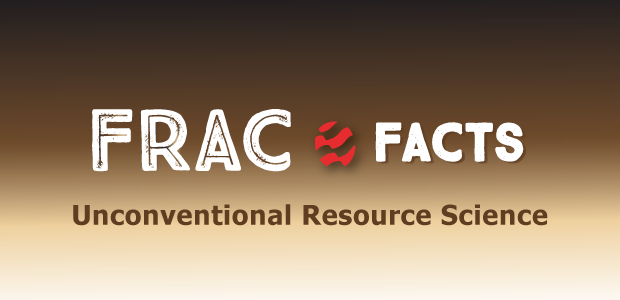
Ultralightweight Proppant Optimizes Propped Fractures To Boost Production, EUR
By Harold Brannon, Nicole Hoffman and Mark McGill
HOUSTON–The combination of extended-length horizontal laterals and high-volume hydraulic fracturing has led to daily production rates that not long ago would have been unimaginable for onshore wells. Yet, the recovery potential of unconventional oil and gas resources is yet to be fully realized. Recovery factors for unconventional wells typically are reported at less than 20% in gas shale reservoirs and less than 10% in tight oil plays.
Boosting average recovery rates is one of the grand challenges in horizontal resource plays. Increasing recovery by even a few percentage points over a well’s lifetime can be economically significant, given the large volume of reserves accessible along the lateral section. Operators are adopting a number of strategies in the quest to achieve this elusive goal. One of the most straightforward strategies is to incorporate neutrally buoyant ultralightweight proppants (ULWPs) with sand in a slickwater frac design.
ULWPs have been demonstrated to provide effective production from fracture areas that otherwise would be left unpropped and unable to contribute production with a conventional sand/slickwater frac. Production simulations illustrate that treatment designs incorporating neutrally buoyant proppant designs tailored for contemporary unconventional well stimulations deliver cumulative production increases of 30% to more than 50% compared with the typical large-volume sand/slickwater treatments.
Unfortunately, simulation results may not sufficiently lessen risk uncertainties for operators planning high-cost multistage horizontal fracs. Consequently, operators continue to initiate field trial projects in extended-length horizontal unconventional wells to validate the production simulations. Since the earliest days of hydraulic fracturing in shale reservoirs, the key to a successful frac treatment has been deploying a particle light enough to remain suspended in thin carrier fluids, small enough to be carried out to the tips of induced fractures, and strong and crush-resistant enough to remain intact (not flowed back with reservoir fluids) while temperature and pressure effects take place during production.
Particle strength at reservoir conditions is a critical characteristic of proppants, ensuring that they will provide long-lasting conductive pathways. But the stronger the proppant material, the heavier it tends to become, making it quicker to settle and more difficult to transport and effectively place deep into fractures.
Staying Suspended
Unfortunately, in the low-viscosity slickwater fluids used to fracture shale and tight oil reservoirs, sand proppants tend to sink like the proverbial rock tossed in the ocean. This phenomenon has been well documented in fracture flow simulations, and fracture modeling of slickwater treatments suggests that only 25%-30% of the created fracture area is propped to provide adequate stimulation.
Simply put, gravity causes some percentage of the sand pumped during a frac treatment to settle out of the fracturing fluid before entering the fracture network. Testing shows that as little as 12% of induced fractures are propped by sand. Even achieving a propped volume on the order of 25%-30% of the fractured area still allows most of the fracture network to close. By mixing near neutrally buoyant proppant with sand, operators can produce 80%-90% of created fractures. Because it is made of an extremely light thermoset nanocomposite bead, ULWP has a specific gravity that is approximately half that of sand. Instead of sinking and settling, it enters the fracture network and stays suspended until closure sets in and locks it in place.
The latest generation of near neutrally buoyant thermoset nanocomposite proppants exhibit an apparent specific gravity ASG of 1.06 and meets or exceeds all ISO/API requirements for reservoir environments with temperatures to 325 degrees Fahrenheit and pressures to 12,500 psi. In addition, this material has excelled in independent large-scale proppant transport testing compared with other proppant materials.
In practice, the ultralight proppant is added to the fracturing treatments at 2%-5% by weight of sand throughout the slurry stages (i.e., in a typical stage 7,500 pounds of ULWP with 250,000 pounds of sand). Fracture modeling of slickwater treatments shows this approach yields a propped fracture area of ±85% compared with ±25% using sand alone. In addition, the increased conductive fracture area provides for greater production, delivering an average 30% cumulative production uplift in the first year, representing an added 50,000 barrels or more of year-one production for a typical multizone horizontal well.
Vertical Well Applications
One of the earliest applications of ULWPs was five vertical wells completed in the San Andres Formation in Andrews County, Tx. Three of the wells were fracture stimulated using slickwater with sand and 8,000 pounds ULWP-1.05. In addition, two vertical offset wells were completed with slickwater and sand without ULWP. The 12-month cumulative production data for the wells shows that the three wells stimulated with sand and ULWP-1.05 averaged 32% more oil production than the two sand-only offset wells.
Similar results were documented in vertical wells completed in the Spraberry Formation in Texas’ Ector and Howard counties in the Permian Basin. In one application, three wells were fractured using slickwater with sand and 6,500 pounds of ULWP-1.05, and their performance was compared with five offset wells completed with slickwater and sand alone. The average cumulative production of the three ULWP-1.05 wells was 30% higher than the five wells stimulated with slickwater and sand.
The results were even more dramatic in a group of four vertical wells in the Clearfork Formation in Mitchell County, Tx., where 12-month average cumulative production from the two wells completed two using slickwater with sand and 12,000 pounds of ULWP-1.05 was 138% greater than the two offsets that used slickwater and sand alone.
In Ward County, Tx., a group of 22 vertical wells completed in the Cherry Canyon Formation included nine wells with slickwater and a relatively small volume (40,000 pounds) of ULWP-1.05 alone with no sand. The other 13 offset wells were completed with slickwater and 540,000 pounds of sand alone with no ULWP. The average 12-month cumulative production data shows that the nine wells using ULWP-1.05 outperformed the 13 sand-only offset wells by 20%, even though the offsets had pumped 13.5 times more proppant.
Horizontal Well Applications
In the Bone Spring Formation in Eddy County, N.M., a group of five horizontal wells were drilled with average lateral lengths of 4,400 feet. Two of the wells were stimulated conventionally with slickwater and sand, and three were treated with slickwater and sand with ULWP-1.05. Figure 1 shows the 12-month cumulative production history for these five Bone Spring wells. Production from the three ULWP-1.05 wells averaged 280% higher than the closest offset wells after 12 months. The cumulative production of the least-productive ULWP-1.05 horizontal wells in the area outperformed the best of the sand-only offsets by 67%. Since the lateral lengths of all these Bone Spring wells are equivalent, the differential is the same at 67% when normalized per 1,000 feet.
In the San Andres play in Andrews County, two wells with 2,000-foot laterals were fractured with slickwater and sand with ULWP-1.05. Their performance was compared with three nearby wells with lateral lengths of 3,100-6,200 feet that had been completed two years before using slickwater and sand alone. The average non-normalized 36-month cumulative production of the two ULWP horizontals was 82% greater than observed in three offsets stimulated without ULWP. When normalized per 1,000 feet of lateral, the production uplift for the ULWP-1.05 wells increases to 107%.
In Eddy County, a well with a 6,800 foot lateral was completed in the Delaware Formation and treated with slickwater and sand with ULWP-1.05. The well’s long-term (60-month) cumulative production was 24.1% greater than the three closest offset wells stimulated with slickwater and sand alone.
An extended-reach horizontal with an 11,400-foot lateral was drilled in the Mancos Shale in San Juan County, N.M., and completed using slickwater and sand with ULWP-1.05. Four similar wells to the south, each with lateral lengths of ±9,400 feet, were completed with slickwater and sand alone. After nine months (270 days) of production, the non-normalized cumulative production of the ULWP well was 38% greater than the average of the four nearby offset wells stimulated without ULWP. Normalized to 1,000 feet of lateral length, the ULWP well produced 28.6% more than the average of the four offsets after nine months.
Moving to the Bakken Shale, two wells with 10,500-foot laterals were drilled in McKenzie County, N.D. One well was stimulated with slickwater and 7.2 million pounds of sand, and the other with slickwater and 6.0 million pounds of sand with 220,000 pounds ULWP-1.05. After 120 days, the average normalized cumulative production data showed that the ULWP well had outperformed the direct offset well by 27.5%. With normalization for proppant intensity, the production uplift was 42%.
Ultralightweight proppant slurries are also proving effective in gas shales. For example, in the Marcellus Shale in northeastern Pennsylvania, three wells with 4,500-foot laterals were completed with slickwater and sand with ULWP-1.05. Similarly constructed wells on the same or adjacent pads were completed with slickwater and sand alone. Cumulative production from the three ULWP wells was 25% greater than the average observed in the three sand-only offset wells after 12 months on line, and the differential increased to 49% after 36 months (Figure 2). Notably, the wells selected for this comparison were the best-performing offsets.
Consolidated Results
The same production uplift trends emerge when the production histories from individual well applications are consolidated in a big-picture analysis. For instance, take the case of 39 vertical oil wells completed in four Permian Basin formations in a three-year window. Of these wells, 17 were fractured using ULWP-1.05 and 22 wells (each near subject ULWP wells) were completed with sand alone. The 12-month cumulative production of the ULWP wells in these formations averaged 35% higher than their offsets with no ULWP.
Looking at a group of 16 horizontal wells targeting four different tight oil formations in multiple basins, seven wells were stimulated using slickwater with sand and ULWP-1.05 and compared with nine nearby offsets with sand-only completions. Figure 3 presents the normalized combined cumulative production average of the well group by formation, and shows that the ULWP wells had 35% production uplift compared with the sand-only wells.
FIGURE 3
Consolidated Cumulative Production of ULWP versus Sand-Only Tight Oil Horizontal Completions
Comparing cumulative production of four horizontal gas wells in the Marcellus and Mancos shales stimulated with slickwater and sand with ULWP-1.05 to seven nearby offset wells completed with slickwater and sand alone shows 45% higher production on average.
With stronger commodity prices, the potential revenue capture from optimizing completion designs increases. Engineers must infer how a given design will impact rock thousands of feet below the surface. Those inferences are becoming more accurate thanks to a growing body of research that leverages new tools for analyzing the downhole environment, more sophisticated and robust models, and more realistic laboratory tests. According to most service companies, the latest research boosts initial and long-term production by helping operators improve proppant distribution and select the best chemistry.
Effective propping by mixing sand with ULWP can increase production by 25%-35% in most wells. Much of the positive long-term results are related to the durability of ULWP. Because of their design, ULWP beads should last forever down hole. Over time, they will flatten into a hockey puck shape, but typical concentrations are low enough that even after this occurs, there should still be plenty of space for hydrocarbons to flow.
Fracture models illustrate the propped fracture area of designs incorporating ULWP is improved to more than 85% of the created fracture area. Field applications in multiple reservoirs have validated the fracture models and production simulations, with first-year normalized cumulative production of wells with ULWP averaging 27% higher.
Both field applications and simulations illustrate that ULWP wells consistently outperform corresponding offsets in all categories, including production, daily output and decline rate, resulting in significant economic benefits. The long-term financial benefit of incorporating ULWP in a frac design, taking into account greater EUR potential coupled with a lower decline rate, demonstrates an increasing economic benefit year over year for the life of the well. In addition, with the ability to increase recovery in stimulation treatments, operators can increase production while reducing their carbon footprints by drilling and completing fewer wells.
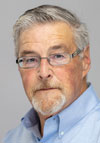
HAROLD BRANNON is the vice president of production enhancement at SUN Specialty Products. With more than four decades of experience in the upstream oil field, he has served as an academic researcher and has authored numerous publications on the topic of hydraulic fracturing and relative permeability. Brannon’s experience includes leading direct multi-disciplined professional technical staff for research, development and engineering in the global pressure-pumping business segment.
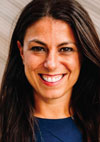
NICOLE HOFFMAN joined SUN Specialty Products in 2017 as executive, sales and marketing, specializing in production enhancement. She started in oil and gas in 2011 with CARBO, where she held various marketing, logistics and sales positions. Before that, Hoffman spent 15 years in aviation working for Pratt & Whitney, a United Technologies Company. She holds a B.S.E. in mechanical engineering from Vanderbilt University. She also has an M.B.A. in finance and international business from the University of Connecticut.
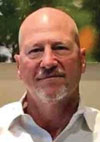
MARK MCGILL is the director of sales and marketing at PropTester Inc. He has more than two decades of oil field experience, including 19 years at Carbo, where he was promoted multiple times into mid-level management and then to the director of the Western Hemisphere. After his stint at Carbo, he also helped multiple companies to realign sales teams, expand their customer bases and launch new products. McGill is a graduate of the Ross School of Business for sales management and Harvard Business School for negotiation.
For other great articles about exploration, drilling, completions and production, subscribe to The American Oil & Gas Reporter and bookmark www.aogr.com.