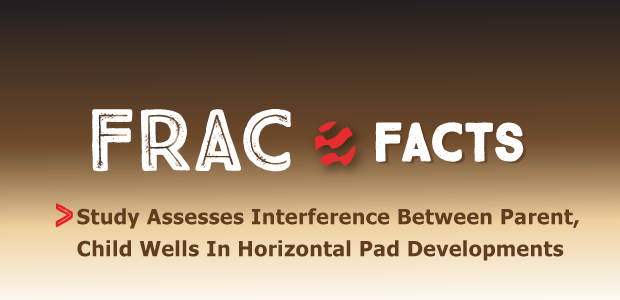
Study Assesses Interference Between Parent, Child Wells In Horizontal Pad Developments
By Ripudaman Manchanda, Prateek Bhardwaj, Jongsoo Hwang and Mukul M. Sharma
AUSTIN, TX.–Operators and service firms are acutely aware that one of the key challenges of horizontal pad well architectures is avoiding interwell interference between parent wells and newly drilled and fractured child wells during infill development. Parent wells are often the initial wells drilled to hold acreage by production. More importantly, they are the only wells on a lease that are drilled, completed and produced under virgin reservoir conditions.
Once field development starts, pad or infill wells are placed near the parent well. These child wells are drilled, completed and produced under reservoir conditions that have been altered by the parent well’s production.
Reservoir rocks form a geomechanical system that responds to both pressure and stress changes. Since reservoir pressures and stresses are coupled, changes in one can affect others. For example, long-term production from a hydraulically fractured well reduces pore pressure around the well, which changes the stresses.
In this way, production of the parent well alters the pressures and stresses around child wells. These altered reservoir conditions often are not considered when designing child well fracturing treatments, but can create subpar fractures that decrease child well productivity and estimated ultimate recovery. Child well fractures also can significantly affect parent well production.
Actually, parent well production typically benefits from the fracturing of a nearby child well in the Bakken and Haynesville plays, while parent well production typically suffers with the fracturing of a nearby child well in the Woodford, Eagle Ford and Niobrara plays. Interference between parent and child wells is observed in the form of pressure hits and microseismic data.
One strategy operators are using to mitigate child well underperformance and reduce negative interference between parent/child well fractures is to refracture parent wells before stimulating child wells. Parent well refracs (or “protection refracs” since they protect the parent well from negative child well interference) also can help improve the performance of child well fractures by preventing their asymmetric growth into depleted parts of the reservoir.
Microseismic, tracer, pressure data and other field evidence indicate that protection refracs indeed can protect parent wells from frac hits and help improve production from both parent and child wells. Field data also show that parts of parent wells that are not refractured effectively can act as attractors for child well fractures. Moreover, protection refracs can help reduce the number of wells on a pad and increase net present value.
Poroelastic Simulation
The focus of a University of Texas at Austin research project was to use a fully coupled 3-D poroelastic model to capture the effect of parent well depletion and reveal the reasons for child wells’ underperformance. The poroelastic simulation framework helps provide a mechanistic understanding of the behavior of the geomechanical changes occurring in the system during parent well production.
Specifically, reservoir-scale geomechanics software was used to model the depletion of the parent well reservoir region and calculate its impact on pressure, total stress and effective stress. Refracturing simulations of the parent well were conducted to showcase the importance of good refracturing operations in reducing the probability of frac hits from child wells. The software’s poroelastic capabilities helped in analyzing reservoir stress changes induced by depletion and refracturing. These stress changes explain observed frac hits from child wells.
The three main factors that induce interference between parent and child wells are reservoir depletion, total stress changes and effective stress changes. All these factors were quantified in the study. Modifications to parent well fracturing treatment design, refracturing treatment design and child well fracturing treatment design are suggested to improve productivity and EURs.
A symmetric sector grid was used in the 3-D reservoir-scale poroelastic simulator to model production from the parent well, with identical and equally spaced fractures along the lateral creating a symmetric system of multiple fractures. Half a fracture in the length dimension was modeled assuming a vertical plane of symmetry along the parent well’s axis. Appropriate symmetric boundary conditions were applied on the simulation mesh. The length of the mesh in the direction perpendicular to the fracture is equivalent to actual fracture spacing in the parent well. Vertical layer heterogeneity was entered into the model using values from upscaled field petrophysical data.
A higher-permeability region was assumed to exist ahead of the propped fractures in the parent well, suggesting the presence of induced unpropped (IU) fractures created during fracture stimulation. The propped part of the fracture was modeled as an infinite conductivity fracture and simulated as an internal boundary with two surfaces, whereas IU fracture regions were described as part of reservoir mesh with higher permeability. The propagated fracture region, including both propped and IU fractures–also known as the stimulated reservoir volume (SRV)–was initialized with a higher pressure and water saturation to include the impact of fracturing fluids leaking off.
Parent Well Depletion Effects
FIGURE 1
Initial Pressure State (Left) versus Depletion-Induced Pressure Changes After 400 Days of Production (Right)
Reservoir depletion causes the pressure to decrease around the fracture in the parent well (Figure 1). The pressure front is elliptical in the fracture plane with its center at the parent well. This front is observed closer to the child well in the fracture plane. Therefore, fractures from the child well potentially will propagate in a region of partial reservoir fluid depletion, reducing the child well’s hydrocarbon production. This is evident from the figure where the overlap of the dashed box and the depleted region is observed. It should be noted that this analysis is for a scenario in which the fracture created in the child well is symmetric around the child well (the dashed box in the right panel shows the possible location of a symmetric fracture in the child well) and production of the parent well has not impacted the child well fracture creation.
FIGURE 2
Initial Stresses (Left) versus Depletion-Induced Total Stresses Perpendicular to the Fracture After 400 Days of Production (Right)
The simulation results shown in Figure 2 were calculated assuming an SRV permeability that is 10 times formation permeability. At higher SRV permeability, the child well fracture would have lower performance than the parent well fracture because it would be created in a region that has been depleted by the parent well fracture. Accordingly, it is important to characterize the permeability of the SRV region.
The simulations calculated the full stress tensor in the entire domain. Figure 2 shows the total stress in the direction along the well. Before depletion started, the stress adjacent to the fracture was high because the fracture’s propped opening compressed the surrounding rock, thereby increasing stress. The layer heterogeneity in the initial stress condition also was accounted for.
Reservoir depletion changes reservoir stresses. After depletion, the stress along the parent-well plane decreased. The stress in the region between the parent and child wells also decreased. Comparing Figures 1 and 2, it is evident that the depletion-induced decrease in stress is observed farther away from the parent well than the decrease in pore pressure.
Decreasing the total stress between parent and child wells can cause the fractures created in child wells to preferentially propagate toward the parent well (Figure 3), with lower stresses in the reservoir near the parent well fracture network providing less resistance to fracture growth. Such asymmetric growth can cause child well fractures to preferentially stimulate regions of the reservoir that parent well fractures already have depleted.
This has two primary effects. First, fractures created in depleted regions of the reservoir will not produce as much as the parent well. This worsens the child well’s performance and decreases EUR. Second, child well fractures do not stimulate parts of the opposite side of the parent well that they were designed to. In order to access this unstimulated reservoir rock, new wells may have to be drilled, which drives up the cost of producing the reserves.
Figure 3 shows the impact of total stress on child well fracture geometry, including a symmetric fracture in the child well (left), an asymmetric fracture in the child well (center) and a region of the unstimulated reservoir that would have been stimulated by a symmetric fracture (gray area at right). Cooler colors depict lower pressure.
Hydraulic fracturing creates networks of fractures in the rock through both shear and tensile failure. Depletion from the parent well reduces pore pressure and increases effective stress (the stress between the grains in the rock fabric) in a compressive state. Greater effective stress increases the force required to break the bonds between the grains in the rock fabric, so depletion from the parent well should reduce the amount of failure observed in the reservoir rock.
This depletion-induced increase in effective stress complicates efforts to create a fracture network, thereby reducing the productivity of child well fractures. In the absence of a good fracture network, SRV permeability and extent also may decline, which will decrease the volume of reserves accessible by child well fractures.
Protecting Well Performance
The obvious solution to child well underperformance is to avoid creating child well fractures in regions of the reservoir that parent wells have depleted. However, spacing between wells can be a tricky optimization problem. Another way to avoid creating fractures in a depleted part of the reservoir is to alter treatment and completion designs in both parent and child wells.
Parent well stimulation designs should be modified so that the spatial extent of depletion is reduced away from the well. The child well stimulation design also should be modified to create child well fractures in the reservoir’s undepleted parts. For a defined well spacing, increasing the number of clusters per stage can create more and shorter fractures along the well to help accomplish this objective without increasing treatment cost.
One known problem of having multiple clusters in a stage is that all clusters may not contribute to production. This can be improved by using limited-entry techniques during perforation. Another option to activate multiple clusters is using far-field diverters to prevent the creation of a single dominant fracture in a stage.
If the parent well already has been stimulated and has been on production for some time, the operator can try to modify reservoir conditions to increase stresses near the parent well to prevent attracting fractures from the child well to the depleted reservoir region. As noted, one way to accomplish that is refracturing the parent well, which increases stresses in the vicinity of the parent well fracture because of stress shadow induced by the extended fracture.
Figure 4 shows the impact of refracturing on the pressures and stresses between parent and child wells. The top figure (A) is before refracturing and demonstrates the effect of only the parent well depletion, while the bottom figure (B) is after refracturing. The top left part of each figure shows the reservoir pressure profile, while the bottom left shows the difference between the stress in the direction along the fracture and in the direction perpendicular to the fracture. The bottom right shows the stresses and pressures along the dashed line in the bottom left figure and the top right shows the stresses and pressure along the parent well’s location.
During refracturing, injected fluid leaks off and increases pressure in the region around the parent well fracture. Fracture opening and propagation also increase the stresses around the fracture.
Note Syy-Sxx indicates the stress contrast between horizontal principal directions. In blue regions of Syy-Sxx, the maximum horizontal stress direction reoriented toward the direction perpendicular to the fracture face. The total stress magnitudes along the dotted line are the magnitudes along the thin solid lines in the left-side figures. This reverses the principal horizontal stress components in the region around the parent well fracture. The relative increase in the stresses and pressures along the specified axes also suggests that fracture opening and propagation reverses horizontal stresses in the region near the fractures.
This increase in stresses and pressures also is observed in the region between parent and child wells, suggesting that the fracture that propagates from the child may be restricted in growth toward the parent well because of altered stress magnitudes and principal directions.
The study results indicate that possible mitigation strategies to prevent child well underperformance include:
- Modifying the completion and treatment design of parent well fractures to reduce the spatial extent of depletion away from the parent well;
- Modifying child wells’ frac design to prevent the propagation of child well fractures in the depleted region of the reservoir; and
- Refracturing the parent well to increase stresses in the reservoir.
Based on these findings, operators can better understand reservoir-scale stress changes during depletion from existing wells, and appropriate strategies for parent-child wells can be designed to maximize the effectiveness of infill stimulations.
Ripudaman Manchanda is a research associate at the University of Texas at Austin. His focus is on developing reservoir-scale hydraulic fracturing models to predict field observations related to the geomechanics of unconventional reservoirs. He has provided consulting support to several oil and gas companies for developing completion strategies for unconventional assets, including optimizing well placement, well spacing, fracture spacing, fracture sequencing, refracturing, fluid diversion, parent-child interference analysis, infill well fracturing, and fracture design. Manchanda has a B.S. in chemical engineering from the Indian Institute of Technology, and an M.S. and a Ph.D. in petroleum engineering from the University of Texas at Austin.
Prateek Bhardwaj is a reservoir engineer with ExxonMobil, based in India. Previously, Bhardwaj worked as a research engineering scientist at the Center for Petroleum and Geosystems Engineering at The University of Texas at Austin. His interests include reservoir simulation, geomechanics, injection well performance and hydraulic fracturing. Bhardwaj holds a B.S. in petroleum engineering from the Indian School of Mines and an M.S. in petroleum engineering from The University of Texas at Austin.
Jongsoo Hwang is a post-doctoral fellow in the Center for Petroleum and Geosystems Engineering at The University of Texas at Austin. He has worked as a reservoir engineer at ConocoPhillips, and as a production engineer at Korea National Oil Corporation. Hwang’s research interests include reservoir geomechanics, fracturing, waterflooding design, formation damage analysis, gas condensate reservoirs and numerical simulations. He holds a B.S. in chemical engineering from Seoul National University and M.S. and Ph.D. degrees in petroleum engineering from the University of Texas at Austin.
Mukul M. Sharma holds the Tex Moncrief Chair in the Department of Petroleum and Geosystems Engineering at the University of Texas at Austin. His research interests include hydraulic fracturing, water management, formation damage and improved oil recovery. He is a member of the U.S. National Academy of Engineering and a former SPE distinguished lecturer. Sharma has been the recipient of the John Franklin Carll Award, the Lucas Gold Medal, the SPE Faculty Distinguished Achievement Award, the Lester C. Uren Award and the SPE Formation Evaluation Award. He holds a bachelor’s in chemical engineering from the Indian Institute of Technology and an M.S. and Ph.D. in chemical and petroleum engineering from the University of Southern California.
For other great articles about exploration, drilling, completions and production, subscribe to The American Oil & Gas Reporter and bookmark www.aogr.com.