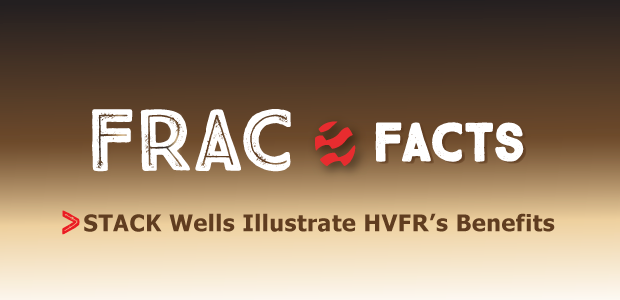
STACK Wells Illustrate HVFR’s Benefits
By Kyle Dahlgren, Brett Green, Brandon Williams, Josh Inscore and Mark Van Domelen
OKLAHOMA CITY–Following successful applications of high-viscosity friction reducer (HVFR) as a value-adding completion fluid in horizontal resource plays such as the Bakken, Permian and Eagle Ford, the technology was deployed in initial field trials in three wells operated by Devon Energy Corp. in the Anadarko Basin’s STACK play.
In addition to reducing pipe friction during hydraulic fracturing operations, HVFR fluids develop higher viscosities than traditional slickwater systems, reducing water and chemical requirements, enabling on-the-fly design change flexibility, and achieving high fracture conductivities. Moreover, by incorporating fit-for-purpose monomer structures, effective breakers and other advanced polymer chemistries, HVFR fluids exhibit higher regain conductivities than linear and cross-linked gels.
Three unique STACK case studies were identified as optimal tests for HVFR. The first included two offset horizontals with nearly identical landing targets, locations and completion designs. The lone differing variable was that one of the wells substituted HVFR for linear and cross-linked gel (prior to this project, most wells used a hybrid frac design incorporating both linear and cross-linked gels). The second case study applied the technology in an extended-reach lateral in a thinning pay zone to optimize economics in a stressed area. The last application was in a horizontal well in the geologic heart of the play.
Numerous benefits of the HVFR system emerged over the course of the three case studies. The first recognizable benefit was operational efficiency, ranging from a reduced number of chemicals on location to pump design simplicity for the operator and service companies. Second, cost savings were realized as a result of the decreased chemicals required, ability to place high sand concentrations, and flexibility to reduce chemical concentrations during completion operations. Also, well flowback exhibited the potential for equal or better production using HVFR compared with linear and cross-linked gels, theoretically because of higher regained conductivities.
The HVFR fluid was tested extensively in the laboratory prior to deploying in fracturing operations in the STACK wells. Laboratory testing analyzed:
- The frac mix water, including using multiple water sources based on logistical factors and the locations of the wells, in addition to bacteria testing that identified the presence of corrosive bacteria that were treated easily with a standard biocide;
- Fluid rheology, including obtaining viscosity profiles for the HVFR system prepared at different concentrations in multiple mix waters, and analyzing the distinct viscosity reduction gained by adding a liquid breaker designed for the system (in addition, friction reduction analysis in a laboratory flow loop showed HVFR consistently provided ±70 percent friction reduction values regardless of mix water composition variations);
- Formation mineralogy sensitivity to the frac fluid, including using drill cuttings to perform capillary suction time and fines migration tests, and fines migration testing to evaluate the presence of mobile clays such as illite within the rock matrix (after hot roll testing indicated a fairly strong presence of mobile clays, adding a clay stabilizer significantly reduced the amount of fines released);
- Fracture conductivity (laboratory work performed prior to this project indicated that the HVFR system was capable of providing very high regain fracture conductivities compared with guar-based linear and cross-linked fluids); and
- Proppant transport, which showed that different sizes of sand at 1-3 pound a gallon (ppg) concentrations were transported more effectively with HVFR fluid with less settling and better distribution within the fracture network than with linear guar gel.
STACK Meramec Wells
The newest horizontal target in the Mississippian-age STACK play is the Meramec, which is located stratigraphically on top of the Woodford and Osage formations. Multiple landing intervals within the Meramec enable operators to target and produce high-volume wells, as well as infill as many as 12 wells in a section. As seen in Figure 1, the Meramec’s stratigraphic thickness can vary greatly. Optimizing a frac fluid that can reduce costs while generating frac heights upward of 100 feet in some sections is a goal of many operators.
The three field trial wells have different characteristics (pay zone thickness, offset well control, gas-to-oil ratio, etc.) within the Meramec section. Additionally, all three case studies involved a different stimulation company to evaluate the cost and benefits of the technology. The primary goals were to either create equally productive wells at lower cost, or generate greater productivity from increased conductivity at costs similar to the hybrid design.
In the first case history, two new parent wells offsetting each other across a lease line were drilled and completed one after the other. Both wells were planned to be as similar as operationally possible, with the only exception being frac fluid chemistry. Both wells were landed 100 percent within the target window, and lateral lengths were within 4 percent. The horizontal offset between the wells is 800 feet. The gross pay within the landing interval for both wells is 125 feet and within the primary pay window in the field. These wells were an ideal opportunity to ensure HVFR could create similar fracture heights to access the full pay zone.
Devon’s standard frac design using two proppant sizes (100 and 40/70-mesh) was implemented on the two wells. Well 1 to the west was selected as the control well and completed first. It used a hybrid pump schedule ramping from slickwater to linear gel and finishing with cross-linked gel. Well 2 substituted all gel in the pumping schedule with HVFR. The volumes between the two wells were kept as similar as possible. Stages, clusters, pump rate and pump design were all held constant.
The same stimulation company completed both wells. All chemicals on the wells were identical, with the lone variable being substituting HVFR for linear and cross-linked gel, and their respective breakers. Operationally, the wells completed nearly identically. The average pump rate between the two wells was similar, with the average treating pressure (psi)/pump rate (bbl/minute) showing no distinguishable differences between the two designs.
Well 2 had a maximum sand concentration of 5.0 ppg, and began conservatively with a corresponding 4.0 gallons a thousand (gpt) of HVFR. As field personnel became familiar with the product, they began to reduce concentrations to 3.5 and eventually 3.0 gpt while successfully placing all designed proppant.
As the standard hybrid pump design changes from slickwater to gel, the sand concentration increases and the friction reducer often is cut. As such, three variables are changing down hole, and changes in treatment pressure can be open to interpretation. The field personnel communicated that the HVFR system is easier to pump and optimize because of negligible changes in fluid friction as proppant and HVFR concentration are increased. Because of the chemical cost difference, number of chemicals pumped, and the ability to optimize during operations, chemical costs on well 2 were decreased by 32 percent compared with well 1.
After successful drill-out operations, both wells were brought on line within 24 hours of each other. Similar flowback strategies were used, only differing after 21 days to test well-to-well interference. At that time, well 2’s choke was opened 2/64 inches while well 1’s choke was closed 2/64 inches. After one week, well 1 was returned to match well 2. As shown in Figure 2, daily oil production began to diverge after 30 days, with well 2 producing at a higher rate. This trend continued for the first 100 days of flowback, with well 2 outperforming well 1 by 30 percent.
Second Case Study
The second field test involved a long-lateral well on the outer edges of the thinning pay zone within the Meramec that was identified as an ideal candidate to test cost-cutting technologies in an economically challenged area. The well accessed fewer than 50 feet of net pay within the landing zone, and fracture modeling software predicted the ability to access nearly the full zone with slickwater fluid, similar to the more expensive hybrid gel design (Figure 3). This helped to eliminate the question of whether the fluid could achieve optimal fracture height, and focus on fluid cost as well as regained conductivity during production.
Moreover, this well also benefitted by having several long laterals landed within the same interval in the surrounding area for production comparison purposes. As a parent well with no direct lease line offsets, this was imperative in candidate selection to calibrate the results.
This well used a different stimulation company than the previous wells, and the entire HVFR chemical suite replaced the vendor’s chemicals, as opposed to the friction reducer only. As such, the efficiencies of the system were realized immediately on surface, where the footprint was decreased by having one fluid, HVFR, take the place of chemical containers for friction reducer, gel, surface and delayed cross-linker, as well as eliminating the need for a gel hydration unit.
This well was another operational success, pumping all design stages. Likely because of the thinner pay and geological area, treating pressures were higher, resulting in more conservative HVFR loadings at 3.0 gpt. The contract with the stimulation company required a maximum proppant concentration of 4.0 ppg. This was still very cost advantageous to the previous hybrid design.
Even at higher average pressures, field personnel described the HVFR fluid as an “on-demand chemical,” in that the significant decrease in hydration time and viscosity assessment while pumping enabled them to increase loadings much quicker as pressure necessitated. Accordingly, chemical cost per stage decreased 33 percent on this HVFR well compared with previous wells treated by the same stimulation company.
After successful drill-out operations, the well was placed on standard flowback. After 30 days of production, it was outperforming its direct offsets by 62 percent on a barrel of oil equivalent a day basis, using a 20-to-1 Mcf conversion rate (Figure 4). Because of the nature of the thin reservoir, the longevity of the production will be essential to document and analyze, but this well also was deemed a success.
Third Case Study
The final case history was selected as a combination between the previous two cases. Geologically similar to the first case study, this parent well is in a thick pay zone area with consistent results in surrounding sections for reliable production comparisons. It was hoped that the well would offer another valuable data point when comparing operational efficiencies, chemical costs, and effectiveness of the HVFR during treatment and flowback. Unfortunately, the well experienced many operational issues, none of which were caused by the HVFR fluid, but influenced success nonetheless.
The well was stimulated by a third stimulation company, providing yet another cost comparison with prior wells pumped by the service provider. It also was another opportunity to pump the full chemical suite, and benefit from the smaller surface footprint. A new benefit discovered with this stimulation crew was the decrease in liquid additive pumps required at the blender on location. Prior wells had issues maintaining the high number of pumps needed to move all of the chemicals in the hybrid design. By reducing the number of chemicals in the package, fewer pumps were needed, leaving more spare pumps for substitution and maintenance efficiencies.
Additionally, the reduced number of chemicals and liquid additive pumps allowed for a tightening in chemical volume variances, leading to a further reduction in chemical costs and ability to meet chemical design more closely.
Operationally, stage-to-stage learnings supported the first two case histories, with a max proppant concentration of 5.0 ppg successfully placed with the frac fluid. A new lesson was the ability to pump efficiently at higher rates. Because of contractual constraints, the first two HVFR wells were pumped at average rates of 70 and 80 bpm, respectively. This well was able to achieve an average rate of 90 bpm. Field personnel found the HVFR more manageable in adhering to the design at higher rates, and the HVFR stages were completed faster, decreasing both the pumping charge per stage and number of days to complete the lateral. The chemical cost savings on this well averaged 38 percent.
Even with the chemical cost savings, the advantages were not fully realized because of numerous operational issues. Mechanical issues during pump-down operations left one spent gun string down hole. After the completion of the well, this string proved difficult to recover and resulted in only 10 of 32 stages being drilled out successfully and able to flow without further intervention.
The well initially produced at competitive rates, but as expected, showed an earlier decline than offsets. As such, further diagnostics are needed to evaluate the productivity of the shortened lateral. Comparing reservoir productivity and production of the well and its offsets, normalizing per productive lateral foot will allow for proper understanding of the performance of HVFR as a fracture fluid in this application. Using this information, in addition to the chemical cost savings during stimulation, generated a positive outlook on the case study, bearing the operational difficulties in mind.
Looking collectively at all three case studies, early production during the flowback period showed promising results compared with offset wells within similar rock and the fluid. Moreover, improved efficiencies by replacing multiple chemicals with one, combined with HVFR’s cost advantages, allowed for an average 34 percent reduction in chemical costs while also reducing the surface footprint, number of pumps needed, number of fluid changes during treatment, etc.
Whether judging by field operations, cost-cutting ability, or production enhancement, these initial field results illustrate HFVR technology’s potential as a fracturing fluid in the STACK play and warrant further testing and development in the field. While HVFR’s regained conductivity benefits could be favorable in both near- and long-term productive life, combining cost savings with improved early-time productivity has promoted the selection of more candidates for continual testing as the STACK Meramec play continues to develop.
Kyle Dahlgren is an asset completions engineer for the Meramec at Devon Energy. He began his career as a reservoir engineer at QEP Resources Inc. and joined Devon as a production engineer in 2012. Dahlgren holds a degree in petroleum engineering from the University of Oklahoma.
Brett Green is a field completions foreman for the Meramec at Devon Energy. Green began his career with Devon in 2014, most recently completing rotations in reservoir, drilling and completions engineering. Green holds a degree in petroleum engineering from the Colorado School of Mines.
Brandon Williams is a completion engineer at Devon Energy. Before joining Devon in 2015, he served seven years at Marathon Oil Corp. in completion, reservoir and production engineering roles in South Texas, Oklahoma and New Mexico. Williams holds a B.S. in petroleum engineering from the University of Oklahoma.
Josh Inscore is an asset completions engineer for the Meramec at Devon Energy. Before joining Devon in 2014, he served six years at Albemarle Corp. in drilling, completions and production engineering roles in South Arkansas. Inscore holds a B.S. in mechanical engineering from Arkansas Tech University.
Mark Van Domelen is vice president of technology for Downhole Chemical Solutions LLC. Before joining the company, he served for 31 years at Halliburton in technology and operations management, field engineering, supply chain, and training positions. Van Domelen’s primary areas of expertise are hydraulic fracturing and well completion. He holds a B.S. in mining engineering from the University of Wisconsin-Madison.
For other great articles about exploration, drilling, completions and production, subscribe to The American Oil & Gas Reporter and bookmark www.aogr.com.