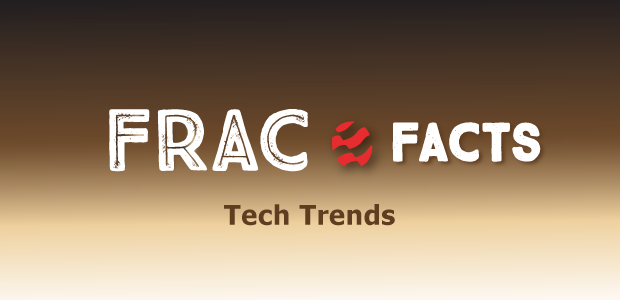
Electric Frac Fleets Continue Evolving
By Colter Cookson
Not long ago, companies that were thinking about building an electric hydraulic fracturing fleet would have to ask themselves whether the environmental and operational advantages would justify the innovation when they had the option to stick with proven dual-fuel fleets. Today, the answer seems clear. While the capability of dual-fuel fleets to run on diesel in the absence of natural gas likely ensures continued use even after the existing dual-fuel fleets retire, the number of electric fleets is growing.
“Electric fleets are great,” says Larry Carroll, vice president of engineering and technology at ProFrac Services, the world’s largest e-fleet operator. “Because they run off power generated entirely by natural gas rather than diesel, they significantly reduce fuel costs and emissions. We have also noticed that they tend to be more reliable.”
Carroll attributes that reliability largely to the electric variable frequency drives connected to each pump having far fewer moving parts than combustion-based engines. “In industrial settings where the electric motor or VFD is stationary, it could have a lifespan of 20-plus years because all it needs to do is spin,” he says. “Since we drive the motors down bumpy roads in temperatures as cold as -50 degrees F and as hot as 120, then expose them to vibration while we’re pumping, we have to work harder to get that type of lifespan.”
In some of the earliest electric fleets, the motors only lasted two or three years, Carroll recounts. However, trailer design changes aimed at mitigating vibration, harmonics and other sources of wear and tear quickly improved performance.
“Past the first generation of e-fleets, we have not had a VFD failure,” Carroll reports. “For many of the fleets’ components, we do not yet know how long their lifetimes will be because we have not yet had any major issues.”
Electric hydraulic fracturing fleets combine significant fuel savings and emissions reductions with high horsepower density and exceptional reliability, ProFrac says. To take advantage of these benefits on sites with insufficient natural gas to power an entire fleet, some dual-fuel fleets now incorporate a few electric pumps.
Today, the company’s newest electric fleets use eighth-generation designs. “Each build gets slight tweaks to different aspects, whether it be how we hang the hoses, how long those hoses are and how big they are; the types of motors we use; or the fans and other cooling techniques that keep those motors from overheating in Texas. On the outside, the latest pumps resemble their predecessors, but they have many small changes that contribute to better reliability and performance.”
While effective designs enable reliability, Carroll emphasizes that e-fleets still benefit from crews with training and experience. “VFDs are complex. It takes a high-voltage electrician to understand how they work and how everything flows,” he says. “If there is an alarm from the VFD, an experienced technician has a much better chance of diagnosing the problem and solving it before it shuts down the pump or causes other issues.”
To make the equipment as robust and user-friendly as possible, Carroll says that ProFrac designs and builds its fleets in-house with considerable input from people in the field. “One of the advantages of in-house engineering and manufacturing is that we can iterate quickly,” he says. “If we notice a problem with a new design on Friday, we can often revise the design, build the new version over the weekend, and send it out to the field on Monday.”
Fuel Savings
Electric fleets can enable faster and more precise control of pump rates than their diesel counterparts, but Carroll says their biggest strength is their ability to displace diesel with more affordable and cleaner-burning natural gas. He adds that they excel at jobs requiring small pads, as each trailer can hold two pumps with a combined 6,000 horsepower, which is 2.4 times as much as a conventional 2,500 horsepower pump.
The pumps motors can draw electricity from an available power grid, but Carroll says it is more common to generate power using aeroderivative turbines or a series of reciprocating natural gas engines. “We are agnostic as to the power source,” he comments. “In many cases, availability, pad size or an operator’s existing power infrastructure determine what a given site uses.”
Regarding pad size, Carroll points out that turbines tend to have a smaller footprint than reciprocating engines. “Many of the recips we see generate 2.5 megawatts each, meaning a site needs a few of them to power a whole fleet,” he explains. “However, some operators prefer them because they know that if one goes down, pumping can continue.”
Recip-based generators can also accommodate hybrid fleets that use both electric and dual-fuel pumps. This can allow operators to try electric pumps without committing fully to them, Carroll mentions. He adds that the hybrid approach can be appealing in areas where insufficient gas is available to power an entire e-fleet because a mixed fleet lowers diesel consumption compared with dual-fuel equipment alone.
“The improvement from adding electric pumps to an existing dual-fuel fleet depends on several factors, such as the type of dual-fuel equipment. Some dual-fuel engines have a nameplate displacement of 85%, while others only deliver 40%,” he notes. “However, we have seen electric pumps take a fleet’s substitution level from around 60% to around 80%, which is significant.”
Finding Power
Finding turbines or reciprocating engine generators to power electric fleets may get tricky because of competition for equipment from other markets, assesses Geoff Bland, vice president of business development for Life Cycle Power, a provider of microgrids and mobile power solutions. “The biggest question is how much power generation equipment will be redirected to data centers,” he says. “The market is so hungry for power right now that the supply chain may not be able to keep up and people will end up using whatever they can get.”
That situation has already pushed lead times for natural gas turbines and some well-known engines years out, Bland relates. “People are looking into slightly more exotic engine suppliers rather than relying on the top three or four brands,” he says.
On many hydraulic fracturing sites, including ones involving simulfracs, turbines’ ability to pack significant power into a much smaller footprint than reciprocating engine generators can be a huge boon, Life Cycle Power reports. The company adds that turbines can run on field gas that has undergone minimal treatment.
Any future tariffs could exacerbate the supply crunch, Bland warns. “The supply chain does not stop with the vendor that a producer works with,” he notes. “As an example, if that vendor’s equipment is manufactured in China, its costs could go up significantly given the aggressive stance that the United States seems to be taking against China.”
To justify investing in electric fleets, pressure pumpers need to be confident that they will have access to power generation, a reality that Bland says has prompted many pressure pumpers to make long-term commitments to secure power without necessarily having contracts in place for their electric fleets. Some have gone further, investing in or starting their own power companies to support their frac operations.
“I expect in the next year or so, there will be more consolidation to help control costs,” Bland predicts. “In the early days of electric fleets, some of the service companies that bought power equipment struggled because they did not have the expertise to package it for efficient deployment or to maintain it. Add in uncertainty about electric fleets’ future, and many companies decided to outsource power to third parties.”
Life Cycle Power, which Bland notes is independent from any pressure pumper, is one of the companies that has benefited from that trend. “At this point, Life Cycle and other third parties have proven that turbines can have the mobility and reliability hydraulic fracturing companies need as long as they get the right maintenance,” he says. “That record is increasing confidence in electric fleets and may see more power brought back in house.”
Turbines’ Appeal
The market will need to draw on every power solution to meet demand and achieve customer goals in certain applications, Bland says. However, he generally recommends generating power with turbines when they are available.
“One reason is the footprint,” he says. “On some simulfracs, the generation equipment will need to supply 50 megawatts of power. Doing that with 2.5 megawatt engines would require 25 units, all of which need to be connected to the switchgear that feeds the pumps. Turbines can have a much larger capacity, so it may only take two to do the same job.”
In fields with small pads, such as many in the Northeast and the Rocky Mountains, turbine power density may be a requirement, Bland says. Even in regions with larger pads, it’s beneficial. “In the field, less is more,” he suggests. “With fewer wires to connect, there are fewer safety hazards and fewer failure points.”
Bland adds that it’s possible to set up turbines with a small crew. “We can get a 35-megawatt turbine ready in about 12 hours,” he illustrates. “It’s possible to achieve similar speeds with engines, but it requires more people.”
Turbines also have the flexibility to run on field gas of widely varying quality, which is often the most economical fuel source a site can access, Bland reports. A reciprocating engine can run on field gas as well, but because the engines have tighter fuel specifications, field gas usually needs more extensive treatment. To perform that treatment, many service companies that rely on reciprocating engines have purchased firms that focus on treating field gas or transporting compressed natural gas to location.
“With turbines, the market can run on field gas that has had minimal treatment,” Bland says. “We are helping several customers do that today because it lets them keep their costs low.”
Addressing Concerns
While turbines have many advantages, Bland acknowledges limitations. For example, because of higher power density, if one turbine goes down, it will have a big impact on the job. “It is theoretically possible to have a backup on location, but that’s too expensive to be practical,” he says. “Instead, we minimize the chance of downtime by doing maintenance beyond the OEM’s recommended service regime.”
With that maintenance, turbines can be extremely reliable, Bland assures. In addition to being used in jet engines, where failures would put lives at risk, turbines generate most base load power for electric utilities. “Engines generally only see use in emergency or peak shaving applications,” he contrasts. “Turbines cost more to purchase, but they have a much longer lifetime and require less service, which makes the overall costs lower.”
Aside from reliability, the other concern that Bland reports hearing frequently relates to fuel efficiency. A perception that turbines consume excess fuel between stages is not supported by field data, he says.
“Turbines’ exact fuel efficiency will vary from job to job, but it is close to the efficiency for engines,” Bland says. “For one recent job, the peak efficiency was 36.75%, and the average efficiency—including all the idle time—was 31.31%. For comparison, engine operators will state that they can get 44% efficiency. However, this figure assumes the equipment is running at full load continuously.”
That is not what happens during hydraulic fracturing, Bland observes. “Engines and turbines see similar efficiency losses at low loads, and engines experience electrical losses from combining so many individual generators,” he says. “In reality on a frac site, the spread in fuel consumption between engine- and turbine-driven solutions is negligible. The data shows that the best way to increase fuel efficiency is to decrease idle time between stages, not to select one generator technology or another.”
Check Valve
After three years of development, Gilmore is commercializing a check valve that lasts three-six times longer than traditional alternatives, says Jean-Louis Doguet, the company’s vice president of unconventional. “A typical flapper check valve on a standard frac pad running 40/70 and 100 mesh sand will last 200-300 hours before it has to be repaired,” he reports. “Advanced coatings and pin materials allow some premium products to average around 600 hours, depending on the environment, treating parameters, proppant type and volumes, and chemicals. With our new valve, which moves away from the flapper concept, we have units passing the 1,800-hour mark.”
By studying fluid dynamics and employing robust materials, Gilmore has developed a check valve that can stay in service for months without requiring maintenance. The company says the check valve almost eliminates the risk of a valve body washing out and causing downtime during hydraulic fracturing.
According to Doguet, this longevity should improve operational efficiency. “Historically, the best valves last about a month, which means companies need to perform maintenance every 30 days or so,” he says. “Usually, that maintenance involves unscrewing the top of the flapper check valve with a wrench, replacing the flapper and/or the seal/seat, and screwing the top back on. This takes about five minutes for each valve and requires a repair kit.”
In contrast, Gilmore’s more durable valve can stay in the field for about three months before any maintenance needs to take place, Doguet reports. He adds that the valve almost eliminates the risk of washing out a body during the job. “Washouts do not happen as often as they used to, but when they do occur, they force the crew to stop pumping in order to replace the valve,” he says. “That downtime can be expensive.”
To explain why Gilmore’s valve minimizes the chance of wash outs, Doguet points out that it has a stainless-steel wear sleeve inside that protects the body from erosion. During months of service, this sleeve will wear, by design, and will be replaced as necessary as part of the maintenance schedule. “We have not had a sleeve exhibit high wear yet, so washing out in the middle of a job is highly unlikely,” Doguet suggests.
In general, Doguet attributes the valve’s longevity to a combination of more durable materials and components, as well as a patented design that manipulates fluid dynamics.
Because the valve contains premium materials, it is more expensive to manufacture than a traditional valve, Doguet notes. The unique design also means that technicians need special training to work on it. With those factors in mind, he says Gilmore decided to provide the valve through a rental model rather than selling it to customers and expecting them to perform the maintenance.
“We think this approach is easier for our customers,” Doguet says. “We deliver the valves to location and repair them when they need to be repaired, so our customers do not need to buy valves and repair kits, manage inventory or spend time messing with check valves. Instead, they can focus on more critical tasks, such as servicing pumps.”
The monthly rental rate range for the longer-lasting valve provides attractive economics for customers when all factors are considered, Doguet says.
According to Doguet, the valve has been tested in the harshest conditions. In one trial, it weathered resin-coated and ceramic sands that can be particularly erosive to equipment, then high flow rates and pressures with produced water on back-to-back pads through 1,800 hours of service.
“The biggest hurdle for us has been convincing customers that the valve lasts as long as the field trials indicate it does,” Doguet says. “The longevity is so far ahead of the norm that it is hard for people to accept the test data, especially if they have had new equipment perform below expectations before. We usually meet with them in person, review design characteristics and offer a trial period so they have a chance to see the benefits for themselves.”
Through those efforts and word of mouth, Doguet sees adoption growing. “Today, we have several customers running our valves, most of them in the Permian,” he says. “In the first half of 2025, we are planning to manufacture approximately 1,000 units with a variety of industry connections. The exact number will be market driven.”
While he expresses Gilmore’s pride in the current design, which he calls market-changing, Doguet emphasizes that Gilmore plans to continue refining it. “We are going to continue making this valve better,” he says. “In a perfect world we can get this valve to a six-month operating life.”
For other great articles about exploration, drilling, completions and production, subscribe to The American Oil & Gas Reporter and bookmark www.aogr.com.