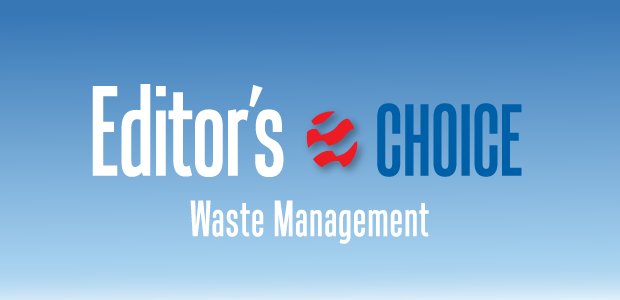
Modern Waste Disposal Is Safe, Green
By Gabriel Rio
A healthy oil and gas industry has been vital to the United States’ economic progress for more than a century, and sensible regulation has been key to fostering industry advancement and ensuring its continued success for the benefit of our country, consumers and industry.
For decades, oil and gas operators have been allowed to dispose of much of their drilling, completion and production waste by putting it in sometimes unlined pits or spreading it on ranchland. These processes were necessary in the 20th century to enable the oil and gas industry to satisfy the incredible thirst for energy that fueled the rapid expansion of the U.S. and global economies.
However, in the 21st century, the industry is undergoing an unprecedented transformation in response to global concerns about its operations’ impact on climate change. Emissions from flaring and other production operations have received growing attention as investors, the media and the public increasingly apply pressure to reduce greenhouse gas emissions. The industry is responding positively, but we can do an even better job of improving overall environmental performance even as we continue to demonstrate our commitment to advancing our communities’ quality of life.
Already, major producers are pledging to achieve net-zero carbon dioxide emissions by 2050, with a concerted effort to make operational changes that lessen any adverse impacts from oil and gas operations. Operators compiling their first sustainability reports are thinking rightfully about water recycling, reuse and disposal, as well as improving their ability to monitor and capture carbon emissions.
While most technologies and processes at drilling sites have advanced in response, waste management practices largely have lagged. More attention can and should be focused on cost-effective alternatives to disposing of drilling and production waste that is exempt from the Resource Conservation and Recovery Act. Identifying and leveraging these alternatives can improve groundwater and soil protections, and further shrink drilling’s carbon footprint.
Traditional Approach
Drilling and production waste contained in reserve pits during drilling, including drilling mud components and cuttings, are not regulated as hazardous waste because of the RCRA exemption. Land application, or land farming, of mud and cuttings, like the use of earthen reserve pits during drilling, continues to be allowed in some states, including Texas and Oklahoma, while others, such as Pennsylvania and New Mexico, effectively prohibit the practice.
Typically, reserve pits are dug near the drilling rig to circulate returns out of the hole, or to contain waste mud or cuttings. But in addition to water, clays, and drill solids or cuttings, the spent material often includes hydrocarbons, salts and other constituents that, if not for the RCRA exemption, likely would be considered hazardous waste.
Professional oil field waste disposal facilities, including slurry injection wells and landfills with multiple liners, sequester carbon-rich waste streams while protecting groundwater supplies and the environment more effectively than on-site disposal.
When drilling is finished and the rig moves off location, construction crews may bury the reserve pit by pushing the dirt excavated to build it back into the pit. Some practices install artificial liners in the pit, but those liners usually are thin and unreliable. Alternately, the returns might be removed from the pit and applied to nearby farm and ranch land by spreading the material thinly and tilling it into the soil. Both practices leave oil and gas operators legally and financially vulnerable.
Reserve pits and land farming risk the possibility of groundwater and soil contamination that can cost operators sizable remediation sums in the future. Usable groundwater often is 50-150 feet below the surface. Depending on soil permeability, drilling materials stored in pits or spread on the land easily can migrate downward. Material spread on the land and tilled into the soil also can contribute to soil contamination from salts and hydrocarbons, which can contact groundwater when mixed with runoff from rainwater that recharges groundwater reserves.
GHG Emissions
Hydrocarbons from land-spread materials evaporate as they degrade and constitute GHG emissions. Indeed, third-party engineers estimate this common, traditional practice can emit 300 metric tons of carbon dioxide equivalent (CO2e) for each new well, assuming a horizontal well design with three strings of casing, 10,000 feet of productive lateral length, and 60% recycling of oil-based drilling mud.
Depending on hydrocarbon chain length, some hydrocarbons will evaporate quickly while others move into the air more gradually as the material is exposed to sunlight, air and microorganisms that shorten the hydrocarbon chain. Such gradual evaporation means land-farmed waste can become a meaningful source of GHG emissions for an extended time and contribute to the country’s total emissions.
Since 1970, CO2 emissions alone have increased by about 90%, with fossil fuel combustion and industrial processes contributing about 78% of the total GHG emissions increase from 1970 to 2011, according to the U.S. Environmental Protection Agency. In 2019, EPA estimates put total U.S. GHG emissions at 6,558,000 metric tons of CO2e.
Although GHG emissions remain above 1970 levels, they have been declining in recent years largely from actions taken by the energy industry. Since 2005, national greenhouse gas emissions have fallen 10%, and power sector emissions have fallen 27% even as our economy has grown 25%, according to the EPA’s 2020 annual report on national GHG emissions. This effect was driven primarily by a switch from coal to natural gas in power generation. It demonstrates the effectiveness of a national effort. The energy industry has been a leader in GHG emissions reduction, and we can do more.
Low-Hanging Fruit
Despite overall progress, oil and gas companies looking for ways to reduce their waste management operations’ GHG intensity may not be considering the fugitive emissions that come from applying material to the land. The evaporating and degrading hydrocarbons have a real, verifiable impact. For operators committed to reaching a net-zero operation, this is low-hanging fruit.
Using pits and land farming may no longer match our values of minimizing our industry’s environmental impact. If taking contaminated material and placing it on the ground increases the likelihood of groundwater and soil contamination and meaningfully contributes to the oil and gas industry’s GHG intensity, we should reconsider these practices. They are no longer necessary and are completely avoidable in a very cost-effective manner.
Thanks to significant investments from service providers, the average drilling rig in the Permian Basin is within 30 minutes of an oil field waste disposal facility. Coupled with advances in facility operation, this proximity often makes the facilities as economic as on-site disposal.
Waste management decisions often are handled by field personnel rightfully concerned with costs and logistics, including drilling performance and employee safety. With the advent of more abundant and cost-effective professional waste management infrastructure, drilling supervisors now can elevate their focus on continuing to shrink adverse environmental impacts.
Historically, off-site disposal facilities for cuttings and other spent drilling material were limited, but that is not the case anymore. Oil and gas waste management companies have invested hundreds of millions of dollars in infrastructure to handle material, including injection wells for slurry disposal and multilined landfills that can accommodate all other waste material and ensure the safety of the environment and the public.
In the Permian Basin the average drilling rig now is located within about 30 minutes of a permitted, professional facility. This proximity effectively renders reserve pits and land farming there unnecessary, easily avoidable and obsolete.
Modern Disposal Processes
Waste management facilities operate using different processes, depending on the waste stream. One key process, slurry injection, involves injecting waste into deep formations. In slurry injection, water- or oil-based mud, tank bottoms and other oily, dirty water and materials are processed, and subsequently blended with produced or flowback water at the disposal facility. Particle size, solids loading, fluid density and viscosity are monitored and managed.
The slurry then is injected into deep geological formations that, because of their placement beneath multiple, impermeable layers, are isolated from shallow groundwater reserves. Those formations typically range from 4,000-12,000 feet deep. Slurry injection facilities take the entire carbon-rich waste streams, blend them and inject them, effectively sequestering the carbon.
One waste management company is estimated to have sequestered 279,000 metric tons of CO2e in 2020. In 2021, with the oil and gas industry recovering, that number will be close to 400,000 metric tons of CO2e.
Permitted energy waste landfills accept certain waste streams that cannot be injected economically. Landfills are a better way to dispose of contaminated soil, including drill cuttings and other materials, and are very different from reserve pits or land applications. Simply put, the landfills are heavily engineered, more rigorously regulated and incomparably superior to reserve pits when it comes to ensuring protection of groundwater and soil.
Unlike reserve pits with single, thin natural or synthetic liners, regulated landfills incorporate a system of multiple liners, including extremely thick layers of synthetic liners containing high-density polyethylene. These systems include leak detection and leachate collection layers. Any waste recovered in the leachate systems is either returned to slurry facilities through a sealed pipeline, where it is permanently sequestered by injection, or solidified with other forms of solid waste and sequestered in the landfill. Beneath the entire system is a natural or synthetic clay liner.
Altogether, the systems are designed to hold up for the long term and isolate waste streams from the surrounding environment. The landfills also have an extensive network of groundwater monitoring wells to ensure they are not impacting groundwater in any way.
Advances in oil and gas drilling and production waste management provide a real opportunity for operators to flip the narrative around and show others that the industry is making substantial progress in minimizing its carbon footprint. Closed-loop waste handling and disposal can turn a liability and potential black eye for the industry into an opportunity to make meaningful progress toward meeting net-zero goals.
Cost-Effectiveness
Cost always is an important concern when weighing the pros and cons of adopting a closed-loop waste management system. The good news is that closed-loop systems often cost no more over the long term than using reserve pits and land farming. More oil and gas waste management companies are pricing services to be cost neutral.
For many Permian Basin drilling operations, it does not cost any more to take waste to a professional facility than to bury it on site. This cost differential has been effectively eliminated by two factors. First, the expansion of energy waste infrastructure has ensured there always is a permitted facility near the drilling rig, and second, energy waste disposal’s growing efficiency has driven down disposal pricing. This has allowed professional disposal to be as cheap as on-site methods, even before considering the potential liability associated with leaving waste on lease.
In a traditional system, it costs money to excavate and construct reserve pits and close them when drilling is finished. Spreading material and tilling it into the land also can be a big expense, and operators must compensate landowners for additional surface damage. In contrast, in a closed-loop system, on-site roll-off boxes receive the waste and are trucked off for disposal. The system also allows operators to recycle and recover more material.
Investing in a closed-loop system may only require tens of thousands of dollars for a well that costs $6 million-$8 million. If the rig is not going to be on the pad long, it is more economic to use a closed loop system than to invest hundreds of thousands of dollars in the reserve pit.
Operators who adopt a closed-loop system also avoid paying for future contamination from a pit. If future contamination occurs, operators must remove the contamination and remediate the surrounding area, a cost that can be substantial. In addition to paying for cleanup and removal, operators will incur the expense of extensive soil and groundwater testing.
I have witnessed this firsthand. I oversaw a landfill operation in North Dakota several years ago in which a customer paid more than $750,000 to clean up a single reserve pit and remove contaminated soil surrounding it. That was in addition to the costs associated with trucking, bringing engineers and scientists on site to sample the soil and hiring heavy equipment operators to dig up the material.
At that time, hauling the waste material off at the front end in North Dakota would have cost only $10,000-$15,000 more for each well.
More recently, in Texas, we have participated in multiple cleanups of old reserve pits that had been improperly closed after drilling ended. In every one of these incidents, the cleanup cost of the contaminated reserve pit exceeded the operators’ perceived “savings” during the drilling process by many multiples.
Insurance
It’s important for oil and gas operators to know that insurance typically will not cover reserve pit remediation or other issues from waste intentionally left on site. Insurance providers will not insure for known or purposeful contamination, including materials rich in hydrocarbons, heavy metals or salt.
In another example as recent as 2019, a major operator agreed to pay an undisclosed settlement in a lawsuit brought by a neighborhood of Oklahoma homeowners who argued that polluted soil and water resulted from reserve pits that previously had been buried on the development.
More companies are adopting closed-loop systems even in areas where they are not required. These companies understand that going beyond regulatory requirements to protect groundwater and soil, as well as reduce GHG emissions, is the right thing to do.
Drilling efficiencies and successful production in the New Mexico portion of the Delaware Basin demonstrate that closed-loop practices are viable, cost-effective and environmentally sustainable. Energy producers elsewhere must move away from outdated waste management methods that potentially can harm humans and the environment. In the process, they can mitigate their environmental impacts, maintain their social license and adopt best practices that enhance their overall operations.
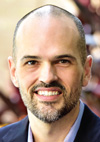
GABRIEL J. RIO is president and chief executive officer of Milestone Environmental Services LLC, an independent energy waste sequestration company with assets throughout the Permian Basin and the Eagle Ford Shale. He previously was executive vice president of strategy and business development for R360 Environmental Solutions Inc. Before that, Rio worked for McKinsey & Co, UBS Investment Bank, TCR Private Equity and Purvin & Gertz. He holds a B.S. in chemical engineering from the University of Texas at Austin.
For other great articles about exploration, drilling, completions and production, subscribe to The American Oil & Gas Reporter and bookmark www.aogr.com.