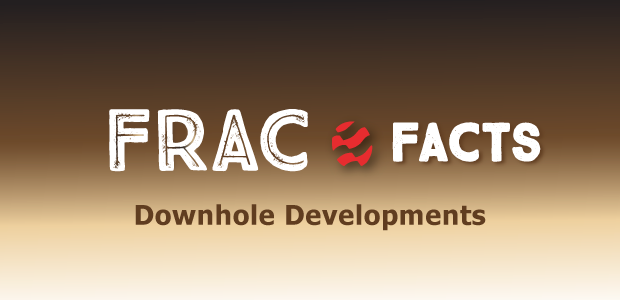
New Setting Tool Reduces Waste
By Mike Robicheaux and Seth Esponge
BROUSSARD, LA.—The quest to set and meet environmental, social and governance standards is becoming an increasingly important part of oil and gas companies’ activities. Organizations, along with their employees and wider communities, are committed more than ever to identifying and addressing risks to achieve a culture of safety and operational excellence. By valuing integrity and sustainability in downhole operations, the oil and gas industry can work to build a brighter future for the world around us.
Many downhole tool companies are dedicated to reducing their physical impacts on the environment. But how does that relate to and help address the kinds of challenges operators experience regularly on their well operations? The surest way to understand the market and identify what operators consider their biggest operational and environmental challenges is to reach out and ask. The feedback received from operators indicated that setting tools were causing significant difficulties, including being responsible for multiple fishing jobs, flooded tools and preset plugs. It became clear that there was an opportunity to focus on methods that would help solve these setting-tools-related issues.
To address these pressing industry challenges, operators are turning to a recycling setting tool program that utilizes state-of-the-art technology for a gas-operated, oil-free setting tool, providing a sustainable alternative to disposable and field-redressable tools. By recycling and rebuilding the setting tools for continuous use in a controlled environment, minimal waste is produced on each run down hole.
Setting Tool Waste
Setting tools may not necessarily be the first thing that comes to mind when thinking about ESG or operational challenges, but the fact is that disposable setting tools produce approximately 50 pounds of waste material during every run or stage. A field-redressable setting tool is another option to disposable designs. As the name implies, these tools can be redressed in the field, but they still require oil, generating approximately 12 pounds of waste in every run.
Alternatively, an environmentally friendly tool with an oil-free design and the latest setting tool technology has been developed to reduce waste to only six pounds per run. Serving as a sustainable solution, reusable setting tools are torn down, washed and rebuilt—and are designed for many repeat cycles in the field. The process includes:
- A clean tool is run into the well.
- After it is run, gas emissions are released inside the well, and not into the atmosphere (a process known as self-bleeding down hole).
- The tool then is returned to the shop to be torn down, where there is an opportunity to recycle the rubber and metal from the O-rings and set screws.
- The same tool then is redressed and prepared to again be run down hole.
A compact tool design means redressing takes far fewer consumables. All processes are conducted in a controlled environment, lessening the risk of pollution and fugitive emissions.
In short, once a redressable setting tool has been down hole and set a plug, it emerges from the wellbore with high pressure on the tool, which requires the gas to be bled off on surface. This procedure carries significant risk to personnel and the environment. In contrast, the environmentally friendly setting tool bleeds off down hole, meaning all the propellant gas is released once the plug is set, a safe distance away from the personnel working on surface.
Quality Assurance/Quality Control
As the tool is washed, all wastewater is collected and either is filtered and recycled for reuse in the wash process or is sequestered for downhole disposal through a saltwater disposal process. This process includes solids removal and oil/water separation. Then, the treated oil-free wastewater is injected into a saltwater disposal well. The skimmed oil is stored until sold and periodically taken away by an oil tanker.
Once the tools are washed, they are cleaned, greased and rebuilt in accordance with a rigorous quality assurance/quality control (QA/QC) process, which is a vital element in maintaining high industry ESG standards. Having any fishing jobs or presets in the wellbores means halting operations, with the accompanying downtime and costs. An efficient and reliable QA/QC program can avoid this.
The tools are inspected visually by QA/QC personnel to ensure they are clean enough to be built. Once built, every single tool is tested before it leaves the shop. Then, another round of QA/QC checks are deployed in the controlled environment of the service shop before they are loaded out for a job. This process is important to minimize downtime for the end user and increase efficiency on the well site.
Real-world results offer the best measure of quality effectiveness, and deploying an effective QA/QC program has enabled our company to have zero fishing jobs and zero preset plugs in more than 150,000 runs. A stringent QA/QC program is critical for operators who do not want to encounter traditional problems of multiple fishing jobs, flooded tools and preset plugs.
Harnessing Software
Specialized software makes it possible to track every QA/QC, shop and delivery process with a mobile software app. Every tool is given a universal tracking asset code and a unique serial number, which makes it possible to track each individual asset. The software tracks every time a tool is rebuilt, which includes pictures of the O-rings, set screws and shear screws. It also captures the testing process that is performed before each tool goes to the well site, ensuring the integrity of the O-rings and conformity to the cleaning and rebuilding processes. Each QA/QC checkpoint also is documented, along with every delivery and pickup of tools from the field.
Once the tools are delivered to the well site, the delivery also is input in the app. Everything can be tracked through the software so that if any problems arise or any assets are lost, photos and information can be retrieved quickly at any time to check the history and current equipment status. This approach can improve efficiencies in the field significantly.
Adopting more of an ESG focus for downhole tools and implementing more sustainable solutions means improving efficiencies for operators and/or service companies. In the downhole tools sector, that focus should be on reducing or recycling tools and tool waste, using fewer consumables and adopting sustainable alternatives. Drawing on tools that do not require the use of oil necessarily leads to an improved environmental footprint, along with the ability to properly wash tools and process and dispose of wastewater in a responsible way.
Delivering exceptional downhole setting tools in compliance with all applicable laws and standards should be the goal for every downhole tool company that wants to improve its environmental impact. This can be achieved only with a core focus on providing responsible leadership and ensuring ethical behavior within a culture of compliance for accountability, transparency and responsibility.
Furthermore, by aiming to build and maintain successful relationships among all employees, customers and the surrounding community, a culture of respect and inclusion can be fostered for everyone. Because it is important to give back to the communities in which we live and work, we support local charities through Stages for a Cause. A portion of the proceeds from every run Fortress tools makes down hole is set aside. At the end of each year, the amounts collected from all customers are calculated and financial donations are made to the charities of their choice.
The Stages for a Cause program has been a proud supporter of charity organizations including Miles Perret Cancer Services, Oil Patch Kids, MD Anderson Cancer Center and the Permian Basin Rehab Center, in partnership with XTO Energy, and we encourage other companies in the industry to do the same.
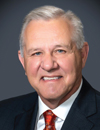
Mike Robicheaux is president and chief executive officer of Fortress Downhole Tools. Having founded the company in 2017, Robicheaux is responsible for the overall management and strategic direction, including its safety program and culture, mergers and acquisitions, and strategic guidance. He has nearly four decades of experience in the oil and gas industry. With extensive experience in operations, management, sales and marketing, and finance, Robicheaux has both managed and owned companies on a worldwide platform.
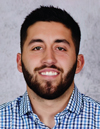
Seth Esponge is the Permian Basin regional manager at Fortress Downhole Tools. He previously served as Fortress’ facility manager at its Broussard, La., site, and joined the company after working as a through-tubing engineer at PetroStar Services. Esponge holds a degree in mechanical engineering from the University of Louisiana at Lafayette.
For other great articles about exploration, drilling, completions and production, subscribe to The American Oil & Gas Reporter and bookmark www.aogr.com.