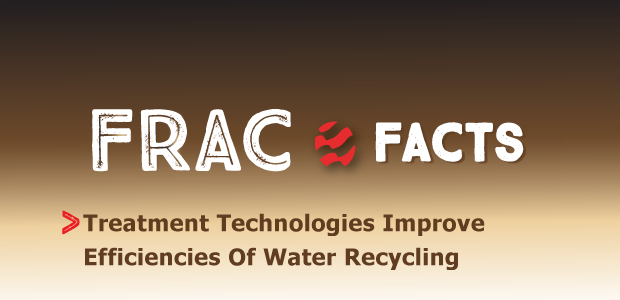
Treatment Technologies Improve Efficiencies Of Water Recycling
Editor’s Note: Standing alongside a dusty lease road looking out across an arid landscape that envelops the horizon in all four directions, it can be hard to believe West Texas and Southeast New Mexico once were covered by a great inland sea. Water was everywhere in the Permian Basin 250 million years ago.
Today, water is again prevalent all across the surface of the basin, but now it is contained within an almost countless number of temporary ponds, pits and holding tanks. Consequently, water management has become big business in the Permian and other U.S. basins. By IHS Markit’s calculations, water management represented a $12.2 billion market in the Permian last year, and is forecast to reach more than $22 billion by 2023.
Many of the millions of barrels of water pumped down hole while fracturing a single horizontal well flow back during production along with formation water, giving operators the opportunity to capture, treat and reuse that water to stimulate the next well. Where is the industry today on the produced water recycling learning curve? How are advanced technological solutions being deployed to cost-effectively treat water on site? What are the primary challenges going forward for water management?
To find out, AOGR presented a series of questions to a panel of water management technology and service experts. Panelists are Mark Wolf, director of onshore facilities at National Oilwell Varco; Dean Fanguy, director of business development, Western Hemisphere at TETRA Technologies; Mark Patton, president of Hydrozonix; and Alex Gonzalez, director of operations at De Nora Neptune.
Questions are in italics, followed by the panelists’ responses.
ENSURING SAFETY
Mark Wolf is director of onshore facilities at National Oilwell Varco. Before joining NOV, he served as president of Merpro Americas, vice president and general manager of U.S. Filter, an applications engineer at Serck Baker, and an operations engineer at ExxonMobil. Wolf is a member of the Society of Petroleum Engineers’ Distinguished Lecturer Committee and the Projects, Facilities and Construction Technical Advisory Committee. He holds a B.S. in petroleum engineering from Texas Tech University |
![]() |
MARK WOLF |
Q: NOV’s water services group offers water handling, storage and transfer services, and treatment options. How can water management practices ensure safety in water handling, treating and disposal? How do they reduce exposure and ensure optimal transfer, storage, reuse and disposal?
WOLF: Water management practices that can influence safety are going to be design- and behavior-based to minimize potential for exposure and unintended release. While water may appear benign, produced water and oil field brines are corrosive and can cause significant environmental impacts in the event of an unintended spill or release. To that end, inherent process design can be used to create systems that are self-contained and can operate with a minimal amount of operator intervention or exposure. As an example, our saltwater disposal (SWD) facility designs make use of Moyno™ offload pumps at the front end. This design allows for rapid offload of trucks and minimizes the exposure and lack of containment that occurs with facilities that gravity drain trucks into open receiving pits. This design eliminates operator exposure to brine, hydrocarbon vapors and potentially dangerous gases such as hydrogen sulfide.
The potential for spills and release is further minimized as greater volumes of oil field brine are transported via pipeline to SWD facilities, rather than by truck. From the offload pumps, the water moves to a horizontal gun barrel (HGB) to separate and recover entrained oil. Many conventional SWD facilities move the water first to a desand tank where suspended solids settle and collect. This invariably results in added maintenance, decreased retention time, and diminished oil separation as the solids accumulate in the desand tank, and eventually expensive and laborious manual removal of the accumulated sediments will be required.
By contrast, the HGB design makes use of an internal system for on line vessel desanding. This allows automated and essentially continuous removal of solids from the facility, eliminating associated downtime for clean-out and minimizing potential personnel and environmental exposure to brine, oil and solids. NOV’s Easy Skim™ technology allows operators to skim recovered oil from water tanks without the potential for tank overflow that is a possibility with conventional skimming designs. Additionally, we incorporate fiberglass piping throughout the SWD facility to eliminate the potential for corrosion and loss of containment that might occur with other pipe types in corrosive water service.
NOV’s digitalization of SWD and other assets provides online monitoring of tank levels, system dynamics, and continuous monitoring of oil-in-water concentrations within the facility. The digitalization provides the potential for continuous remote monitoring and also eliminates the need for operators to grab process samples, thief samples from tanks, or otherwise create the potential for exposure to process water and its contaminants or risk spills and releases. Digitalization allows operators to more intelligently operate their facilities and minimize the potential for process upsets ensuring process safety and optimal transfer.
Optimal water management also can address not only personal and environmental safety, but also asset safety. We provide seawater treatment systems for seawater injection on offshore assets. Proper operation of seawater injection systems is critical to prevent system corrosion caused by oxygen and provide sulfate removal to eliminate formation fouling that may impair production and well life. As mentioned earlier, intelligent design and incorporation of fiberglass flowlines can minimize platform weight, which is at a premium, and also can assure asset integrity in harsh, corrosive service offshore.
Our seawater package digitalization efforts, as presented by NOV’s Austin Wilcox, Rene Mikkelsen and Pei Ling Esther Lian at the 2019 Offshore Technology Conference (OTC 29567), also have optimized system maintenance and membrane cleaning cycles to extend membrane life and identify fouling mechanisms. This enhances the safety of the overall asset, including both the platform and the reservoir.
Q: What technologies can be employed to provide better visibility into water availability throughout the life cycle? How do these technologies improve understanding, safety and efficiency? Where are the primary challenges in the water life cycle?
WOLF: Visibility to water availability and quality are achieved through digitalization of the water assets and infrastructure. There are third-party providers of water and disposal availability data that provide better visibility to resource availability on a market or regional level. At the asset level, our GoConnect™ digital platform provides an avenue to tie together system monitoring and to pair that with artificial intelligence and adaptive machine learning to optimize water and other production assets throughout the production chain. OilWatcher™ monitors provide real-time, continuous monitoring of oil-in-water in the produced water chain and can be used to monitor water quality and better manage water operations.
OilWatcher data can be accessed remotely via the GoConnect platform and can be tied into operational control as well. Traditional oil-in-water monitors have been prohibitively expensive to widely employ, resulting in many operators guessing at operating conditions, or taking periodic spot samples, which often led to inaccurate assessments of water quality and operational effectiveness. OilWatcher’s innovative design was created to dramatically reduce the cost of oil-in-water monitoring, thereby making it cost-effective to get real-time operating data on water quality throughout the water management cycle or across multiple assets.
The great challenge in closing the water cycle is matching water demand with water availability and making sure that the available volume also meets the required water quality specifications of the demand. Often there is plenty of water, but it is not available at the required water quality for industrial reuse or beneficial discharge. It is where these dislocations of available water at the appropriate quality occur that opportunity exists. Providers of water treatment equipment who also possess the capability to integrate equipment within a larger process solution, or deliver turnkey engineered water treatment solutions offer the greatest value in bridging the gap between water availability with water demand. We can deliver integrated water treatment process solutions as needed to efficiently provide water at the required quality for reuse, injection or discharge.
Q: How do offshore and onshore water treatment challenges and solutions differ? Does the treatment flow rate keep up with completion flowback? How can technologies help meet differing requirements on- and offshore?
WOLF: All offshore water handling system designs are governed by space and weight constraints. Water is very heavy, so it is critical to minimize the volume of retained water. This means very few tanks and prolific use of complex vessel internals and dynamic separation systems such as hydrocyclones, floatation cells and coalescing media. Offshore water treatment systems have to treat the water as it is produced, and must meet strict environmental standards for discharging to the ocean. Since offshore facilities cannot utilize storage tanks for upset conditions, the systems have to be very reliable, provide continuous operation, and require minimal manpower. Offshore water treatment systems tend to have much higher capital costs for systems that are designed to operate for decades.
Depending on location, onshore facilities can make extensive use of tank or pit storage, which gives the operators some relief when things are not working quite the way they should. The transient nature of completion flowback with high short-term volumes that constantly change location adds a unique challenge to designing for unconventional production. Water handling facilities in onshore shale plays tend to be lower capital cost per barrel of water treated, are designed for much shorter expected operating lives, and can have higher operating costs in the form of manpower and consumables. Transportation can be a major cost component in unconventional plays and has contributed to the rise of the water midstream industry with extensive networks of pipelines, truck fleets, and distributed recycling and disposal facilities.
Q: What are your thoughts on the economics of treating produced water for reuse? In water-scarce regions such as the Permian Basin, operators are sourcing water from natural brine formations. What are the treatment challenges for these brines? Do you see the use of municipal treated waste water increasing? The idea even has been suggested to pipe water into the Permian from the Gulf of Mexico. Could that become practical one day?
WOLF: Recycling produced and flowback water for completions makes great economic sense. When water is produced and consumed in the same vicinity, transportation and disposal costs go way down, and the cost of treatment to meet reuse standards is very reasonable. The growing network of saltwater pipelines is making it more practical to centralize recycling facilities that can serve a wider area and have a longer useful life.
Selecting a water source for any industrial activity is always a balance between the cost of treatment and the cost of transportation. You can spend less to source a high-quality water that needs little treatment, but excessive transportation cost will swing the economic balance to more expensive systems to treat local water to lower the overall cost. In water-scarce regions, the social costs of diverting high-quality water sources from more traditional uses will have a strong impact on issues such as license to operate and public relations.
Brackish groundwater sources historically have been a good source of completion fluids, but are now being viewed as a potential substitute for freshwater in some water-stressed regions. As brackish desalination capacity grows, industrial consumers will feel pressure to reduce use of this source. I think transporting water from the Gulf to West Texas is a nonstarter. Water flows downhill, and most of West Texas sits above 2,500 feet elevation. The economics of pumping or hauling seawater out west just will not pencil out.
OPTIMIZING QUALITY
Mark Patton is president of Hydrozonix LLC. He joined the company in 2012 as an applications engineer after serving for 14 years as vice president at American Remedial Technologies and seven years as a program manager at Waste Management Inc. Patton holds a B.S. in chemical engineering from the University of Southern California. |
![]() |
MARK PATTON |
Q: What are the major challenges for water quality management going forward? How do different sources affect quality? What techniques are required for blending fresh and treated water for completions using cross-linked gels as opposed to slickwater?
PATTON: The biggest challenge will be managing the effects of induced seismicity on disposal well capacity in the Delaware Basin. The Delaware already produces a significant amount of produced water and any disposal well restrictions will strain capacity concerns that already exist. In terms of the produced water quality, one typically sees changes in chloride levels, iron, bacteria and sulfides from different sources. In itself, this is not a challenge, but designing systems to account for these changes is critical. Most systems are designed assuming a steady state, but with produced water, a steady state doesn’t exist, so variability has to be accounted for in a system design.
As for cross-linked gel chemistries, these gels have a higher sensitivity to chloride levels, so special attention has to go into maintaining a consistent blend. We patented a process using real-time monitoring and water chemistry testing to maintain a blend for a stable, consistent fluid. The other challenge is that boron in produced water can cause premature cross-linking. Borates typically are added to a cross-linked gel system to create a delayed cross-linking, which basically means the gel will thicken once the fluid is moving down hole. Boron in produced water can cause this thickening to happen immediately, making it very difficult or even impossible to pump down hole. So part of automated blending has to include boron testing in real time. Boron inhibitors can be added to prevent boron from causing premature cross-linking, but one must know how much boron is present to inhibit its effect.
Also, it is common for working tanks during a frac job to be contaminated or source water to see bacterial growth if not aerated. One common way to prevent this is to recirculate water between stages of a frac to clean working tanks or prevent bacterial growth in the source water storage system. Of course, even better is to include aeration in the storage system.
Q: How can produced water treatment be standardized across an operation rather than applying a customized approach for each site? When is customization necessary? How can operators reduce treatment costs through greater use of standard practices?
PATTON: Even with variability in produced water quality, standardization is very possible and necessary. Rather than relying on a service provider to define the produced water reuse specification, the operator should take control over its program and develop quality needs internally. By developing a produced water reuse specification, the operator can standardize a system around those needs and reduce cost by not overtreating or overdesigning a system.
In simple terms, bacteria and iron control will be needed. If sulfides are present, then that should be included as part of the program. Total dissolved solids (TDS) are controlled by blending and are less important in slickwater systems. Total suspended solids (TSS) and oil content can be managed using the operator’s own traditional tank batteries and gun barrel systems, so there is no need to move beyond those systems. Smaller pits or weir-type tanks can be used to settle solids.
Customization is often a result of poor planning. Proactive management should allow standardization and prevent too much customization. That being said, things change. Operators have to be prepared to change their systems as water quality changes. Some of this can be handled in a standardized operation, but sometimes there are unexpected events that require a custom solution. For example, we have had to employ customization when we have seen spikes in water quality. The best way to handle this is to allow for expansion to aeration of treatment systems to address the spikes.
Q: What contaminants present the biggest challenge for operators? Bacteria? Iron? Sulfide? Boron? TSS/TDS? How can different technologies be leveraged to address them?
PATTON: With the prevalence of slickwater systems, TDS and boron become nonissues, and bacteria and iron become the most important, but not necessarily challenging. Sulfides can be less prevalent, but are the most challenging. In lower concentrations (<10 parts per million), a standard oxidation approach works best. In higher concentrations, air stripping can be the most cost-effective. There also are hybrid solutions that use both oxidation and stripping. The challenge is to find the sweet spot between these approaches to keep costs low.
TSS and turbidity can be challenging based on the goal, but we have found TSS and turbidity to be mostly misunderstood. Most TSS can be settled and turbidity is really unnecessary. We have done plenty of core flow and proppant conductivity tests, and although they support lower turbidity and TSS, most people forget that there will be dust loading after treatment–especially in West Texas–and proppant fines when the proppant is added. These sources of TSS and turbidity create a very high baseline and make using aggressive TSS and turbidity goals overkill. We have seen systems that have been in place for longer than a year using only gravity settling for TSS control and they are creating a perfectly suitable recycled produced water at rates up to 40,000 bbl/d.
In terms of specific technologies, we recommend aeration in the storage phase. We also like using aeration as a pretreatment step if there is an available location. This is the best way to reduce overall cost. We also like to utilize our fully automated ozone systems. They reduce the cost of oxidation, and as a liquid chemical alternative, there is no liquid chemical storage required, which reduces cost and improves safety.
As the scale of operations has increased, storage requirements and the demand for higher blends of produced oxidant for on-the-fly systems also have increased. High oxidizer concentrations can create compatibility problems with friction reducers and gels. With the addition of aeration and pretreatment systems, oxidant demand for on-the-fly systems has decreased, making it easier to employ without compatibility problems.
Q: What is the best way for operators to select technologies and best practice for their projects? What are your thoughts on alternative sources such as natural brine reservoirs and municipal wastewaters? How do the economics of treating and recycling produced water compare with these alternative supply sources?
PATTON: The first step is to develop a realistic specification for the produced water stream. Then, the use of full-scale pilots always helps verify field performance. Last, a good water quality test program is needed to validate results.
Natural brines have become a great alternative to freshwater, and we are finding that most operators are replacing freshwater with more brackish sources. Most of the larger municipal wastewater sources in the Permian have been contracted. There are still some smaller municipalities that can be contracted with, but many of these discussions are already ongoing.
However, as operators develop more produced water recycling programs, it likely will reduce the demand for alternate sources, making it difficult to consider significant long-term investments in them knowing they ultimately may get replaced by treated produced water. But with water recycling slowly transitioning into full-scale operations, alternate sources are still needed to bridge the development to more recycling.
The cost of recycling using a typical service company model ranges between $0.20 and $0.30/bbl. A company-owned model, where the operator buys the equipment and we use our own automated ozone systems, has developed programs at a cost below $0.10/bbl. We have more than 600,000 bbl/d of installed capacity in the Permian today, and our experience shows that the savings from minimizing hauling and disposal offset treatment costs, and then some. In fact, it reduces the overall cost. Operators not only are recycling produced water at a lower cost than disposal, but they also are eliminating the need for that equivalent volume in freshwater or brackish water.
CLOSING THE LOOP
Dean Fanguy is director of business development, Western Hemisphere, at TETRA Technologies Inc. Before joining the company in 2013 as director of North American sales, he was director of sales for U.S. operations at Tervita. Prior to that, Fanguy had worked for 32 years in business development and product line management positions at Baker Hughes, a GE company. |
![]() |
DEAN FANGUY |
Q: How does closed-loop water management improve economics for oil and gas operators? How much of the process can be automated? How can operators plan and manage their project needs?
FANGUY: A closed-loop water management system provides greater simplicity and control over blending and fluid quality because it lends itself to more seamless integration and computer-controlled automation.
In terms of the economics, the dramatic increase in unconventional shale development means operators now are confronted with higher water management costs and more environmental and operational risks than ever before. The challenges are sourcing freshwater and incurring higher volumes of produced water and sand flowback. Scaling up services to meet these challenges and trucking produced water from the well fracturing site to another site for disposal further compounds the cost and exposure to risk.
We address these challenges with our closed-loop solution to provide the lowest-cost-per-barrel water management solution. Using this solution, we can fully integrate and automate every step in the process, from water transfer to desanding, treatment and recycling, blending, storage, and distribution.
This approach yields several benefits, including more efficient job planning, reduced personnel costs (often as much as 30 percent), greater transparency of the process, enhanced quality control, and reduced risk of safety and environmental incidents. Additionally, the TETRA solution is scalable, allows for remote monitoring and control of water management, and provides valuable data for planning.
Q: What sourcing challenges will operators face as they focus on full-field development in existing core areas of resource plays and extend development into new areas and even new basins? How can they better manage the supply for just-in-time use when using multiple sources, including treated and recycled water?
FANGUY: If operators continue development in the same manner, increased activity in and around existing shale basins or in new basins will present three logistical challenges: trucking high volumes of freshwater to job sites, trucking produced water from job sites to other sites for disposal, and coordinating these two phases of transportation so they are properly timed and consistently reliable. The problem is that increased truck traffic increases both operational costs and the potential for incidents, and few communities actually welcome more trucks on their roads.
The solution is to recycle more of the produced water on the fly to reduce the volumes of freshwater needed for an optimal frac fluid, integrate the steps of the water management process for more efficiency, and automate these steps for greater control and better allocation of personnel.
Our closed-loop water management solution addresses these needs. Automated water recycling systems can process different types of produced water on the fly, with blending and treatment technologies that eliminate bacteria, sulfides and other suspended solids, and can ensure a consistently high-quality frac fluid throughout completion operations.
Q: What kinds of technologies do you see being used to deliver supplies of water from multiple sources with varying qualities and constituencies? How can technology be leveraged at every step in the process to optimize water quality regardless of source for consistent frac fluid performance?
FANGUY: We have developed a number of innovative technologies to address the challenges of recycling diverse types of water, from produced to brackish waters and flowback with sand. First, our Oil Recovery after Production Technology (ORAPT™) separation units pretreat produced water prior to recycling and recover residual hydrocarbons, which are then returned to the operator for sale to the market. The SwiftWater Automated Treatment (SWAT™) system chemically treats produced water and provides accurate ongoing chemical dosage to ensure the water is treated to exact specifications. Its web-based, real-time monitoring and control gives operators on-demand access to treatment and recycling operations 24 hours a day, with a transparent view of the chemistry and its efficacy.
Our on-the-fly water treatment system for both produced and freshwater contains EPA-approved biocides to prevent or eliminate 100 percent of the bacteria and remove sulfides prior to fracturing. The system uses the flow of water in the transfer line to generate the biocides and automatically stops when flow is interrupted to ensure a safe work environment. The automated blending solution can treat diverse types of water with an automated blending controller and a patented, on-the-fly blending manifold. The system measures input and outbound fluid conductivity and automatically adjusts flow rates in real time to achieve the specified blend, thereby minimizing variation in frac fluid quality while maximizing the use of produced water.
TETRA Steel™ double-jacket, flexible lay-flat hose and patented Rapid Deployment and Retrieval Vehicles are revolutionizing onsite water transfer. The hose includes zero-discharge couplings and allows for higher operating pressures than a single-jacket hose. These products improve operational efficiency, reduce risk to the environment and to personnel, and lessen the impact on landowner properties.
Finally, our Automated Distribution Manifold (ADM) facilitates more efficient and predictable management of frac water buffer volumes in real time, with computer control of tank levels to ensure a steady supply of frac fluid while preventing tank overflow. It can independently control and monitor up to 10 frac tanks, and it can be configured for varying output levels depending on operational needs, reducing the uncertainty of water provision and helping to ensure continuous operation. Additional ADM systems can be linked to manage more frac tanks seamlessly.
Q: With per-well fluid and proppant volumes continuing to climb, how do you see water supply challenges shaping up going forward? Will more water come from alternative sources such as brine reservoirs? Will greater volumes of produced and flowback water be treated and reused in fracturing?
FANGUY: The demand for water will grow exponentially over the next few decades, so formations with brine and nonpotable water may indeed become more integral to unconventional strategies. Down the road, municipal wastewater might be another source as well. Obviously, the more dissolved solids and other impurities in the sourced water, the more it will have to be treated. Capturing and treating such waters must be cost-effective.
Treating and reusing produced water at the frac site is very economical. In fact, it is a win-win for operators. The more produced water they can use, the less freshwater they will need to source, and the less produced water they will need to then haul and dispose of. That reduces both costs and risks, and makes operations more efficient. Where the water management solution recovers residual hydrocarbons that can be sold, the captured product actually can offset the cost of the water system.
TREATING ON THE FLY
Alex Gonzalez is director of operations at De Nora Neptune. Before Neptune Enterprises was acquired by De Nora in April, Gonzalez served for five years as the company’s president. He previously served in executive roles at BioCatters LLC, River Bend and Bosque Systems. He holds a degree in management from Texas A&M University. |
![]() |
Alex Gonzalez |
Q: On April 1, De Nora announced its acquisition of a majority interest in Neptune Enterprises, forming De Nora Neptune LLC. How do the two companies’ technology and service offerings complement each other, and what do the combined capabilities look like?
GONZALEZ: Neptune has specialized in on-the-fly frac water treatment and cost-effective produced water recycling services, and De Nora is a leader in on-the-fly water disinfection and treatment technologies. The Neptune acquisition allows De Nora to begin indirectly offering our technologies by directly servicing operators in the Permian Basin and beyond. De Nora Neptune is now providing more than just the technology; it is delivering that technology as a service. It also allows De Nora to provide high levels of on-the-ground support and service 24/7 to existing technology customers, giving them seamless operation, maintenance and support to meet operators’ demand for safe solutions that save money on every barrel.
Our focus is on cost-effective frac water disinfection and produced water recycling using on-the-fly treatment solutions that give operators the mobility and flexibility they need in shale plays. The industry primarily is using oxidants as the primary source of disinfection. When used properly, oxidants are extremely effective at killing bacteria, but oil and gas operators struggle with the safety and cost of using most oxidants. Our mobile treatment unit (MTU) is a unique, field-ready, onsite sodium hypochlorite generation system that offers oxidant at the lowest cost, generating no hazardous chemicals, and requiring no hazardous precursor chemicals to be transported to a site. This intrinsically makes it the safest approach available.
De Nora Neptune also provides low-cost recycle solutions for produced water sites. Utilizing operators’ existing infrastructure, we recycle produced water on-the-fly for fracturing and for safely storing large quantities in recycled water pits. Recycled produced water allows operators to reduce, and in some cases, even replace the need for freshwater in their well fracturing operations.
Mobile on-the-fly treatment capability is important for both operators and service companies, because they operate in a world where the sweet spot moves, and some of the most productive wells can be tens of miles from infrastructure. As a result, providing them with the ability to easily and safely disinfect their fractures, or recycle produced water using only the tanks and infrastructure they already have in place, saves time and money while maximizing operational flexibility.
Q: Why are on site services valuable to some operators? How do these services reduce sourcing issues and conserve freshwater resources? How do you characterize the economics associated with treating water on site for reuse?
GONZALEZ: A shale well could be characterized as a water well that produces some oil and gas. On average, three-seven barrels of water are produced for every barrel of oil. Turning that water back into frac fluids reduces the freshwater drawdown, lowering operators’ costs and reducing the drawdown on the aquifer. On site services give operators the security of knowing that a total solution is available if needed, anywhere that they need it. Operators have chosen turnkey solutions with De Nora Neptune to recycle their produced water, store the water, blend it with freshwater, and then disinfect at the frac job site. Others have purchased our technology and have had us train their employees on using the equipment. Economically, there is no better choice.
The economics vary depending on the required output specification, which is set by the operators’ completions teams and completion chemical use. At this point, most geophysicists agree that for completions, the water should be as close as possible to the water already in the formation (the produced water). When using an approach that generates a clean brine (only the TSS and iron are removed), the water can be less than 10% of the cost of using freshwater, with hauling costs the same as freshwater. As freshwater becomes scarcer in the Permian Basin and other regions, prices are rising, with water now trading for over $1/bbl. This makes recycling not just environmentally friendly, but also the most cost-effective solution for operators.
Q: Treating produced water in the field for reuse in fracturing operations is one thing, but how can produced water be treated on site to meet community needs for use in agriculture and other activities?
GONZALEZ: Produced water tends to have such high levels of dissolved salts that a number of conventional treatment options–reverse osmosis, for example–are not efficient on their own. As a result, treating the salt from the water tends to require evaporative processes. These approaches are fairly mature, but power costs render them currently uneconomic compared with recycling for use in frac operations, where the dissolved salts can remain in the water.
They also cause logistical problems, and the obvious question becomes, “What does one do with all of that removed salt?” Our R&D team has been working with educational partners on these challenges since 2012, and we look forward to working with operators to solve this challenge economically by introducing new technologies that transform produced water to usable water for application in a number of beneficial uses.
Q: In West Texas in particular, the industry already is deploying desalination, disinfection and purification methods to treat natural brines sourced from deeper formations. Will this continue be a solution for the future? At some point, could we see treated seawater from the Gulf of Mexico being used to fracture wells in South Texas or the Permian Basin?
GONZALEZ: Nonpotable reservoirs and natural brine reservoirs are commonly treated the world over, from resorts in the Caribbean to provide drinking water, to industrial applications, to farming. Typically, this water is fairly easy to treat, with a combination of some pretreatment and reverse osmosis membrane treatment. The issue with using any water for oil and gas operations is transportation cost. If the water originates too far from the completions activity, the transportation cost rapidly becomes higher than the cost of the water itself, making it an uneconomical option. It is, however, gaining prevalence in the Permian Basin, where water resources are scarce and activity levels are high.
Piping water from the Gulf of Mexico is an option, and this approach has been used in the Middle East. There are some chemicals in seawater that may interfere with downhole conditions, but these tend to be treated easily. The advantage of using seawater is that there are several technologies, including our seawater electrochlorination systems, which can disinfect that water, using no more than the seawater itself. This would enable it to be used immediately for frac operations. As noted, however, one must consider the added cost associated with transporting water over long distances, which again reinforces the point that recycling produced water in-basin is the most cost-effective and most practical solution.
For other great articles about exploration, drilling, completions and production, subscribe to The American Oil & Gas Reporter and bookmark www.aogr.com.