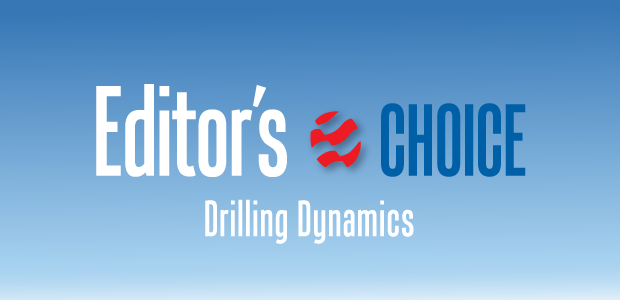
Robust BHAs And Better Bits Drill Faster And Farther
By Colter Cookson
U.S. oil production continues to set records with fewer rigs as rates of penetration increase, nonproductive time falls and laterals reach as far as four miles.
“Advances in horizontal drilling and hydraulic fracturing have increased well productivity, enabling U.S. producers to extract more crude oil from new wells drilled while maintaining production from legacy wells,” the U.S. Energy Information notes.
The increase in new wells’ production comes in part from the longer laterals enabled by rapid improvements in drilling efficiency. Whether these gains originate from novel ideas or gradual refinements to proven concepts, they are delivering step changes in performance.
The Delaware Basin illustrates how significant and fast progress can be. “An average well in the Delaware Basin requires two fewer bottomhole assemblies today than it did in the first quarter of 2020,” says Jonathon Schliem, U.S. sales engineer manager for Ulterra. “The time savings from eliminating trips varies from well to well, but it can often result in saving days of nonproductive time.”
BHAs can stay in the hole longer thanks partly to improvements in bit design. “For example, shaped cutters that mitigate downhole dysfunction have taken off in the Delaware Basin,” Schliem says. “Shaped cutters have been around for some time, but we have hit a turning point in terms of adoption as the cutters have built a track record that allows us to quantify how much they increase efficiency.”
Meanwhile, advances in materials science and manufacturing are equipping bits with more robust hardfacing and matrix powders, Schliem says. Add improvements to motors, rotary steerable systems and other BHA components, and efficiency can improve quickly.
“A year and a half ago, I would have advised many operators in the Delaware Basin to plan for two or three vertical BHAs or to plan for a dedicated curve assembly rather than trying to drill the curve and lateral in a single run. At that point, the ROP gains from swapping to a fresh bit made up for the tripping time,” he says. “Today, we are seeing higher one-bit tendencies, because bits and BHAs can stay in the hole longer and maintain high instantaneous ROPs.”
Energy is another critical aspect that is pushing performance, Schliem observes. There is more energy at the bit today than ever before. Motors are more robust, and rigs are capable of higher flow rates. “In the past five years, we have seen the average flow rates across the United States increase by up to 20%,” he details. “Our engineering teams are looking at how to maximize that flow to get cuttings away from the bit as quickly as possible.”
Consistency
As operators dial in on their acreage, they are asking BHAs for more consistent and repeatable performance, Schliem reflects. “By the time they move from delineation to development, many operators have enough data to understand what their performance should look like given today’s technology. They use that information to set a bar, so they know what to expect,” he clarifies.
As part of the push for more consistent performance, Schliem says drilling teams are emphasizing directional control. “This is true not only in the curve and lateral, but also in the vertical section,” he reports. “With more wells out there than ever, avoiding collisions has become extremely important.”
Schliem adds that a directionally capable BHA helps drilling teams achieve consistent performance by minimizing slide time.
Faster drilling speeds make quick corrections more important than ever, Schliem assesses. “Our drive to improve directional responsiveness has led to shortened cutter layout profiles and recently sparked a resurgence in shankless bits like our original UD513 design,” he says. “Now, using modern bit construction techniques, we can improve both responsiveness and tracking by matching the correct profile length with more contoured gauge pad designs.”
Strong directional control can help set the well up for long-term success, Schliem remarks. “Even on the drill bit side, we are seeing more people discuss how the drilling program affects completion and production,” he relates. “Usually, that manifests as operators asking us to design bits that minimize tortuosity so it’s easier to get tools into and out of the well.”
Accelerating Iteration
Whether an application calls for a longer profile that will drill a smooth, straight lateral, an aggressive design that will deliver eye-popping ROPs or a workhorse that will endure hard and abrasive formations, Schliem says it’s vital to learn from each run and consistently improve performance.
“We are not looking for one-hit wonders,” he stresses. “What moves the industry forward month over month and year over year are the constant incremental gains that we achieve together.”
Sustaining those gains requires a broad focus, Schliem suggests. “It’s not only making sure the designs are improving 2% or 3% with every iteration,” he says. “As a bit provider, we also need to look at our internal processes to figure out how we can be faster.”
Thanks in part to rapid design iteration, drill bits are getting better at harnessing the growing amount of energy provided by the rig and mud motor. In conjunction with improvements to other BHA components, Ulterra says the latest bits stay in the hole longer while maintaining impressive instantaneous rates of penetration.
Those internal processes range from manufacturing and back-office support to design and performance analyses. “We want to get as much information as we can from each bit dull and make sure we are addressing the problems seen in the field,” Schliem says.
“Maintaining trust and having strong relationships with customers is key,” he comments. “In cases when we are granted access to drilling data, we treat that as a privilege and work hard to reward it with quick feedback. That information not only gives us extra insight into how our bits perform, but also allows us to do our best work together with customers in developing products that aim directly at their operational goals.
“With the drilling data, we can produce a complete report on the bit’s directional tendencies, how it rotated, how it slid, and where we hit our performance goals before the bit has even left the hole,” he adds.
Internal process improvements and close collaboration can lead to fast iteration, Schliem says. “In some cases, I have seen bits go from being ideas to physical products on the rig within a week, and that kind of responsiveness is what drives us forward,” he illustrates.
Downhole Sensors
To understand, and ultimately mitigate, high-frequency torsional oscillations that accelerate BHA wear, many operators and downhole tool manufacturers are embedding shock and vibration sensors in the bit or mud motor, says Steve Jones, president and chief executive officer of Sanvean Technologies. “These embedded sensors let us sample shock and vibration data at a high frequency, revealing vibrations that reduce the performance and longevity of the BHA,” he explains.
“Historically, operators in North American onshore plays would get shock and vibration information from the measurement-while-drilling tool,” he acknowledges. “However, the MWD tool is not the best place to learn about the bit because the rubber in the mud motor’s power section isolates the MWD tool from the HFTO that occur as the drill bit cuts the rock.”
The sensors can detect HFTO because they record at 800 or 1,000 hertz, Jones describes. In many applications, they are embedded in the mud motor’s bit box to record HFTO and in the motor’s top sub to monitor mud motor back drive. “Back drive has become a major concern,” Jones comments. “Today’s mud motors put out a lot of torque, with some generating even more than the top drive, so the forces they send up the drill string can be significant.”
Since their introduction eight years ago, Jones says the embedded sensors have helped evaluate and refine bits and BHA configurations. Today, he indicates the sensors are tackling other challenges as well. For example, some companies use them to verify that automated processes are being performed correctly.
“When people think of automated drilling, they tend to imagine pushing a button and letting the rig go to work,” he says. “That may happen eventually, but drilling is so complicated that it is difficult to fully automate. Instead, automation is progressing one process at a time.”
So far, automation’s accomplishments include mitigating stick-slip and vibrations through soft torque systems, streamlining trips back to bottom and detecting when motors stall, Jones details. He says removing the reliance on manual input, and therefore the inevitable variability from person to person and day to day, is increasing consistency significantly, which will reduce unexpected nonproductive time and overall costs.
This mud motor from Turbo Drill Industries includes sensors from Sanvean Technologies that gather high-frequency data on drilling dynamics, as well as inclination and pseudo-gamma measurements. By using the measurement-while-drilling tool to send critical information to the surface in real time, Sanvean says the motor will help teams optimize drilling parameters and keep the bit in zone.
“During drilling, HFTO and mud motor back drive are the primary concerns,” he notes. “However, a rig spends significant time off bottom as well, and the vibrations that occur during those periods also influence how long the bit and power section last. With that in mind, operators and drilling contractors are using automation to control transitional operations.
“Once a stand of pipe has been drilled down, the automation system will pick up off bottom at a steady speed, move the necessary distance to make a connection, and then go to bottom to put weight on the bit,” Jones relates. “The operation looks almost identical every time.”
As such automation spreads and processes become more consistent, it will be easier to identify other factors that contribute to wear and damage on the drill bit, Jones says. “The more variables we can take out of the equation when we are analyzing downhole data, the more confident we can be in the message it’s sending,” he explains.
Dampening HFTO
Many operators are tapping the downhole sensors to compare tools for mitigating HFTO, Jones mentions. “Several companies are developing these tools because they help reduce the failure rate of rotary steerable systems,” he says. “HFTO can cause severe damage to the mechanical and electronic components of an RSS, so most BHAs with an RSS include an isolator below the motor to dampen torsional forces before they reach the RSS.”
Although tool designs vary, Jones says most perform the fundamental task of reducing HFTO’s severity. “Operators are trying to figure out which tools work best in different situations,” he says. “Although Sanvean is a business unit of Turbo Drill Industries, which makes a torsional dampener, we operate as an independent company. We are often called in to take measurements on other providers’ tools and give feedback on their performance.”
In general, Jones recommends looking for two characteristics in HFTO dampeners. “The first is a long stroke,” he says. “With a shorter stroke, the tool can bottom out and stop functioning if it encounters severe HFTO.”
Ideally, the tool also should be bidirectional. “Moving in both directions lets a tool dampen torsional forces during drilling, then shift to removing lateral vibrations when it’s off bottom,” he explains.
Jones points out that every TDI dampener includes embedded sensors. “Based on the data they record, TDI has made a few minor changes to the design to ensure it can operate in different environments,” he says. “The goal is to have one design that will work in every application, as that reduces costs.”
Real-Time Data
To move beyond recording data down hole and analyzing it after a run, Jones says Sanvean is working with TDI to embed sensors in the company’s compound angle motor. Through a clever geometry that allows it to deliver directional responsiveness in the curve but stability in the lateral, the motor is helping operators drill wells with fewer trips and BHAs, he reports.
In many applications, Jones says the compound angle motor can deliver performance akin to an RSS at a much lower cost. “By enabling the motor to send information on drilling dynamics at the bit in real time, we should be able to unlock even better performance,” he envisions.
This information includes shock and vibration data, Jones describes. He says getting detailed information from the motor’s rotor rather than the relatively isolated MWD tool will make a huge difference in challenging environments. “When we look at the data our sensors collect after a run, we frequently see information that may have eliminated the need to pull an assembly out of hole if it was available immediately,” he says.
To help with geosteering, the sensors can measure inclination. “Because the sensors are ahead of the MWD, the directional driller will have more time to make decisions about when to slide or rotate,” Jones comments.
“Along with inclination, we can take advantage of a correlation between high-frequency vibration and gamma ray readings in some types of rock, including shale carbonates, to produce pseudo-gamma measurements,” he adds. “Based on extensive testing in West Texas, those measurements should be quite accurate.”
For now, Jones says the inclination and gamma ray logs will be unnecessary in many unconventional plays. However, he suggests that may change as development continues and the space between laterals shrinks.
To get data to surface, the sensors use a transmitter in the rotor catch to share data with the MWD tool, Jones outlines. Because the sensors collect far more data than the MWD tool can send, transmission must be selective. “We are processing the data down hole to identify HFTO, mud motor back drive and other concerns that are impossible to see from the MWD, but that can restrict drilling performance,” he says.
“There have been motors in the past with on-board measurements, but they generally required complex equipment that imposed limits on the motor’s mechanical strength and power output,” Jones recalls. “In designing our tool, we used instruments that are small and reliable enough to get the right measurements without constraining the motor.”
After five years of testing and iteration, Jones says the intelligence-granting motor is almost ready. “The next step is going through customer validation,” he says. “We know we can get the data in real time, but we need to confirm that operators can use it to make better decisions during drilling. If all goes as we expect, they should see meaningful economic benefits.”
For other great articles about exploration, drilling, completions and production, subscribe to The American Oil & Gas Reporter and bookmark www.aogr.com.