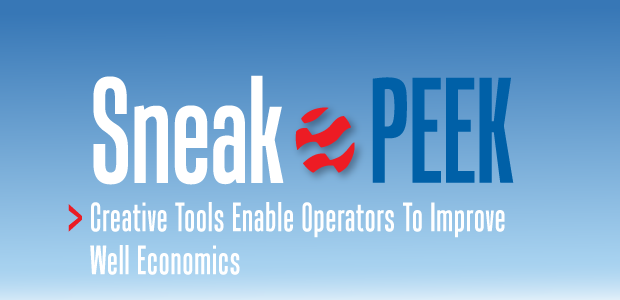
The Innovators
Creative Tools Enable Operators To Improve Well Economics
By Colter Cookson
Psychologists say constraints often breed creativity. There likely is no better showcase for that theory than the oil and gas industry, which must cope with sudden shifts in demand while delivering free cash flow, complying with strict regulations and continuously improving its environmental profile.
To handle such demands, operators and service companies look for ways to do more with their available resources, which often means deploying emerging technologies. Fortunately, there are plenty. The latest innovations leverage machine learning and new hardware to provide data for planning wells, drill faster and straighter, improve completions and simplify water management.
Adapting to geology is often the key to landing laterals in the best places and optimizing completions, says Carl Neuhaus, vice president of well data products for TGS. “When we compare production from wells in the same formation, we often see 25%-30% differences,” he reports. “Natural variability in geology accounts for some of that, but the high performers frequently are in less favorable geology. They produce well because the operator has the expertise to optimize for the rock.”
To illustrate how much geologic data can improve performance, Neuhaus points to 3-D seismic. “Even in shale plays, where operators know where the reservoir is and can drill into it reliably, 3-D seismic has considerable value,” he says. “I have seen pads where the wells drilled using 3-D seismic performed twice as well as the others.
“Where a well lands in the target matters,” he explains. “Even two laterals that are within 10-15 feet of each other can have different frac efficiency if there are limestone stringers or lamination in one but not the other.”
Modeling’s Role
To understand geology’s impact on well performance, operators often turn to multivariate statistical models based on historical data from comparable wells, Neuhaus notes. “Operators use these models because the industry’s understanding of physics is not advanced enough to accurately predict how ultratight rocks will behave and fluid will flow during hydraulic fracturing. It is usually easier and more effective to look at the statical relationships between various input variables and performance,” he says.
Building a reliable model requires high-quality data, Neuhaus stresses. “Multivariate statistics and machine learning can deliver impressive results, but they are only as powerful as the data on which they are based,” he says. “The dataset needs to be large and standardized or the resulting model often will give inaccurate predictions. In fact, it takes luck to create a model with 50% accuracy if the data is poor.”
In most machine learning applications, Neuhaus estimates that cleaning data is 80% of the work. “Take well logs,” he illustrates. “They are acquired at different times with different vendors and slight variations in downhole fluid composition. For them to yield an accurate model, the modelers need to correct for those variations and remove outliers caused by poorly-calibrated tools.”
By standardizing its well log databases, TGS has created machine learning algorithms that can predict missing measurements, Neuhaus reports. “For example, out of the 320,000 wireline logs we have in the Permian, 85% are missing a sonic velocity measurement and 80% are missing density measurements,” he details. “By looking at the partial logs and applying machine learning, we can fill in the missing measurements with 90%-95% accuracy.”
LEFT: By applying artificial intelligence to standardized well log data, such as these sonic logs, RIGHT: TGS reports it can predict measurements in other areas with accuracies exceeding 90%.
TGS has completed similar work to expand its well log libraries for unconventional basins across the United States, Neuhaus mentions.
“We are using machine learning to speed time-consuming parts of seismic processing,” he adds. “For example, when salt is in an offshore image, we have to locate the salt’s base and top, which takes a long time to do manually. By using machine learning to help, we were able to cut the time required for an average survey from 80 days to 10. These internal improvements enable our customers to make decisions sooner.”
At-Bit Steerable Systems
To increase wells’ initial and long-term production in unconventional plays, operators often want to drill a sharp curve so their lateral accesses more of the pay zone, notes Gilles Vie, RSS product champion at Schlumberger. He says the company is helping operators achieve that goal with bits that integrate steering systems.
At-bit steerable systems’ short distance between the bit and pushing mechanism enables them to drill aggressive curves that maximize wells’ exposure to the pay zone. According to Schlumberger, the systems then deliver smooth, straight laterals by leveraging sophisticated sensors and downhole automation to stay on course.
“By bringing the steering system as close as possible to the bit, at-bit steerable systems maximize the dogleg output in the curve while enhancing stability and drilling performance in the lateral,” Vie says. “While they have a higher upfront cost than mud motors or a mud motor paired with a rotary steerable system, they often eliminate the need to change the bottomhole assembly between the curve and lateral, which can reduce overall costs significantly.”
At-bit steerable systems deliver both an aggressive curve and a smooth, straight lateral through sensors and automation, Vie indicates. “They have a full direction and inclination 6-axis package placed less than 10 feet from the bit face that takes high-frequency measurements. These measurements allow the system to know when it has deviated from the intended plan,” he describes. “When that occurs, the system can correct steering settings autonomously rather than waiting for a command from the surface. This automated, closed-loop drilling mode enables the lowest possible tortuosity in long laterals.”
To show how much at-bit steerable systems can improve drilling performance, Vie cites a case study in which SRC Energy used both ABSS and conventional RSS to drill wells on a pad in the Denver-Julesburg Basin. The ABSS wells had a 20% faster rate of penetration and much smoother boreholes.
ABSS have completed 700 runs and drilled more than 6 million feet through unconventional reservoirs in North America, tallies Raul Suarez, drilling tools product manager for well construction at Schlumberger.
“At first, customers used the system primarily to drill high-dogleg curves and long, straight laterals in one run,” Suarez relates. “As the technology has built a track record, it has moved into drilling complex 3-D profiles with aggressive tangents, such as the ones we see on large pads, and extended reach wells, where minimizing tortuosity is key to ensuring the operator can run casing.”
Autonomous Drilling
Ziad Akkaoui, Schlumberger’s digital product champion for well construction, describes at-bit steerable systems as a key step in a broader effort to achieve autonomous directional drilling. “The system’s unique hardware and control system allows us to take full advantage of both surface and downhole automation,” he explains.
To ensure data can get to and from the surface reliably, Vie says Schlumberger has introduced a service that combines high-speed electromagnetic and mud pulse telemetry. This lets operators benefit from electromagnetic telemetry’s higher speed until it becomes unreliable, at which point mud pulse telemetry kicks in.
“The service should increase footage drilled each day by reducing or eliminating survey wait times,” Vie says. “Because it provides access to data from azimuthal gamma ray packages, including the ones on our at-bit steerable systems, it will also improve geosteering accuracy and operators’ ability to place wells.”
Measurements While Fracturing
To help operators optimize completions and eliminate understimulated stages that contribute little to production, Seismos has developed a device that continuously monitors stimulation during fracturing. The real-time quality control device measures fracture dimensions, stimulated near-wellbore complexity, fracture conductivity and untapped reservoir volume during pumping, details Seismos founder and Chief Executive Officer Panos Adamopoulos. He says the tool tracks stimulation by emitting acoustics through the wellbore fluid and evaluating their reflections alongside other available data.
“During the past two years, we have evolved the technology beyond merely providing measurements,” Adamopoulos says. “Using machine learning and AI-powered agents, we have created a virtual assistant that correlates the data with geology, treatment design and offsets’ fracture systems to assess whether the operator is leaving money on the table by understimulating or wasting money and creating other problems by overstimulating.”
When the system detects under- or overstimulation, it alerts the crew with a prompt, a vocal warning, an e-mail or a phone call, Adamopoulos relates. “Then it pinpoints the problem,” he says. “For example, it can say whether the issue is near-wellbore complexity or excess fracture extension. In effect, it acts like a real-time quality control agent for fracturing.”
LEFT: Seismos says its acoustic technology tracks fracture dimensions, stimulated near-wellbore complexity, fracture conductivity and untapped reservoir volume during hydraulic fracturing operations. RIGHT: A virtual agent analyzes this information in real time to highlight under- or overstimulation so crews can adjust completion parameters and improve frac consistency.
By deploying such quality control, Adamopoulos says operators can address a costly problem: Completion parameters that deliver the desired fracture network in one group of stages often cause issues in the next.
“Across basins, most stimulations follow a pattern. Four or five stages look great, but the next two or three go poorly as a result of subtle geological changes, stress buildup or other reasons. As this pattern repeats, it leaves a third or even half the lateral understimulated or overstimulated,” Adamopoulos warns. “This happens because minute changes in rock properties skew fracture behavior. By allowing operators to adapt to those changes, Seismos can greatly improve production.”
In early applications across the Eagle Ford, Permian and Haynesville, real-time measurements have helped operators increase wells’ six-month cumulative production by eight or nine barrels of oil equivalent per foot of lateral, Adamopoulos reports. “With oil prices at $40, that often translates to more than $4 million per well per year,” he calculates.
In many applications, he adds, the system saves money by showing operators how to get a better fracture network by doing less. “The AI agent correlates treatment data to fracture system properties for every type of geological profile and dynamically compares the current well to offset well systems to identify the point of diminishing returns,” Adamopoulos describes. “For example, the system can identify when to stop pumping 100 mesh proppant and how much time it will take to reach the maximum rate.”
The acoustic monitoring tool is easy to deploy, he assures. “Installing the instrument on the wellhead takes less than 30 minutes and it runs continuously at the back end without introducing any downtime or requiring any changes to operations,” Adamopoulos says. “In fact, people tell us they forget it’s there except when the system alerts them about understimulation.”
Frac Hit Detection
As part of its service, Seismos can install its device on nearby wells to watch for frac hits. Because the company looks at acoustics as well as offset pressure/strain, the data used by existing solutions, it offers much greater resolution and adds granularity to interpretations of interwell communication, Adamopoulos reports.
“Our acoustic technology takes 4,000 samples a second rather than one, 10 or 100,” he says. “Most importantly, the inherent nature of the acoustic measurement allows us to differentiate the type of communication in high detail.
“The system sees slight dilations or closures in the offset fracture network to distinguish between a tip-to-tip stress effect, a fracture bypass and a hydraulic connection,” Adamopoulos describes. “By providing information in real time, it lets the operator back off before irreversible damage to the stimulated reservoir occurs.”
Seeing Down Hole
After building and selling an industrial imaging company that developed optical imaging systems that became the industry standard for performing quality control on cardboard boxes, the founders of DarkVision Technologies Inc. partnered with an oil industry veteran to tackle a new challenge: providing ultrahigh-resolution images and measurements inside oil and gas wells.
To help operators identify well integrity issues, evaluate completions and perform fishing operations, DarkVision Technologies Inc. has developed downhole tools that capture high-resolution images through opaque fluids. In addition to perforations, DarkVision says this image shows casing damage at the same depth as a frac plug, a common problem the industry is striving to address.
“We were very familiar with optical imaging technologies, so at first, we planned to develop a next-generation camera or laser scanner for inspecting wells,” recalls Stephen Robinson, the company’s CEO. “However, the more we talked with operators, the more we understood how optical imaging’s requirement for clear fluids would fundamentally limit what we could do.”
To deliver high-resolution images and measurements even in murky fluid, DarkVision looked at tools and technologies used in the medical industry and other fields before deciding to base its platform on acoustic imaging, Robinson relates.
“Our acoustic technology can see details as small as a quarter of a millimeter, which is roughly a hundred times better than traditional acoustic imaging,” he reports. “Operators are using the technology to find well integrity issues such as corrosion, ovality, parted connections, cracks or deformation in the casing. We can also show stuck objects that need to be fished out, or diagnose problems such as scale buildup, even in opaque fluids where camera systems cannot operate.”
The imaging tools also can help evaluate completion designs, Robinson adds. “Operators routinely run our tools to measure erosion in each perforation, which is a strong indicator of proppant and fluid distribution. The erosion across each stage should be uniform if the completion design succeeded at distributing proppant evenly,” he explains. “Numerous operators now periodically deploy the tool as a feedback loop for their completions to understand their hydraulic fracturing programs’ effectiveness and efficiency.”
According to Robinson, the completion evaluation runs highlighted a previously unknown problem that has been seen across the industry. “In many wells, the casing around the frac plugs had been eroded or completely breached,” he warns. “We think the plugs’ sealing elements are eroding during the frac, which creates paths around the plugs that wash out the casing.”
The breaches often mean proppant that is intended for one area goes elsewhere, Robinson notes. “We are working with operators and service companies to put case studies together and perform surface tests so we can figure out why the erosion occurs in some wells, and with some plug types, but not others,” he says. “We are planning to present our findings in a paper at SPE ICoTA in March 2021.”
Robinson says demand for the company’s technology is growing steadily. “In addition to displacing legacy solutions, such as calipers and cameras, we are expanding the market for downhole diagnostics,” he relates. “Our tool is precise and reliable enough that operators know they will get useful information on every run, so they are willing to run it in situations where traditional solutions would not have been worth the cost.”
DarkVision is headquartered in Vancouver and based its first service office in Calgary, so much of its early work has been in Canada, Robinson notes. “During the past year, we have used our Calgary-based sales and operations teams to organize and perform jobs in the Permian, Bakken, Marcellus and Eagle Ford,” he says. “With financing from Koch Industries, we recently opened a Houston office so we can provide our full set of services to our growing U.S. client list, which now includes 35 operators.”
Managing Excess Water
When completion activity dips, operators must figure out what to do with the produced water they normally would recycle. Disposal well operators rarely have the spare capacity to handle a sudden influx without raising prices, so many operators are looking for other ways to get rid of the water, indicates Mark Patton, president of Hydrozonix LLC.
This flare from Hydrozonix controls emissions with a wet scrubber that runs on produced water. The company points out that the scrubber evaporates the water, allowing operators to cut disposal costs while improving their environmental profiles.
“In response, we have introduced a surface evaporation system that addresses surface evaporators’ traditional downside: When water is sprayed into the air, it drifts on shore and leaves behind salt that can blow onto surrounding properties and contaminate them,” Patton says. “Our new system uses spray nozzles originally developed to keep fountains in public parks from causing safety hazards by wetting sidewalks. The nozzles limit how much mist drifts and where salt can go by creating larger water droplets.
“To make sure we control the drift adequately, we put wind and humidity monitors around evaporation pits,” Patton adds. “If the wind kicks up, we can reduce the pump’s speed and the amount of spray coming off the nozzles. If we sense humidity, which keeps mist in the air longer, we do the same. If humidity is only increasing on one side of the pit, unwanted drift is occurring and the system shuts down.”
Hydrozonix’ initial evaporation modules can handle 12,000 barrels of water a day, Patton says. “They are small enough to fit into most pits with a capacity of at least 100,000 barrels without being so close to the edge that mist carries salt on shore,” he comments. “We plan to offer the modules as rentals so clients can return them once they have another outlet for their water.”
For areas with flare gas, Hydrozonix offers a flare gas combustor that evaporates water as part of its emission control system. “This provides an environment, sustainability and governance benefit by giving the flare gas an alternate use while reducing emissions,” Patton says. “We trialed the system in the Permian, but we are expecting the first permanent installation to be in the Powder River Basin because it has high disposal costs and limited water infrastructure.”
Patton points out that the surface evaporation system and flare combustor operate autonomously. “In addition to reducing labor costs, this minimizes the number of trips employees have to take to the site, eliminating the safety risks and emissions associated with driving,” he says. “We see minimizing trips as an important goal, given the industry’s growing focus on sustainability.
“At most places, that focus has yet to change field teams’ purchasing decisions. They ask almost exclusively about cost and reliability,” Patton acknowledges. “However, we have had a major company tell us it has an internal carbon tax that must be factored into cost calculations.”
At other companies, Patton says, Hydrozonix gets a positive reaction when it mentions its products’ environmental benefits. “For example, we had one client switch to our recycling systems, which treat the water with ozone that is generated on site rather than chemicals that must be trucked in, to reduce costs. When we pointed out that switching also cut the carbon footprint, the company told us that was a big topic of conversation and asked us to calculate how much.”
As it works on those calculations, Patton says Hydrozonix is expanding its client dashboards to include ESG. “Our goal is to tally every reduction in pounds of carbon dioxide operators get by adopting our technology,” he says. “That will make it easier for operators to track their progress and give them an easy way to show investors and the public how much they pay attention to emissions.”
For other great articles about exploration, drilling, completions and production, subscribe to The American Oil & Gas Reporter and bookmark www.aogr.com.