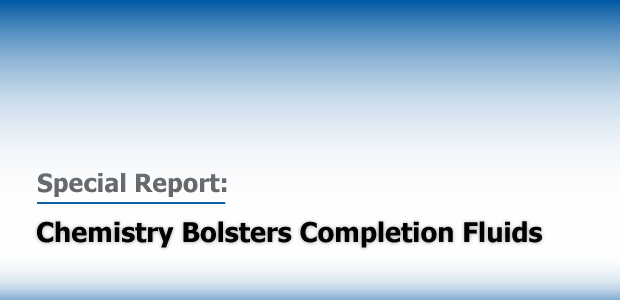
Well Stimulation & Completion Technology
Chemistry Bolsters Completion Fluids
By Colter Cookson
Engineers who design completion fluids must balance two competing goals: the desire to keep chemical costs as low as possible and the need to ensure fluids have the desired characteristics. Using laboratory tests, previous results and sound theories, they work to identify the chemical mix that will provide the desired performance at the lowest total cost.
As the industry learns more about how chemicals behave down hole, and as chemical manufacturers invent improved solutions to meet changing requirements, the number of tools at engineers’ disposal continues to grow. The latest additions include more efficient high-viscosity friction reducers and surfactants, as well as a versatile sodium silicate monomer and solid chemical carriers that gradually release scale, corrosion and paraffin inhibitors down hole.
Qi Qu, vice president of research and innovation for oil and gas for Solvay Novecare, says today’s completion fluids must be more robust than ever. “As operators move toward longer laterals, the fluids have to endure greater physical and mechanical stress,” he notes. “They also need to carry proppant longer distances.”
Because there is a direct correlation between initial hydrocarbon production and proppant intensity, the amount of proppant that completion fluids must transport through formations continues to rise, Qu adds. “To carry the proppant, operators could increase the amount of fluid they pump, but that is expensive and inefficient. Instead, they generally viscosify the fluid so it can keep more proppant in suspension for longer. This has allowed them to gradually increase proppant loading from one-half to one pound per gallon to two, three or sometimes even four pounds per gallon.”
Rather than using cross-linked gels or guar to achieve the necessary viscosity, operators frequently rely on synthetic polymers that act as both friction reducers and gelling agents. Qu says these high-viscosity friction reducer (HVFR) polymers must be efficient, versatile and easy to break.
“HVFRs face many challenges,” he comments. “One of the biggest is effectively generating viscosity in produced water, which often is recycled for use in completion fluids. Even after treatment, most produced water has high total dissolved solid levels. Maintaining viscosity is difficult once TDS levels reach 10,000-15,000 parts per million.”
Qu says Solvay is conducting research to develop more efficient and reliable HVFRs and other chemical solutions. “Our research center in The Woodlands, Tx., has the ability to synthesize new chemicals and test their characteristics, including their ability to reduce friction and improve proppant transport. This helps us create and evaluate new formulations quickly,” he says.
“Our goal is to deliver the most efficient proppant transport solution to the industry,” Qu describes. “In addition, we want to make sure the product works well in both high and low-TDS water. Fracturing water quality can vary dramatically within the same well and from well to well, so flexibility is needed to keep fluid design and logistics as simple as possible.
“Proppant transport solutions also need to break down quickly and leave almost nothing behind,” Qu continues. “This is becoming more important as the industry moves to smaller and smaller sand, replacing traditional 20/40 mesh with 40/70 and 100 mesh. These smaller sands create flow paths that are harder to clean and more likely to plug.”
As it refines its high-viscosity friction reducers, Qu says Solvay is looking for additional ways to optimize proppant placement. “We are developing a new family of chemistries that is changing the conventional view of how effectively a given viscosity fluid can carry proppant under downhole conditions,” he relates. “This will allow operators to increase the propped surface area without increasing proppant intensity, giving them another way to raise production.”
Flowback Surfactants
Qu reports Solvay has developed a suite of flowback surfactants, including an environmentally-friendly formulation that is compatible with any type of frac fluid.
“These surfactants are a step forward from traditional alternatives, which are designed primarily to help fracturing fluid return to the wellbore,” he says. “While the new surfactants retain that capability, core flood testing shows they also significantly increase hydrocarbon production rates across different pressures. This occurs because we have optimized surfactant properties that are critical to production, including surface tension, interfacial tension and contact angle.”
To ensure that completion fluids can handle rising proppant intensities, Solvay reports it is developing more efficient high-viscosity friction reducers. These new products work well in produced water and break easily, the company says.
The company also is investigating new techniques to release chemicals gradually down hole to extend the effective lives of scale, corrosion and paraffin inhibitors, Qu reports. “For example, we are developing a long-lasting paraffin inhibitor that is compatible with most water-based completion fluids,” he says. “It should last a year or longer down hole, greatly reducing the need for separate chemical treatments.”
Turning to Solvay’s cementing innovations, Qu says the company is researching cement formulations that minimize fluid loss in high temperature wells without compromising cement slurry viscosity characteristics. “We have had great success with first-generation formulations, and we are refining those to increase efficiency and flexibility,” he concludes.
Surfactant Evaluation
Surfactants have the potential to significantly increase recovery factors, says Larry Tietjen, president of Verde, a Midland-based chemical company. “An effective surfactant will imbibe into the formation and change it from oil-wet to water-wet. This will separate the oil from the formation, and allow it to flow more easily into the wellbore,” he explains.
Getting beyond the formation's surface is critical to the surfactant’s long-term effectiveness, Tietjen emphasizes. “Unfortunately, many of the surfactants commonly used are based on solvents. They clean the formation’s surface and allow the oil there to flow more quickly but rarely get beyond the surface to mobilize trapped oil. As a result, these surfactants tend to increase initial production but have a limited effect on the well’s long-term performance.”
Tietjen acknowledges that solvent-based surfactants perform well in column tests but argues that these tests do a poor job of evaluating surfactants’ effectiveness. “To perform a column test, the lab grinds cuttings from the well, which destroys the porosity. Without that porosity, it is impossible to see how well the surfactant will imbibe into the formation to dislodge the oil,” he says. “The test will show how well a chemical flows through compact spaces, but that makes it more of a flowback test than a completion test.”
Tietjen adds that column tests generally are performed at 75 degrees Fahrenheit, far below the temperatures typically encountered down hole.
To develop a more accurate way to predict surfactant performance, Tietjen says, Verde worked closely with David Schechter, a petroleum engineering professor at Texas A&M University. Schechter came up with a test centered around the contact angle between an oil droplet and a rock chip that has been exposed to the surfactant.
“This test requires a chip from a core sample that is a fifth the size of a quarter, which is quite small but still larger than most cuttings,” Tietjen outlines. “The lab ages the chip for two weeks in crude oil from the well or at least the same formation, then puts the chip in an aqueous solution containing the surfactant. Finally, the lab places an oil droplet on the chip’s surface and measures the contact angle.”
Surfactants that can penetrate and water wet the formation significantly increase production. Their ability to do so can be measured using contact angle tests, Verde reports. The company says its latest surfactants (center) are able to achieve extremely low contact angles.
Without a surfactant, Tietjen says interfacial tension between the oil-wet chip and the oil droplet will cause the droplet to spread across the surface, forming a wide sphere and yielding a high contact angle. With an effective surfactant–one that water-wets the chip and reduces interfacial tension–the droplet will take on an oblong shape, with its narrow base touching the chip. The angle formed between the oil droplet’s outer slope and the chip will be acute.
According to Tietjen, the lower the angle, the more effective the surfactant. “A low angle indicates the surfactant has imbibed into the chip and rendered it water-wet,” he says. “In the field, such surfactants penetrate the formation and displace the oil from the surface so it can flow into the fracture network. Because that fracture network is water-wet, it acts as a slick, oil-repelling highway that encourages the oil to move into the wellbore, increasing production and ultimate recovery rates.”
Field trials validate that thesis, Tietjen assures. He cites a 17-month trial that compared two wells targeting the Wolfcamp formation in Howard County, Tx.: a well with a new surfactant at concentrations capable of producing 83-degree contact angles, and a direct offset that had the same lateral length, stage count and artificial lift system but employed a more traditional surfactant.
“The well with the new surfactant produced 145,000 additional barrels of oil,” Tietjen reports. “That number is impressive, but I am more excited that the gap between the wells’ cumulative production continues to widen even after 17 months.”
The surfactant has yielded similarly impressive results in 90 completions, including many targeting the Wolfcamp and Spraberry formations in West Texas and Oklahoma’s Caney formation, Tietjen says. He mentions that operators plan to deploy the surfactant in North Dakota, Colorado and Wyoming.
“We now have a second-generation version that has even lower contact angles. At a concentration of one gallon per thousand barrels of fluid, the angle has gone from 83 degrees to 57, and at two gallons per thousand barrels of fluid, it has fallen fall from 73 degrees to 50,” Tietjen reports. “The second-generation surfactant should be incredibly effective not only in initial completions, but also in restimulation jobs, frac hit protection treatments and waterfloods.”
Versatile Monomer
The more water-wet the formation, the higher the well’s recovery factor, observes Shawn Kurtz, a technical services consultant at Mako Chemicals & Services LLC. He says the ability to water-wet formations can be measured through the contact-angle tests developed by Schechter.
“With a tetrahedral sodium silicate monomer, we can achieve contact angles below 40 degrees without using a surfactant,” Kurtz says. “Schechter’s research suggests these contact angles should recover 40-50 percent of the oil in place, a substantial improvement over the 20-30 percent recoveries typically seen.”
By using a tetrahedral sodium silicate monomer from Mako Chemicals & Services LLC in stimulation fluids, operators can achieve a low contact angle between oil and the rock. The company says this low contact angle shows how effectively the monomer water wets the formation and increases recovery factors.
Kurtz says these low contact angles were achieved on chips from an area of the Eagle Ford that starts 85-90 percent oil wet. “If we can get 36-38 degree contact angles in the Eagle Ford Shale by giving the monomer time to imbibe, I am excited to think what we could accomplish by adding a strong surfactant package to speed the reaction time,” he comments.
Field trials have only reinforced Kurtz’s enthusiasm for the technology, he says. “We have applied it in 34 formations over the past year, including carbonates, shales, sands and limestones in Kansas, Oklahoma, Texas, New Mexica, Utah, Louisiana and the Southwest. The production increases range from 150 to 300 percent,” he reports.
Many of the tests have been on stripper wells, Kurtz notes. “For a well that is making two-three barrels of oil a day, we might put 50-100 gallons of the monomer downhole, follow it with 30-60 barrels of fluid and shut the well in for a week to give the monomer time to imbibe. When we re-open the well, it usually makes nine or 10 bb/d. Two months later, production starts falling, but even at the three-four month mark, it still is at six-seven bbl/d.”
In the Eagle Ford Shale, Kurtz says an operator applied the monomer while shutting in a well to protect it from a fracture hit. The treatment involved injecting 8,000 barrels of fluid, including 1,000 gallons containing the monomer at a 15 percent concentration.
“Before the well was shut in, it averaged 1.3 million cubic feet of gas and 20 barrels of fluid a day,” Kurtz recalls. “When the operator opened the well 30 days later, it came on making the same amount of gas as before. However, the liquids production jumped from 20 bbl/d to 200 bbl/d.”
Kurtz attributes that 10-fold increase in liquids production to two mechanisms. “First, when the monomer reacts with the formation, it leaves behind a silicate barrier that greatly reduces interfacial tension,” he says. “And second, the monomer removes organics from the formation, which means there is less material to plug pores and impede flow.”
In addition to removing organics, Kurtz says the chemistry minimizes corrosion and hydrogen sulfide formation. “Removing most of the organics and hiding the rest behind the silicate barrier keeps sulfate-reducing and corrosion-causing bacteria from accessing their normal food source. Instead, they cannibalize each other, reducing the need for periodic treatments,” he reports.
The chemical barrier also protects equipment from corrosion while reducing friction, Kurtz continues. “Many users have seen a significant reduction in downtime,” he comments.
Noting that the monomer’s base technology is used to treat water wells throughout the United States, Kurtz says it carries a green certification from NSF International, a public health and safety organization. “With a strong backer, we could build an NSF-certified frac line that includes production enhancers, scale and corrosion inhibitors, and clay stabilizers,” he says. “That would do wonders for the industry’s ability to address public concerns about water contamination.
“The beauty of this technology is that it can increase production, boost recovery factors and protect assets using green chemistry that is more affordable and more effective than traditional solutions,” Kurtz says. “We can adapt the silicate monomer for everything from completions to waterfloods. It really is a game changer.”
Solid Chemistries
By deploying long-lasting scale, corrosion and paraffin inhibitors in completion fluids, operators can cut the costs associated with injecting chemicals, says Dennie Martin, director of the fracture and stimulation chemical division at Energy & Environmental Services, which maintains a chemical plant in Edmond, Ok.
“Every time operators perform a scale squeeze, they have to shut the well down and pull the rods and tubing,” Martin notes. “If we can eliminate two or three squeezes from the first two or three years of the well’s life, it will provide a much greater return on investment.”
To minimize treatment costs, Martin says Energy & Environmental Services is refining and expanding its “solid chemical” technology, which transports chemicals down hole using hydrophilic solid carriers that gradually release the treatment. “These solid chemicals stay in the formation much longer than liquid versions, which often flow back quickly,” he says. “How long the solid chemicals remain effective varies with the well’s production rates, brine composition and temperature, but they generally last 18-36 months.”
These white buckets contain solid chemical carriers that can be delivered down hole during completion. Once there, they mitigate production issues by slowly releasing corrosion, scale or paraffin inhibitors. According to Energy & Environmental Services, their provider, these carriers generally last 18-36 months.
According to Martin, as much as 70 percent of the carriers’ weight is chemical. “These high concentrations often mean that a small, easily-transported treatment can do the job,” he comments.
“The solid chemicals do not need to be diluted to prevent freezing,” Martin adds. “Their gradual release can eliminate the need to travel to a site during winter, so they should do well in cold areas such as North Dakota and Wyoming.”
So far, Martin says the chemicals primarily have been used in the Permian Basin, the Mid-Continent, and South America. “One of the advantages our solid chemistries have over traditional ways to gradually release chemicals is that they can be water-soluble or oil-soluble, which means we can make paraffin inhibitors more effective,” he mentions.
Martin says that Energy & Environmental Services is testing solid chemistries to break down the polymers that build up in formations as frac fluid flows back.
Donald Lindblad, who directs the company’s production chemicals division, says solid chemicals also can be applied during the production phase. “For example, we use them to treat wells in Kansas and eastern Oklahoma,” he relates. “To do that, we put the solids down each well’s rat hole. As the well produces, these solids gradually release corrosion, scale, paraffin or hydrogen sulfide treatments, which get carried up the wellbore.
This approach allows operators to treat a well without paying drivers to bring chemical trucks on site or installing an injection pump, which can cost $1,000, Lindblad says. He describes the chemicals as a big improvement over soap sticks, which have lower concentrations and contain wax that can contribute to paraffin issues.
The solid chemicals are easy to transport, Lindblad adds. “If they spill, they can be cleaned up with a broom and dust pan. There is no need to file a report,” he says.
Recycling Produced Water
Reusing produced water in completions can reduce costs greatly, observes Mark Patton, the president of Hydrozonix LLC. He says the cost savings are becoming more significant as water treatment technologies improve and the industry refines reuse best practices.
Before produced water can be reused in completion fluids or waterfloods, it must be treated to remove bacteria, iron and sulfide. Water treatment specialist Hydrozonix recommends using ozone, a strong oxidizer that can be generated on site and degrades too quickly to interfere with friction reducers and other chemicals in the completion fluid.
“We have seen operators complete wells using 100 percent produced water, but blends with 30-50 percent produced water and 50-70 percent freshwater are more common,” he says. “More aggressive blends increase chloride levels, which can cause incompatibilities with traditional friction reducers, forcing the operator to use higher concentrations or switch to catonic friction reducers, which cost more.”
Operators need not worry that produced water fracs will be less effective than freshwater, Patton assures. “Numerous studies show that even at 100 percent, produced water is as effective as freshwater and may even slightly improve production,” he reports.
Produced water can reduce the need for clay stabilizers, Patton continues. Like the potassium chloride typically used as a clay stabilizer, the produced water’s sodium chloride content keeps clay from absorbing water and swelling, he explains.
To reuse produced water in a completion, Patton says operators need to remove oil and solids, a task most operators already perform on their produced water. Recycling also means removing bacteria, iron and sulfide, which he says can be done easily with an oxidizer.
For most applications with flows exceeding 5,000 barrels a day, Patton recommends ozone as the oxidizer of choice. “It is a strong oxidizer, so it reacts quickly with almost everything,” he says. “This allows us to verify it is working in real time, which means we can zero in on the minimum effective concentration in order to reduce costs.”
Ozone’s rapid degradation also keeps it from interfering with friction reducers and other components of the completion fluid, Patton reports. Because ozone is made on demand by passing air through an electric current, he adds, it does not carry the risks and costs associated with transporting and storing chemicals on site.
Patton points out that ozone breaks down into oxygen rather than hazardous, long-lasting byproducts associated with disinfectants such as chlorine dioxide and sodium hypochlorite (bleach). “This is a big benefit if the operator might want to sell the produced water to agricultural companies or treat it for discharge once completion activity moves away,” he comments.
“Oxygen acts as mild oxidizer, so if the produced water needs to be stored, the oxygen left behind by the ozone can help maintain water quality,” Patton says. “It is like a booster shot for the aeration systems generally used for that purpose.”
To reduce treatment costs, Patton says Hydrozonix is experimenting with ozone generators and aeration systems that create nanobubbles. “These tiny bubbles lack bigger bubbles’ ability to overcome the water’s viscosity, so instead of rising to the surface and disappearing, they stay in suspension. They also have a much larger surface area. Both these changes cause the ozone or oxygen to interact more with the water, making it more effective.”
The nanobubble systems would shrink treatment units’ size 20-30 percent and significantly reduce overall costs, Patton says. “Because the nanobubbles act like tiny ball bearings in the fluid, they might allow operators to use completion fluids with less friction reducer,” he remarks.
When the treatment systems are used to prepare water for injection into saltwater disposal wells, the reduced friction could translate into higher capacity, Patton adds.
Managing Stranded Water
Saltwater disposal wells and waterflood injections are the most common ways to handle produced water when reuse is uneconomic, Patton notes. “Because produced water often is generated far away from completion programs, that is quite common,” he says.
But, in many areas, increased activity is stressing disposal well capacity. “In the next two or three years, disposal wells may no longer be an option in those regions,” Patton predicts. “With that possibility in mind, we are looking for ways to remove TDS from produced water so it can be discharged.
In the Powder River Basin and the Eagle Ford, it is possible to remove the salts with conventional desalination membranes, but in other areas, TDS concentrations are too high for that technology to be effective. Patton says Hydrozonix is evaluating specialized membranes that should be able to handle extreme TDS levels with proper pretreatment.
“We also are investigating ways to make evaporating water more economic,” Patton says. “For example, we have developed an evaporator that runs on field gas and releases the water into the atmosphere, rather than condensing it for discharge.”
For other great articles about exploration, drilling, completions and production, subscribe to The American Oil & Gas Reporter and bookmark www.aogr.com.