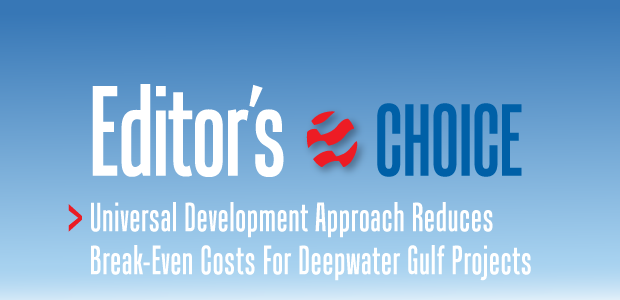
Universal Development Approach Reduces Break-Even Costs For Deepwater Gulf Projects
By Richard D’Souza, Shiladitya Basu and Sandeep Khurana
HOUSTON–The industry has reduced the average break-even costs for Gulf of Mexico deepwater field developments dramatically–from $70 a barrel in 2014 to $40-$50/bbl in 2017–making many projects economic. However, the challenge going forward is reducing costs on projects that require new floating platforms.
Between 2014 and mid-2018, only four such projects were sanctioned in the Gulf (Hess’ Stampede, Shell’s Appomattox and Vito, and BP’s Mad Dog Phase 2). To advance a greater number of projects with new host facilities to a final investment decision, the industry will have to drive break-even costs to the $30-$40/bbl range.
Operators are implementing numerous strategies to achieve additional cost efficiencies, including standardization, simplification, technology and unitization. Several independents active in the deepwater Gulf have leveraged aspects of these concepts successfully over the years, but in most cases, these strategies have been addressed at a component, rather than at a field development, level. Consistently reducing break-even costs requires a universal field development approach that entails using repeatable floating host platform and subsea building blocks for most field developments.
A universal field development solution has to accommodate a range of reservoir types, sizes and complexities, and must allow maximum flexibility for field layout, phased development and contracting options. In addition to reducing cost structures for deepwater Gulf projects with floating platforms, it also would reduce project delivery uncertainty by facilitating standardization and repeatability, thereby significantly improving discovery-to-first-oil cycle times while adapting to changing reservoir information during the development phases.
The three major “building blocks” of a field development are the host facility, subsea system and well systems (drilling and completion). The traditional approach to sanctioning Gulf projects has been to spend a considerable amount of time and resources on the front end to define and select a development plan that satisfies multiple commercial, technical and safety drivers.
However, deepwater development projects that have used standardized, repeatable designs have demonstrated clear economic and operational advantages, and many of the host facility and subsea technologies used on these projects have matured to the point of commoditization.
Wet Tree Host Facility
A key selection factor for a deepwater floating host platform is choosing a dry or wet tree system. Each offers distinct advantages and constraints. The decision must be made in the context of the overall development and must include the reservoir, recovery mechanism, well placement and design preferences, full-life reservoir management, impact on host facility and riser selections, etc.
Historically, a dry tree host platform with direct vertical access through an integrated drilling/intervention rig had advantages in lower well construction/intervention cost, reduced downtime and increased well recovery versus a wet tree host. However, advances in subsea technology, well construction methods, standardization, demand-based supply logistics, and reduced drilling rates have narrowed the spread significantly between wet and dry tree drilling costs.
Moreover, the reliability of subsea systems, seabed boosting technologies and rigless intervention have improved the competitiveness of wet tree systems for a range of deepwater applications, including those with high intervention requirements such as electric submersible pumps. In fact, as shown in Table 1, the vast majority of all deepwater Gulf field developments with a host platform that either have been sanctioned or advanced from select to define (FEED) phases since 2010 use wet tree hosts.
With a wet tree as the basis for a universal host platform, the next step is selecting the wet tree concept itself. The four proven wet tree host solutions that have been deployed in the Gulf are the tension leg platform; spar; semisubmersible; and floating production, storage and offloading vessel.
Selection criteria for a universal host capable of encompassing a majority of field development variables likely to be encountered in the deepwater Gulf include:
- Water depth range (3,000-10,000 feet);
- Payload range (10,000-40,000 plus tons);
- Flexibility for future expansion to compress cycle times and maximize recovery;
- Flexibility for redeployment;
- Topsides-to-hull integration and installation; and
- Engineering and fabrication contracting flexibility (fabricating the host platform typically represents 25-40 percent of total project CAPEX).
Table 2 provides a qualitative green/yellow traffic light matrix (a green light implies suitability and a yellow light significant constraints) for the deselection of the TLP and spar platforms as candidates for a universal wet tree host facility based on these criteria, narrowing the choice for a universal Gulf wet tree host platform to an FPSO or semisub.
The FPSO is the de facto universal host facility for all major deepwater producing regions except the U.S. Gulf, where only two of 53 installed platforms are FPSOs. The factors that have prevented a wider acceptance of FPSOs in the Gulf are the same reasons for deselecting an FPSO as a universal wet tree host candidate, namely the extensive pipeline network, limited availability of Jones Act-compliant shuttle tankers to transport the produced crude, and the need for a disconnectable turret mooring and riser system to enable sail-away of the FPSO in advance of an approaching hurricane.
Qualitatively assessing the various wet tree host platform candidates shows that the semisubmersible is the most versatile option that best satisfies requirements for a universal wet tree host facility. It also is reflective of current trends in the Gulf, where 12 of the 15 deepwater projects with a host platform that have been sanctioned or advanced to FEED since 2012 have been semisubs. These facilities are in water depths ranging from 4,000 to 7,000 feet and have topsides operating payloads from 10,000 to 50,000 tons.
Benefits Of Standardization
The industry has made great strides in reducing CAPEX requirements for deepwater developments by employing a standardization strategy for subsea, topsides equipment, hulls, moorings and risers. The vision is to streamline procurement by standardizing specifications for procured equipment, thereby realizing significant schedule and cost compression benefits. One study estimates standardization has the potential to improve the total value of deepwater projects by as much as 30 percent by reducing direct costs, project overruns and cycle times.
The JIP 33 Capital Project Complexity Initiative begun by a consortium of operators in 2015 sought to drive structural reduction in upstream project costs (including subsea trees) with a focus on noncompetitive collaboration and standardization. Preliminary estimates of the first phase indicate potential reductions of 10-20 percent in equipment capital expenditures, and 40 percent in schedule compression, and improved quality and reliability.
The industry can reduce CAPEX substantially by focusing on “re-base-lining” the scope and specifications for a field development’s host facility and subsea components. An example is Shell’s efforts to reset the base line used to develop future projects. Shell engaged third-party engineering companies to deliver “unconventional” designs of topsides, hulls and seabed systems to enable delivery of safe and affordable solutions for developing small, complex marginal reservoirs. The designs were calibrated with a minimum technical scope developed by Shell’s internal engineering team to meet all internal safety standards.
In addition to the minimum technical scope, a number of optional functionalities related to flow assurance, uptime and operational and field expansion flexibility were identified. A rigorous process was used to justify or reject each optional functionality and value enhancing ones retained and added to the minimum scope (Figure 1). This methodology of “zero-based design,” rigorous benchmarking, learning from those with simpler facilities, and using only value-added options has yielded dramatic capital cost reductions.
Semisubmersible Host
The four-column ring pontoon hull configuration is the universally accepted standard configuration for a semisubmersible production platform. This basic configuration is scaled up or down easily to match the payload and footprint of the topsides, the size of which is driven by the reservoir, production rates and subsea requirements. Major variants of this basic configuration are the tuning of the hull and riser system, and the type of deck structure.
In the past, a great deal of time and effort has been spent on recycling between the hull and riser system which has been, by default, a steel catenary riser (SCR). The acceptance of the steel lazy wave riser (SLWR) decouples the hull from the riser system. This allows for an intermediate-draft semisub as a “standard,” and the SLWR is tuned to the hull response. The SLWR has the advantages of superior strength and fatigue performance over an SCR for a wide range of water depths and metocean conditions.
The deck structure that supports the topsides and structurally connects the top of columns can be categorized as an integrated deck or a module support frame (MSF). An early decision regarding the type of deck structure must be made, since it drives hull global strength as well as topsides layout, design and integration. As a general guideline, a topsides that can be installed on the hull in a single lift (under 10,000 tons) is better suited as an integrated deck. Larger topsides requiring multiple heavy lifts are better suited as MSF decks.
It is important that an experienced semisub hull designer with a proven track record be used for hull and deck design. While a standardized hull configuration and its associated riser system is a major early decision, there are several second tier decisions regarding marine and mooring systems that can further improve overall life-cycle cost and performance. The important take-away is that standardization decisions for these elements should be made with a focus on ease of fabrication, simplicity, and operational safety and performance over the life of the field.
The cost and schedule benefits of the universal semisubmersible host platform can be amplified significantly by standardization. Standard and repeatable host platform designs lend themselves to standard and repeatable specification, procurement and contracting strategies as well as increasing confidence in project execution and on-time, on-budget delivery by minimizing rework and change orders.
Operators have adopted this philosophy successfully for various types of host platforms, including semisubs, to employ “a design one, build two (or many)” strategy. Examples are LLOG’s semisubmersibles deployed on the Who Dat and Delta House fields, and Anadarko’s Lucius and Heidelberg spars in the Gulf. Maximizing the cost, schedule and predictability of this approach requires:
- Maintaining as close to identical hull and topsides configurations as possible while adapting to individual reservoir variables;
- Ensuring continuity in leadership teams, design/fabrication/installation contractors, suppliers and management systems; and
- Providing a reasonable overlap between projects to enable continuity of key operator and contractor teams and a systematic transfer of lessons learned.
Reducing Break-Even Costs
To realize significant reductions in break-even costs, the industry has successfully implemented standardization and simplification strategies that have enabled the sanctioning of BP’s Mad Dog Phase 2 and Shell’s Appomattox and Vito projects. Each of these developments employs the universal field development concept of a subsea development tied to a semisubmersible host.
BP originally designed Mad Dog Phase 2 with a large wet tree spar dubbed Big Dog. With the estimated cost of the initial development plan exceeding $20 billion, BP began reviewing alternative field development options in 2013 to make the project more economical. Mad Dog 2 was sanctioned in late 2016, replacing the spar with a smaller semisub host facility.
BP achieved a 60 percent CAPEX reduction while producing the same resources by standardizing and simplifying the host facility, subsea systems and well construction. It also implemented advanced ocean-bottom seismic nodes and low-salinity water injection technologies to significantly improve reservoir imaging and recovery factors.
The selection of a semisubmersible host (a TLP and spar also were considered) was predicated on the excellent execution and operational performance of BP’s Atlantis semisub host platform. Repeatability of a successful design to provide greater certainty in project delivery and operability factored into the decision. BP worked collaboratively with key engineering suppliers and contractors to simplify the host facility (topsides and hull) and subsea systems without sacrificing safety, availability or flexibility for expansion. Project-sanction-to-first-oil cycle time is about four years.
Appomattox is located in 7,200 feet of water. Shell sanctioned the project in July 2015, selecting a wet tree semisub host based on a combination of water depth, ability to support large topsides, prior experience with Nakika, and flexibility for future expansion.
The topsides weight is in excess of 40,000 tons and the subsea system features six drill centers, 15 producing wells and five water injection wells. Shell was able to reduce capital costs by 20 percent prior to sanctioning and another 20 percent post-sanctioning by rationalizing and simplifying scope and specifications of the host facility, subsea systems and well construction.
Shell sanctioned the Vito four-block project in 4,000 feet of water earlier this year after redesigning the original development concept using a simplified semisubmersible host design and subsea infrastructure, ultimately reducing cost estimates by more than 70 percent from the original concept.
Base Case Development
As a hypothetical base case for the proposed universal field development solution, an ultradeepwater development in 7,000 feet of water with 200 million barrels of recoverable reserves from a Lower Miocene or Paleogene formation at a drilling depth of 31,000-34,000 feet was analyzed. The field development plan consists of a wet tree semisub host and subsea development, as shown in Figure 2.
The production facility is designed for light, sweet oil with processing capacity of 80,000 barrels a day of crude oil and 40 million cubic feet a day of gas. Space is provided for future water injection equipment. The subsea design consists of 12 production wells to drain the recoverable resource over 15 years.
Break-even analysis was conducted with a 10 percent discount rate and a Gulf fiscal regime of 12.5 percent royalty and 34 percent tax on profits. The analysis accounts for cost efficiencies realized through 2017, resulting in a break-even cost of $42 a barrel of oil equivalent. The additional cost and schedule gains from the repeatability, standardization and simplification of the universal field development solution reduce cycle time from the select phase to first oil by one year, and reduce CAPEX of the host facility and subsea system by 20 percent. The analysis shows a $5/boe break-even reduction to $37/boe (Figure 3).
Moreover, by fully leveraging the standardized and simplified universal approach, additional opportunities for operating and drilling cost reductions can drive break-even cost below $35/boe to help make deepwater Gulf projects competitive with shallow offshore and even onshore shale projects.
Richard D’Souza is a former managing director and currently a consultant at Granherne, a KBR company. D’Souza was a principal at Omega Marine Engineering Systems, which designed the first floating production unit in the Gulf of Mexico: a converted drilling semisubmersible. He and his teams have since been involved in designing a number of frontier deepwater platforms, including the Diana Hoover spar and the semisubmersible production systems at Thunder Horse, Jack/St. Malo, and most recently, Mad Dog Phase 2. D’Souza has a bachelor’s from the Indian Institute of Technology, Kharagpur, and an M.S. from the University of Michigan.
Shiladitya Basu is a technical adviser at Granherne, a KBR company. With 10 years of experience focused on deepwater developments, he has worked with both majors and independents in designing and analyzing floating, fixed and subsea marine structures. He holds a bachelor’s from the Indian Institute of Technology, Kharagpur, and a Ph.D. from the University of Michigan.
Sandeep Khurana is a principal project manager at Granherne, a KBR company. He began his career in 2000 as a principal engineer at Granherne, and subsequently served as project manager for Kerr McGee/Anadarko at Wood Group/JP Kenny, as offshore and international subsea and facilities adviser for Devon Energy, and as manager of major projects development planning at Noble Energy before rejoining Granherne in 2014. He holds a master’s from Rice University.
For other great articles about exploration, drilling, completions and production, subscribe to The American Oil & Gas Reporter and bookmark www.aogr.com.