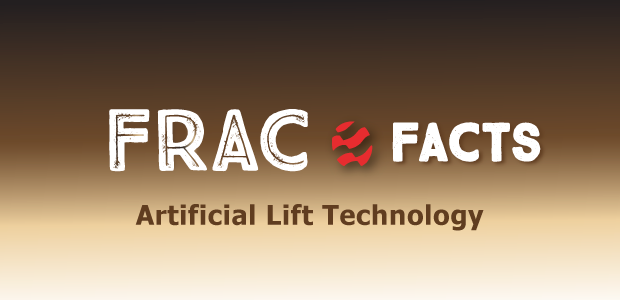
ESPs Excel In Lifting Water, Restoring Production Following Frac Hits
By Marian Perez Salazar
LUBBOCK, TX.–Oil and gas companies have devoted significant efforts to minimizing the impacts of hydraulic fracturing hits in horizontal resource play development strategies as activity has progressively shifted to infill locations with longer laterals. Considerable knowledge has been gained over the years in understanding how stimulation fluids and pressures can interact with one or more adjacent wells during active frac treatments, including several methods to protect offset wells from both short- and long-term interference.
However, should a well be impacted by a fracturing operation on an adjacent well or pad, what is the best course of action to restore production as quickly as possible? A Texas Tech University research study analyzed the repercussions of a frac hit on a well’s operational parameters, with an emphasis on the comparative effectiveness of employing optimized artificial lift techniques following a frac hit to facilitate a rapid recovery in well performance.
Recognizing artificial lift systems are not universally applicable across all wells given the diversity in well characteristics and reservoir conditions in shale plays, the scope of the analysis was narrowed to wells using electric submersible pumps and gas lift—both of which facilitate high rates of fluid extraction—to establish a comparative framework for evaluating lift efficiencies in the context of frac hits. Moreover, the research focused on individual wells situated in parallel configurations to exclude the complexities introduced by multiwell pads and provide a clearer understanding of the direct impacts of frac hits and the subsequent recovery strategies using artificial lift systems.
Common Mitigation Practice
One of the most common frac hit mitigation practices is shutting in an offset well during nearby new well completion activities as a precautionary measure. However, when a shut-in well is brought back into production, it may perform quite differently than it did before shutting in. This could be the result of several factors, including:
- Pressure variations (pressure changes sometimes can be beneficial and enhance oil recovery, but they also can be detrimental and reduce flow rates or create unexpected pressure conditions);
- Interwell communication through fractures (if the created fracture network connects adjacent wellbores, it is possible for the fluids to intermingle and lead to cross-contamination or production changes); and
- Frac fluid migration (fluids injected during the fracturing process can migrate to adjacent wellbores, altering reservoir fluid composition and properties and affecting flow characteristics and production rates).
Figure 1 shows an increase in pressure in a Woodford Shale parent well (Well A) that was shut in while an adjacent offset child well (Well B) was being hydraulically fractured. The well was opened after the fourth stage of the child well’s completion.
FIGURE 1
Parent Well Casing Pressure versus Child Well Surface Treating Pressure (Woodford Shale)
Source: SPE 187192 (George E. King, et. al., 2017)
Overall, frac hits tend to negatively impact the performance of wells in liquid-rich reservoirs, particularly as a well’s natural reservoir pressure decreases over time. After being shut in because of a frac hit, wells often experience a rapid drop in oil and gas production followed by a gradual recovery period. Although this pattern can vary by region, water output tends to spike immediately after a hit and then decrease as the well stabilizes.
In areas with an underlying brine formation, a frac hit can also increase brine production in the impacted well and any others it connects with. The financial consequences of such bottom-water hits hinge on several factors, including the ability of the fractures to seal over time and the presence of a driving force from the underlying water.
Production Trajectory
Figure 2 shows a parent well’s production trajectory before and after an adjacent child well’s completion. The depicted production curve incorporates a phase during which the parent well was temporarily shut in, followed by its reintegration into the production regime. In this case, the parent well was on gas lift. It required 28 days to restore its production levels to the pre-shut-in trajectory. On day 60, a coiled tubing clean-out run was performed to ensure no bridges had been created in the lateral during offset completion operations.
FIGURE 2
Production Curve Before and After Shut In (Woodford Shale Child Well)
Source: SPE 187192 (George E. King, et. al., 2017)
Since fracture development is so unpredictable, the likelihood and consequences of a hit vary widely. There can be instances where a well never returns to its previous decline curve, as well as ones where communication between wells actually increases the older well’s production.
One of the primary concerns is the effect on estimated ultimate recovery. Shutting in a well may alter the reservoir dynamics and fluid distribution, potentially reducing the total volume of hydrocarbons that can be economically extracted over the well’s life. The disruption caused by nearby fracturing treatments can affect the pressure equilibrium and fluid flow paths within the reservoir, which, in turn, may degrade EUR.
Furthermore, the recovery time required for a well to return to its pre-shut-in production level can be extensive. This delay is not just a matter of lost production time, but also reflects the well’s resilience to operational disturbances and its ability to regain momentum. Longer recovery times translate directly into deferred revenues, complicating financial planning and profitability forecasts.
In addition, shutting in a well and subsequently bringing it back on line entails extra costs. These may include the expenses associated with monitoring and evaluating well status, implementing additional interventions to restore production rates, and potentially adjusting or repairing equipment to compensate for changes caused by the shut-in/restart processes.
ESP Optimization
Implementing an ESP system is a nuanced process that demands a comprehensive understanding of several interrelated factors. Unlike traditional pumping methods that may aim to lift a predetermined volume of fluid, ESPs are engineered to exert a consistent amount of force across the fluid column. This allows ESPs to adapt to varying conditions within the well, altering the flow rate based on the differential pressure they can generate. Consequently, the performance of an ESP is inherently linked to the fluid’s characteristics and the well’s physical parameters.
The key to optimizing an ESP design is evaluating the inflow performance relationship (IPR), which predicts the volume of fluid the reservoir can deliver under certain conditions. This aspect of design involves analyzing the reservoir’s behavior in response to different pressures to estimate how much fluid can be feasibly extracted. Alongside the IPR, outflow performance must be considered, encompassing factors such as fluid density (or specific gravity) and the vertical distance the fluid must be lifted. These considerations help define the energy needed for the ESP to impart sufficient energy to the fluid to overcome the physical challenges and ensure efficient lifting to the surface.
The design of an ESP plays a vital role in optimizing oil well production, particularly through the manipulation of wellbore pressure conditions. According to Darcy’s law, which governs the flow of fluids through porous media, the differential pressure across the formation face is directly proportional to the flow rate of the fluid. In the context of an ESP, this principle implies that an increase in the pressure differential created by the pump will result in a greater drawdown of pressure at the reservoir level, thereby enhancing the well’s flow capacity.
High Water Volumes
However, the performance of an ESP, and by extension the productivity of the well, can be impacted by the ratio of water to the total volume of fluids produced. As water cuts increase, it leads to a corresponding pressure decrease, which can be attributed to the specific gravity or density of the produced water. In scenarios where the produced water has a high specific gravity, the resulting increase in the density of the fluid mixture necessitates more energy (or a higher pressure gradient) to lift the fluids to the surface.
This relationship between water cut and well productivity becomes particularly pronounced in wells that encounter water with a high specific gravity. Despite these wells potentially possessing high intrinsic productivity because of favorable reservoir characteristics, such as high permeability or porosity, their output is considerably diminished by the challenges associated with managing high water production. The presence of water with high specific gravity increases the load on the ESP, requiring it to work harder to achieve the same level of fluid lifting, thereby directly impacting the efficiency of hydrocarbon production.
FIGURE 3
Gas Lift and ESP Performance Comparison (Reservoir with High Water Cuts)
Source: SPE-185773-MS (Suat Bagci, et. al., 2017)
In terms of mitigating the effects of a frac hit in which fracturing fluid invades an adjacent well, the primary objective is to expediently extract the influx of water from the formation to resume hydrocarbon production. To this end, deploying an ESP is a strategic choice, given the higher fluid lifting capacities and ability to enhance recovery rates. Figure 3 shows the favorable performance of ESPs relative to gas lift systems across varying degrees of water saturation within the reservoir.
The efficiency of ESPs becomes particularly pronounced as the water cut escalates, substantiating their effectiveness in minimizing the recovery time required for a well to regain its productive capacity after a frac hit. This advantage is attributable to the ESP’s inherent ability to handle substantial volumes of water and expedite the removal process, allowing oil production to be restored.
The design and selection of an ESP in oil wells with high water cuts necessitates careful consideration of the specific gravity of the water to ensure the system can handle the anticipated fluid densities. This entails not only choosing a pump with adequate pressure-generating capacity but also implementing strategies to manage or minimize water production to optimize overall well production performance.
Proactive Approach
While temporarily shutting in wells as a precautionary measure during offset well frac treatments presents both benefits and drawbacks, a spectrum of performance impacts can become evident quickly when production is resumed. These impacts are attributed to a complex interplay of factors, but primarily include reservoir pressure alterations and cross-well migration of reservoir and frac fluids.
The phenomenon of increased post-frac-hit water production spotlights the critical role of ESPs in navigating these challenges. With their robust design for handling substantial fluid volumes, ESPs can play an invaluable role in mitigating frac hits’ adverse effects by efficiently removing the influx of water to shorten the recovery period and minimize downtime—allowing production to resume as swiftly as possible.
The operational challenges associated with well shut-ins and frac hits demand sophisticated management strategies. Adopting ESPs represents a proactive approach to addressing these challenges. As the industry continues to navigate the complexities of reservoir management and production optimization, the insights gained from using ESPs to manage post-frac-hit recovery illuminate a path forward. By leveraging advanced technologies and an integrated approach to well management, operators can enhance production resilience and safeguard the long-term productivity of their assets.
Editor’s Note: This article was adapted from “How are ESP-lifted Wells Affected by Shut-ins for Offset Hydraulic Fracturing Treatments?” a paper originally presented at the Southwestern Petroleum Short Course, which was held April 15-18 in Lubbock, Tx.
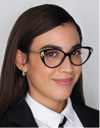
MARIAN PEREZ SALAZAR holds a B.S. in petroleum engineering from Texas Tech University. During an internship with Diamondback Energy in the summer of 2023, she studied how Midland Basin wells’ production curves change after being shut in during nearby hydraulic fracturing operations, tracking how location and artificial lift technique influence recovery times. The previous summer, she interned at ProPetro Services Inc., gaining both field and office experience with hydraulic fracturing, including a project related to dynamic gas blending pumps.
For other great articles about exploration, drilling, completions and production, subscribe to The American Oil & Gas Reporter and bookmark www.aogr.com.