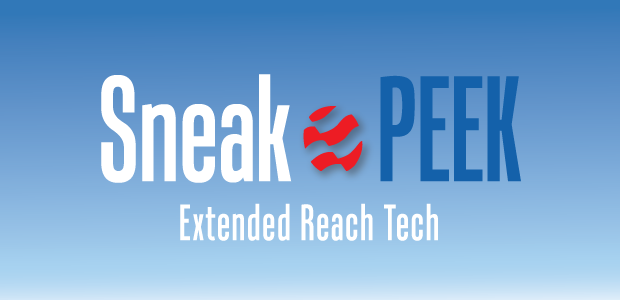
Breakthrough BHAs And Digestible Data Speed Well Construction
By Colter Cookson
To access more pay zone, operators are working with service companies to drill progressively longer laterals. Not many years ago, a two-mile lateral would have qualified as an impressive feat. But as drilling and completion technology improve, the definition of “long” stretches ever further.
Today, many operators are drilling three- or four-mile laterals. Ideally, service companies note, these wells should be drilled as smoothly as possible to ease the processes of running casing, setting plugs and pumping hydraulic fracturing fluid into the most productive zones. Of course, the well also needs to be drilled and stimulated efficiently to control costs and maximize returns.
The well construction industry has tackled that challenge with the fervor one would expect from a team only a few yards away from a Super Bowl-winning touchdown. As soon as improvements to one tool address today’s performance constraints, they look for tomorrow’s performance bottleneck and remove it.
One of the bottlenecks limiting well economics in many plays is drilling the vertical section, where bits must endure potentially damaging torque spikes generated by sudden formation changes, notes Brady Walters, the vice president of engineering for Ulterra Drilling Technologies LP. To extend bit life in these applications, he says Ulterra has invented a novel PDC cutting structure that is delivering exciting results.
“Across 775 runs and almost 3.5 million feet drilled, we are seeing ROP increases averaging between 15% and 23%,” Walters reports. “This improvement in performance comes because the wave-like cutting structure minimizes vibration, wasted energy and drilling dysfunctions.”
According to Walters, the cutting structure mitigates these issues by varying the blades’ shape. “Instead of making every blade straight or slightly curved, we give every single blade on the bit a unique shape that has been engineered so that each cutter will engage the formation in a distinct way. For example, the third cutter on one blade will interact with the rock differently than the third cutter on the other blades,” he outlines.
“We are trying to let the bit step through imperfections or changes in the rock one cutter at a time, with each blade disrupting and breaking up the pattern of the blade in front of or behind it,” Walters continues. “This leads to smoother drilling than biting into the imperfection simultaneously, which can spike reactionary forces that transmit up the drill string as vibration and potentially create resonance.”
Staggering when and how cutters contact downhole imperfections turns those spikes into gentle bumps and concentrates the energy that normally would cause vibration to instead cut rock, Walters contrasts. He notes that the concept for the cutting structure originates with a design engineer named Spencer Case. “He came up with the idea while watching YouTube videos of recycling shredders cutting through tires and other objects,” Walters recounts. “The shredders’ teeth are spaced so they each engage the tire individually, allowing the machine to shred tire after tire without locking up.”
By varying each blade’s shape, a new cutting structure concept from Ulterra Drilling Technologies LP enables PDC bits to engage the formation one cutter at a time. According to the company, this approach minimizes reactive torque and drilling dysfunctions, enabling bits to drill faster and longer.
Since pioneering the concept, Walters says Case and other Ulterra engineers have applied it to 27 bit designs. “Most of these bits fall between 7-7⁄8 and 12-1⁄4 inches in diameter and are used to drill intermediate sections and gentle tangents where bits often fail. For example, many of our runs are in vertical sections of the Delaware Basin,” he says.
“The data from the runs shows that we are getting higher ROP for the same weight on bit with an otherwise comparable design,” he reports. “Today, we are beginning to test the new concept in laterals, where the more efficient cutting structure has shown an aptitude for improving directional responsiveness and predictability that enables increased ROP and run length.”
Accelerating Engineering
Applying the new cutting structure to proven designs takes careful engineering, Walters comments. “We need to lay out the waves to minimize spots in the cutting structure where two blades may behave the same so we can introduce as much disruption as possible in the blade-to-rock interaction,” he explains.
To aid its engineers, Walters says Ulterra is improving the tools they use. “One of the most frustrating parts of engineering is inputting an idea and then waiting 30 seconds for computer feedback,” he reflects. “It’s much easier to stay in engineering mode when we barely notice delays, so we are optimizing our software’s code to get more from multithreading and other processor improvements.”
For particularly demanding tasks, such as computational fluid analysis, Ulterra is moving calculations from engineers’ computers to the cloud, Walters adds. “When engineers want to check how a particular nozzle layout will affect performance, which can take 10 or 15 minutes to calculate, they can leave the number crunching to the cloud and work on other tasks until the results are ready,” he explains.
Walters points out that a commission is updating the International Association of Drilling Contractors’ standard for dull grades. “The new standard breaks the bit into zones–cone, nose, shoulder and gage–to provide more resolution than the existing system, which only classifies cutters as inner or outer,” he says. “The standard also calls for quantifying the percentage of diamond loss on each cutter, which should help the industry diagnose and improve bits even faster.”
Walters predicts that the more precise dull grades predominantly will be generated using artificial intelligence. “Ulterra and other companies are developing mobile applications that can analyze photos of dull bits to grade them,” he mentions. “The goal is to let people in the field take photos at about the same pace as they do today, but get back a more useful report.”
For the more precise data to speed drilling improvements, Walters stresses that it must be easy to find and interpret. “For the industry to move forward as quickly as possible, we need to develop data transfer standards so operators and service companies can import dull grades and other information into internal tools and match them with well headers,” he clarifies.
Some companies already are well down that path, Walters praises. “It is powerful to see drillers with tools that allow them to check dull photos, other bit details and directional data from offsets without doing any manual research or collation,” he comments. “Having that information will help company men and others on the rig make better choices.”
Meaningful Automation
As lateral lengths have grown, so has the importance of holistic drilling approaches, suggests Wayne Symons, global product line director for directional drilling at Baker Hughes. “We all love setting ROP records, but minimizing tortuosity can be critical in long laterals to successfully running completion and production equipment,” he notes.
To minimize tortuosity, Symons recommends rotary steerable systems. “We have published several SPE papers documenting that rotary steerable systems with proportional steering deliver smooth, high-quality wellbores,” he reports. “Today, we are improving these systems’ performance by using downhole sensors to automate decisions and provide directional drillers with more accurate information.
“We still have a long way to go to fully automate the end to end well construction drilling process,” Symons muses. “However, we have made great strides on automating key areas such as reservoir navigation and wellbore hydraulics. By pairing automated systems with real-time monitoring, we can do an excellent job of managing hole cleaning and avoiding stuck pipe events and drilling dysfunctions. In many applications, this approach reduces overall spending by shortening trip times and increasing ROP.”
For efficient and reliable monitoring, Symons says the data from the rig and downhole sensors needs to be aggregated and shown in a way people can leverage it. “Clear visualizations can help data tell a story, but there is so much information coming from the rig that we also need to direct attention to the right data at the right time,” Symons says.
“In other words, we have the ability for various levels of automation, including managing by exception,” he says. “Today’s drilling software can monitor key indicators, such as torque and drag, equivalent circulating density and trip speeds. If the well starts to deviate from expectations, the system alerts the appropriate people and provides actionable information that will help them respond quickly. When running in automated mode, parameters can even be updated in closed loop.”
Thanks to improvements in cellular networks and drilling software, Symons says many aspects of drilling can be managed remotely. “Close to 90% of the wells Baker Hughes helps drill in North America involve some aspect of remote operations,” he reports. “On some, we have no employee on site. Other jobs are hybrids, with someone on site but many tasks handled remotely.
“While remote operations can reduce transportation and living costs, the true benefit is centralized expertise,” Symons stresses. “Instead of relying entirely on personal knowledge and experience, the engineers at the remote center can draw on a vast support network for any challenge. For example, if they are having trouble decoding a signal from a downhole tool, they can lean across a desk and ask a peer to double-check their interpretation. This, combined with automating numerous processes, is helping us continuously drive down the risk of lost-time incidents resulting from human error.”
The remote monitoring centers accelerate employee learning by giving them access to several mentors and exposing them to a variety of rigs and situations, Symons adds. “The employees there also appreciate that they can go home to their families when their shifts end,” he comments.
Vibrating Casing
To help operators get casing to bottom quickly and reliably, Thru Tubing Solutions offers a tool that vibrates the casing to reduce friction between it and the wellbore, notes Daniel Steelman, one of the company’s regional managers. He says the improvement to casing running speed can be striking.
“In a run earlier this year, we had a customer that managed to float the casing to 900 feet above total depth. At that point, even after filling the pipe with fluid and rotating it, progress slowed to two feet an hour,” Steelman relates. “Once the operator began pumping fluid through our tool at rates high enough to activate it, the speed jumped to 22 feet an hour. By end of the run, it hit 36 feet, which helped the casing get to bottom at a reasonable cost.”
These cement bond logs from three wells on the same pad compare different casing running options. The rightmost log shows dense cement and better zonal isolation than the middle, which has low-side channeling, or the left, which has unconsolidated cement, Thru Tubing Solutions describes. The company attributes the rightmost well’s high-quality cement partly to its casing vibration tool and notes that better zonal isolation can improve hydraulic fracturing effectiveness.
In many applications, vibrating casing eliminates the need to rotate it, which exacts a toll on both the rig and casing. “When casing rotates, collars can get overtorqued, which can deform the casing and make it hard to set plugs or get mills through the collars,” he warns. “Operators often reduce that risk by buying premium collars with higher torque ratings, but that extra cost may be unnecessary if the casing can land without rotation.”
Past runs suggest the vibration tool frequently increases wells’ production, says Jared Clifton, Thru Tubing’s international operations manager. “In the United States and abroad, we have run more than 400 tools and often see a production uplift,” he says. “We think this uplift occurs because the vibration improves the cement job’s quality and therefore zonal isolation during the frac.”
Clifton explains that the tool generates pulses within the cement that break down the surface tension between the casing and the drilling mud, dislodging the mud and allowing the cement to take its place.
“We liken the tool to the formwork vibration machines that concrete companies use as they pour sidewalk to get rid of the pockets of air, fluid and materials that otherwise may cause the cement to crumble,” Clifton says. “But in our case, the result is a denser, more consistent cement plug behind the casing. This cement has few microfractures or voids, so it directs the fluid into new rock.”
To confirm that the production uplift often associated with the vibration tool comes from more effective zonal isolation, Steelman says Thru Tubing has partnered with several operators to take cement bond logs across the lateral. “The operators saw a tremendous difference between the wells with the tool and the ones without it,” he summarizes. “In one test, an operator compared three wells on the same pad: one that paired centralizers with a chemical component to improve cement density, one that used centralizers by themselves, and one that combined centralizers with our tool.”
In cement bond logs, a lower amplitude reading indicates denser cement, Steelman notes. “In the chemically treated well with centralization, the amplitude reading averaged about 17 millivolts. With centralization only, the average fell to 10 millivolts. With our tool in a centralized string, the average was five millivolts, indicating much denser cement behind the casing. In fact, five millivolts is the target the Texas Railroad Commission has set for plugging and abandonment operations.”
Based on these tests, Steelman says many operators have made running the vibration tool alongside centralizers a standard practice. “They understand how much strong zonal isolation can help the initial completion. Some also think the dense cement will enable them to refrac the well several years later without spending money on a cement squeeze to restore zonal isolation,” he says.
Steelman describes the casing vibration tool as reliable and risk-free. “The tool has no rubber components or moving parts, so it is unlikely to fail because of internal issues, exposure to chemistries or excess temperatures,” he assures. “It can erode and lose efficiency if fluid is pumped through it too rapidly, but as long as the operator has strong fluid management, it’s a low-cost way to ensure casing gets to bottom while strengthening cement bonds and potentially increasing production.”
Tailoring Cement
As laterals extend outward, cementing is becoming more complex, reports Lucas Albrighton, director of technology at American Cementing. “As with any cement job, success depends on thorough hole cleaning, centralizing the casing, preventing fluid influx and compensating for friction,” he advises. “These challenges grow as laterals extend farther and farther. To overcome them and get the job done right, we need to do more preparatory work and planning.”
That planning includes tuning fluid rheology to the well’s mud system. “In the past, we would focus on the mud used immediately before the job,” Albrighton recalls. “Today, we consider everything that has happened during drilling since the previous casing shoe was drilled out all the way to total depth to ensure we are preparing for any potential risks.”
To show why drilling events matter, Albrighton points out that when operators trip out of a well, they frequently control formation fluid with a heavyweight pill. “The pill has different properties than the drilling mud, and it tends to collect in one place when the well is static,” he notes. “If the pill is removed by the mud once drilling resumes, its characteristics may not matter. But if part of the pill remains, we need to remove it or at least make sure it won’t interact poorly with the cement.
As drilling activity has ramped up, American Cementing has expanded its recruiting efforts across the United States. Today, the company reports it has staff from more than 30 states.
“Operators are becoming more open about sharing cement bond logs and other relevant historical data with service companies and collaborating with them to spot indicators of potential challenges,” Albrighton affirms. “That is helping cementing companies modify their products and systems for specific wells.”
Albrighton adds that it is getting easier to turn data and experiences into useful guidelines. “Today, the systems we use to manage data are easy to mine,” he characterizes. “We can find historical analogs for future wells from across every district where we operate, then try to replicate the successes and avoid the pitfalls.”
Like other parts of the oil and gas industry, cementing companies are working to shrink their carbon footprints, Albrighton reports. “Many cement manufacturers have moved to 1L cement, which has a much lower carbon footprint than traditional types,” he illustrates. “1L has the performance we need, so that change is a win-win.”
Albrighton mentions that cement companies are seeking alternatives to traditional cement additives such as fly ash, which comes from coal-fired power plants. “Because of supply chain constraints, we are exploring different formulations and constituents that would have been less attractive when standard options had shorter lead times and lower costs,” he elaborates.
Thanks to increasingly automated surface equipment, cement blends can be more precise, says Aaron James, American Cementing’s chief operating officer. “The more we automate mixers and pumps, the more consistently we hit our mixing targets and the tighter we can make chemical tolerances,” he says.
“We also have added real-time diagnostics systems to our pumps to improve maintenance and reliability,” James continues. “When an issue occurs, we can use the real-time wear analysis to figure out which components experienced excessive wear and look for solutions rather than merely slapping in a new part and heading out to the next job.”
Recruiting People
Although automation capabilities will continue to expand, James says cementing always will require human involvement. “Since we began ramping up activity in 2021, getting people has been a challenge,” he assesses. “To compete with other industries for skilled workers, we have had to adjust our compensation. In the long run, that is saving us money by reducing turnover and the costs associated with training new people.”
With retailers such as Walmart advertising higher pay than many oil field companies, American Cementing must be creative to attract the right people, James allows. “Instead of requiring employees to be local to our districts, we have implemented flexible schedules and broadened our recruiting strategies across the entire country,” he says. “Today, we have employees rotating in from more than 30 states.”
Noting that 70% of American Cementing’s workers require a commercial driver’s license, James says the company frequently hires people without CDLs and sends them to schools for training. The company also offers retention bonuses and recruiting bonuses that encourage employees to recruit friends they will enjoy working alongside.
“We have had employees leave for jobs at Walmart, Frito-Lay or PepsiCo that pay a higher hourly wage only to return in two weeks or a month,” he recounts. “After seeing a few paychecks, many people realize they like the chance to work overtime and make extra money.”
James suggests that American Cementing’s draw comes in part from the many people on its staff who have been in the industry for a couple decades. “For new employees who have only worked in industries where the paycheck is all that matters, seeing their coworkers’ commitment and comradery can be eye-opening,” he reflects. “They start to take pride in supporting the American energy industry and appreciate that it supports them and their family.”
Leveraging Existing Data
The data operators routinely collect during drilling holds clues to solving the never-ending question “what is the best way to complete this well?” advises Jason Glascock, lead reservoir adviser for Drill2Frac. “We can use mechanical specific energy, which is calculated from typical diagnostic information, including weight on bit, ROP and torque, to determine how much energy it takes to drill through the rock across the lateral and infer its confined compressive strength,” he reports.
These strength ratings have several completion applications. “The most basic is identifying which stages have unusually hard rock or exceptional heterogeneity, to proactively assess potential completion hazards,” Glascock begins. “Operators use this insight to predict which stages will have anomalous treatment responses and understand why any anomalies occur, which helps the completion crew put contingency plans in place and spot warning signs early.
By analyzing readily-available drilling data, Drill2Frac can quantify rock strength throughout a lateral. The company says many operators leverage this information to anticipate completion hazards and to place stages and clusters in similar rock, which improves fluid distribution.
“For many customers, the data is used to place stage boundaries according to the near-wellbore rock to decrease the level of heterogeneity within each stage. Others go a step further and place the clusters within each stage to be in like rock,” Glascock says. “The goal is to create a situation where it takes the same amount of energy to initiate fractures throughout a stage, resulting in more evenly distributed fluid between clusters.”
Operators who use rock strength to place stages and clusters often see lower treatment pressures and fewer screen-outs, Glascock reports. “One operator went from three-four screen-outs on every well to zero once it started placing clusters in similar rock strength.” he illustrates.Drill2Frac’s process also can significantly decrease the risk of frac hits, Glascock adds. “When a fracture network is depleted and a child well intersects that depletion, it takes more energy to drill the rock,” he explains. “By looking for anomalous spikes in rock strength and other drilling data signature variances, we can see where a new well has intersected existing localized depletion and hydraulic stimulation is highly likely to immediately connect to, and communicate with, the existing offset producing well.”
Based on comparisons using additional data to validate depleted fracture identification results, Glascock estimates that the process identifies depleted fractures with 87% accuracy.
Once an operator knows the location of a potential depleted fracture, it can utilize the data to determine what best fits current operations. Some operators watch for communication as they frac the stages with identified existing depletion, and stop pumping if it occurs, while others move their cluster location to avoid the existing fracture network.
“How much space operators put between the existing depletion in the new wellbore and the planned hydraulic fractures will vary based on their experience, risk tolerance and supporting contextual knowledge; some use 30 feet and some as much 100,” Glascock says. “One operator that capped the space gap at 40 feet eliminated frac hits in areas where it used to see multiple immediate interactions during every infill well completion.
“Even with implementing gaps, the newly initiated fracture might eventually connect to the existing fracture networks,” Glascock acknowledges. “However, the longer that takes, the more stimulated rock volume the completion will create.”
In addition to guiding initial completions, Glascock says rock strength can help operators evaluate refrac candidates. “By looking at how rock strength varies along the lateral and comparing it to the as-pumped completion design, we can simulate how the frac fluid distributed between clusters during the initial treatment, then highlight understimulated areas of the well,” he says. “When we do that across a field, the operator can best determine which wells are the low-hanging fruit where a refrac is most likely to deliver impressive returns.”
Ensuring Accuracy
Analyzing drilling data from a well usually takes about 24 man-hours, Glascock reports. “Standard drilling MSE embodies drilling efficiency artifacts and the strength of the rock,” he explains. “To isolate the rock’s strength, we have to clean up the raw drilling data to filter out noise and account for changes caused by drilling artifacts and operations.”
Those changes often come from routine events such as swapping bottom-hole assemblies or varying the mud’s viscosity, but also include less common events. “For example, if a mud pump goes down and gets replaced by a less efficient backup, the reported flow rate will often stay the same even though the actual flow rate has dropped. Our process accounts for this change,” he illustrates.
The output’s resolution is between one and three feet, depending on the quality of the drilling data, Glascock mentions. He says the results match closely with rock characteristics inferred through other measurements, such as petrophysical logs and fiber optics.
“To validate our data and results of our applications, we have executed numerous blind studies,” he assures. “Typically, the operator will send us data on a well it has studied using other techniques. This allows the operator to evaluate how our data can enhance what it already knows and add efficiency to its current operations.”
To get even more from the data, Glascock says Drill2Frac continues to refine its internal tools to speed up processing while migrating data and calculations to the cloud. “Our goal is to enable operators to pull mass quantities of their well data from our system, import it into their software, and conduct large-scale, field-level analyses more efficiently,” he outlines.
For other great articles about exploration, drilling, completions and production, subscribe to The American Oil & Gas Reporter and bookmark www.aogr.com.