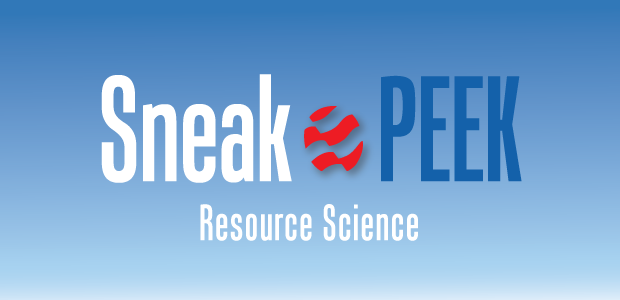
Common-Sense Insights About Proppant, Chemistry Advance Completion Design
By Colter Cookson
As oil prices rise, so does the potential revenue to be gained from optimizing completion designs. To do that, engineers must infer how a given design will affect rock thousands of feet below the surface.
Those inferences are becoming more accurate thanks to a growing body of research that leverages new tools for analyzing the downhole environment, more sophisticated and robust models, and more realistic laboratory tests. According to service companies, the latest research is boosting wells’ initial and long-term production by helping operators improve proppant distribution and select the best chemistry.
One of the most effective ways to boost completions’ effectiveness is to discard the long-held assumption that proppant travels with fluid, says Steve Baumgartner, senior engineering technical adviser at GEODynamics. “One issue is gravity, which can cause proppants to settle out,” he says. “Gravity always has been a factor, but when the industry primarily was drilling vertical wells, we could ignore it because turbulence in the casing was strong enough to keep proppant in suspension.”
Of course, Newton’s law of gravitation applies in laterals, too, where it has a greater influence on proppant behavior. Early on, most proppant stayed in suspension because completions used thick fluids, Baumgartner recalls.
“Even after we moved to slickwater fracs, engineers who looked at velocity and turbulence would predict sand would stay almost uniformly mixed with the water from the heel-most perforation to the end of the toe,” Baumgartner acknowledges. “However, physical tests and more realistic models show that gravity causes sand to sink.”
By pairing full-scale hydraulic fracturing simulations at surface with downhole studies, a coalition of operators and service companies has shown how much gravity, fluid velocity and particle size influence variations in proppant distribution across clusters. GEODynamics says these experiments have validated a physics-based model for predicting proppant distribution that can help operators increase production and reduce screen-outs.
Gravity’s role became apparent while GEODynamics was trying to figure out why an operator’s wells were not performing as expected, recounts Phil Snider, GEODynamics’ senior engineering completion adviser. “The rate and pressure data from the completion suggested the operator had done a fantastic job of injecting fluid into the wells’ clusters, but when they ran production logs, they found that only half the clusters were producing,” he says. “Since we knew the operator was putting fluid into the clusters, we thought the uneven performance stemmed from issues with proppant transport.”
To understand how proppant moves down hole, a handshake-based consortium was formed with several operators and service companies to conduct tests. This group invested about $5 million in surface tests and downhole studies. “We thought about trying to scale up experiments, but given how much pressure is involved in fracturing, it would have been difficult to get accurate results in a small plexiglass pipe,” Baumgartner says. “Instead, we built a full-scale model by perforating 200 feet of 51⁄2-inch casing at surface, then capturing the fluid and sand coming out of each cluster in tanks.”
After each test, a technician would decant the water from the tanks and measure how much sand remained. In the first test, Baumgartner reports, the toe side cluster had three times as much proppant as the heel side cluster.
“The full-scale test drove home how much gravity, fluid velocity and particle size affect proppant distribution,” he reflects. “As proppant flies past the heel side cluster, it remains distributed evenly throughout the fluid but is moving so quickly that only the proppant very near the actual perforation has a chance to exit the wellbore. But as the fluid passes each perforation, velocity decreases and sand settles out, and the area surrounding the perforation where proppant can exit increases.”
Improving Proppant Distribution
To figure out how to distribute proppant more evenly, the consortium conducted full-scale tests to evaluate several completion scenarios, Snider shares. He says these tests validated a model that uses physics to predict how much proppant each perforation will receive, given different completion strategies.
“By applying this model, we think we can help operators improve well productivity 10%-15%,” he estimates. “We do not yet have the data to verify that, but early tests show that recommendations based on the model can reduce screen-outs and other issues.”
The model considers several factors, including the casing’s size and weight, the perforating gun’s orientation, the cluster spacing, the number of perforations in each cluster, total stage length, the pump schedule and proppant size, Snider describes. He says GEODynamics will run the model for free for operators who use or are evaluating its products, which include perforating guns and charges. “Across the board, we are seeing a strong match between the model’s predictions and the results operators get in the field,” he reports.
Based on the model, Snider and Baumgartner currently recommend orienting perforating guns at three o’clock and nine o’clock. They acknowledge that conventional wisdom suggests pointing the guns straight up or down to minimize rock stresses that can inhibit fracture growth. However, the model suggests this approach leads to wide variations in proppant distribution.
“If the guns are pointing up, the heel-side clusters tend to be undertreated because the proppant velocity is too high for the proportionate share to exit,” Baumgartner clarifies. “As velocities slow, the proppant concentration on the low side of the pipe increases. The middle clusters get the right amount, but by the toe, there is so little fluid and velocity left and so much proppant remaining that we see extreme overtreatment. In fact, the proppant concentration can be two or three times as high at the toe as it is at the heel.
“If we instead point the guns down, the pattern reverses,” he contrasts. “The earlier clusters get overtreated because gravity helps sand fall toward them, but by the toe clusters, the sand has been depleted and there is no longer enough to hit the target concentration.”
The model indicates that alternating between shooting up and shooting down will level the swings in proppant distribution. “However, the distribution is even flatter with the guns at three o’clock and nine o’clock,” Baumgartner reports. “The well still will be slightly undertreated on the heel side and overtreated on the toe side, but to a lesser degree. In general, we think this approach will reduce deviation from the target concentration across clusters to plus or minus 20%.”
Snider adds, “We are a few thousand stages into treating with this orientation. We have yet to see any decrease in our ability to frac because of higher rock stresses, and there are fewer screen-outs.”
Mitigating Proppant Settling
Because gravity causes some sand to settle out of the fracturing fluid before it enters the fracture network, completions generally fail to prop the majority of the fracture network they create, warns Nicole Hoffman, the sales and marketing executive for SUN Specialty Products’ production enhancement division.
“When we run models, we have seen sand prop as little as 12% of the induced fractures,” she reports. “Most completions should manage 20% or 30%, but that still allows most of the fracture network to close.”
By mixing near neutrally-buoyant proppant (NBP) with the sand, Hoffman says, operators can produce from 80%-90% of created fractures. “Because they are made of an extremely light thermoset nanocomposite bead, NBPs have a specific gravity of 1.055, less than half that of sand (which is at 2.65). Instead of sinking as sand would, NBPs enter the fracture network and stay in suspension until closure sets in and locks them in place,” she explains.
In most wells, more effective propping can increase production 25%-35%, Hoffman reports. “Even during the pandemic, when oil prices were around $40, the production boost was strong enough that NBPs could pay for themselves in fewer than 90 days,” she says.
Fracture Conductivity (Closure) with Sand Only (left) and 4.4% NBPs (right)
Because near-neutrally-buoyant proppants have a lower specific gravity than sand, they stay in suspension and travel deeper into the fracture network, SUN Specialty Products reports. In these examples, sand propped 32% of a 372,128 square foot fracture network, while NBPs propped 94% of a 425,952 square foot fracture network. SUN says the resulting increase in conductivity delivers production uplifts that start strong and grow with time.
Sun’s NBPs debuted in 2007, Hoffman says, and the production uplift grows with time. To illustrate, she compares two Bakken wells that used NBPs with sand-only wells that were fractured around the same time using similar designs. “Approximately 100 sand-only wells we looked at had an average 20-year estimated ultimate recovery of about 660,000 barrels,” she reports. “For the NBP wells, the average 20-year EUR was 1.5 million.”
Hoffman attributes NBPs’ long-term results to their durability. “The beads will last down hole for the life of the well,” she says. “Over time, they will flatten into a hockey puck shape, but our concentrations are low enough that even after this occurs, there still will be plenty of space for hydrocarbons to move.”
NBPs can help reduce environmental impacts and safety risks by enabling operators to achieve production targets with fewer wells, Hoffman suggests. “Drilling fewer wells means not only much improved returns on capital, but fewer trucks on the road, less water use and lower carbon emissions,” she notes.
In the Permian Basin, Hoffman says Sun is working with an operator to determine whether NBPs can prop fractures that extend across benches. If so, the operator may be able to tap its reserves with fewer wells.
The newest NBPs can withstand closure pressures as high as 14,000 psi and temperatures as hot as 325-350 degrees F, with the exact temperature ceiling varying by application, Hoffman describes. “We used to sell the product in two mesh sizes: 14/40 and 30/80,” she comments. “Today, we also offer a 100-mesh version. Our goal is to keep the size consistent with the sand operators are pumping alongside the NBPs, and in many plays, 100-mesh has become quite popular.”
Custom Chemistry
To stand out in the competitive specialty chemical market, chemical suppliers need the flexibility and breadth to adapt to customers’ needs, reflects Jerry Don Sweatt, vice president of product development and technology for Smart Chemical Solutions. “We have to listen to customers and design synergistic chemical suites and application techniques that allow them to achieve their specific definition of long-term success from production, environmental awareness, and total cost of operation standpoints,” he clarifies.
“For many operators, exceeding expectations during the completion phase is no longer enough,” Sweatt adds. “They want partners who will work closely with their completion and production engineers to come up with solutions that deliver value well into the production phase.”
Through laboratory testing and partnerships with operators, Smart Chemical Solutions says it is deepening its understanding of how completion chemicals interact with various downhole environments. The company explains that tailoring chemistry to those environments to preserve the rock can minimize issues during production and ultimately improve well economics.
To help operators achieve both economic and environmental objectives, Sweatt reports that Smart Chemical Solutions is developing friction reducers with much lower hydrocarbon footprints. “These friction reducers are based on polymers that outperform conventional emulsion polymers at lower treatment rates, meaning we can put less polymer on the reservoir. This efficiency reduces costs while mitigating common issues, such as clay swelling.”
According to Sweatt, the novel friction reducer line enables customers to create the desired amount of viscosity and place more proppant without as much concern about the water salinity.
Sweatt also highlights new shale stabilizers and surfactants that work together to preserve production levels and prevent long-term issues. “These products allow operators to more consistently meet initial production goals, maintain production above type curve and avoid long-term production issues such as corrosion and biological growth,” he says.
“To formulate chemical packages that support both short- and long-term objectives more effectively, we are deepening our understanding of how chemicals interact with the reservoir during and after the completion,” Sweatt says. “Our research has solidified the fact that even wells within the same reservoir may have different needs and that a common chemical package will not always address them.”
With that truth in mind, Sweatt recommends tailoring fluid systems to each well’s mineralogy. “We are hiring skilled researchers and investing in best-in-class laboratory equipment to ensure we can analyze each well’s minerology and predict how chemicals will respond accurately,” he says. “Our goal is to develop custom fluid systems that preserve the rock’s integrity, which will optimize production rates and reduce failures during the well’s life cycle.”
For other great articles about exploration, drilling, completions and production, subscribe to The American Oil & Gas Reporter and bookmark www.aogr.com.