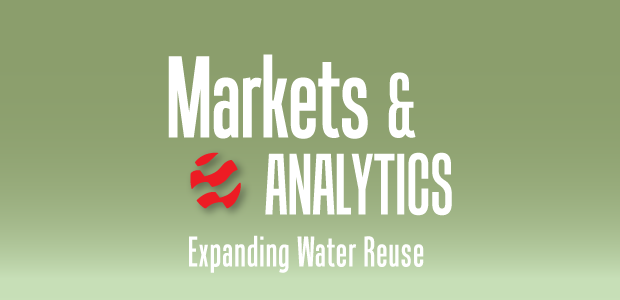
Produced Water Innovations Can Become Scarcity Game-Changers
By Jon Malone
Produced water has become oil and gas production’s largest waste stream. In North America’s most prolific region, the Permian Basin, disposal continues to be the destination for the lion’s share of produced water. There are, however, at least four reasons relying primarily on disposal is not a sustainable, long-term solution.
First, the Permian Basin essentially sits atop an ancient sea, water entrapped in the subsurface when the Permian Period came to an abrupt and cataclysmic end some 250 million years ago. As the oil and gas industry taps this subterranean sea, we can expect the amount of produced water to keep rising exponentially.
Between 2010 and 2022, disposal volumes increased sixfold. There is simply not enough disposal capacity to handle future growth from ongoing depletion and increased completion activity. According to Rystad Energy, many operators are concerned about “potential shut-ins within two-four years if matters continue along the current trajectory.” In other words, disposal constraints may become a significant factor for the industry to continue supplying needed oil and gas.
Second, the seismic activity associated with injection wells has become a top concern among regulators in several states, most recently in New Mexico and Texas. This concern has led to restrictions on disposal volumes and well permits, which seem to be growing more stringent. For example, the Texas Railroad Commission issued a notice in December 2023 stating that all new or amended saltwater disposal permits “will have a requirement to collect and report initial and periodic static bottomhole pressure measures.” This requirement will likely increase disposal costs.
Third, injecting produced water into the subsurface often causes a pressure buildup in the formations that can spread out and disrupt proximate oil and gas development. Not only does nature abhor a vacuum, it also adores equilibrium; pushing fluid into a formation without removing the same volume invariably elevates internal pressure. This rippling out of background pressure has forced several operators to install additional casing strings to manage the elevated pressures, another measure that drives up costs.
Finally, for several reasons, water itself has become a scarce commodity, even financialized and traded like gold and silver. Whether or not one welcomes this commodification, the scarcity of clean, potable water is raising alarm not only in the western United States, but also around the world. Using scarce freshwater for hydraulic fracturing and later disposing of the resulting produced water is neither sustainable nor popular with the public and political leaders.
Given this situation, a pessimist may view produced water as a cursed albatross hanging around the industry’s neck. But since the oil and gas industry thrives on transforming challenges into opportunities, it’s best to see growing water production as a challenge that can be solved with the right innovations.
Recycling In Completions
The immediate solution to the over-abundance of produced water is that operators west of the 98th meridian—dividing the United States’ arid West from its watery East—need to recycle more water in completions. It is ironic that in the Marcellus Shale play, part of the water-rich East, recycling and reusing produced water has been the norm for years thanks to the high cost of disposal in regional injection wells. Fortunately, the water-stressed West is working hard to balance the efforts.
Recycling is more sustainable than disposal, and in the Permian Basin, it’s now more affordable than transporting wastewater off site—whether by truck or pipeline—and offloading it in saltwater disposal wells. Treatment protocols and oil-skimming technologies now can economically render produced water optimal for use in completions, reducing not only wastewater but also the need for freshwater. At the same time, skimming captures additional oil that can be routed to the sales pipeline.
In terms of operational costs, the industry has surpassed the proverbial tipping point. With per-barrel costs currently ranging from $0.25 to $1.00 for disposal (or more in areas lacking infrastructure) but only $0.15 to $0.20 for reuse in completions, the economic benefit of recycling is clear.
Introducing automation into a recycling program enhances the value, reducing on-site head counts, blending chemicals more precisely and operating pumps more efficiently. Monitoring and controlling a water management system remotely also means fewer trucks on the roads and less risk of a health, safety or environmental quality incident.
The industry trend appears to reflect the economic benefits as well as the embrace of sustainability. According to Rystad Energy, the U.S. water management market is valued at $12 billion and is growing fast, with a compound annual growth rate of 10% expected through 2028. In 2023, recycled produced water met 40%-42% of the demand for frac water, up from 39% in 2021 and projected to be 45% in 2024.
Evaporation
While the economic and environmental case for reusing produced water in completions can be strong, it is not always practical. Even with pipeline networks expanding, sometimes the distance between the produced water’s source and current hydraulic fracturing operations is too great.
Evaporation offers another way to reduce reliance on SWDs, one that is especially popular in Wyoming, Colorado and Utah. However, it has limitations. The water must be pretreated to remove oils, and natural evaporation is slow and requires large ponds to store the water. It’s possible to accelerate evaporation by spraying water into the air as droplets, but that can create problems for farmers by allowing winds to deposit undesirable salts on nearby crops.
Sometimes it’s worth heating water manually rather than relying on the sun, especially at facilities with access to waste heat from compressors, turbines or other equipment. But in general, evaporation is expensive, with prices as high as $4-$8 a barrel.
Researchers at universities and companies are investigating ways to boost evaporation rates and reduce costs without putting nearby agriculture at risk, but given how much the West needs water, it’s important to investigate opportunities to reuse produced water outside the oil and gas industry.
The Road To Beneficial Reuse
The effort to repurpose produced water has broad support. For example, the U.S. Department of Energy’s Office of Fossil Energy and Carbon Management (FECM) recently announced $10 million in funding for four projects that will research and develop technologies to beneficially reuse produced water and wastewater from coal power plants for “irrigation of nonedible crops, hydrogen generation, and aquifer re-charge and recovery.”
New Mexico took a step in this direction when its governor announced in December 2023 the establishment of a “first-of-its-kind strategic water supply.” Though still in the planning phase, it’s an ambitious program to purchase treated brackish and produced waters for use in water-intensive processes associated with, for example, “creating green hydrogen, storing energy produced by wind and solar, and manufacturing electric vehicles, microchips, solar panels and wind turbines.” Texas should follow suit and establish its own strategic water supply for the beneficial reuse of produced water.
The most sustainable, long-term objective is to render produced water sufficiently clean or near-potable for agricultural and livestock use—what we could term the best of beneficial reuse. That likely will require clearing a public relations hurdle, but severe water scarcity across the Western United States is already driving this application forward.
California is the most populous state and the sole source of many specialty crops, such as almonds, artichokes and broccoli. It’s also one of the most water-stressed states in recent years. The state’s Central Valley Food Safety Panel has sponsored research into using produced water to irrigate food crops. In a 2021 white paper, the panel candidly explained that “concern that severe drought may become more common in the future has increased interest in using unconventional water sources for irrigation.”
California’s program is still in its preliminary stage of limited use in a specific region with continued testing and research, but so far, the results are promising: “There were no findings from crop sampling to indicate a food safety or public health concern related to the reuse of produced water for irrigation in this region.” The Central Valley study is supported by Duke University researchers, who “found that produced water reused for irrigation by Cawelo Water District is of comparable quality to the local groundwater, and that the majority of chemicals do not exceed irrigation or drinking water standards.”
Desalination And Mineral Extraction
Other solutions to the over-abundance of produced water are desalination and mineral extraction, two distinct processes that are often paired because the latter generally involves the former (Figure 1). Desalination of seawater has long been viable and even necessary in regions where water is scarce, such as the Middle East, but produced water poses additional challenges. With research and development accelerating over the past couple years, the hope is that new techniques will be affordable and scalable enough to significantly reduce the strain on freshwater supplies in water-stressed regions.
Thanks partly to improvements in automation and remote monitoring capabilities, the footprint and costs associated with managing produced water continue to fall. Today, it is frequently more economic to recycle produced water in completions than to send it to a saltwater disposal well.
Lastly, extracting minerals from produced water may well prove to be the Rosetta Stone with respect to monetizing what is today considered a waste stream. While mineral content varies from basin to basin, water in the Permian has been found to contain worthwhile levels of calcium, lithium, magnesium, potassium and strontium, all of which are commercially useful and needed. The FECM’s funding for water management research—which since 2021 amounts to $27 million—includes recovering critical minerals from produced water. Combining beneficial reuse of treated water with mineral recovery would be an economic win-win.
The Texas Produced Water Consortium identifies six technologies for extracting minerals from produced water: (1) reverse osmosis; (2) multistage flash evaporation; (3) multi-effect distillation; (4) mechanical vapor compression; (5) membrane distillation; and (6) thermal processes. No single technology will be the ‘one-and-all’ solution given the varied composition of produced water and the at-scale costs of extraction. But as one may expect, a race of sorts is on to improve these technologies, and the progress so far is very encouraging.
Federal funding for research is key to bringing down mineral extraction’s costs, but ultimately the burden of proof, as it were, lies with the scientists who are developing solutions in the lab and testing their efficiency and economics in the field. They have their work cut out for them, but history is on their side. It shows that with hard work, resources, ingenuity and a pressing need, people can overcome any obstacle.
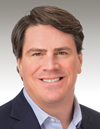
JON MALONE is director of business development at TETRA Technologies. With nearly 25 years of experience in the oil and gas industry, he has held roles in domestic and international operations management, as well as sales and commercial management. Malone holds an M.S. in geology and earth science from Ohio University and a B.S. in geology and earth science from St. Francis Xavier University in Canada.
For other great articles about exploration, drilling, completions and production, subscribe to The American Oil & Gas Reporter and bookmark www.aogr.com.