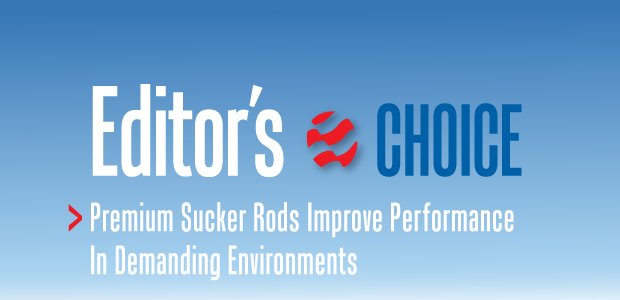
Artificial Lift Technology
Premium Sucker Rods Improve Performance In Demanding Environments
By Martín Bühler, Edgardo Lopez, Esteban Oliva and Federico Camara Guillet
HOUSTON–Downhole failures in artificial lift systems using sucker rods usually are related to three main component systems: the sucker rod string, the subsurface pump or the production tubing string. Failure can involve one of more of these systems, such as rod-tubing abrasive wear, but the good news is that readily available solutions exist to help producers overcome sucker rod string-related failures in challenging downhole environments.
Operating conditions for sucker rods are becoming more aggressive as water and the presence of carbon dioxide and hydrogen sulfide grow. In addition, increased bending loads and tensile stresses require robust mechanical properties. Under the combined effect of those conditions, sucker rod failures can occur mainly because of corrosion fatigue under multiaxial loads. Severe corrosion issues also are observed because of wear corrosion or erosion corrosion phenomena, again as a consequence of those demanding conditions.
Shale operations and high volumes of injected water for mature fields have shown increased risk of failures related to corrosion processes. Corrosion fatigue of carbon and low-alloy steels is a complex type of failure and the behavior of the materials is very hard to predict.
Therefore, the performance of steel under the combined action of cycling loads and corrosion depends on many factors, including the environment’s characteristics, the mechanical properties and the applied stresses. In corrosive environments, the fatigue life–both in terms of failure stresses and failure times–can be drastically reduced compared with the cycling stress in a noncorrosive environment.
As a result, there is a constant effort to evaluate the behavior of standard materials in aggressive environments, seeking to find stronger steels and connections. Currently, lab and field trials are being carried out both for sucker rods and rod couplings to develop materials that could notably increase sucker rod performance under corrosive environments.
Corrosion Fatigue
Corrosion fatigue is the result of the combined action of a cyclic stress and a corrosive environment to decrease the number of cycles to failure in comparison with the life in a corrosion-free context. Corrosion fatigue accounts for most of the sucker rod failures in the rod’s body and near upset bead areas.
Corrosion fatigue failures progress as an accelerated fatigue failure; the fracture is characterized by one or several initiation points, followed by a smooth fatigue propagation area (slow propagation), a rough propagation area (fast propagation), and the final fracture caused by a lack of section to sustain the load. When two or more initiation points are present, the typical ratchet marks frequently are observed. Concentric ring marks, known as beach marks, and river marks showing the direction of progression of the fatigue crack, are also usually observed.
The final fracture can be flat (uniaxialloads and low toughness materials) or angled with one or more “ears” (in cases with flexion/bending loads and/or high toughness materials). Corrosion fatigue failures often originate at corrosion pits, but pitting is not a prerequisite for corrosion fatigue cracking in steels. Furthermore, a used sucker rod could look like new, with no apparent defects, and still fail.
Because there is no real fatigue limit under harsh environments, a corrosion fatigue failure is unavoidable (i.e., a sucker rod working in a corrosive environment will always eventually fail). The speed of damage will depend on service conditions and rod characteristics. The corrosiveness of the environment can include CO2, H2S, or any other acidic gas dissolved in water. Chlorides, which are often present, also can increase the corrosion reaction.
The combination of bending loads and tensile stresses from the movement of beam pumping leads to failures at a reduced number of cycles when compared with the life cycle when only axial loads are present. This combination produces an effect where one side of the rod surface experiences higher effective stresses, resulting in the initiation and propagation of fatigue cracks.
In this type of failure, multiple fatigue initiation cracks usually can be found on the convex side of the rod coincident with the initiation zone. Bending or flexion loads are associated with deviations of the well or with compressive loads that lead to bending. These type of failures in sucker rods usually occur in combination with fatigue corrosion. Usually they are located close to the upset bead since the bending stress is highest at this point.
Premium Sucker Rods
Several years of research and development have resulted in new premium sucker rods technology designed to cope with demanding conditions in the field. Installed in more than 500 wells worldwide, results have been consolidated and analyzed applying specific key performance indicators from more than 200 installations. Operators have run the premium sucker rods in many combinations, including full string, taper combined with other grade taper (high-strength or API), and taper with fiberglass taper.
For simplicity, a protocol time period was defined and the net run life comparison (number of days) was calculated within it. Therefore, the majority of the data points were still active and counting days by the time this analysis was conducted. As general criteria, when a failure of the string or taper occurred, the following procedure was followed: change taper/string (most of the cases), or continue with the same taper/string. In both cases, the run life counter started from “zero” again. The resulting run life was calculated as an average of previous ones.
For the most part, there was an effort to replicate the operational conditions before and after installation. However, there may have been some cases where certain application conditions were modified, either in the interest of well productivity, or the overall performance in the system.
The loading range was typified for the analysis in a qualitative way. A three-tier system was used to provide insight to the set of complex and varied well conditions faced. Of course, with the premium sucker rod a non-API high-strength grade, the range levels were set in the upper half of the loading scale according to load level:
- Low load level (up to 60% Goodman);
- Medium load level (61%-80% Goodman); and
- High load level (more than 81% Goodman).
The goal of this approach for Goodman analysis was to normalize all loadings to 0.9 fatigue safety factor (SF) for ease of comparison, and is not a statement of application guidelines for different corrosive environments.
Because there is no universal standard to qualify the harshness of the environment for sucker rods in oil-producing wells based on fluid composition, a general criterion was established and expressed in terms of H2S, CO2 and bacteria content. Also, understanding the influence of chlorides (C1+) as a corrosion mechanism accelerator, this was incorporated in the ambient classification. Table 1 shows the reference values for each parameter.
In addition, the following factors were considered for scoring each case:
- High levels of Cl+ are not enough to qualify a corrosion level in the absence of an agent (CO2, H2S or bacteria);
- The presence of one agent is enough to qualify corrosion levels;
- More than two agents on the same level increase corrosion severity; and
- Above a medium load level (per previous Goodman classification), corrosion severity levels increase.
Performance Results
With more than 200 U.S. installations considered in the analysis (more than 450 estimated total strings), it has become the leading region worldwide utilizing the new premium sucker rod. A wide application range with a diverse set of goals was tested, including string weight reduction, increased reliability or run life in aggressive environments and increased production in wells with unrealized potential.
Although it was not possible to execute fully controlled test protocols, several variables were put under scrutiny, including rod loading, wellbore conditions, previous rod string/grade reliability metrics or production increase. Often, expectations of previous run life increase were specifically defined and measured. In other cases, a baseline doubling was set as a reasonable goal.
In this specific aspect of value proposition and expectations, it is important to highlight that most of the U.S. operators chose the toughest application conditions to test the new sucker rods to the fullest extent. Therefore, a very high percentage of the installations are located in high loading range and high corrosion-level environments.
The performance of the sucker rods was mainly being compared by operators against previous installations of D, KD and HS4138 rod. There was, of course, a slight predominance of KD rods in the Permian and Eagle Ford plays, and HS4138 in the Bakken play.
Results obtained in U.S. wells showed that the new rod operated in loading ranges around 90% Goodman (normalized to SF 0.9) in mild to aggressive fluid conditions. However, these results have to be aligned properly with run life expectations. As with any other steel component, under harsher conditions, a reduction in allowable loading capacity should be incorporated in order to deliver longer run times.
Figure 1 shows the grouping of the installs in loading versus corrosion level and the resulting run life increase for each batch of wells. The performance was aligned with the expectations from end- users for a 2x run life improvement in all corrosion levels at high loading ranges.
As corrosion increases to a mid-level, the widest separation is detected between the new sucker rod grade and D, KD and HS4138 rod grades. This is because it at this level of loading and corrosion where the previously installed rod grades suffered the most from corrosion fatigue mechanisms. The premium rods offer better performance with a higher life span.
Applying the same criteria, and grouping all regions’ data, the global integration of the results tends to mimic that of the U.S. experience. In general, increased run life was attained compared with standard steel rods under medium- and low-corrosion conditions. Results obtained in the different regions versus standard rod for each of the corrosion levels are shown in Figure 2. The results for low and medium corrosion levels were similar for all regions. In average, previous run life in this environment was almost duplicated.
Entering severe conditions, with increased presence of corrosion agents and accelerators, corrosion-fatigue mechanism experienced a higher probability of occurrence, with the majority of failures registered in the body. For these cases, other solutions to increase corrosion resistance dramatically should come from ongoing R&D programs.
Based on the results of the research performed for the new premium sucker rod, the rod grade selection chart shown in Figure 3 is recommended.
Wear Corrosion
Wear corrosion, or tribocorrosion, is a surface material degradation from the combined effect of corrosion and wear. When no corrosion is present, the main process related to wear failures in sucker rods is known as abrasive wear.
Wear is surface damage caused by the relative movement between two surfaces in contact. In sucker rods strings, this contact is a consequence of a well deviation or bending stresses applied on the string. When some corrosion is present, a synergetic phenomenon notably increases the wear process. The friction between surfaces removes the corrosion products that in static conditions usually act as a barrier to decrease the corrosion rate. Moreover, the particles of corrosion products are hard and can accelerate the rate of wearing.
The corrosion performance of materials could be completely different under static corrosive conditions when compared with dynamic conditions of wear corrosion or erosion corrosion. For example, low-alloy steels under CO2 corrosion lead to the formation of an iron carbonate siderite layer, which provides certain protection against further corrosion. However, the mechanical damage on this layer by sliding contact can destroy the siderite layer, eliminating its protection.
Aiming to address this issue, several tests were performed using specific equipment. A tribology machine implements a sliding contact between tubing and coupling segments while applying close-to-reality downhole conditions. By these means, the synergistic effect between wear and corrosion can be investigated suitably to provide a reliable “fast-test” screening method for tubing and couplings.
Tests were carried out in CO2-saturated brine at temperatures ranging from 60 to 135 degrees Celsius under anoxic conditions, and CO2 pressures of 4.5 bar. Wear conditions were simulated by applying a normal load of 500 N at ±20 strokes a minute. The friction coefficient between tubing and coupling was monitored continuously and material losses in both the tubing and coupling were measured with different techniques. The main goals of these tests were twofold: understand surface interaction mechanisms between tubing and coupling as functions of chemical composition and temperature, and determine the most adequate surface engineering solutions for mitigating tubing damage.
The results show a significant difference between both tubing and coupling wear (Figure 4). For this issue, a solution was presented through a coupling coating with superior erosion, corrosion and abrasion resistance when compared with standard API SM or T couplings, and with a lower wear rate on tubing.
The results also highlight that tribocorrosion is a complex phenomenon that requires adequate lab setups for performing experiments under realistic conditions. Extrapolation of data obtained under pure wear conditions is usually not reliable.
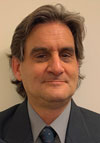
Martín Bühler is senior technology adviser of sucker rods at Tenaris. Bühler joined Tenaris in 1998, starting as a senior researcher in metallurgy and corrosion, and subsequently passed through the product engineering department before assuming managerial positions in quality control. Bühler holds a degree in physics.
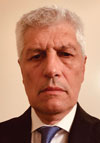
Edgardo Lopez is senior technology director for sucker rods at Tenaris. Currently based in Argentina, he has worked for Tenaris for more than 30 years, covering different technical departments and positions with international assignments in Mexico, Italy and the United States. Lopez holds a degree in metallurgical engineering and has completed post-graduate studies in welding and business administration.
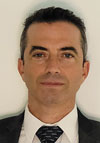
Esteban Oliva is senior North American technical sales manager of sucker rods for Tenaris. He joined Tenaris in 2019. Oliva began his career in 1996 after graduating with a degree in mechanical engineering, working extensively for both service companies and operators in artificial lift systems in Venezuela, Canada, Mexico, Colombia and the United States.
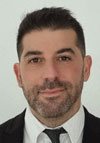
Federico Camara Guillet is senior technical sales manager of sucker rods at Tenaris. He is currently transferring to special projects as technical senior manager for Latin America. After graduating with a degree in electromechanical engineering, he joined Tenaris in 1997 as a process engineer focused on sucker rod production and optimization. He has worked in Argentina, Brazil, Colombia, Venezuela, México, North America, Europe and Africa.
For other great articles about exploration, drilling, completions and production, subscribe to The American Oil & Gas Reporter and bookmark www.aogr.com.