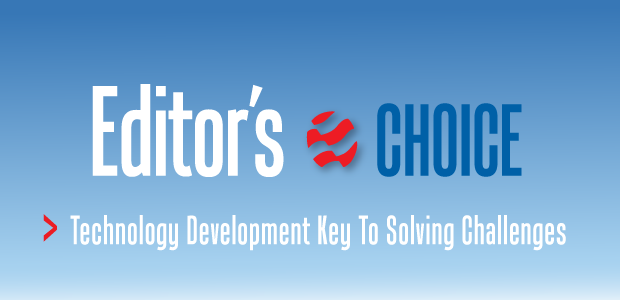
Technology Development Key To Creating Value, Solving Technical Challenges
By Tom Williams
HOUSTON–The ability to create value is what distinguishes the most successful participants in any market. In the oil and gas industry specifically, value creation is an incremental process that typically takes years to materialize and requires significant capital investment at multiple points, from leasing acreage and acquiring seismic data to drilling wells and installing production infrastructure.
The key to driving economic returns throughout the process–spanning the complete life cycle of an oil and gas asset (from discovery to enhanced recovery)–is leveraging technology at each decision point and in every discipline to reduce financial and operational risks.
Consider how much value the industry has created collectively over the past 10 years by applying technological advancements such as rich-azimuth 3-D seismic in deepwater fields, horizontal drilling and multistage completions in onshore resource plays, or carbon dioxide enhanced recovery in mature fields.
It is anyone’s guess what the next significant enabling technologies may be, but there is no doubt they will be applied by innovative companies to help find and develop reserves at lower cost with increased productivities, and enhanced safety and environmental performance.
Volatile product prices only reinforce technology’s powerful effect on the value creation equation for producers and operators. As painful as it has been, the downturn that began in late 2014 has been a reminder that oil and gas commodity prices do not change the need to develop new technologies. In fact, tighter operating margins necessitate deploying new tools and practices to improve efficiencies and reduce costs. Perhaps this explains why the number of oil- and gas-related patents increased in 2015 and 2016, according to the U.S. Patent & Trademark Office.
For a wide-angle perspective on oil and gas research and development in 2017, it is instructive to look to the results of a study the National Petroleum Council completed 10 years ago. The study found that it took 16 years on average for a technology to mature from the concept stage to commercialization.
The study went on to note that because of the declining investment of research-related funds from the federal government, the burden was shifting to the oil and gas industry to efficiently allocate research funds into worthwhile projects. The report encouraged Congress to increase government investments in R&D.
What has transpired since NPC issued that 2007 report is nothing short of remarkable. Research from industry and government did ramp up, the country benefited from increased production and reserves (namely in unconventional and deepwater plays), and the 16-year technology cycle was shortened as the industry embraced innovation.
Today, however, the R&D situation looks similar to 2007, with the same declining investment of research-related funds. What does that mean for technology development going forward and the industry’s ability to repeat the experience of the past decade?
Changing The Game
The technologies, practices and applications developed over the past decade have changed the game. Major drilling efficiency gains give operators the ability to evaluate, analyze and improve wellbore construction processes from spud to total depth. Horizontal sections of wells are being drilled longer, faster, better and cheaper almost by the day.
This illustration shows how multicomponent fiber optics-based seismic sensing technology and acoustic micro emitters can be applied in horizontal well developments for effective and accurate monitoring of unconventional oil and gas reservoirs. Image courtesy of Paulsson Inc.
High-resolution 3-D laser imaging provides comprehensive field surveys and detailed models of subsea assets to support a variety of life-of-field and asset integrity applications, including subsea inspection, maintenance, repair and operations. Images courtesy of 3D at Depth.
The U.S. Energy Information Administration says average U.S. horizontal well drilling costs now range from $1.8 million to $2.6 million a well. This has caused total onshore well construction costs versus completion costs to flip in a relatively short period, from 60-70 percent to 30-40 percent. That is, before the expansion of horizontal drilling in unconventional plays, the drilling component accounted for 60-70 percent of total well cost. Today, completion costs averaging between $2.9 million and $5.6 million a well account for 60-70 percent, with drilling representing 30-40 percent.
In deep water, EIA reports that drilling continues to comprise 60 percent of total well cost while completion activity makes up 40 percent. Even so, costs related to the rig (i.e., drilling and completion operations) account for 90-95 percent of total deepwater well costs.
Per well productivities also have increased at an astonishing pace. New-well oil production per rig jumped by 7.5 times in the Permian Basin between November 2013 and November 2016 (from 79 to 611 barrels a day) while new-well gas production per rig more than doubled in the Marcellus (from 6.038 to 12.290 million cubic feet a day) over the same three-year span, according to EIA data. In the Niobrara, per-well production per rig went from 317 bbl/d of oil and 995 Mcf/d of gas in November 2013 to 1,177 bbl/d and 3.794 MMcf/d, respectively, by November 2016.
As these numbers illustrate, each well drilled today is as productive as multiple wells drilled and completed only three years ago. Even with lateral lengths increasing to almost 7,000 feet on average, the industry has experienced a nearly threefold increase in daily footage drilled. This increased efficiency, in combination with optimized completion techniques, is leading to overall downward pressure on drilling costs, and is allowing far fewer rigs to drill much more productive wells.
Thanks largely to technological innovation, the industry was able to respond to the severe drop in oil prices in late 2014 in a rather remarkable way. In many onshore shale plays, operators have slashed break-even prices by half. In fairness, this was made possible in part by equipment and field service costs falling to levels that likely are not sustainable.
Higher demand typically drives up the costs of goods and services, which would impact break-even costs as commodity prices recover, reinforcing the need for R&D. Moreover, the dramatic decline in break-even costs in shale plays was not achieved to nearly the same level in deep water and conventional reservoirs, where additional R&D could provide added benefits.
Reduced drilling costs, competitive leasing pressures, and low commodity prices have contributed to increased numbers of drilled but uncompleted (DUC) wells. While there always is some inventory of DUCs, EIA estimated 4,117 uncompleted wells in the Bakken, Eagle Ford, Niobrara and Permian, and another 914 DUCs in the Marcellus, Utica and Haynesville as of the end of August.
Blowing down the DUC inventory to normal levels will add considerable new oil and gas production, especially considering the potential of increased production per well that will come from improvements in well completions.
Well refracturing treatments in shales and tight sands can improve reservoir access, restore production, and increase reserves recovery. This figure depicts improved conductivity and extension of existing fracture length by refracturing a vertical producing well to drain a new part of the reservoir.
Research is leading to major advances in identifying the most productive areas of a well to complete as well as in optimizing frac job design and implementation. Applying these advances to the DUC inventory, coupled with an estimated 6,000 wells a year in recompletions using these same advances, could generate notable increases in production while keeping the overall number of new wells relatively flat.
R&D Drivers
The advances in technology made over the past decade are paying off during a time of volatile commodity prices. In addition, the potential for additional drilling and completion activity is enhanced by the results of the 2016 election, and there is renewed optimism from the industry and investors for lower regulatory costs, improved land access, and greater tax stability. This also may change how the government views investments for increasing production.
Just as potentially significant is the Organization of Petroleum Exporting Countries’ agreement to cut production in concert with key non-OPEC nations. With global supply and demand already rebalancing, OPEC’s move reasserted the cartel’s historical commitment to managing oil production and controlling prices. It remains to be seen how successful the agreement will be in practice, but at the very least it signals a major departure from the strategy OPEC adopted in late 2014 to let the market dictate prices.
Change is again at hand, but the primary drivers of oil and gas R&D remain similar to what they were 10 years ago:
- Solving “grand challenges;”
- Gaining competitive advantages;
- Taking advantage of requests for proposal from outside funding;
- Responding at a corporate or industry-association level to political and public actions;
- Addressing major events;
- Addressing economic necessities; and
- Training the next generation.
While these seven drivers remain more or less constant, it is important to point out that the investment sources vary for each driver, and changing political, market and economic conditions can influence funding availability dramatically.
Mechanical slot cutting is a novel alternative concept for stimulating low-permeability reservoirs using a tensioned abrasive cable. The low-cost, environmentally friendly approach is scalable and designed to improve production and reserves recovery. Image courtesy of Carter Technologies.
Examples of solving grand challenges include “unlocking the source rock code” through horizontal drilling and multistage fracturing in onshore reservoirs, as well as the collaborative multidisciplinary research that allows the industry to drill and produce reservoirs 25,000 feet below the mud line in 10,000 feet of water. Much of what has become routine today scarcely could have been imagined 10-15 years ago, and the same will no doubt be said a decade from now.
As remarkable as these accomplishments are, equally amazing is how the industry has responded to events. Safety and environmental protection have improved, and there is more transparency in the way business is conducted. Industry participants have worked together to apply the adage that when identifying goals collaboratively, “what gets measured gets done, what gets identified gets dealt with.”
Consortia Framework
Investments from government co-funding contributed to both the shale revolution and deepwater development, ultimately allowing the United States to regain its role as one of the world’s leading oil and natural gas producers. Government-funded research should have a specified goal and be done when the same research would not be done through industry funding.
Government-funded research also should have potentially high rewards that benefit the nation, including safety and environmental protection. Increased domestic activity generates economic growth, which translates to jobs as well as federal, state and local tax revenues. It only makes sense that some percentage of these revenues is reinvested in R&D efforts to sustain activity.
The value of government co-funding of oil and gas research also can be documented by reviewing a recent Research Partnership to Secure Energy for America consortia report that highlights research that is contributing to several notable accomplishments both on- and offshore. The report documents the process of collaborative efforts in completing more than 150 projects through a consortium framework and the advantages over a traditional government-centric approach.
This process starts with industry experts working together to identify a research priority, issuing a request for proposals, providing a venue for teaming, then selecting and managing awards. Awards are made only when there is oversight by an advisory board and an end-user involved in the project.
These research priorities come from a well-defined and vetted list of challenges addressed by advancing technology. The program has brought various segments of the industry, universities, and government agencies together to create a common understanding on issues impacting oil and gas exploration and production.
This research model is an example of what can be accomplished through a government-funded consortium and of what conditions work best. The process speeds the road to commercialization. The not-for-profit objectivity, a policy of not owning intellectual property, and a broad membership base contribute to success.
Among the oil and gas industry’s broadest (and biggest) challenges is figuring out how to operate profitably during extended periods of low commodity prices while meeting safety and environmental performance requirements. The consortia R&D model is as relevant to solving this challenge as it was to making shale plays and ultradeepwater blocks economic and safe to develop. This model is a contrast to prior Department of Energy funding because it provides continuity to research funding and full engagement by end-users. This is a good thing.
The brilliance of the 2005 Energy Policy Act legislation, which has funded the past 10 years of RPSEA projects, is that funds were not appropriated, but instead came from royalties. Consequently, the program was not at the mercy of annual appropriations. The investments made to support the goal of enabling the development of solutions to onshore and offshore production challenges are now paying dividends.
Improving EURs And Safety
The program members’ technical experts have provided a long list of topics where government investments in R&D today could continue to pay high dividends. At the top of the list is improving recovery factors and safety performance, both of which are universal themes across all RPSEA programs.
The ultradeepwater program, for example, includes a study assessing needs and identifying concepts for improved recovery technology in two deepwater plays: the Paleogene and Neogene, in which a projected 81 percent of the combined 79 billion barrels of original oil in place remains untapped. Meanwhile, the small producer program includes a project that has identified a target of 135 billion barrels of potential production though CO2 EOR in the Permian Basin’s 12-county San Andres formation.
Some of the ultradeepwater R&D projects that address optimizing safety and/or recovery rates include improved seismic imaging for pressure prediction, mitigating annular pressure buildup, deepwater cementing with oil-based and synthetic muds, subsea chemical storage and injection, real-time riser integrity management, vortex induced motions and ocean currents, intelligent blowout preventers, subsea monitoring of produced water, high-voltage direct current connectors for subsea processing, conventional dry tree-based floating drilling and production systems, tanker offloading, “smart” cements and drilling muds, intelligent formation telemetry, deepwater coiled tubing drilling and intervention vessels, and high-resolution 3-D laser inspection using autonomous underwater vehicles.
Organizations leading these consortia efforts include Blade Energy Partners, CSI Technologies, Princeton University, Safe Marine Transfer, GE Global Research, Houston Offshore Engineering, Fugro, Society of Exploration Geophysicists’ Advanced Modeling Corporation, Clearview Subsea, Det Norske Veritas (USA), Stress Engineering Services, Remora Technology, University of Houston, Nautilus International, and Lockheed Martin. Many of these companies also partnered with academia and operators.
Shale Play R&D
The need to increase recovery efficiency is particularly pressing in unconventional plays, where recovery rates can be less than 15 percent for oil wells and 30 percent for gas wells. Some studies are focused directly on increasing EURs in resource plays through improvements in characterizing shale reservoirs, or through advancing the state of well completion/recompletion technologies, including advanced diagnostics and optimized frac designs.
While focused less directly on increasing EURs, some of the RPSEA R&D projects that generally support that long-term objective in shale plays include enhancing fracture connectivity and matrix porosity, remediating sustained casing pressure and other isolation breaches, characterizing and recycling flowback and produced water, improving zonal isolation in horizontal wells, geomechanical analysis of fractured reservoirs, and optimized stimulation treatment designs.
The backbone of the shale R&D program includes a strong environmental element where a variety of projects addresses air quality, water, seismicity, and land use.
Institutions engaged in these research projects include the Houston Advanced Research Center’s Environmentally Friendly Drilling Program, GSI Environmental, Colorado School of Mines, Colorado State University, Southern Research Institute, University of Southern California, Gas Technology Institute, Texas A&M University, Drexel University, Oklahoma State University, University of Texas at Austin, and the University of Oklahoma. These institutions are teamed with a variety of operators, universities and national labs.
Focused On Small Operators
Research addressing increased production and recovery from marginal and conventional wells ranks high. These resources have been somewhat lost in the shadows of the more high-profile shale and deepwater plays, but marginal wells collectively produce more oil than the United States imports annually from the Middle East. What is more, conventional and marginal wells provide access to twice as many oil reserves as the nation has produced to date.
Conventional and marginal fields are operated predominantly by independents, and often small independents. One of the challenges is that the companies operating these assets do not have the resources to conduct stand-alone R&D initiatives. This is where visionary leadership and investments could mesh academia, operators and service providers to have a major impact on this valuable resource, while also improving the environment.
The small producer program also addresses boosting EURs through enhanced and tertiary recovery. For instance, one project seeks to identify and develop technologies engineered to enable small producers to target residual oil zone fairways in the Permian Basin using CO2 EOR. Another study is researching next-generation CO2 flooding methods to recover more of the oil left after secondary recovery in Permian fields.
RPSEA small producer research projects include technologies such as hollow-fiber membrane nanofiltration for treating produced water, enhanced cement integrity, basin-scale produced water management for tight reservoirs, noninvasive ultrasonic technology for paraffin management in production tubing, conformance control, hybrid compression technology for multiphase and liquids-rich production streams, surfactant injection, and chemical EOR.
These small independent producer-focused R&D efforts are led by organizations such as Advanced Resources International, Melzer Consulting, New Mexico Institute of Mining & Technology, New Mexico Petroleum Recovery Research Center, Rice University, University of Texas of the Permian Basin, Battelle Memorial Institute, University of Missouri, and the University of Kansas.
Two other R&D focal points of note are developing and demonstrating new technologies that could increase the use of natural gas, and monetize stranded or underutilized natural gas resources. As is the case in on- and offshore safety performance technologies, the public is best served by having the industry work together with regulators and stakeholders in support of these solutions.
Looking forward, the industry will see similar changes as it did a decade ago. Despite the vocal critics, a changing attitude toward viewing fossil fuels as an asset rather than a liability will create opportunities for government and industry to work collaboratively to make prudent investments in new technology research. Together, we can take advantage of what we have learned over the past decade to ensure a safer, more productive and more profitable tomorrow.
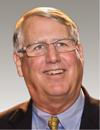
TOM WILLIAMS is president of the Research Partnership to Secure Energy for America. He has served as senior adviser to the Environmentally Friendly Drilling program, an organization he co-founded in 2005 while working as a vice president of technology at Noble Corporation. Williams has been in the energy business for 35 years as an operator as well in managing and commercializing new technologies. He held senior executive positions at the U.S. departments of Energy and Interior, and has served on a number of energy organizations, associations, and public and privately held corporations, including chairman of the Interstate Oil & Gas Compact Commission’s Energy, Environment, Research & Technology Committee, and the International Association of Drilling Contractors’ Drilling Engineering Association Board.
For other great articles about exploration, drilling, completions and production, subscribe to The American Oil & Gas Reporter and bookmark www.aogr.com.