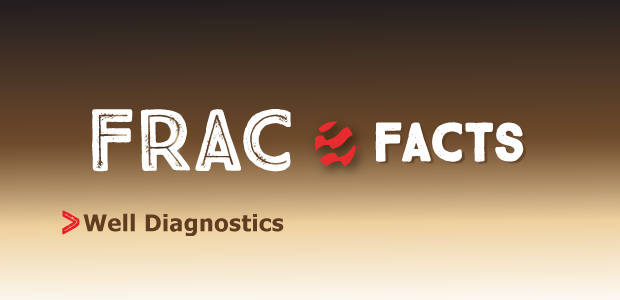
Downhole Tools Collect Data Efficiently To Drive Well Performance
By Colter Cookson
In the oil field, knowledge is power. The more the industry learns about the subsurface, the more it can optimize everything from drill bits and completion designs to enhanced oil recovery techniques, which ultimately translates to higher returns and smaller environmental footprints.
Understanding what is happening thousands of feet beneath the surface must always require inferences, but between more robust and affordable downhole tools and models that can turn data into deeper insights, it is becoming easier to picture downhole events at the surface.
Wired drill pipe can enable operators to get more information from down hole. “Wired pipe’s general reliability has improved enough that we believe the technology will follow a similar adoption path as rotary steerable systems, making another step forward in the well construction process,” says Ian Silvester, chief executive officer for the U.S. subsidiary of Reelwell AS. “It will not only improve drilling efficiencies, but also help drillers put the well in the optimum place and deliver smooth, high-quality wellbores.
“These benefits come because wired drill pipe can send data at rates above 56 kilobytes a second, 10,000-15,000 times faster than existing mud pulse or electromagnetic telemetry,” Silvester reports. “At that speed, operators can be much less selective about the essential data they need to send to surface.”
According to Silvester, more detailed and frequent data can unlock three benefits. “First, it helps drillers put wells in the right place,” he begins. “If they drill geometrically, they can get much more frequent updates on the bit’s position, inclination and azimuth and adjust as needed. If they are geosteering, they can make better decisions based on higher-resolution gamma ray and resistivity logs.”
Drillers also will have the visibility to be able to react faster to drilling dysfunctions that can impact hole cleaning, cause stuck pipe or damage the bit and bottom-hole assembly, Silvester adds. “For example, we can go from sending data on shock and vibration or stick-slip every minute or two to sending it multiple times a second. This change lets drillers see early signs of drilling dysfunctions and change drilling parameters before they cause major damage to the hole or lost time,” he says.
“The third benefit of faster telemetry is that it removes invisible lost time associated with taking direction and inclination surveys, downlinking to rotary steerable systems or waiting for confirmation measurements after adjusting a mud motor’s tool face. Industry studies suggest wired pipe’s telemetry rates can reduce nonproductive and invisible lost time accounting for 5%-15% of total drilling time,” he reports.
Silvester predicts wired drill pipe will make it possible to advance automated drilling processes by using high-frequency downhole measurements and closing the loop between down hole and surface, which should improve consistency from well to well and crew to crew.
Powering Downhole Equipment
In addition to moving data, Reelwell’s wired drill pipe can send power from the surface to downhole equipment, Silvester reports. “Our wired braid delivers 500 watts down hole,” he details. “At first, we expect this power to be used as a backup in case downhole turbine generators fail or lithium batteries run out of life. It should enable longer runs in areas where that is common.”
As operators and service companies get comfortable with power by pipe, they may remove the turbines and batteries entirely to shorten their BHAs and increase run length, Silvester says. “Shorter BHAs would put measurements closer to the bit, which can improve steering, and reduce downhole tools’ complexity, which should save money and increase reliability,” he says.
Reelwell AS’ wired drill pipe can improve drilling performance by sending high-speed data and power to and from downhole tools. For reliability, transmission takes place through a copper braid with 816 wires inside. The company explains that if one wire short-circuits, others continue to carry the signal.
“In the long term, we believe service companies will build tools that take advantage of greater downhole power to deliver better performance,” Silvester says. “That could mean, for example, converting a battery powered ultrasonic caliper logging tool that today only stores data in memory into one that sends a memory-quality log to surface in real time.
“With fewer power constraints and the freedom to send verified commands to and from downhole tools regularly, drillers eventually may be able to tweak the settings for circulating valves, or variable gauge stabilizers or reamers on demand,” he remarks.
“As we developed our wired drill pipe, we kept reliability and ease of use in mind,” Silvester assures. “From the outside, the pipe looks like normal double-shoulder drill pipe. It does not require special handling, racking or doping. The connectors are extremely robust, but in the unlikely event one does get damaged, it can be replaced in the field.
“We transmit data and power using a copper braid that is bonded to the pipe’s inner diameter,” Silvester describes. “This braid is made up of more than 800 wires that are interlaced such that if one wire gets damaged, others still can carry the power and data.”
To validate its wired pipe, Silvester says Reelwell has conducted more than 90 test runs across six rigs in Norway and the United States. These included an 80-hour customer demonstration of the entire system at the NORCE Ullrigg test rig during which the wired pipe maintained 100% uptime for both power and data transmission, running BHA tools from both Reelwell and a large service company without batteries down hole.
In March, Reelwell made its first commercial sale when Nabors Industries ordered two wired drill pipe strings for use in U.S. land applications.
Affordable Logging
Open hole logs can help operators improve completion efficiency and effectiveness, says Darby Witt, completions technology specialist with Cordax Evaluation Technologies Inc. “With log data, we can package stages so each cluster has similar wellbore facies and geomechanical properties,” he outlines. “Minimizing differentials between closure stress, near-wellbore friction and net pressure within each stage drives better cluster efficiency.”
In many applications, Witt says logs give operators the confidence to use more aggressive stages. “For example, they may move from five clusters in 250-foot stages to eight clusters in 400-foot stages,” he illustrates. “Treating more clusters in each stage has a huge impact on pump idle time and overall economics.
“In West Texas, analyzing logs helped us turn a 40-stage frac in a 10,000 foot lateral into a 26 stage frac,” Witt reports. “That cut days off fracturing time, saved half a million dollars and dramatically reduced greenhouse gas emissions.”
To reduce logging costs, Cordax Evaluation Technologies has developed techniques for recording open hole logs as the drill bit trips out of hole and cased hole logs as plugs are being milled. According to the company, these logs can help engineers design hydraulic fracturing operations and evaluate performance.
Witt says limiting emissions is increasingly important to operators of all sizes. “By reducing idle time during hydraulic fracturing, tailored completions can eliminate 80 tons of carbon dioxide emissions from a typical job,” he calculates.
For context, the World Bank estimates that the average U.S. citizen produces 15 tons of CO2 a year. In other words, the savings from one job can offset five people’s emissions for an entire year.
To obtain open-hole logs efficiently, Witt recommends a Cordax technique that allows logs to be collected as the bit trips out of the hole. Called logging-while-tripping (LWT), this technique involves putting a monobore collar above the final drill bit and drilling to total depth, then pumping logging tools down hole that seat inside the collar.
“In vertical or moderately deviated wells where logs normally would be acquired with wireline, LWT eliminates the rig time associated with rigging up the wireline unit, dropping it and coming out of hole,” Witt reports. “In unconventional horizontals that otherwise use through-the-bit systems, we save the time associated with tripping out of hole to switch to bits and going back down to log the lateral.”
In many unconventional horizontals, removing those tasks saves 12-16 hours of rig time, Witt estimates. He adds that LWT almost eliminates the risk of losing a source down hole. “The logging tools stay inside the drill pipe throughout the entire run, and if the pipe itself gets stuck, the tools can be fished out,” he explains.
Meanwhile, to help operators evaluate completions, Cordax has spent the past year developing a similar process for gathering post-frac logs. “With this new technology, we can deploy logging tools and take cased-hole logs as frac plugs are milled out,” Witt describes.
“Combined with the open-hole logs, these logs enable us to determine cluster efficiency, closure stress differentials and variations in cement thickness,” he says. “We can use this information not to only see which clusters treated poorly, but also to understand the near-wellbore characteristics behind that performance. Our goal is to accelerate improvements in completion design.”
Intelligent Wells
In their quest to shrink production costs and environmental footprints, many operators are looking at intelligent completion systems (ICS), says Paul Tubel, CEO of Tubel Energy. “These systems combine increasingly sophisticated sensors with control systems that can be remotely actuated to block or restrict production flow from specific areas,” he describes. “Wireless intelligent completions let operators monitor in real time what is going on in the tubing, production, casing and reservoir permanently, then make adjustments to improve production.”
In offshore wells, especially deepwater ones, Tubel says ICS have helped operators significantly reduce or at least delay water encroachment. “In wells’ lateral sections, ICS can equalize pressure to address the tendency for production to come mostly from the heel instead of the entire section,” he adds. “The ability to produce from multiple zones simultaneously should increase hydrocarbon production and accelerate cash flow as well as reduce CO2 generation.
“We are not yet at a point, however, where deploying a full ICS in a shale well is economic,” he acknowledges. “That may change as the systems become more affordable and their capabilities expand.”
By enabling operators to monitor and control downhole flow, intelligent completion systems minimize water encroachment and increase oil production. Tubel Energy says ICS’ benefits will become more widely available as advances in electronics, downhole power generation and wireless communication reduce deployment costs and improve reliability.
Tubel says that is exactly what is happening. As a case in point, he cites advances in electronics’ reliability. “As car companies depend on intelligent systems to manage everything from engines to brakes, they are developing chips and other components that reliably operate at high temperatures. We are adapting these technologies to oil and gas,” he relates.
“The other breakthrough driving more widespread interest in intelligent completions is in situ power generation,” Tubel continues. “For that, we use turbines that can last seven-10 years, far longer than the two-three years typical for downhole batteries.”
The key to these turbines’ longevity is protecting them from large solids and designing the internals to allow smaller solids to pass through, Tubel outlines. He recommends placing turbines in side pocket mandrels rather than putting them inside the production tubing, where they would restrict production and complicate interventions. Side pocket mandrel deployment also means the turbines can be replaced by slickline if they fail.
The turbines provide enough power for downhole sensors and actuators, Tubel assures, noting that the smallest systems produce up to 100 watts. In most wireless intelligent wells, the downhole system sends data to and receives commands from surface by transmitting acoustic waves through the production tubing.
“Wireless communication, downhole power generation and reliable electronics eliminate the need for lengthy downhole cables and hydraulic lines,” Tubel says. “In addition to simplifying installation and improving reliability, this lets us deploy intelligent systems anywhere, including the lateral.”
Wireless Power
To help operators monitor completions and production, Tubel says his company has engineered sensors that can be installed permanently inside the casing and are robust enough to survive the completion. Historically, these sensors would be powered by lithium batteries, which only last two-three years.
“To extend casing sensors’ useful life, we have created a wireless power transfer technology that can send power from a turbine in a tubing side pocket mandrel to the casing. Think of this technology as the downhole equivalent to wireless iPhone chargers,” Tubel compares. “When the casing sensors receive power, they turn on, record data and send the data to a tubing receiver using short hop electromagnetic telemetry. The receiver forwards the data to surface through the production tubing using acoustic real time wireless communications.
“For the first time, operators can have sensors in their casing that can provide real-time updates about the casing and reservoir for a long time,” Tubel emphasizes. “These include strain gauges for seeing if external forces are being exerted on the casing and may cause it to collapse. We also can deploy induction and resistivity sensors in the casing to track water and hydrocarbon flow in the reservoir so the operator can spot and slow water movement before it reaches the production stream.”
Optimizing Drawdown
Software that automatically performs rate transient analysis on early production data can help operators optimize their drawdown rates, says Darryl Tompkins, chief technology officer at Revo Testing Technologies. “The benefits can be huge,” he reports. “For one client, we had the chance to compare wells using our software with several wells on the same pad that followed a drawdown rule of thumb. By showing that the operator could produce more aggressively without damaging the wells, our software brought forward $750,000 in revenue.”
Revo Testing Technologies’ software automatically performs rate transient analysis on wells’ production data. The company says this helps operators optimize reservoir drawdown to recover oil and gas as quickly as possible without reservoir damage.
In other deployments, Tompkins says the software has identified excessive production. “Aggressive choke increases are one reason wells with a high initial production rate can underperform,” he warns. “Flowing too fast can wash proppant out of fractures, reducing the fractures’ longevity, and potentially create sand-based pinch points between the fractures and the wellbore.
“Dropping the pressure too quickly also may cause hydrocarbons to break into the fracture system before frac water has been cleaned out. This can leave water locked inside the fracture system, limiting its hydrocarbon conductivity,” Tompkins adds. “Overly-aggressive pressure drops also may close far-field fractures that are being held open by pressure.”
In an unconventional well, the drawdown rate can change every four hours, says Christina Costello, Revo’s executive vice president of business development. “To show when a change needs to be made, the software uses colors. Green means drawdown can be accelerated, while red means it needs to be restricted,” she illustrates. “This makes it easy for both engineers and field hands to see when they are producing the well as aggressively as possible without causing damage.”
Other Insights
Revo CEO Adam Swartley emphasizes that the company’s software has unique capabilities. “The traditional rate transient analysis techniques that most commercial software programs implement are tailored for long-term data,” he says. “We have been working with academia to create cutting-edge physics-based models so we can use flowback data to provide more insights.”
Tompkins says that work is paying off. “We are adding features now that can give a complete characterization of the subsurface conditions with limited production data. In unconventional wells, we only need 30 days’ data to characterize the reservoir, infer the frac geometry and estimate total production.
“Our models also can detect subsurface issues,” he adds. “For example, we can tell that a sand bridge is forming within an hour of it first occurring, allowing operators to address it before it causes more damage.”
“The software’s ability to get detailed information on the reservoir within 30 days should help operators zero in on the best completion designs and well spacing for new fields more quickly,” Swartley assesses.
High-quality data can increase the software’s accuracy and reduce the time needed to recommend choke changes, Swartley mentions. “A few years ago, flowback data often was collected by sending someone out to the field to use a dip stick or read a gauge.” he recalls. “Today, more operators have moved to automated measurement systems, which allow us to make predictions with greater speed and certainty.”
To help clients transition from manual to automated flowback hardware, Costello says Revo built its own flowback system. “To ensure data quality, we have made some changes to the internal geometry and deployed baffles that improve oil and water separation. We use Coriolis meters to measure water and oil at the exact same time every hour, which gives us consistent, high-quality data.
“The system uses electric valves rather than pneumatics, so it is a good fit for operators who want to reduce emissions,” Costello adds.
For other great articles about exploration, drilling, completions and production, subscribe to The American Oil & Gas Reporter and bookmark www.aogr.com.