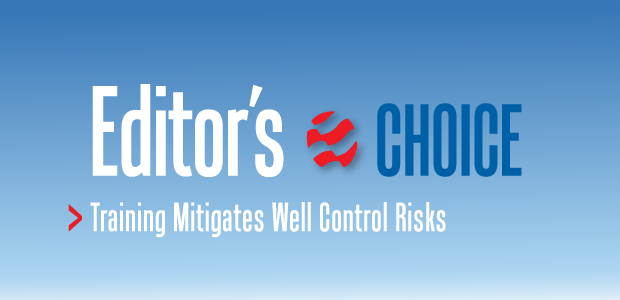
Training Mitigates Well Control Risks
By Steve L. Richert
HOUSTON–Mitigating risk is a key tool to properly manage today’s business. One definition of risk is “susceptibility to the chance of injury or loss.” Everyone in business must manage risk. From financial to safety, risk is one of the variables that can be controlled, or at least mitigated. From the chief executive in the corporate office to the floor hand on the rig, every employee can play an important part in risk management.
Universally, for oil or gas wells, risk management begins with the planning of a well and ends with plugging, abandonment and monitoring of the spent well. In the areas of rig crew training and well control, the main source of risk is the potential for uncontrolled release of hydrocarbons and other formation fluids to the surface. The highly explosive nature of methane gas means that an uncontrolled release to surface can cause an explosion and fire, which potentially could destroy life, property and the environment. If a rig crew is unable to properly anticipate the potential for a release, the entire drilling operation can be considered high risk.
Environmental and occupational risk management works to mitigate the possibility of uncontrolled hydrocarbon releases into the natural environment, which is crucial to avoiding long-lasting damage. The ability to manage risk has been clearly defined, taught, implemented and tested for many years. Unfortunately, the lack of commitment to implementing basic risk management principles–which include proper crew training–is still widespread.
The consequences of poorly implemented risk management programs are severe. Failures in any area of risk management very easily can destroy a company’s reputation and bottom line. As an industry, all personnel involved in the oil and gas operational structure–from the top to the bottom of the chain of command–must challenge any apathy they encounter toward environmental or occupational risk. We must continue to highlight the importance of addressing the full range of environmental risk factors and emphasize that it is inexcusable for human lives to be put at risk in the workplace.
Multifaceted Approach
On-location drills provide an assessment of all crew members’ well control response readiness. The introduction of mobile classrooms takes training to the rig site to reach those on the first line of well control defense: derrick hands, rig mechanics, floor hands, etc. Moreover, the mobile classrooms can work in combination with kick drills and assessments.
A decade ago, wells were drilled at a much slower pace, taking a month or longer from spud to total depth. With today’s drilling technology and practices, the same wells are being drilled in a week. Things are happening at an increasingly rapid rate on the rig. Today’s drilling crews need people who are trained, knowledgeable, skilled and regularly retrained to continually avoid the potential of a catastrophic blowout event.
The main drawback to traditional approaches to risk management is conformance to the status quo. The notion of “it is the way we’ve always done it” is a dangerous one. Each operation is unique. If proper individual operation risk analysis has not been accomplished and a reasonable risk management plan implemented, what always has worked before might fail, resulting in catastrophe.
Fortunately, more companies are realizing that not managing risk can result in severe financial loss that far exceeds the cost of implementing an engineered risk management plan and training personnel to carry it out. As a result, at least from the executive perspective, more effective risk management plans are being developed. The much bigger challenge, however, is ensuring that those plans are properly realized in field operations. A worrying gap continues to exist between executive memorandum/policy and how things are done in practice. This is where training, drills, exercises, and crew and equipment assessments have a beneficial role to play: What gets inspected gets done.
The most important aspect to consider when selecting a risk management program is the expertise of the consultant responsible for understanding the risks involved and how they can be managed. The consultant should have expertise solely in managing the risks of uncontrolled hydrocarbon releases, and demonstrable experience in training crews, writing risk management programs, implementing emergency response planning to blowouts and spills.
Many risk assessment companies provide risk analysis and risk plans. However, the key is taking the next step: implementing the risk management plan in the field where the work is done. Application of the designed risk plan finalizes the full circle of risk analysis, risk planning and risk management implementation. One of the key roles the risk assessment company should play is assisting operators and contractors in executing the plan to produce the desired results in the field, and conducting follow-up assessments.
A multifaceted approach to risk is needed. Rig site crew training is provided in well control schools as well as in mobile classrooms on the rigs for those who cannot attend the school sites. Emergency response plans are devised with assistance in rollout. Drills and exercises acquaint personnel with the plan. Well control equipment surveys check equipment condition and readiness. Kick drills and exercises test crew readiness. Well integrity and gas storage analysis is concentrated on field management equipment and tubulars transporting hydrocarbons. Other industry needs are addressed as new programs are developed.
Mobile training uses interactive simulations to review critical operational scenarios. The curriculum focuses only on what causes hydrocarbon influxes in a well, what equipment the rig crews need to maintain and function to control a well, how to recognize influxes, and how to shut in a well and capture the influx in a safe and efficient manner.
Team Process
Well control on the rig, combined with the office engineers, is a team process. Procedures should be developed and implemented with everyone in agreement. The rig crew must provide reliable data to supervisors and engineers so they can make informed decisions. Supervisors and engineers must communicate the process and procedures going forward in the operation. Obviously, supervisors, engineers and rig site personnel should have proper well control training and certification.
Consider a real-world example. A former student of an International Association of Drilling Contractors-certified WellSharp® training course placed a phone call to the Wild Well Control team. He was working as a mud logger on a rig, and since he was an engineer, the rig manager and company man had approached him for his advice. The rig crew was pulling pipe from the well and swabbed in a kick. This eventuality would not have been a problem in most cases if managed properly, but in this case, the pressure in the well was about to push the pipe out of the hole. Had this happened, the people, environment and equipment would have been at risk.
Two well control engineers experienced in pressure control issues were dispatched to the rig to assist the rig manager and company man in implementing a safe management plan for the risks involved. Because of his prior classroom exposure to risk training, this particular engineer understood that the rig crew’s plan was going to place them in a situation of greater risk. He also recognized that the risks involved were beyond his capability of managing or advising, and that mitigating those risks required the assistance of well control engineers experienced in dealing with similar well conditions. As a result, the situation was resolved safely.
The International Association of Drilling Contractors and the International Well Control Forum continue to build new curriculums such as managed pressure drilling to meet the industry’s needs. Several companies have developed ancillary courses covering issues such as ballooning, stuck pipe and well integrity.
The driving force behind the expansion of industry training courses is clear. Aside from the risks to human life, expensive equipment and damage to the environment, the risks of lost revenue and company reputation because of a catastrophic release of hydrocarbons into the atmosphere cannot be overstated.
In December 2016, the U.S. Occupational Safety & Health Administration issued enforcement guidance to inspectors concerning well control training and certification of that training. It is understood that an OSHA inspector potentially could fine a company if everyone on a rig site does not have well control training and documentation to prove attendance, such as a certification card.
Higher-Level Training
Because the science of well control never varies, but wells and the application of the science changes, courses should teach not only how to do well control, but how to think about well control (not just the “what,” but also the “why”). A good course will encourage students to go beyond memorizing facts into higher-level learning for higher-level thinking. Attention to the details of learning styles, which include visual, auditory and kinesthetic (hands-on), improves knowledge retention. Other lesser-known learning styles such as aural (music) and logical (critical thinking/discussion/debate) should be applied as well.
With the IADC WellSharp curriculum, the industry has enhanced the required knowledge content. WellSharp certification testing is much more rigorous in that the testing is centralized with IADC and the exams are proctored by a third-party provider. But a good training and certification program will expand the WellSharp curriculum beyond the required content.
For instance, the WellSharp drilling certification course requires 24 hours of class and three hours of testing. To accommodate needed extra training, Wild Well has increased the length of the certification from 24 hours to 36 hours. Several further training projects are being developed, including a Level 2 introductory online course. This 15-20 hour course meets the WellSharp introductory curriculum and is developed with 3-D software. This state-of-the-art course delivery will be both instructional and memorable so that students will remember what they learn.
Initially, rig crew training was provided at the rig. This has grown into crew kick drills/assessments whereby crew knowledge/skills gaps are noted and reported to employing companies; a risk assessment tool that continues today. However, it has become obvious that the rig crew, the first line of well control defense, is where training needs to be focused. The introduction of mobile classrooms is intended to accomplish that objective by reaching the often-untrained members of rig crews, and mobile training classrooms can work in combination with kick drills.
Mobile training brings the elementary parts of well control to the crew members who do not get the chance to attend well control school (the derrick hand, the rig mechanic and the floor hands). The training curriculum focuses only on what causes hydrocarbon influxes in a well, what equipment the rig crews maintain and function to control the well, how to recognize influxes around the rig without the computer equipment the supervisors have access to, and how to shut the well in and capture the influx in a safe and efficient manner.
Once the well is shut in, the supervisors and engineers can take over to safely resolve the situation. In a two-hour class, this mobile training solution instructs the very people who are the first to see an influx, and often the people who are the least trained to recognize and react to it. The crews are trained with their own team members on their own rigs so they can talk about how their teams manage kick detection and shut in. The ability to learn within the context of one’s own crew and rig setting lowers the risk of a blowout and the catastrophic results.
Risk mitigation is a crucial part of properly managing today’s business. Most companies realize the advantages to risk management, but do not have the tools to assess, write or properly implement a plan. In well control, risk management begins with training that teaches the “what” and the “why,” and emphasizes not only how to do, but also how to think. Training is not the only solution to risk management, and risk plan implementation and subsequent follow-up are imperative. Risk management involves identifying the risks, writing a plan that includes training, and being certain that executive policies/procedures are followed in the field.
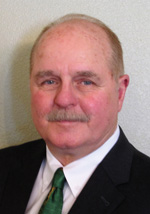
STEVE L. RICHERT is manager of instructor and course development at Wild Well Control in Houston, where he leads education and development for well control instructors, including knowledge progression, certification, and course and instructional materials development. He has 20 years of industry experience, coupled with a 20-year adult education background in the pedagogical study of human knowledge acquisition. Richert joined Wild Well Control in 2012 after previously serving as a driller at Ensign Energy Services, and as a financial specialist at U.S. Bank and TD Ameritrade. He studied mechanical engineering at the University of Oklahoma and holds a B.A. in history and philosophy from Grace University.
For other great articles about exploration, drilling, completions and production, subscribe to The American Oil & Gas Reporter and bookmark www.aogr.com.