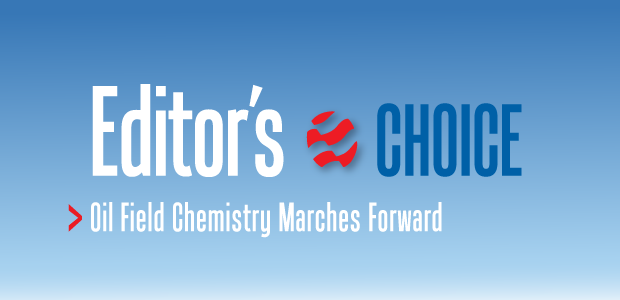
Oil Field Chemistry Marches Forward
By Colter Cookson
Whether it is being included in completion fluids to reduce pumping pressures or applied to an aging stripper well to prevent equipment corrosion, chemistry is vital to oil and gas production. It can be tricky to find chemistries that are affordable, effective and compatible with the chemicals, water, oil and rock they will encounter.
Advances in chemistry are furthering the quest for economic solutions. Equipped with proven techniques for automating costly experiments and evaluations, chemical providers say they are developing better products for everything, from maximizing unconventional wells’ initial production rates and treating fracturing flowback to optimizing waterfloods and reviving stripper wells.
These solutions frequently perform better than their predecessors while minimizing safety risks and the industry’s impact on communities, service companies report. They add that technology transfer is alive and well. For example, one company says it is introducing the oil field to a mixing technique long used in other industries to boost chemicals’ effectiveness by hastening the point at which they achieve peak efficiency.
Operators increasingly have the knowledge and interest to seek new chemistries when they face challenges or need to improve their acreage’s economics, says Danielle Allen, senior vice president of global communications and technology commercialization for Flotek Industries Inc. She attributes operators’ growing focus on chemistry to several trends.
“The publicly-traded oil and gas producers are focusing on profits rather than production growth at the behest of their shareholders,” Allen observes. “They are prioritizing capital efficiency, and chemistry is one of the most cost-effective knobs producers can turn to get more from their acreage.”
In many plays, operators already have pinpointed the optimal lateral lengths and proppant intensities, suggests James Silas, Flotek’s senior vice president of research and innovation. “Increasing lateral length and proppant intensity appear to have reached a point of diminishing returns in many plays, including the Midland and Delaware basins,” he says. “That leaves chemistry as one of the primary ways operators can improve well economics.”
Successful chemistry is tailored to the reservoir, emphasizes Bill Hill, the company’s vice president of basin and reservoir chemistry. “The rock matrix, in situ water and oil, and completion fluid all help determine which chemistries will be most effective for meeting the operator’s goals,” he says. “For example, if the oil in a reservoir has a high paraffin content, it makes sense to include more solvents and increased detergency.”
Improving Predictability
“Unconventional reservoirs’ characteristics vary far more than the industry once assumed,” Hill adds. “When we look at cuttings from laterals, we often see changes in the rock matrix chemistry from the heel to the toe. If we want a treatment to deliver the expected results, it needs to be robust enough to accommodate those changes.”
It’s possible for generic, one-size-fits-all solutions to work, but their results tend to be inconsistent, Hill warns. “Data from across basins shows a reduction in production variability and uncertainty in the wells that are treated using a reservoir-centric approach,” he reports. “More predictable results make it easier for operators to allocate capital.”
To show how beneficial reservoir-centric completion chemistry can be, Hill shares a comparison of two four-well pads in Karnes County, Tx. All eight wells targeted the Lower Eagle Ford and had lateral lengths around 5,000 feet, comparable proppant intensities, and similar separation distances from the nearest lateral.
The wells completed using proprietary blended surfactants and solvents tailored to the reservoir had a cumulative 12-month production of 88,413 barrels of oil equivalent for every 1,000 feet of lateral, Hill relates. The other wells employed more intense completions, with an average 883 pounds of proppant pumped per foot rather than 771 pounds. Nevertheless, they only delivered 50,837 boe per 1,000 feet of lateral, almost half as much as the ones with reservoir-centric chemistry, according to public data provided by RS Energy.
The benefits of tailoring chemistry to the reservoir are visible in much larger datasets, Hill assures. As an example, he cites a study of wells targeting the Wolfcamp A in the Texas counties of Midland, Martin and Upton. The study included 122 wells treated with a reservoir-centric blend of solvents and surfactants and 240 wells completed using other chemistries.
“The wells were completed around the same time, so they had similar lateral lengths and proppant intensities,” Hill says. “The ones treated with reservoir-centric blends had an average cumulative three-month production of 7,464 boe for every 1,000 feet of lateral, while the others produced 6,679 boe for every 1,000 feet of lateral despite using 50 pounds more proppant per foot, according to data from RS Energy.”
Hill says the difference in production between the wells has persisted for three years (Figure 1). “The reservoir centric chemistry offsets the decline curve, providing incremental barrels,” he assesses.
Growing Integration
Operators are taking a more integrated approach to chemistry, Hill remarks. “In the past, completion engineers would be the primary people asking about completion chemistry,” he recounts. “Today, interest has spread upstream to the geology and geophysics folks who describe the reservoir and make predictions about how it will produce.”
By incorporating completion chemistry into their models, these geoscientists can more accurately predict wells’ production, costs and returns, Hill explains.
As operators in many plays shift focus to infill drilling, they must grapple with fracture-driven interactions between wells, Silas notes. While completing a child, or infill, well occasionally boosts the parent’s production, the effects frequently are detrimental. For example, the child well’s completion could alter pressure gradients and flood the parent.
“The industry is using several approaches to mitigate frac-driven interactions,” Silas says. “These include increasing well spacing or using smaller treatments on the infill wells to minimize the chance of cross-well communication; shutting in, pre-loading, or conducting a preventative refrac on the primary well to protect it; and adopting modified zipper fracs or cube development techniques to minimize the time between completions.”
The right chemistry can complement those approaches, Silas says. “In many applications, the chemistry’s goal is to improve the mobility of the infill well’s completion fluid and the in situ water and oil,” he outlines. “This reduces the chance of a phase blockage or shortens its duration while improving oil recovery.”
To illustrate how much chemistry can help, Silas describes a remediation treatment for a well targeting the Woodford Shale in Grady County, Ok. “The primary well had been on production for 250 days before an infill well’s completion severely reduced its production,” Silas recalls. “Even 100 days after the completion, production had not returned to previous levels. To restore it, we designed a remediation program to mobilize the trapped water and remove the phase blockages it created.
“After the program, the primary well’s water production spiked. Once the water was unloaded, oil production returned to prior levels,” Silas reports. He estimates the program accelerated the well’s recovery by 200 days.
Water Recycling
“Water is a precious resource for both the oil and gas industry and the communities in which it operates,” notes David Horsup, vice president of research, development and engineering (RD&E) for Nalco Champion’s upstream business. “It will be even more precious in the future, so we are finding ways to help operators recycle produced water at economically attractive costs.
“As part of that effort, we are developing friction reducers (FR) that work in produced water with extremely high concentrations of total dissolved solids,” Horsup relates. “Our newest FR polymers hydrate/uncoil and reduce friction reliably, even at very high TDS levels of 240,000 parts per million. This allows flowback and produced water to be reused, minimizing dependency on freshwater.”
In December, this SpaceX Falcon 9 rocket delivered a particularly corrosive strain of microbes from the Permian Basin to the International Space Station. By studying those microbes’ effects in microgravity, where biofilms grow more rapidly than they do on Earth, Nalco Champion is deepening its understanding of localized corrosion. The company says the research is part of a broader effort to help customers assess their microbial risks more precisely and identify the most cost-effective solutions.
Nalco Champion also is refining water treatment chemistries, according to Vic Keasler, the company’s RD&E director for oil field chemicals. He says the company has developed a comprehensive program for treating produced water that controls iron sulfide, hydrogen sulfide and microorganisms.
“With an effective treatment, recycling produced water can deliver a great return on investment,” Keasler says. “An operator we worked with in the Fayetteville Shale went from recycling none of its produced water to recycling all of it, which reduced each well’s freshwater consumption by 20-50 percent and saved the operator $1.2 million in water-related costs.”
Digital technologies also are beginning to impact water treatment. Keasler points out that with sensors replacing manual water sampling and dosing, remote monitoring systems and algorithms can automatically determine how much chemistry is required to treat the water effectively.
Microbial Control
Microbial risks continue to be a challenge in the oil and gas industry. When unchecked, microbial growth can lead to localized pitting corrosion, hydrogen sulfide production and fouling, Keasler notes. He describes treating completion fluids with microbial control chemistries as critical to reducing microbial risks, even in areas where the risk appears low. “The Eagle Ford is a classic example,” he says. “Because downhole temperatures there often exceed 250 degrees F, many operators assumed microbial treatment would not be required.
“Unfortunately, that proved not to be the case,” Keasler says. “While the downhole temperature limited growth, organisms that survived were able to flourish once the fluids returned to the surface and cooled, which led to extremely high corrosion rates in topside separation facilities and production pipelines.”
It is possible to fight corrosion-causing microbes at the surface, but to reduce overall costs, Keasler recommends controlling them from the start. This control involves a robust biocide program during drilling, completion and drill-out operations. “Appropriate treatment programs will vary from one formation to the next,” he acknowledges. “Understanding the risk and designing an appropriate program is key to reducing a microorganism’s potential impact.”
Nalco Champion’s research continues to find ways to predict and control microbial risks more accurately, Horsup says. “We have been deploying new analytic techniques, such as quantitative polymerase chain reaction technology, to quantify microbes and identify high-risk organisms in operators’ pipelines, filters and membranes,” he explains. “By studying how different microbial consortia correlate to corrosion, we are able to estimate customers’ risk based on a system's microbial populations.”
As part of that effort, Keasler says, the company partnered with the Center for Advancement of Science in Space and NASA to utilize microgravity to understand the mechanism of microbial corrosion risks better.
“Previous research established that biofilm thickness, mass and cell number are significantly increased on the International Space Station (ISS) relative to what is observed on earth,” Keasler says. “By comparing the biofilms and corrosion rates in microgravity and Earth’s gravity, we can begin to understand the factors that directly influence the localized corrosion phenomenon.”
Understanding microbial corrosion risks would be difficult on Earth alone because it would be impossible to grow a larger but otherwise identical biofilm without a corresponding passage of time, notes Keasler. Aside from biofilm thickness and time, other factors that may drive corrosion rates include a bacteria’s total mass and activity levels.
“We have completed the growth experiments on the ISS and the Earth controls and are analyzing the data from the experiment. We hope to complete our findings in 2020,” Keasler says.
Enhancing Production
To help unconventional operators improve initial production rates and flatten their decline curves, Nalco Champion has been actively developing novel chemical solutions, Horsup reports. “To maximize their impact, we are tailoring formulations to reservoir characteristics,” details Horsup. “Geology, temperature, pressure, and water salinity all dictate the optimal formulation.”
The company is finding formulations that work in both high temperatures or high salinities and are compatible with conventional completion fluids, Keasler adds.
“On the production side, we are developing digital technologies to identify wells that need attention so we can manage by exception rather than checking every well,” he describes. “We also are refining monitoring techniques for production issues such as paraffin so we can offer more precise and accurate chemical recommendations.”
When the company dispatches technicians to a well site, they may be equipped with intrinsically safe augmented reality headsets to enhance their problem-solving capabilities, Horsup mentions. “If they come across a problem, they can use this technology to connect to a center staffed by our top experts, show what they see, and get immediate advice, which enables us to bring our best minds to the field in real time,” he concludes.
Accelerating Innovation
To help operators continue to become leaner and meaner, chemical providers must develop more efficient internal processes, argues Jonathan Wylde, head of innovation for Clariant’s oil and mining business unit. “To remain competitive, we need to look at the way we conduct research and development, so we can develop solutions to operators’ problems faster and cheaper,” he says.
By leveraging robotics, miniaturization and data analytics to automate experiments, chemists at Clariant’s new high-throughput experimentation laboratory in Houston can evaluate formulations rapidly. The company predicts this capability will help it develop more cost-effective solutions for common problems, including corrosion, scale, paraffin and methane hydrates.
Toward that end, Wylde says Clariant has expanded its laboratory in Houston to include high-throughput experimentation (HTE), a technique that allows chemists to automate experiments, and conduct several in parallel, using robotics, miniaturization and data analytics. According to the company, the facility is the first of its kind supporting the oil and gas industry.
To illustrate HTE’s power, Wylde uses corrosion inhibitors, which he estimates account for 25 percent of production chemical spending. “High-throughput experimentation can provide a performance indicator on a corrosion inhibitor formulation every 15 minutes, meaning it can evaluate 96 formulations a day,” he says. “That is much faster than traditional application testing, which takes weeks for each formulation.
“HTE does not replace such testing,” he notes. “However, it allows us to look at a much wider range of formulations and ranks them, so we can focus more detailed and expensive testing on the most promising options.”
Screening and ranking numerous formulations will be especially beneficial for corrosion inhibitors, Wylde predicts. “The most effective corrosion inhibitors blend three, four or five base chemistries to unlock synergies that increase performance by orders of magnitude,” he says. “But get the mix wrong, and the chemicals can go from working together to working against each other.”
Traditional techniques have limited even the best chemistry companies to exploring a small fraction of possible formulations, Wylde says. While that will remain true even with HTE, he predicts the technique will empower veteran chemists and help Clariant identify inhibitor formulations that are 15-20 percent more effective than traditional alternatives at comparable cost.
“Corrosion inhibitors have become so complex and synergistic because corrosion is an age-old problem into which several industries have poured resources for the past 80 years,” Wylde reflects. “By making experiments more affordable, HTE should allow us to accelerate progress for the younger and simpler chemistries used to address scale, methane hydrates, paraffin and asphaltenes.”
Noting that Clariant’s oil and gas business has used HTE capabilities at the company’s Center of Innovation in Germany for years, Wylde says the technique already has led to improvements in paraffin inhibitors. As an example, he offers a new inhibitor for cold regions, such as Canada and the Rocky Mountains.
“Because they are waxy, much like paraffin itself, paraffin inhibitors are notoriously difficult to deploy in cold temperatures,” Wylde says. “In the past, the industry needed to install and operate tank and line heaters to keep the inhibitors warm, or buy low-concentration inhibitors and pump them at high rates to ensure they had an effect.
“HTE has helped us develop a high-concentration inhibitor that is pumpable even at minus 40 degrees F,” he reports. “The concentration is 10 times that of the closest classical winterized polymers, which means the inhibitor will deliver a 10-fold increase in performance.”
Green Chemistry
By nourishing carefully engineered enzymes with plant sugars that otherwise go to waste, Solugen can produce environmentally-friendly peroxides and iron control agents, says Tom Swanson, the company’s vice president of innovation.
“The enzymes convert the plant sugars into organic oxidizers and bio-chelants that have a low toxicity and excellent biodegradation when exposed to the natural environment,” Swanson describes. “These green characteristics reduce the risk that dangerous chemicals will enter the water table during hydraulic fracturing operations or waterfloods. They also are safer and easier to transport and use.”
The bio-chelant has proven extremely effective at keeping iron in solution, Swanson reports. He mentions that this reduces the risk of corrosion and scale in production equipment and pipelines, as well as simplifying water reuse.
This before-and-after comparison shows that Solugen’s bio-chelant helps remove iron sulfide by sequestering the Fe3+ irons. The chelant biodegrades when exposed to the natural environment and can be produced much closer to oil field activity than traditional alternatives, Solugen says, noting that this reduces the costs and environmental impacts associated with shipping.
“The green bio-chelant is a big improvement over traditional iron control chemistries,” Swanson says. “The most common, tetrakis hydroxymethyl phosphonium sulfate (THPS), is toxic, can be produced only through a dirty process and must be imported from China. There are amine-based alternatives, but like THPS, they biodegrade slowly and must be used in a controlled manner.”
The green chemistries Solugen produces can help reduce carbon emissions associated with oil production, Swanson says. “The peroxide and bio-chelant are made using oxygen, water and dextrose from corn sugar, a renewable resource. For every ton produced, the creation process takes several tons of carbon dioxide from the environment,” he says.
Swanson adds that the chemicals are made in Houston, eliminating the cost and emissions associated with importing THPS. “The production process has a small enough footprint that, as demand grows, we can build miniature mills even closer to the action,” he says. “For example, we plan to put one in Midland to supply the Permian Basin and one in Bakersfield, Ca., for that region’s oil producers and farmers, who use our chelant and peroxide for crop irrigation.”
In California, the green chemistries are helping clean water so it can be injected down hole during waterfloods. “By controlling iron with our chemistries, some of the operators in the Los Angeles Basin have been able to double the amount of water they can inject without exceeding the state’s injection pressure limits,” Swanson reports. “This is increasing their oil production while preserving safety and regulatory compliance.”
In Oklahoma, the chemistries have helped disposal well operators comply with injection pressure limits, Swanson continues. In Texas, he says they are remediating production lines clogged by iron sulfide to reduce the overall cost to ship crude oil to refineries.
“In the agricultural industry, we are conducting field trials to see how well our chemistries clarify irrigation water and protect irrigation pipes and spray nozzles from corrosion and plugging,” Swanson mentions. “We are looking at other applications outside the oil and gas industry as well. If they are as successful as we hope, they will help create the demand necessary to build miniature mills near more plays.”
Oil Mobilizer
The chemicals used to enhance or improve oil recovery often create byproducts that reduce the crude’s value and add to downstream processing, observes Kevin Gentry, president of MadMackenzie Solutions. He says he founded the company to market an enzyme that mobilizes oil more efficiently without chemical reactions.
“This enzyme is a water-soluble protein that has three components: a nonionic DNA part that is attracted to oil and two polar parts, H+ and OH-, that do not like oil. Once the DNA part contacts hydrocarbons, the two polar parts result in an enzymatic fit that physically releases and mobilizes the oil. This interaction produces no byproducts of any kind and is the reason for our excitement about this technology.”
In video demonstrations on MadMackenzie’s website, the product rapidly releases droplets of oil from an oil-soaked rock in water, Gentry describes. He adds that this behavior can be applied to oils with gravities ranging from API-10 to API-40 or beyond. “Utilizing application-specific methodologies, we can treat heavy oil and light oil alike without altering the oil’s viscosity, impacting the hydrocarbon chain or creating emulsions,” he says.
An enzyme distributed by MadMackenzie Solutions mobilizes oil without altering the composition, maintaining the oil’s value and avoiding processing complications. The enzyme does not interact with salinity or acidity, the company adds, allowing it to excel in a variety of formations.
“The enzyme is an inert molecule,” Gentry continues. “It only reacts with oil, so it can be paired with other chemicals without worrying about compatibility issues. The product does not react with salinity or pH, enabling it to mobilize oil from a variety of formations. Nor does it imbibe on rock like a surfactant; without significant product loss to imbibition, we can effectively displace the product farther into the reservoir without losing efficacy, helping to reach and recover trapped oil.”
Because it only interacts with oil, the enzyme has no risk of harming humans or animals, Gentry assures. “In toxicity tests, its impact on minnows is comparable with that of drinking water,” he reports. “It is noncorrosive to equipment and nonpathogenic, and it is not a food source for any bacteria, making it a low-risk solution for operators.”
Longevity is one of the enzyme’s biggest strengths, Gentry maintains. “Because it works at the molecular level as a catalyst that generates motion rather than through chemical reactions, none of the protein components are altered as a result of its interaction with oil. This allows the product to continue working in the reservoir for much longer durations than traditional chemistry,“ he explains.
Eventually, the enzymes will disperse through the reservoir and become so diluted that their effects are no longer detectable, Gentry acknowledges. “We do not know how long that takes yet, but in field trials, we have had treatments yield results for more than a year,” he reports.
In fact, Gentry says operators have been able to use produced water from a treated well to increase production from a second well. He cites multiple applications in Texas where clients have re-applied a single dose of product either through huff-and-puff methods or water injectors.
In waterfloods, it may make sense to treat the most productive wells through huff-and-puff techniques, then recover the water and deliver the enzyme to the other wells through an injector, Gentry suggests. “We are testing that approach in a Texas field with two injectors and 12 producers,” he relates. “The field has extremely tight rock and oil that has an API gravity of 24 degrees, so other treatments have had limited effect. But we are seeing production improvements that should deliver a positive ROI with effects lasting five or six months.”
Other ongoing field trials involve unconventional wells. “In one, we are adding the enzyme to the fracturing fluid to see whether it will slow the decline rate,” Gentry details. “In another, we are injecting the enzyme into two older unconventional wells to release the oil stranded in the existing fractures.”
Although it was invented by a Texas A&M graduate, the enzyme primarily has been used overseas, where Gentry says it has a 10-year track record with national oil companies. In the two years since MadMackenzie became the U.S. distributor, it has been applied to 30 U.S. wells, with about two dozen more coming before year’s end, Gentry says.
“We also are exploring surface applications,” he reports. “At its heart, the technology is an oil separator that mobilizes oil from other surfaces. It has been used to clean storage tanks and railcars, and is able to clean drill cuttings, soil and pipelines.”
Static Mixing
How well chemicals mix with the fluid they are supposed to treat has a significant impact on their effectiveness, says Paul Tarmann of Tellerus Corporation. “The amount of mixing relates directly to the turbulence inside the pipe where the chemical is being injected. Using traditional ports only allows inefficient mixing contact, if any mix occurs at all, within the stream,” he reports.
To accelerate chemicals’ dispersion, Tarmann recommends Tellerus static mixers. “Our mixers use baffles and mixing vanes inside the pipe to cause the flow to tumble and churn,” he illustrates. “Generally, the mixers are two to eight feet long. By the time the fluid gets to the end, the chemical is dispersed evenly throughout.”
For chemicals to be as effective as possible, they need to spread throughout the liquid that carries them. By using baffles and vanes to accelerate that dispersion, Tellerus Corp. says its static mixers unleash chemicals’ potential, enabling them to work even at much lower dosage rates.
According to Tarmann, static mixing has a long track record in other industries. “It is newer to oil and gas, but the results so far have been impressive,” he says. “In most applications, static mixing can reduce chemical consumption 40%-80% by making the chemical more effective.”
One of the most common uses involves production line emulsion breakers. “Because the static mixer allows the breakers to treat the fluid coming from the wellhead more quickly, operators are frequently able to reduce flowline pressures,” Tarmann relates. “In the Williston Basin, an operator reduced emulsion breaker demand 80%, saw a 35% drop in flowline pressure, and increased production five-six barrels a day.”
In that field trial, Tarmann says, the Tellerus mixer paid for itself in 90 days. “For emulsion breaker application, payback generally occurs in 90-120 days, but occasionally takes five or six months,” he calculates.
In Central Montana, an operator with high-water-cut stripper wells uses the company’s static mixers and produced water to deliver scale and corrosion inhibitors down hole, Tarmann reports. “Before installing the mixers, the operator needed to replace each well’s electric submersible pump every three or four years,” he recalls. “Ten years have passed since the installations. Only one pump has failed, and it lasted six years.”
Static chemical mixing also is helping operators in Montana and Wyoming clarify water to meet surface discharge standards, Tarmann says. In North Dakota, he adds, it is being applied to gas lift wells on multiwell pads to enhance hydrogen sulfide scavengers.
“We are only beginning to explore the potential applications,” Tarmann affirms. “In the near term, we hope to see our mixers applied to friction reducers used inside pipelines, to the biocides that treat drilling fluids and to paraffin inhibitors.”
For other great articles about exploration, drilling, completions and production, subscribe to The American Oil & Gas Reporter and bookmark www.aogr.com.