may provide both the liquids viscosity reduction and the drive pressure to produce much more liquid than would initially flow without help.
Flush production from natural fractures accelerates the decline and pressure loss problems, because it tends to allow fast gas production that is perhaps not an efficient use of this initial gas to displace and drive liquids. Because of the low matrix permeability, fractures are not recharged at the rate required to offset the fracture closure pressures.
Once the hydraulic pressure is removed from fracture stimulation, and the gas and light-end fluids start flowing out, the natural fractures begin to close. Flow paths can close or become plugged, and the propped hydraulic fractures can (and do) experience embedment of the proppant and plugging by formation fines.
To sustain production and increase total recovery, liquids-rich shales must have a large contact area that remains open. Better production requires that we preserve or replace the driving force to move the liquids. To increase recovery even further, we need to identify mechanisms to reduce liquid viscosity and stabilize the flow paths. Pressure drop management is still a key to continued production.
Intersecting Fractures
Keys to fracturing success include intersecting, opening and stabilizing natural fracture and microfissure systems. There is simply no way to access the hydrocarbons locked in the shale matrix unless there is a system of stable natural fractures and fissures connected to the wellbore.
FIGURE 1
Outcrop Showing Multiple Potential Natural Fracture Sets
Source: Gary Lash, State University of New York
High natural fracture occurrence and flowable liquids are the first indicators of a sweet spot. Well paths, and fracture and cluster points must be selected to optimize contact with these sweet spots. In low-permeability shale formations, gas flows preferentially through natural fractures that are or can be opened. Complex or network fracture stimulation focuses on contacting, widening and propping natural fractures to create a high-density natural fracture network than maximizes formation contact, in contrast to the long and narrow biwing planar fractures created with conventional fracturing.
Many shales have one or more natural fracture sets, often at 60-90 degree intersections (Figure 1). Where the difference between minimum and maximum horizontal stresses are within about 5 percent, each of these fracture sets can open at various times in the fracture treatment.
This interaction of the natural fracture sets opened creates a contact area that can be several orders of magnitude larger than for conventional planar fractures. The amount of shale volume that is stimulated and can take part in flowing fluids is the stimulated rock volume (SRV).
Methods for accurately describing the SRV are still in flux, but the SRV may be millions of square feet of contact area; and all of it must be formed and stabilized by the fracture treatment. The flow path developed from natural fractures is a torturous, potentially unstable flow path. Therefore, both fracturing and production techniques must be developed to keep these flow paths open.
Complex fracturing uses slickwater (water with a friction reducer), to open natural fractures by a stepwise sequence of injection rate increases. Starting at 5 or 10 barrels a minute, the surface injection rate is raised in 5-10 bbl/minute increments with a few minutes between rate increases for the incompressible frac fluid to leak into the natural fractures before the next pressure step increases the pressure and widens the natural fractures.
Multistage fracture stimulation in a horizontal well can significantly increase total formation contact area and reduce the overall environmental footprint since one horizontal well with multiple fracture stages will reduce the need to drill 10 or more vertical wells. Multiple horizontal wells on small pads further reduce the footprint by reducing the area required for roads, pipelines, facilities, single-well pads and groundwater penetrations..
Quantitative studies are needed on fracture stage placement. My personal opinion is that fracture stages should be placed only where there are strong gas shows, groupings of similar brittleness, or groupings of similar stress patterns, rather than simply placing fracture stages at evenly-spaced increments along the lateral. Natural fractures are not evenly spaced, nor do they all hold gas. There are sections of every shale that have little or no gas. Placing a fracture stage in a high water saturation shale section or a section without natural fractures may not be wise.
A mud log with a gas show analyzer can be used during drilling to locate zones capable of flowing above rates of background gas (or the gas released from the shale as it is drilled). However, spikes of gas may indicate more porosity, more organic content, or higher density of natural fractures.
The key to deciphering the gas log is to examine the gamma ray log readings, porosity logs and the ratio of gases that are recovered. The gamma ray log picks up higher isotope activity, while the density log decreases and the neutron log increases when organic content increases.
However, the gas ratios may be a much better clue. Methane gas flows more easily through low-permeability rock than other light-end gases (ethane through butane) and much more easily than oils of C-6 and above.
Figure 2 illustrates how the hydrocarbon chain ratios change during drilling in a section of a lateral. In this case, methane dominates the gas flow in first and second gas shows, but the gas composition changes in the third gas show, indicating a change in either organic carbon content (on which heavier gases can adsorb) or a higher-permeability streak, perhaps a natural fracture.
This approach allows for more targeted fracturing, eliminating pumping frac treatments into unproductive sections of a horizontal wellbore. In fact, I was able to cut two or three stages from every well using this method in one shale play, saving significant cost while getting better production than any of the offset wells.
Reservoir engineers often disagree with this approach because they believe there could be natural fractures in close proximity, but not intersected by the wellbore, that could be contacted through hydraulic fracturing. That is valid reasoning, but the absence of gas in a section of a shale should, at minimum, be a warning flag. I prefer concentrating the fracturing investment in areas that show the greatest potential for flow.
Maximizing Contact
Natural fractures and stresses along the wellbore are critical to developing large fracture-to-formation contact areas. The key to production is maximizing contact with these flow channels. The challenge is keeping them open; not only propped, but free of liquids that block the microcracks. Slower production decline generally is associated with using premium proppants and frac fluids that can transport the proppant deeper into the fractures. There is an economic trade-off in this area that is very likely shale-specific.
In my opinion, there are definite technology gaps in fracturing when shales are considered. Propping the microfissures would require small (»200 mesh) proppant grain sizes that may be easier to transport, but may act as plugging agents in or around other, larger mesh proppants. The proppants for fracturing should have a narrow mesh size range. Mixing different particle sizes can increase the risk of decreasing permeability, with proppant going from a propping agent to a plugging agent pretty rapidly.
Opening and stabilizing even the smallest fracture could deliver hundreds of times more flow capacity than the interstitial porosity offered by the matrix of the shale. The enormous number of these natural fissures and fractures, if propped, could deliver flow capacity where none existed before.
It is also important to recognize that even when closed, natural fractures may open before the rock actually fractures. Research conducted by Julia Gale at the Bureau of Economic Geology at the University of Texas found that natural fractures open at 50-60 percent of the pressure required to create a fracture in the non-naturally fractured rock. Even when the natural fractures appear filled with calcite, the fractures could be opened easily since calcite does not bond tightly to silica (Figure 3).
FIGURE 3
Weakly Bonded Calcite ‘Fill’ in Previously Closed,
Filled Natural Fracture (New Albany Shale)
Source: Julia Gale, Bureau of Economic Geology at the University of Texas
Higher pressure in unconventional reservoirs adds significant reserves stored as free gas in the fractures, overcomes capillary blocking problems, and enables better recovery. Pressure management during flow back after the fracture treatment can preserve gas drive energy and help drive both water and hydrocarbon liquids toward the wellbore. Holding a small level of back pressure on a well during flow back may keep fractures from closing early.
This pressure management is very important in some formations, such as the Eagle Ford and the Haynesville shales, but may not be as important in other, perhaps more brittle shales. Managing the pressure drop may decrease the initial production rate, but repeated testing has shown increases in total fluid recovery for those formations in which it is needed. Flow-back control and analysis can reveal a great deal about the reservoir.
The amount of total dissolved solids or salts in the fracture flow back and the ratio of specific ions in the back-flowed water are part of the data package that can provide valuable information about the fracture type and formation access points. Tracers used in the fracture treatment also can provide a wealth of information that can improve both technical and economic success when stimulating a shale well. Changes in water chemistry reflect the architecture of the stimulated fracture network.
Monitoring these data can indicate whether the fractures are planar or complex, and how fluids have mixed. Water returning from a freshly fractured formation will have different ion ratios than water returning from natural fractures. Flow-back analysis can help decide the type and degree of drawdown control to use, including rate and pressure drop as well as information on optimizing the fracture treatment.
Improving Recovery
The future of shale likely is intertwined with chemistry inside the rock and how it can be modified. Reducing viscosity of the liquids through CO2 flooding is a known process in conventional reservoirs, but the concept has not yet been applied on a large scale in shales.
Surface modifications, including changing the interfacial tension between the flowing fluid and the rock as well as the surface tension between the fluids (gas, water or oil), reducing capillary blocking pressures, and perhaps even chemical modifications and/or reactions with in situ oils are possible, although certainly not easy–yet.
It may be important to examine the wetting layer on shale surfaces to determine if a wetting or coating layer can be thinned or removed. This topic is where the industry needs to take a step back and think outside the box about how chemistry could be used in conjunction with pressure, heat, added fluids or even catalysts.
Adding production chemicals in the fracture stimulation should be considered also. This has generated favorable results in the Bakken and Eagle Ford shales. Chemicals may include various inhibitors, microemulsions, surfactants, solvents, liquefied gas, gas-phase surfactants, and dispersants. Carbon dioxide can be used to reduce viscosity, while surfactants can reduce interfacial and surface tensions.
Where a large contact area has been created and held open, an opportunity emerges to inject a sweep fluid, either as a well-to-well drive or a huff-and-puff technique. Because of their relatively low cost, both natural gas and carbon dioxide are attractive options. Gas-phase surfactants added to the sweep can help pry the oil from the rock surface. The gas provides drive energy and the surfactants either strip the oil coatings off or further reduce the interfacial and surface tensions within the rock, reducing capillary blocking pressure.
The fact that natural fractures will open at 50-60 percent of the pressure required to fracture the well makes this approach particularly interesting, since the lower opening pressure for natural fractures would require smaller pumps or compressors and much less power. Using dense-phase gas may further reduce the surface pressure required to push the fluids.
One might expect a very quick response in this type of flood as the gas front sweeps through the reservoir. In some of these reservoirs, fractures will have had time to refill with oil from the fissures, but might be blocked by narrow or closed fracture sections. Using a simple displacement sweep, operators have a chance to inexpensively evaluate the concept.
Once tested in active fields, gas sweeps also could be used to reopen unproductive wells. Gases would be used to repressurize the reservoir, put solvents back in and start recovering residual hydrocarbons. Companies that know how to apply technology might be able to pick up plugged wells and breathe new life into them.
Natural gas prices strengthened significantly this winter, but given the continued valuation difference between oil and natural gas, relatively low recovery costs, and high gas recovery rates, injecting natural gas for flooding oil shales may be economic over the foreseeable future.
Moving Forward
Progressing techniques for improved recovery from oil shales from a conceptual stage to the prototype stage for evaluation will have to be accomplished one step at a time. The first step may be a laboratory setting as part of a university program that is studying shales already and has a good idea of the macropores, microfissures and other key properties.
In this environment, stress tests could be run on flow capacity of the fissures and methods of opening them. Initial studies at the University of Oklahoma found these microfractures and fissures are in the neighborhood of a couple ten thousandths of an inch wide, and other work shows the fractures may inflate several fold under fracturing pressure.
The next step would be a well-to-well test. Companies are moving to tighter well spacing with smaller, more numerous fracture stages per lateral. An ideal test would compare results from wells that are reasonably close.
The approach would be to gas flood from one horizontal well to another, rather than a pattern flood. If some of the gases could be swept into fractures and fissures, their flow capacity definitely would be changed. That may take a bit of trial and error because we must know what we are placing and evaluate how to optimize the performance.
This kind of field test would help operators optimize fracture positioning, fracture effectiveness, and the use of production enhancing chemicals in the fracture system. When two parallel wells start flowing back, connectivity between the wells could be evaluated. The next step would be implementing gas flooding with just enough pressure to open the natural fracture systems and add a gas phase surfactant. Including core analysis would reduce experimentation cost and time.
At the end of testing, we would have a much better idea of whether the reservoir’s reaction to gas flooding meaningfully improved oil recovery. I believe total liquids recovery in some liquids-rich shales can be raised from today’s 5-8 percent level. This will take a lot of science, but the upside could be a significant increase in oil recovery. The industry should be researching and applying practical science and spending the money to conduct research and field testing. This is the surest way to elevate liquids-rich shale reservoirs to a new level of production performance.
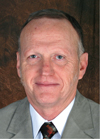
GEORGE E. KING is distinguished engineering adviser at Apache Corporation with more than four decades of industry experience. He began his career with Amoco Production Research. King also served as a petroleum engineering consultant and new technology advocate at BP Amoco, an adjunct professor of petroleum engineering at the University of Tulsa, senior vice president of engineering at Rimrock Energy LLC, and a consultant on completion, stimulation, intervention, shale well fracturing, and workovers. He is a former Society of Petroleum Engineers distinguished lecturer, and has served on numerous SPE committees and workshops. King is a recipient of the Amoco Vice President’s Award for technology, and SPE Production Operations Award and was SPE’s Houston Region’s engineer of the year in 2012. He holds a B.S. in chemistry from Oklahoma State University, and a B.S. in chemical engineering and an M.S. in petroleum engineering from the University of Tulsa.
For other great articles about exploration, drilling, completions and production, subscribe to The American Oil & Gas Reporter and bookmark www.aogr.com.