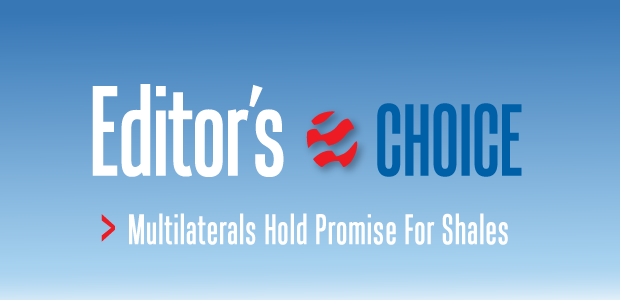
Multilaterals Hold Promise For Shales
By Doug G. Durst
Editor’s Note: The proceeding article is the first in a two-part feature on applying multilateral technology in unconventional plays. Part II will appear in AOGR’s August issue and primarily focus on completion and multistage stimulation options for multilaterals.
HOUSTON–In conventional geological formations around the world, multilateral drilling has been synonymous with improving recovery by contacting more reservoir area and adding drainage. Thousands of multilateral wells have been drilled and completed in conventional plays, including complex deepwater and extended-reach wells. Particularly in heavy oil applications, multilateral technology has improved field development efficiency by more effectively draining the reservoir with fewer well locations, saving drilling and completion costs while minimizing production and surface equipment needs.
While there have been limited applications to date in U.S. onshore tight oil and shale gas reservoirs, multilateral wellbore architectures ultimately could revolutionize how resource plays are developed. In these plays, the technology can help operators meet the objective of recovering the maximum amount of hydrocarbons at the lowest cost per foot of completed borehole by increasing exposure to the reservoir volume. Moreover, multilateral wells can be more economical from a drilling and well construction perspective, and help operators achieve improved economies of scale in production and treating facilities.
Multilateral solutions have been deployed in a handful of unconventional resource plays, including the Bakken Shale, the Mississippian Lime, the Granite Wash, and multiple formations in the Permian Basin. The documented benefits in these early applications include increased well productivities and the ability to access multiple targets using a single parent wellbore (reducing surface footprints to maximize lease acreage while potentially increasing recovery factors).
Experience shows that the overall success of any multilateral well likely will be more dependent on the planning and execution associated with drilling and completing each individual lateral leg than with the wellbore’s construction. Therefore, all the typical critical factors that determine the success of a single horizontal well also apply to a multilateral well in unconventional reservoirs, including factors such as drilling in the optimum orientation/direction, intersecting the “sweet spots” of a shale section to ensure good conductive fracturing, completing with the proper hydraulic fracturing design, etc.
Adopting multilateral technology would introduce a step change in unconventional reservoir development, combining the well construction capabilities of multilateral drilling with multistage hydraulic fracturing and commingled production. Development programs in unconventional plays have gained tremendous efficiencies and cost savings by progressing from a single pad with a single horizontal well to a single pad with multiple horizontal wells, and operators should achieve additional efficiencies and savings by moving to single-pad/multiple-well multilateral programs. Figures 1A and 1B illustrate how multilaterals can increase reservoir access, in this example, comparing single horizontal wells with dual-laterals on a four-well pad.
The key to success will be the optimal planning and scheduling of operational procedures and surface facilities. There are many operational, logistical and infrastructure-related aspects of multilateral reservoir development that must be taken into account, particularly if economics are the primary determining factor.
TAML Junction Levels
For well construction, operators have the choice of constructing Technology Advancement of Multilaterals (TAML) level 1, 2, 3 or 4 multilateral junctions, each of which has specific benefits and design issues. While the levels of complexity and cost progressively increase from level 1 to level 4 (Table 1 compares trips between typical level 2 and 4 multilateral wells), cost efficiencies can be gained with higher-level junctions. Moreover, higher-level junctions provide pressure isolation and mechanical support, and in some cases, allow repeatable and positive re-entry into any given lateral.
A level 1 junction is a multilateral with an open-hole main bore and an open-hole junction. Typically, bent sub motors or directional drilling bottom-hole assemblies are used to kick off and drill a lateral from the main branch. This is generally the lowest-cost option because it does not require any additional junction/casing equipment and a minimal number of trips, but the downside is that re-entry and production isolation are limited. Level 1 wells typically are stimulated by running a long fracturing string to depth, fracturing the lateral, running the frac string to a point just outside the main bore (in the lateral), and then cutting the string and repeating the process for the other lateral(s).
A level 2 junction has a cased and cemented main bore and an open-hole junction. To sidetrack and directionally drill additional laterals, a milling system is necessary to cut a casing window. A liner can be installed in the lateral and cemented, or an open-hole frac sleeve completion can be installed, both with a polished borehole receptacle (PBR) positioned at the top of completion/liner string. As with a level 1 lateral, a long surface frac string can be used in some level 2 wells. However, there always will be some length (30-50 feet) of open-hole section from the main bore to the top of the lateral liner/completion.
A level 3 junction has a cased/cemented main bore and a liner isolating device in the junction to provide mechanical support. The liner device typically has an oriented pre-milled window opening to allow access back to the main bore, and a milling system is used to cut a casing window to directionally drill laterals. Most level 3 multistage fracturing completions consist of open-hole sleeves combined with an open-hole packer for stage isolation. Typically, the entire completion is run and tied back to the main bore and all the packers and hangers are set before releasing the rig and moving in a frac spread to begin multistage treatments.
A level 4 junction has a cased/cemented main bore combined with a cemented liner in the junction to provide cement isolation and mechanical support. Some level 4 versions use level 3 junction equipment, but add cement. Another solution is to cement the liner in place with the liner top near the top of the window, removing the portion of the lateral liner top in the main bore. Level 4 eliminates any open-hole formation area in the junction and provides easier access to the lateral liner. Because the junction is cemented, level 4 is better suited for plug-and-perf or cemented liner fracturing. An open-hole fracture completion, combined with an inflatable packer and stage tool, can be used to stage cement the junction area to get the benefit of level 4 design.
Initial Field Applications
Several operators have experimented with multilateral technology in unconventional reservoirs in North America, and have deployed various types of junctions as well as lateral entry options for completion and stimulation. In many cases, the operators have documented cost savings and environmental improvements when transitioning to pads with multilateral architectures. These initial applications also have identified some of the key design issues and operational considerations for drilling, completing and producing multilaterals in resource plays.
One example of a multilateral application in a resource play is a 25-well program that SandRidge Energy executed in the Mississippian Lime play using open-hole sidetracks and cased-hole whipstocks to initiate the multilaterals. The wells used various configurations, and validated the mechanical feasibility, economic and production benefits associated with multilateral development in the play.
Other examples are a Cimarex Energy-operated project in the Granite Wash in the Texas Panhandle that constructed dual level 4 junctions drilled from a single vertical wellbore, and Penn West Exploration’s dual-lateral development program using open-hole junctures and open-hole multistage systems in the Slave Point tight oil play in northern Alberta.
In assessing the economics of a multilateral project, the cost of drilling additional vertical sections has to be compared with the cost of building junctions for the multilaterals. For example, consider the case for drilling and completing two single horizontal wellbores from a pad versus a dual-lateral wellbore. The higher the cost of the vertical section of each horizontal well, the more competitive becomes the cost of creating a multilateral junction and isolating it for stimulation.
As with a single horizontal well, a multilateral requires a minimum of a drilling rig, a frac spread and a coiled tubing unit. However, how the well is drilled, completed and stimulated determines how and when this equipment is used, and how long it is required on location. In some cases, a workover rig could be used instead of a drilling rig for certain operations. On the other hand, the contiguous use of a fracturing spread, CT unit and workover rig also could be necessary, which would obviously impact the bottom line.
Design Considerations
Should reservoir pressures require a barrier to be installed after each lateral is stimulated to protect against working in a “live well” scenario, it could require lubricator risers, a CT unit and a crane to either remove or drill out the temporary barriers. It may be possible to use a CT indexing tool to retrieve barriers to stimulate additional laterals. If not, a diverter/deflector will have to be installed to gain re-entry into additional laterals, requiring a workover rig.
Mobilization/demobilization costs can be a factor in determining the economics of drilling and completing a multilateral well. The impact of rig moves on overall project economics are a bit of an unknown, since each operator schedules rig moves relative to mobilizing frac spreads a bit differently. For pad drilling, however, optimized rig and frac spread moves can be managed to effectively minimize mobilization/demobilization costs without drastically impacting overall authorization for expenditure (AFE).
Planning multilateral well subsurface activities requires the same stringent approach to drilling and completion as a single horizontal well, with some caveats. Given that multiple lateral legs are created from a single well, there is a greater need for nontortuous wellbores, good hole cleaning practices, accurate pipe tallies, high-level torque and drag modeling, and accurate force and stress calculations. In addition to sound operational procedures, it is critical to ensure that surface equipment and facilities can support the multilateral wellbore construction activity. This includes having load and torque capabilities to accommodate milling operations and setting/releasing various temporary packer-based BHAs, whipstocks, diverters, deflectors, etc.
Window quality and window milling issues has been a concern for some operators that have experimented with multilaterals. Constructing long, straight windows and ensuring debris removal are crucial for getting completion strings and centralized liners into the laterals in level 2, 3 and 4 junctions. Some operators have attempted to use level 2 junctions with one-trip whipstock milling systems, but have had to make second mill runs to extend window openings to get liners or completion strings to depth, or revert to level 1 completions because of window issues. A cement log should be run to ensure the window kickoff area has satisfactory cement. If not, a squeezed cement operation should be performed before milling begins.
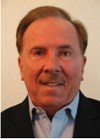
Doug G. Durst is a global technology adviser for Halliburton in Houston. His diversified industry background spans drilling, completion and production, and he has been associated with a number of service companies, with responsibilities ranging from product and business development to project management. Durst holds multiple patents. He has a B.S. in engineering from the University of Houston.
For other great articles about exploration, drilling, completions and production, subscribe to The American Oil & Gas Reporter and bookmark www.aogr.com.