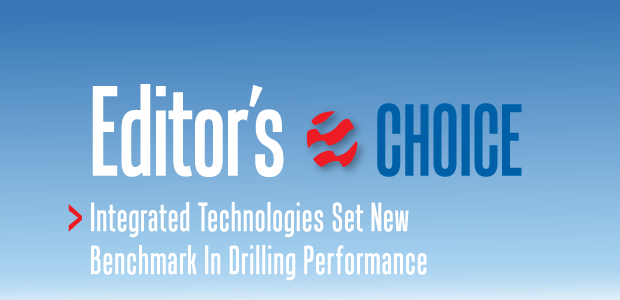
Integrated Technologies Set New Benchmark In Drilling Performance
By Dale Fidurko, McKenna Czerneski and Adam Cobb
PARKERSBURG, W.V.– Daily footage has become a key metric in quantifying Northeast drilling efficiency, and the pace of the improvement has been phenomenal. Six or seven years ago, drilling 2,500 feet of lateral in a day was a major accomplishment. Today, some operators are drilling 4,500-5,000 feet/day regularly. However, in September, HG Energy II LLC, in partnership with Baker Hughes, a GE company, redefined Marcellus/Utica performance standards by drilling 9,055 feet in 24 hours. In fact, it is believed that the West Virginia horizontal well set a new world record for footage drilled in a single day.
HG Energy II’s objectives on this well were to minimize the number of drilling days and reduce overall drilling costs while remaining in the target zone and producing a smooth, completion-ready wellbore. The drilling environment was not particularly severe in terms of reservoir pressure and temperature, and because the company’s team already had drilled several Marcellus and Utica wells in the region, it had a good understanding of the target formation’s location, thickness and properties.
However, the operator recognized that staying in-zone throughout the length of the well at such high rates of penetration would prove challenging without the right technology. The drilling operation had to address wellbore stability and quality management challenges to simplify running casing and completion tools in the long-lateral well to avoid stuck-in-hole situations or other downhole problems during drilling, casing and multistage hydraulic fracturing.
The answer was an integrated drilling solution that paired an advanced high-buildup rate rotary steerable system (HBRSS) with a high-performance drilling motor and a customized, high-velocity PDC drill bit. It also utilized remote integrated reservoir navigation and measurement-while-drilling services to keep the well on target, avoid crossing faults, and attain fast and consistent ROP.
The remote navigation and MWD technology were key in keeping every foot of the lateral within the target zone, achieving 100 percent net-to-gross across the entire interval. Maximum instantaneous on-bottom ROP exceeded 1,000 feet/hour, and over the 24-hour period, ROP averaged more than 375 feet each hour.
The entire 9,146-foot lateral, which extended from 7,300 to 16,446 feet measured depth, was drilled in 1.04 days. The curve and lateral together were drilled in 3.64 days, which was 1.86 fewer days than the aggressive 5.5-day drilling plan had called for, reducing overall drilling cost by 35 percent compared with offset wells. In an environment where the time required to drill from spud to total depth is critical to well economics, saving almost two full days of rig time without compromising wellbore quality or operational safety is consequential.
The drilling landscape in the Marcellus and Utica shale plays has changed dramatically in recent years, with operators realizing ever-greater efficiency gains and establishing drilling records seemingly with each new project. By slashing drilling times and optimizing drilling and completion designs, the industry has forced down break-even costs even as it has ramped well productivities by orders of magnitude in West Virginia, Pennsylvania and Ohio.
According to the U.S. Energy Information Administration, new-well natural gas production per rig averaged nearly 17 million cubic feet a day in the third quarter in the Appalachian Basin, representing a five-fold increase since 2012. Even during the 2014-16 industrywide downturn, when rig counts plummeted, well productivities kept climbing, propelling regional gas output to all-time highs. In October, production in the basin topped 29 billion cubic feet a day for the first time, up 375 percent in six years.
Horizontal drilling performance was redefined in September when a world-record 9,055 feet were drilled in a single day in an HG Energy II LLC-operated Marcellus well in West Virginia. The operation achieved maximum instantaneous on-bottom ROP exceeding 1,000 feet an hour, averaging more than 375 feet/hour over the 24-hour period. The entire 9,146-foot lateral was drilled in 1.04 days while staying 100 percent in zone using an integrated drilling solution with an advanced high-buildup rate rotary steerable system, a high-performance drilling motor, a customized PDC bit, and remote reservoir navigation and MWD services.
One of the driving forces behind the incredible production growth is integrated drilling technologies that are improving the wellbore construction process and making it possible to efficiently extend Marcellus/Utica lateral lengths to 10,000 feet and longer. The value proposition is simple: Longer laterals expose more shale volume per well, which means higher per-well productivity, which in turn, generates more revenue per well regardless of wellhead price. If those longer laterals can stay within the highest-potential reservoir zone and reach total depth in less time with fewer trips in and out of the hole, operators can lower well cost meaningfully while simultaneously enhancing production and recovery rates.
Integrated Technologies
A number of technologies and processes support the successful execution of record-breaking shale drilling projects, including fit-for-purpose fluids, drill bits and cutters customized for specific downhole conditions, and RSS and MWD/reservoir navigation tools engineered for directional drilling applications. Over the past four years, integrating these technological components in the Appalachian Basin has increased average lateral footage drilled per well by 30 percent and increased daily footage rates by 33 percent. This step-change in drilling efficiency has allowed operators to increase the Marcellus/Utica well count by 30 percent using 42 percent fewer rigs.
The proper drilling mud plays a key role in keeping the wellbore stabilized, particularly when drilling a one-mile or longer lateral in an open-hole horizontal section. Geologic variations and operational considerations from one well or pad location to another make customized drilling fluid solutions crucial in the Marcellus/Utica and other resource plays.
Each fluid system should be developed with careful consideration of the particular drilling environment, the characteristics of the reservoir and the wellbore design challenges that must be resolved. Water-based mud systems can be customized to improve shale stability, maximize clay inhibition, minimize pore pressure transmission and improve ROP–all while reducing well costs and environmental impact.
Drilling high-quality wellbores at fast penetration rates would not be possible without innovative bit technology. The newest generation of PDC bits are designed with application-specific profiles that improve cutting and mechanical efficiency, boost ROP and run life, and extend durability while minimizing vibration.
In the case of the HG Energy II well, the bottom-hole assembly was equipped with an 8 1⁄2-inch high-velocity drill bit that had been optimized and revised numerous times over the course of several years for Marcellus/Utica operations. This design incorporated a refined blade layout and the latest in PDC cutter technology to maximize speed, efficiency and reliability. Hydraulics were also key for this bit and it was the product of ongoing analysis and testing to maximize cuttings evacuation in these high-performance well settings.
Proper gauge configuration is imperative with a HBRSS. The bit’s gauge was customized to provide the necessary lateral responsiveness to achieve strong buildup rates in the curve, while providing ample stability to mitigate drilling dysfunctions over the course of the run. This configuration has been refined with software modeling, lab testing and field data.
Key Differentiator
HBRSS is a key differentiator that is enabling record-setting drilling success in the Northeast region. Specially designed for shale applications, HBRSS can drill challenging build-outs and curve/long-lateral sections in a single run. This advanced technology is revolutionizing the way horizontal shale wells are drilled by taking a fundamentally different approach to rotary steerable design principles using continuous proportional steering rather than conventional push-the-bit and point-the-bit systems.
Push-the-bit systems use steering pads that deflect against the wellbore in an on/off cycle, which raises the risk of doglegs and drilling an angular wellbore profile. Point-the-bit systems use a BHA with a fixed tilt, which causes hole spiraling and a consistently over-gauge wellbore. Both systems restrict bit selection and flow rates, which artificially limits ROP and hinders steering control, invariably raising well construction costs and possibly leading to diminished production rates.
In contrast, the HBRSS solution deployed in HG Energy II’s Marcellus well uses precision-controlled pads that maintain a continuous proportional steering vector to ensure superior control for a smooth, in-gauge borehole, even with complex horizontal trajectories. The technology constantly monitors near-bit inclination and steering vector to make course adjustments every second, if needed. This effectively eliminates the risk of high-local doglegs for trouble-free casing and completion runs.
And because holes remain in gauge, the driller can collect high-quality MWD data (bulk gamma and azimuthal gamma) to optimize drilling operations, lateral placement and steering, and reserves estimations. In-gauge holes also minimize cuttings and maximize hole-cleaning velocity.
Figure 1 compares the effectiveness of the three primary steering methods using high-resolution wireline inclination measurements from more than 700 wells drilled in the Middle East. The results demonstrate that point-the-bit (shown in red) and push-the-bit (green) steering mechanisms both tend to drill wells that drift, sometimes widely, around the target inclination. On the other hand, continuous proportional steering (blue) shows an ability to reduce tortuosity by four-six times. This translates to consistently better hole quality in horizontal wells.
FIGURE 1
Wellbore Inclination versus Measured Depth for RSS Steering Methods
Source: SPE 189408, Albaraa Alrushud, et. al.
Working closely with the operator’s team, a single target inclination was set for the HBRSS to hold throughout the record drilling run on the Marcellus well, effectively reducing the downlinks needed to consistently stay in zone without manual user intervention. Adding a high-performance drilling motor increased torque and rpm at the bit to optimize HBRSS drilling performance.
Most Critical Element
Even with all the advanced technologies deployed on the Marcellus well, the single most critical element contributing to the success of the operation was teamwork and the commitment of dedicated personnel from both the operator and service provider during all phases of the project. HG Energy II’s drilling engineers and geologists worked closely with the directional drilling and reservoir navigation engineers at BHGE, to develop and deploy an integrated drilling solution to minimize nonproductive time while accelerating drilling speed and efficiency.
Extensive preplanning and pre-pad meetings among the team helped minimize delays and address any questions or uncertainties before the drilling rig arrived on location. Operational efficiency was improved further with the remote MWD/reservoir navigation support provided by subject matter experts located at an offsite operations center. The remote experts were available 24 hours a day to analyze data and provide assistance and insights to the geologists located at HG Energy II’s office and to drilling personnel located on the rig.
It must be emphasized that it would not have been possible to achieve a record drilling performance without the full support and buy-in of the field personnel. Each person was committed to staying on the rig around the clock as a dedicated resource to make sure that every part of the operation–from data transmission and the drilling mud system to geosteering and downlinking–went precisely as planned. Members of the field crew, many of whom were relatively inexperienced and previously had not worked with one another, took ownership of their respective roles on the team and in attaining the bottom-line project objectives.
Buoyed by the success of the Marcellus well, HG Energy II is planning to soon use the same integrated drilling solution on a Utica Shale well with a lateral length of approximately 16,500 feet, which would rank as the longest horizontal Utica well ever drilled in West Virginia. Both the operator and service company realize that unforeseen complications can arise whenever a drilling crew attempts to push operational limits to new boundaries. That is why it is so important to take experiences and lessons learned from one well to improve drilling operations on the next well as part of a continual improvement process.
The same combination of advanced technology, operational expertise and collaborative operator/service company teamwork that enabled the safe drilling of the long-lateral Marcellus well in record time will be fundamental to further advancing the already world-class performance of Marcellus/Utica horizontal drilling. While drilling 9,000 feet in a single day is not likely to become the new normal anytime soon, with mile-a-day footage rates quickly becoming routine, averaging 7,500 feet in 24 hours may be a realistic target for operators in the very near future.
Dale Fidurko is drilling and completion manager at HG Energy II Appalachia LLC in Parkersburg, W.V. He began his career in 2008 as a field engineer at East Resources Inc., and subsequently served as a field superintendent at Shell, director of operations at Inflection Energy LLC, and director of operations at S&A Resources. Fidurko holds a degree in petroleum and natural gas engineering from Penn State University.
McKenna Czerneski is engineering manager at Baker Hughes, a GE company, which has drilled more than 200 wells in the Marcellus and Utica shale plays with footage rates exceeding one mile a day. She joined the company in 2010 as an MWD/LWD field engineer in the Appalachian Basin. Czerneski holds a B.S. in petroleum engineering from Montana Tech of the University of Montana.
Adam Cobb is a project manager at Baker Hughes, a GE company. He joined BHGE in 2009 as an MWD/LWD field specialist in the NE region. Cobb holds a degree in animal and veterinary sciences from West Virginia University.
For other great articles about exploration, drilling, completions and production, subscribe to The American Oil & Gas Reporter and bookmark www.aogr.com.