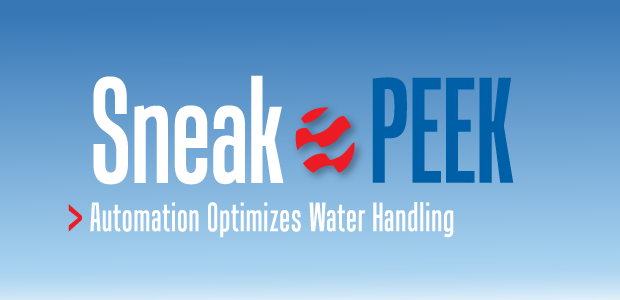
Unconventional Resource Science
Automation Optimizes Water Handling
By Jonathan Cox
LUBBOCK, TX.–Efficiency is the name of the game for oil and gas companies. By doing more for less, operators continue to find ways to operate profitably despite weak commodity prices. Technology, of course, is a major component in the ongoing drive for greater efficiency. Advanced technology allows operators to not only better understand the reservoir and how to optimize hydrocarbon production from it, but also how to improve virtually all other aspects of their business as well.
As companies look for ways to increase the economic impact of their operations, many are turning to automation to allow them to understand the big picture of their operations faster and more accurately in order to make more timely and better-informed decisions. Automation is being employed across all oil and gas workflows, but it is proving especially beneficial in improving areas of operations such as the management of produced water on a well site. Particularly in the Permian Basin, where produced water outpaces oil production on a per barrel basis, the safe and effective handling of the produced fluid stream can greatly enhance a producer’s overall ability to operate economically.
Depending on the method and distance it needs to be transported, Permian operators can pay $2-$3 to handle every barrel of produced water, with disposal and recycling costs adding to those numbers. According to the U.S. Energy Information Administration, more than 5 million barrels of crude oil and upwards of eight times that amount of water were produced every day in Texas on average through the first 10 months of 2019. Given the sheer volumes of water being lifted to surface and passing through Permian production facilities, the cost to handle it scales up quickly. Fortunately, automated solutions are creating new efficiencies in produced water management.
Mechanical valves that required field personnel to open or close with a wrench have been replaced by actuators, and actuators once controlled by an on-site terminal have been connected to a remote operating facility. Many oil and gas companies also have made the move to smart digital systems autonomously controlled by an industrial personal computer (IPC) either on site or hosted on the cloud.
Automation Benefits
Automation allows producers to have greater insights into all aspects of their operations and make critical decisions quickly. A high-level alarm on a holding tank at a remote saltwater disposal facility can start going off at any time, day or night. Traditionally, this would be addressed by on-site personnel at the time of the alarm, or during routine site visits only when the pumper makes it back to that location. With an automated system, however, preset parameters allow facilities to continue operating at maximum capacity without the risk of an environmental incident.
An added benefit of automated systems is that the pumper in charge of operations can receive notifications and make decisions independent of the facility’s parameters. For instance, he may decide to open a fill line valve on an adjacent tank with available capacity, allowing the flow of produced water being piped in to continue without incident. The pumper could then check the daily volumes for the well and begin pumping the excess produced water down hole, all without leaving the comfort of his home.
This way of managing the transportation, storage and disposal of produced fluids using automation tools is not new, but it finally is reaching the point where facilities operating without automation and/or remote control and monitoring are the outliers.
Almost all large operators working in the Permian Basin have implemented some form of automation and remote control and monitoring. While the exact solution varies based on corporate policy and the definition of “automation,” what stays the same is that operators need to remain competitive and operate on a cash-flow basis.
With institutional money spreading throughout the upstream and midstream sectors of the oil and gas industry, operators are increasingly interested in reducing operating costs and minimizing the “hands-on-equipment” management style in favor of unmanned operations controlled by IPCs and programmable logic controllers, with a small team of operations personnel comprehensively monitoring multiple facilities all at once.
The modern fluid management facility is being equipped with these digital components responsible for controlling everything from tank levels and flow rates to pump speeds and electronic ticketing systems. The smart technologies on these facilities makes real-time adjustments to operations by controlling actuators, variable frequency drives and other equipment to manage the movement of fluids. The brains controlling the smart technologies are a combination of on-site computing power and remote cloud-based edge computing. This allows facilities with limited network connectivity to operate “offline,” while still utilizing the computing power of a cloud network for advanced analytics and reporting.
Facility managers and operators are able to access the system on any computer through Web-based dashboards that display current operating conditions and data trends, and also give managers with the required permissions the ability to remotely control operations from anywhere in the world.
Increasing Complexity
The importance of automation and remote control capabilities increases with the complexity of the average fluid management facility. Equipment in the field is responsible for the operation of the facility whether it is operated by personnel on site or from a remote facility miles away. As with any industry, the increased complexity brings with it an increase in equipment failure as well as a need to calibrate or adjust that equipment to bring it back into an acceptable operating range.
The average fluid management facility operating in the most active U.S. basins (either a saltwater disposal or production facility) has 3.85 meters to manage the processes involved in fluid management, with some sites having as many as 27 meters. And as the size and complexity of new facilities increase, the number of meters increases too. Facilities built within the past two years have an average of 5.13 meters on site.
It has been observed that the average failure rate of meters is approximately 0.15 per year and they require adjustments at a rate of 0.9 per year. While these numbers seem relatively small, when one considers what these meters manage and how they impact an operator’s bottom line, the reality of the potential for erroneous readings is enough to keep operators up at night, regardless of company size.
While these meters were used almost solely for ticketing prior to the shale boom, they now function as the “cash registers” of the oil field. Any error in the accuracy or reliability of even a single meter can have a significant impact on the profitability of that facility. While the threat of lost revenue should be enough to worry operators, the need to review transaction data increases the support or back-office costs to operate, and it is a hidden waste that can be eliminated.
Adding automation and remote monitoring to a facility further reduces operating costs by reducing the need for on-site personnel. The ability to perform live, remote readings decreases the need for the on-site coordination of events and operations personnel no longer need to wait for flows to come on line. This can save the average facility eight man-hours during startup, or $331-$395 per meter, resulting in a savings of $1,290-$1,540 per site. Depending on how quickly an operator brings new sites on line, the cost savings could make a significant impact on the bottom line for even modest, organic growth.
Facility automation also reduces the need for daily readings because those values are digitally transferred to a central office, where they can be recorded on a weekly basis. By eliminating daily readings, a facility can save an average of $383-$458 per meter for a yearly per site savings of $1,497-$1,786.
One of the most valuable aspects of leveraging automation to control a remote facility is its ability to send anomaly detection alarms in real time to any device with a network connection. This automated alarm reporting capability eliminates the time lost between the triggering of an alarm and field personnel’s response to address the anomaly. The estimated yearly savings per meter are $383-$458 and $1,497-$1,786 per site.
The savings provided by automation are compounded at facilities with a large or complex geographic footprint. Automation at a facility with one or more wellheads positioned some distance away from the manifold and tank battery eliminates the need for field personnel, often working alone, to visit each piece of facility infrastructure, which saves valuable time and reduces risk.
Facility Configuration
The configuration and layout of a modern smart facility looks identical to a traditional saltwater disposal or production facility. The increased complexity comes with the introduction of the control equipment needed to automate the operations performed on a given site.
To evaluate the effectiveness of an automated solution, it is important for operators to look objectively at the operational improvements associated with an automation system and understand the full scope of the expected cost savings. The major downside of integrating automation into a new or existing facility comes with the capital expense required to install the digital equipment and run new electrical service to connect each piece of the automation puzzle to the control module and data access point.
On a new facility, the inclusion of automated systems usually increases construction costs by approximately 20%. For upgrades of an existing facility, that percentage could go up or down depending on what equipment is already in place. Either way, to accurately judge the return on that type of investment, it is necessary to look at the expected operational life of the facilities to determine if the increased operational efficiencies and resulting lower costs are worth the upfront capital investment.
The oil and gas industry always has been on the forefront of technological advances when it comes to mechanical improvements that involve heavy steel. We now are seeing the industry embrace high-tech, digital solutions to solve its complex problems. Satellites are being used to identify geographic features such as cleared pads and reservoirs to predict future operations in a basin, and fully automated fluid management systems are running autonomously based on site-specific operating parameters.
But the future of automation is not devoid of human intervention; the future of the digital oil field will use automation and other technologies to enhance oil field workers’ abilities. By enabling one operations manager or pumper to control operations of dozens of sites from his or her laptop or smart phone equipped with the latest remote control and monitoring software, the future of the industry becomes safer, more economic and more environmentally friendly.
While the technology needed to reduce costs and operate with greater efficiencies exists today, the oil field has yet to set standards around remote control, automation and various other digital technologies. But the industry is moving in a direction that is getting closer to that standard, and in doing so, it has reduced enormous amounts of waste and unnecessary cost in field operations.
The exact roadmap to the industry’s future will be determined by operators who understand how to integrate the most advanced digital technologies with highly skilled operational personnel. The digital oil field is not a humanless void of control equipment, but a place where both human and machine work as one in an effort to scale operations and improve business performance.
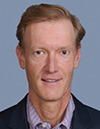
JONATHAN COX is chief operating officer of SitePro, a developer of real-time, cloud-based software solutions to optimize fluid management operations. He is responsible for the company’s operational activities, including field operations; a remote operations center; health, safety and environmental operations; automation engineering; supply chain; and project management. Cox has extensive oil and gas operational and logistical experience with a focus on crude oil and oil field wastewater operations. Prior to joining SitePro, he was chief executive officer and co-founder of Juniper Energy Solutions, an oil and gas supply chain solutions provider, and senior vice president of the transportation logistics group at NGL Energy Partners. His background also includes more than 15 years of various technology roles in different industries at the executive level, including product management, software development and systems engineering.
For other great articles about exploration, drilling, completions and production, subscribe to The American Oil & Gas Reporter and bookmark www.aogr.com.