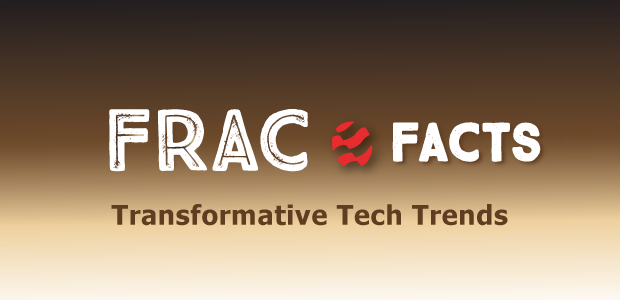
Extending Service Life Of Equipment Components Key To Improving Frac Efficiency
By Ryan Bludau
HOUSTON–Like the dizzying evolution of computing technology in the 1990s and early 2000s, the industry’s rapid advancement of the solutions, techniques and best practices to first enable, and then optimize, hydrocarbon production from ultralow-permeability formations during the past two decades has been remarkable. And the result is no less profound than the outcome of the computing revolution: Shale plays have forever changed the energy world.
From the beginning, operators recognized that hydraulic fracturing was essential to unlocking economic production rates. But the other major part of the story that emerged early on to enable the shale revolution was about horizontal pad drilling. Directional drilling times went from being measured in weeks to days and now to hours, even though today’s lateral lengths extend as far as to 10 times longer. The combination of multistage fracturing and multiwell laterals is the game changer.
The improved efficiencies during the drilling phase, combined with the fact that extended-reach well architectures expose vast sections of the reservoir for hydraulic fracturing on a single pad site, are crucial drivers of well productivity and economics. Today’s long-lateral multiwell pads continue to drive new capabilities in all aspects of well stimulation, from wireline equipment to hydraulic fracturing fleets, to achieve equal efficiency gains in well completion operations.
To prevent nonproductive time spent on equipment maintenance on the frac site, the ideal service interval for pumps and check valve repairs must be 500 hours, which aligns with the time required for a spread to stimulate a typical four-well pad campaign. This allows for maintenance on all equipment between fleet moves to the next pad site.
For hydraulic fracturing, operational cost is being reduced by using larger manifold systems and displacing as much diesel fuel consumption as possible, with many pressure pumping suppliers moving to dual-fuel engines to reduce operational cost and limit exhaust emissions. In addition, many fleets now are adding electric motor-driven pump trailers with higher flow rate outputs to reduce the number of trailers needed on the pad site. These electric motors can be powered by the local power grid, but typically run off electricity supplied by natural gas turbine-powered generators.
The original manifold systems consisted of hammer union connected iron developed years ago for well cementing and treating applications. Because of the pressure levels sustained for long durations during hydraulic fracturing, hammer union piping and connections were subject to extreme stresses that often led to frac site problems. The need to frac multiple pad wells in one spread mobilization made it feasible to assemble larger, more robust manifolds. These monobore systems consist of larger pipe with either clamp or API-style flanges. These systems have proven to be much more resilient in high-pressure fatigue applications.
In some instances, dual monobore systems are assembled on larger multiwell pads to allow for continuous pressure pumping operations on two wells. With simultaneous fracturing, a single crew can operate double the assets and leverage all the ancillary support of vendors and equipment, effectively doubling their utilization to further optimize efficiency.
More Innovation Needed
Despite all these new technological developments, more innovation is still needed to further unlock efficiencies and improve safety. The level of maintenance required to keep a single pressure pumping spread operational is significant. Reliability issues with positive displacement (PD) pumps subject to the unforgiving conditions on a frac spread have taught pressure pumping companies they must maintain additional pumps as backups. This increases the footprint of the operation and capital equipment cost.
A traditional pressure pumping setup employs 20 or more PD pumps to achieve pump rates around 100 barrels a minute. This number includes extra pumps as backups. It is common for PD pumps to have valves/seats or plunger packings begin to leak while pumping a stage. Pumps exhibiting issues are taken out of service, while the remaining pumps take on the added workload to compensate. When a pump is taken out of service, it is common to utilize a check valve to prevent pumped fluid from back flowing through the damaged pump. Without the presence of a check valve, the pumped fluid will leak out onto the pad site or back into the lower pressure rated feed side of the pump. Once the stage is complete, the damaged pump is disconnected and pulled from service for maintenance.
Over the years, the life of the valves/seats and plunger packings have improved significantly, but service life remains highly dependent on pumping pressure conditions. Because of these conditions, components need to be replaced periodically. In addition to the maintenance on PD pumps, check valves also must be rebuilt periodically to ensure they continue to function at peak performance. Most check valves used in pressure pumping applications are clapper style, using a flap-like sealing component that swivels up when flow from the discrete pump impinges on it; the faster the flow, the further up the flap swivels to expose more flow area. The service interval for check valves is much more frequent than for PD pumps, keeping support personnel busy during a pressure pumping campaign.
Extending PD pump and check valve consumable life will unlock efficiency gains. Increasing the service intervals for these products must be a priority for pressure pumping service providers. The combustion efficiency and emissions improve when gas turbines run at a steady state. Spooling large gas turbine power generators up and down can be a slow process that threatens to degrade operational efficiency when done frequently. The last thing any fleet operator or oil and gas company wants is a 35-megawatt generating unit operating with pumps and check valves in need of maintenance.
To prevent nonproductive equipment maintenance time, the ideal service interval for pumps and check valve repairs needs to align with the duration of time typically required to frac a four-well pad campaign, which averages 500 hours of service. This allows a refresh of all equipment between pad site moves. To achieve 500 service hours, products must evolve beyond the current state-of-the-art designs.
This requires engineers to approach product design from a new perspective. Most of the time, engineers must balance functional requirements against what customers consider most important. Field serviceability always has been particularly important to users of these products, but field serviceability is often not as important as product longevity and initial product cost is often not as important as the total ownership cost. The truth is, in situ product maintenance is usually not as cost-effective as it may seem.
Extending Service Life
Because of their limited service life-spans, products such as clapper check valves must allow easy field repair. The industry has responded by employing a top entry design to facilitate repair with the check valve still connected to flowlines. This configuration is suboptimal, however, and places the flap sealing element directly in the flow path, where it is subjected to erosion that compromises the check valve’s functionality.
In addition, the very turbulent flow from each of the PD pumps causes severe flutter and vibration of the flap, resulting in substantial abrasive wear in the hinge mechanism. The combination of erosive and abrasive wear can lead to the failure of clapper check valves.
Some pressure pumping companies are pursuing rental models for equipment rather than owning the assets, allowing experts to manage pressure relief and flow control equipment and other discrete products. This lets the pressure pumper focus on its core business of executing frac campaigns and gives the rental supplier insights to enhance product performance and identify new product development opportunities.
Similar to what is observed in clapper check valves, erosive and abrasive wear also leads to valve and seat failures in PD pump fluid ends. Erosive and abrasive wear eventually prevents the valve sealing element from providing adequate sealing effectiveness, despite its conical shape.
Historically, most pressure pumping service providers have focused on minimizing operational expense, driving buyers to focus on the initial price tag for products and rebuild kits. As with any product, the lowest-cost option rarely equates with the best operating performance, which leads to never-ending maintenance cycles. Now, the industry is beginning to transition to a new paradigm by looking at total cost of ownership models for making product and equipment investments.
In some instances, pressure pumping companies are pursuing rental models for equipment, compared with owning the assets. This allows product experts to manage discrete products that are used during a pressure pumping campaign. Suppliers that specialize in pressure relief and flow control product rentals allow the pressure pumper to focus on its core business of executing frac campaigns. This also allows the rental supplier to learn about how its respective products are performing, which helps foster the identification and development of product improvement opportunities.
Shifting the timing of when equipment is maintained thanks to increased product service life offers many benefits, including less human effort, fewer opportunities for safety incidents and reduced equipment downtime. All these benefits lead to increased equipment utilization. Performing maintenance is much easier and faster when more space is available around the equipment. Personnel can take advantage of forklifts and telehandlers to remove and replace heavy components, helping eliminate back injuries and other safety concerns. Performing maintenance after all equipment is shut down is not only safer, but much faster because of the ability to communicate with co-workers without the need for noise-suppressing devices.
Considerable innovation has transpired in recent years in the pressure pumping market. This innovation must continue to unlock additional efficiency gains. In addition to product innovation, shifts in ownership of pressure pumping equipment will continue to occur through the equipment rental model. Having specialized rental suppliers for pressure relief and flow control products has driven product focus, resulting in improved performance. This continual improvement in product performance is the key to achieving even greater operational efficiencies and jobsite safety objectives going forward.
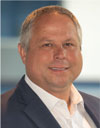
RYAN BLUDAU is chief technology officer at Houston-based Gilmore. Before joining Gilmore in 2019, he had more than 25 years of experience leading new product and technology development and supply chain management at Weatherford International, TechnipFMC, FMC Technologies and a GE Aviation company. Bludau brings a unique mixture of manufacturing, technical, operations and business management experience. He holds a B.S. in mechanical engineering and an MBA from Texas A&M University.
For other great articles about exploration, drilling, completions and production, subscribe to The American Oil & Gas Reporter and bookmark www.aogr.com.