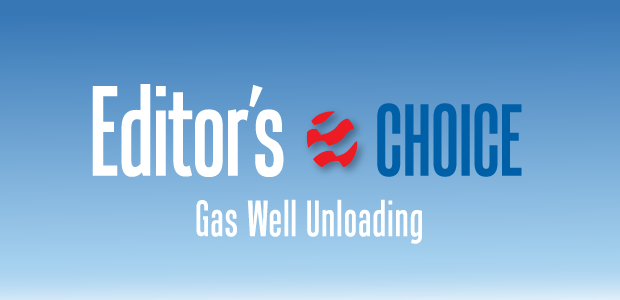
Savvy Operators Bring Mature Barnett Wells Back To Industry Forefront
By Paul Munding, Ted Garner and Nancy Choi
FORT WORTH–The unconventional revolution began in the gas-rich Barnett Shale of North Central Texas. But as the first commercial resource play, the Barnett is also the most mature, with the vast majority of wells at least 10 year old. As in other shale plays, where pressure support from the low-permeability matrix is low, when fractures deplete and bottom-hole pressure becomes dependent on matrix diffusion, mature Barnett wells often lack the necessary downhole pressure to efficiently unload liquids.
Consequently, many wells now require some means of unloading liquids to increase gas velocity above the minimum critical rate needed to flow gas and carry liquid droplets to surface. Using gas-assisted plunger lift (GAPL) to inject compressed gas down the annulus and into the tubing string for enhanced plunger efficiency is a proven solution for unloading gas wells.
With any flow through a pipe from reservoir to surface, there are three main contributors to pressure drop: gravity, friction and acceleration. Given the low rates, acceleration is negligible in these wells, leaving gravity and friction as the main contributors to pressure loss. However, the surface head pressure against which the well must produce also can add backpressure to the system. The higher the head pressure, the larger the critical rate necessary to overcome backpressure. Lowering head pressure by only 10 psig can make a tremendous impact on liquid-loaded, low-pressure gas wells.
Injecting gas into the well annulus lightens the fluid gradient and minimizes the gravity-related pressure loss in lifting the fluid to surface with a plunger. Gas injection directly reduces the pressure drop by reducing fluid density. Compression can reduce both head pressure and the density of the wellbore fluids, lowering wellhead production pressure at surface. Adding a “T” to the compressor’s discharge line allows some of the gas to be injected back into the well and the remainder to go to sales.
XTO Energy Inc. has numerous Barnett wells that benefit from compression to flow liquids and gas at low costs. For this compression application, cost is a function of efficiency. With a right-sized unit outfitted with the proper automation, efficient on-site compression and injection are achievable.
A choke on the injection line is required to control the amount of gas injected down hole. With an automated choke, the choke body adjusts to maintain a certain injection volume. In the absence of an automated choke, automation must originate upstream of the choke to control injection. This is where a rotary screw compressor equipped with advanced programmable logic controls has succeeded on XTO well sites. The PLC control system, coupled with a modem, allows users to virtually connect to a unit and remotely control it from anywhere.
Rotary Screw Packages
XTO Energy equipped three horizontal Barnett wells (wells A, B and C) with the rotary screw compressor packages and PLC panels. After that, it evaluated these systems by comparing them with the reciprocating compressors that previously performed the same function.
One aspect of success is properly sizing a compressor given the performance conditions. In these wells, when suction pressure dropped below 45-50 psig, it hampered the existing reciprocating compression that was injecting gas down hole. In Well C, the rotary screw package replaced a large recip that had struggled to inject efficiently with suction pressure below 45-50 psig. Insufficient head loading can occur when suction pressure is too low for a reciprocating compressor, causing the unit to run rough and reducing time to cylinder/packing failure.
In wells A and B, rotary screw units replaced small-horsepower, two-stage reciprocating units. The units lacked telemetry or autostart and recycle, and offered limited speed control, while also requiring at least 50 psig suction pressure. Between plunger cycles, the fluctuating suction pressure impacted the ability to stay under load while maintaining a high discharge pressure. This, in turn, cut the volumes at which these units could deliver.
Since failure can occur when reciprocating compression is not efficiently loaded, units tend to experience more downtime. Subsequently, the well will not obtain the injection needed to stay unloaded during downtime events, thereby increasing nonproductive time and cutting revenue.
Other Barnett wells in the area were studied for downtime impacts of compressor injection for liquids unloading. The study showed that low-pressure wells must always have a consistent source of lift gas to stay unloaded. When they do not, it can impact profit margins.
Another factor common in the Barnett occurs when multiple wells on a pad communicate with one another in terms of flow. If one well on a pad gets loaded, it can have a cascading effect on the pad’s other wells. As a result, the lack of compression run time gets magnified across a pad’s producing wells. Of course, considerable amounts of field personnel resources are absorbed when responding to compressor downtime issues. It involves not only compressor mechanics to bring a unit back on line, but also field personnel to evaluate the unloading of the well and return it to a routine operating sequence that harmonizes with the plunger system.
Reducing Backpressure
Well A has been producing since November 2010. As of mid-October 2021, it was producing 203 Mcf of gas and 13 barrels of water a day at 128 Mcf/d of gas injection, 106 psig casing pressure, 93 psig tubing pressure and 60 psig line pressure. The well is on GAPL, and the bumper spring setting depth is 7,593 feet measured depth at 47 degrees deviation.
The two-stage reciprocating compressor was struggling to produce, as evident from the beginning of Figure 1 (October 2020) through Feb. 24, 2021 (green line), when it was replaced by a 108-millimeter rotary screw. The well experienced high line pressure increases from 49 psig at the end of November 2020 to 60 psig in mid-December 2020. Even though this higher line pressure would benefit the compressor on the suction side to stay fully loaded, it also added backpressure at surface, which then prevented the plunger from surfacing completely.
Subsequently, several actions were taken that included fishing and replacing the bumper spring as well as replacing the plunger completely. Even soap sticks were dropped in an attempt to lighten the liquid and surface the plunger. However, none of these efforts were successful and the well continued to stay loaded for 75 days, reducing production from 232 Mcf/d before loading to an average of 54 Mcf/d during the loaded period.
When the rotary screw unit was set, it was configured so that it could send gas down hole through a manual choke and control was set through the PLC panel rpm speed control to give the well more injection volume when needed. All other gas on the discharge side was sent down the sales line. Immediately, the well was able to kick off with very little downhole injection (1.4 Mcf/d). At the same time, the compressor was able to lower wellhead pressure to 20 psig on the compressor’s suction side. This 20 psig of suction allows a minimum pressure with which to operate an SSD valve. Apparently, the minimal injection of the head pressure reduction was the impetus in successfully kicking the well off.
On the first day, the flow rate was 227 Mcf/d and then increased to 404 Mcf/d on the second day as the wellbore continued to unload storage gas volume. Injection was then targeted at 50 Mcf/d to maintain stable plunger unloading and the well stabilized above its trend, producing an average of 279 Mcf/d during a 30-day period following the first 10 days of unloading. Because of the added injection gas, water production also doubled to 16-20 bbl/d for this period.
From May to October 2021, line pressure gradually increased from an average of 47 psig to near 60 psig. From June to July, the well had a few worn-out plungers associated with a bumper spring unseating. Once the bumper spring was fished and replaced, production stabilized back on trend, allowing the well to unload via the plunger runs. In addition to lowering static head pressure to near 20 psig, 140 Mcf/d of injection gas has been used to maintain efficient plunger operations and well production.
The screw compressor has proven a perfect fit for this well, enabling a lower suction head pressure while delivering more injection volume to help reduce fluid gradient. Additionally, the ability to remotely control the unit by logging in to change rpm saves valuable personnel time and money, and the high compressor run time protects production revenues.
Optimized Injection, Production
Well B has been producing since June 2010. As of mid-October, it was making 164 Mcf of gas and 32 barrel of water a day at 230 Mcf/d gas injection, 146 psig casing pressure, 74 psig tubing pressure, and 69 psig line pressure (Figure 2). The bumper spring setting depth is 6,388 feet MD at 46 degrees deviation.
A 108-mm rotary screw compressor was installed on March 29, 2021 (green line). Three months prior to compressor change out, the small reciprocating compressor experienced sporadic downtime as it struggled to efficiently drop below 50 psig suction pressure to meet the conditions. The well also had “poor boy” gas lift injection valves removed in May. These shutdowns required time-consuming resets of plunger settings and gas injection volumes for GAPL operations.
After installing the rotary screw compressor, the suction controller was set at 30 psig and maintained at that level constantly. The pressure differential between a 69 psig line and 30 psig suction pressure made a positive performance enhancement. Comparing the well’s performance from Jan. 1 with Oct. 13, 2021 (before and after the rotary screw was set) shows decreased casing pressure (~25%), decreased gas injection volumes (~25%), and increased gas production rates (~27%) without compressor downtime.
Well C has been on production since January 2008. As of mid-October, production was 96 Mcf of gas and 18 barrels of water a day at 135 Mcf/d gas injection, 109 psig casing pressure, 55 psig tubing pressure, and 61 psig line pressure (Figure 3). The bumper spring setting depth is 6,379 feet at 47 degrees deviation.
The 108-mm rotary screw compressor was installed on June 30, 2021. Three months prior to compressor change out, the smaller reciprocating compressors were shutting down because of low suction pressure conditions. The recips averaged 71 Mcf/d gas production at 155 Mcf/d gas injection and 110 psig casing pressure.
Through mid-October, the well averaged 89 Mcf/d gas production (up 25%), gas injection averaged 143 Mcf/d (down 8%), and casing pressure averaged 104 psig (down 6%) on the rotary screw compressor. A constant 20 psig suction pressure was maintained with a 62 psig line pressure. The last three months on the production graph show consistent daily gas production, steady injection volumes and constant casing pressure. The injection rate appears to be optimized, and most importantly, indicates no downtime.
Increased Run Times
Keeping mature, low-reservoir pressure horizontal shale gas wells unloaded can be a challenge. Achieving success takes the right type of artificial lift solution tailored to the well’s individual needs. When looking at shale wells with low pressure and volumes below critical rates, one needs to attempt to lower the head pressure back against the well while ensuring the compressor can run consistently.
Each of the three Barnett wells exhibited marked increases when compressors were changed from reciprocating units to rotary screw packages that could deliver GAPL injection while also lowering critical wellhead backpressure by 10-30 psig. Only rotary screw compressor packages are able to get the wellhead suction pressure down to a range around 20 psig, which seems to be vital in getting these wells to unload. Proper compressor maintenance, as well as real-time telemetry alarm and control, are critical to achieving ideal run time.
The PLC-based advanced control system allows XTO to remotely control rpm (injection rate). As pressure depletes on older leases, XTO only injects intermittently instead of continuously while lifting the plunger. When the plunger goes into after-flow or off-time, the controller shuts off injection. As an alternative on wells with no controller, casinghead pressure transducers are used to control when an injection valve opens and closes. These advanced controls provide a huge advantage over the previous compressors used on the three wells, which lacked PLCs with auto-start and remote control access to change compressor settings.
Well A has had only 27 hours of fault downtime since it was set in February 2021 for 99.6% run time. Well B has had 48 hours of fault downtime since it was installed in March 2021 for 99.3% run time. Well C has only been faulted for 42 hours since June 2021, equating to 99.1% run time.
One often overlooked aspect of rotary screw compressors is their ability to be mounted on mobile trailers and used in place of a swab rig to kick off loaded wells with very little head pressure. In the past, the typical response to a loaded-up well that was failing to lift the plunger was to mobilize a swab rig to unload the liquids and allow the well to be vented while swabbing. If the swab rig is on location for two days, it can mean multiple days of venting. The rotary screw compressor in this case hits an environmental, social and governance homerun by capturing the gas in the sales line rather than venting it.
XTO now has three trailer-mounted rotary screw compressors to kick wells off in only a couple of hours versus multiple days of swabbing. In addition to the ESG benefit, a swabbing rig can cost $1,500-$3,000. Having trailer-mounted rotary screw packages allows XTO to quickly return wells to production rather than waiting for a swab rig.
Editor’s Note: The authors acknowledge the contributions of XTO Energy’s Bob Manthei, Jared Hebert and Robert Keim, as well as Flogistix’s Danny Cassady, Kris Hoff and Eric Kim.
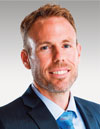
Paul Munding is vice president of petroleum engineering at Flogistix in Oklahoma City. Before joining the company in 2016, he worked as district production engineering manager in the Delaware Basin at RKI Exploration & Production/WPX Energy. Munding began his career in 2003 at Chesapeake Energy Corp., where he focused on reservoir, completion and production engineering in Mid-Continent plays. He holds a B.S. in petroleum engineering from the University of Oklahoma.
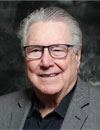
Ted Garner is senior petroleum engineer at Flogistix L.P. Prior to joining Flogistix in 2016, he worked for Compressco Partners L.P. as petroleum engineering manager. With 55 years of oil and gas engineering and management experience, Garner has worked with majors and independents both on and off shore in domestic and international basins. He holds a B.S. in petroleum engineering from Mississippi State University.
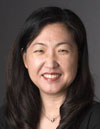
Nancy Choi is principal engineer at XTO Energy in Fort Worth. She joined ExxonMobil in 2003, where she conducted research to develop enhanced stimulation technologies for carbonate, tight gas and shale gas reservoirs. She transferred to XTO in 2011, working in Barnett, Eagle Ford and Piceance Basin assets. She currently supports hydraulic fracturing across XTO.
For other great articles about exploration, drilling, completions and production, subscribe to The American Oil & Gas Reporter and bookmark www.aogr.com.