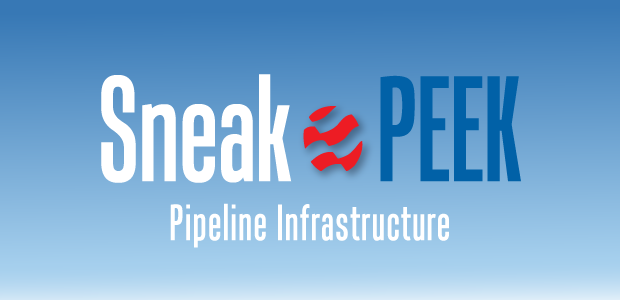
H2S Treatment Continues To Improve
By Paul Stephens
In many areas of the Permian Basin in general and the Delaware Basin in particular, hydrogen sulfide is becoming an increasingly common concern. Through complex geologic activity, many of the most promising drilling opportunities that remain in the Delaware Basin target formations that contain relatively high concentrations of the potentially deadly sour gas.
Because dealing with H2S adds extra costs, operators prioritize sweet formations when all other aspects are equal. However, the sour formations in the Delaware Basin contain so much oil that they increasingly are competing for capital as operators develop their acreage. One geologist estimated that more than half of the Delaware Basin’s future wells will produce sour gas.
Meanwhile, pipeline operators are taking a closer look at their corrosion risks and tightening their standards for H2S concentrations. Corrosion risk assessments are mandated by the Pipeline and Hazardous Materials Safety Administration’s Pipeline Safety Mega Rule, but I suspect many of the changes would be happening regardless. No one wants a pipeline rupture to expose people or the environment to H2S. Additionally, state and federal regulations are becoming stricter regarding flaring of sour natural gas.
Fortunately, the industry has gotten much better at handling it. Long ago, operators would use wood chips to absorb H2S from sour gas, plug wells with high H2S volumes or build expensive plants to treat the gas. Today, most operators rely on a far more economic solution, the chemical scavenger MEA triazine. Although it has been in use since the 1980s, triazine still is one of the best scavengers in many applications.
Alternatives’ Appeal
Unfortunately, triazine comes with a significant downside. As it reacts with H2S, it turns into sulfur-containing liquid that must be hauled away for disposal. Trucking and handling this spent triazine can be costly. In some areas, disposal well operators no longer accept it because it’s incompatible with the area’s produced water. They may be able to handle some scavenger, but if the amount exceeds the reaction stoichiometry threshold, plugging solids will form.
It does not help that spent triazine stinks. Like most chemicals, it can be handled safely with proper personal protective equipment. But for some disposal well operators, the extra revenue is not worth the hassle or risk.
That is where an expanding suite of MEA triazine alternatives steps in. In many applications, spent material from the right alternative can dissolve in produced water without causing precipitates to form. Instead of designating a separate tank in the tank battery for spent scavengers, the operator simply sends the scavenger into the produced water.
This convenience adds up to significant cost savings. Normally, a lease operator needs to check the scavenger tank and periodically call a water hauler to take the scavenger away. This service frequently costs $7-$30 a barrel, as well as compensation for driving time. At sites that process large volumes of sour gas, eliminating scavenger-specific trips can save thousands of dollars a month.
Affordable Options
With knowledge of certain chemical reactions, it’s possible to provide alternative scavengers that are soluble in produced water but still available at a cost comparable to MEA triazine.
Even so, there are situations where triazine continues to be the best solution. Sometimes the alternatives are incompatible with produced water or offer too little benefit to warrant forgoing a familiar workhorse.
In other applications, external factors favor triazine. For example, triazine endures condensate contamination more effectively than many other scavengers. Ideally, condensate will be removed before the gas enters the treatment vessel. However, pressure, temperature and volume conditions complicate the situation. When condensate persists despite the operator’s best efforts, triazine may prove to be the most reliable and economic scavenger.
As activity in the Delaware Basin increasingly focuses on formations with hydrogen sulfide challenges, bubble towers like this one will become more common. The inevitability of encountering dangerous sour gas and oil is accelerating interest in novel H2S scavengers that can simplify operations and reduce costs in many applications.
The industry standard also may cost less on sites that must treat an especially large volume of gas because it can be run at higher concentrations. Higher concentrations mean fewer gallons are required at the site, thus reducing transportation costs.
Yet in three out of four applications, it’s possible and worthwhile to switch to an alternative. This is true whether the scavenger is applied by bubble towers, mixers or pipeline atomizers.
In pipeline atomizer applications, alternatives can reduce chemical consumption. Because alternatives often have a lower molecular weight than triazine, they disperse through a gas stream more quickly and thoroughly. This dispersion increases the chance each droplet of scavenger will encounter H2S, allowing a smaller volume to remove more.
Resilient Supply Chains
Even if alternative scavengers merely performed as well as MEA triazine, chemical suppliers would have a strong reason to look at other options to keep clients’ wells on line through supply chain disruptions. When Hurricane Beryl caused flooding in Houston, it became nearly impossible to get MEA triazine. After the city recovered, the market remained tight.
Triazine’s price and scarcity also jump in response to disruptions in the supply chains for its precursors. As a case in point, a shortage began in late 2023 following a fire and a series of explosions at an ethylene oxide plant in Louisiana. The resulting lack of ethylene oxide made it more difficult to manufacture MEA and thus MEA triazine.
Chemicals exist in a global market. When something limits Europe’s access to MEA, U.S. suppliers rightly start shipping it overseas to get a better price for their product.
To mitigate market volatility, smart chemical suppliers are investing in the technical expertise, relationships and equipment necessary to source alternatives. Today, the most common alternatives for scavenging gas include hemiacetals, other reacted aldehydes and monomethylamine (MMA) triazine, which resembles MEA triazine. For treating liquids, the options include hydanteoin, glyoxal, oxazolidine and zinc carboxylates, as well as MMA triazine.
Access to these alternatives can pay huge dividends when unexpected events put operators in a bind. In July, a large midstream company reduced the H2S concentration it would allow in one of its oil pipelines, which forced several wells to shut in. Thanks largely to the alternatives—and a fleet of trucks capable of delivering thousands of gallons to various sites on short notice—those wells were back on line within two days.
A New Need
Five years ago, a similar situation would have vexed almost every chemical supplier. Until recently, I rarely got calls from producers reporting that wells had been shut in because of excess H2S in the oil. Pipelines likely have had to tighten standards to prevent corrosion as operators increasingly produce from sour formations.
Whatever the cause, it has proven the adage that necessity is the mother of invention. My team and I have spent many days and nights developing specific testing protocols, shaking bottles and field trialing samples to come up with solutions. Those solutions are evolving rapidly, with the most recent innovations representing the fifth generation of chemistry. We still have much to discover, but through a mix of laboratory testing and trial and error, we have come up with approaches that work well.
Numerous applications show that maximizing treatment effectiveness requires agitating the oil to help the scavenger contact the H2S. This translates into working with operators to install circulation pumps, in-line mixers or other equipment.
That equipment can pay for itself quickly. For one customer, installing an in-line mixer as a first step reduced chemical expenses by 40%. In more optimized facilities, effective agitation and other improvements have cut costs as much as 60%.
One of the most powerful principles for handling sour oil is Henry’s law, which observes that the solubility of a gas in any liquid depends on the pressure above that liquid. In most cases, the sourness of oil comes from sour gas that has dissolved into it. If a facility reduces pressure on that oil, the gas will be released, leaving relatively sweet oil. For this reason, some operators are installing extra vapor recovery towers at new facilities or adding them to existing sites.
As chemical suppliers gain more experience removing H2S from oil, the universe of products is being reduced to ones that are effective, affordable, and wherever possible, free of negative side effects. However, it still takes care to find the most economic solutions in a specific situation. The process should always start with testing, as a treatment’s efficiency and side effects depend on oil characteristics.
Maximizing Contact
While the right chemistry is essential to an effective treatment, how chemistry is applied frequently matters even more. In liquid applications, the gains from in-line mixers demonstrate this principle. In gas applications, one of the biggest illustrations involves contact towers.
In a contact tower, gas is bubbled through a liquid scavenger. Breaking the gas into bubbles increases the contact area and therefore the probability that any H2S in the gas will react with the scavenger. Bubbling is the most mechanically efficient way to increase contact area, which is why many glycol-based dewatering systems and amine plants use it.
Over time, towers are getting better from improvements to internal components that create gas bubbles. Continuous treatment drives even more effective change. Whether the scavenger is MEA triazine or an alternative, it eventually will exhaust its ability to react with H2S. In the past, the industry would have to wait for almost all the scavenger to be spent, then take the tower off line to drain the spent material so it could be refilled.
Whether a treatment vessel is deployed alongside twins to sweeten huge volumes, or tasked with turning a small amount of field gas into compressor fuel, it needs to be sized appropriately for the application. For effective treatment, the gas stream also must enter the vessel at a slow enough velocity that it will interact with the hydrogen sulfide scavenger as it passes through.
This dump-and-fill approach works, but the operator must halt production every time the scavenger needs to be replaced. Before that happens, the spent material accumulates in the tower, making it more difficult for H2S to react with the remaining unspent scavenger. In the worst-case scenario, the tower will send sour gas downstream.
To eliminate the downtime and risk, I generally recommend using flooded towers. Rather than allowing the spent material to accumulate, these towers use the gas to carry it out the top. A downstream separator sends the gas to the pipeline while isolating the liquid for disposal. Meanwhile, a chemical injection pump replaces the scavenger as it is used, keeping the amount at the most efficient level.
Flooded towers are extremely reliable. As an example, I helped place two in 2010 that have operated since then with minimal maintenance. They have never had to be drained, and they have never allowed sour gas to escape.
The payback for moving from dump-and-fill to continuous injection can be rapid. Recently, I had a chance to work with Midland Basin producers on two sites that processed significant volumes of sour gas. The traditional towers both had to be dumped every week, which was expensive and labor-intensive.
When calculations showed that flooded towers would reduce chemical consumption significantly, the producers agreed to put in downstream separators and switch to continuous injection. Both separators paid for themselves in 45-60 days.
A Toolbox Approach
In certain situations, it makes sense to stick with dump-and-fill. For example, if a production facility barely sees any sour gas and the tower only needs to be drained every two months, the savings from a flooded tower may not justify the extra capital cost for a separator. Other sites may lack the space for a separator.
Sometimes a site cannot accommodate a tower at all. Instead, operators will treat the gas by installing atomizers on a pipeline. The atomizers break the liquid scavenger into thousands of tiny droplets before injecting it into the gas stream. As with bubble towers, the goal is to maximize the chance of a reaction occurring by increasing surface area.
Atomizers are affordable and readily available, so they excel in applications with low H2S concentrations. The threshold varies from site to site, but I often recommend them when the concentration is below 50 parts per million. Above that, it’s frequently worth investing in a tower because bubbling gas through a liquid is much more efficient than atomizing a liquid into a gas. In fact, an atomizer will require two or three times more scavenger to deal with a given concentration of H2S.
For towers to be effective, they need to be sized for the application. The ideal size varies widely based on gas volumes, compositions and pressures, with some towers as small as 18 inches and others exceeding eight feet in diameter.
Proper sizing is only the beginning. It’s also vital for the velocity of the gas stream to fall within the expected range so the tower has time to treat the gas effectively. This range is similar whether a tower is helping fuel a pipeline compressor by treating 100 Mcf a day or supporting a large tank battery by sweetening 18 million cubic feet of gas a day.
In some applications, high production volumes and space constraints make maintaining the necessary velocity impractical. On those sites, mixers come into play. They are not as efficient as a tower, but they can accommodate higher velocities.
Math Matters
The good news is that treating sour natural gas has become a science. With basic information on the site, including expected H2S concentrations and gas volumes and pressures, a knowledgeable engineer can select a treatment system and scavenger that is almost certain to work.
That was not always the case. From the 1990s to the early 2000s, I had many opportunities to use MEA triazine in gas processing applications. It’s a fantastic chemical, but sometimes it worked and sometimes it didn’t. The misses helped launch me on a careerlong quest to figure out why scavengers that excel in most situations perform poorly in others.
I am happy to say that many of the mysteries have been solved. Lab testing and experience have revealed the strengths and weaknesses of common scavengers and application techniques, as well as the amounts necessary for anticipated H2S concentrations. With that knowledge, the most powerful tool in my arsenal is not my intuition, but my computer.
Today, the industry is grappling with a new set of treatment challenges. In addition to coming up with more economic ways to turn sour crude into sweet oil, we frequently need to remove H2S from produced water. This is particularly common when the water will be stored in an open pit long enough for H2S to bleed out and create a safety hazard.
The chemistries for treating gas, oil and water differ, but they all call for a deliberate approach. Because H2S concentrations can change with time, chemical suppliers should take regular if not constant measurements so they can adjust their recommendations and keep operators’ costs as low as possible.
Today, most of those measurements are collected by hand. However, operators and service companies are looking for ways to gather and share information digitally without compromising security or giving access to proprietary information. As those efforts bear fruit, we will be able to collaborate and solve problems even faster.
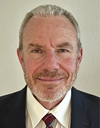
PAUL STEPHENS is senior vice president for the Permian Basin at Jacam Catalyst, the basin’s largest supplier of oil field chemicals, including alternatives to MEA triazine. He has worked with oil and gas chemistry for 41 years. Stephens joined Jacam in 2014, when its parent company, CES Energy Solutions, acquired Southwest Treating Products LLC, which he founded in 2006. Earlier in his career, Stephens worked at Multi-Chem, Catalyst Technology, Baker Performance Chemicals and Dresser Di-Chem. He holds an M.B.A. and a B.A. in chemistry from Baylor University.
For other great articles about exploration, drilling, completions and production, subscribe to The American Oil & Gas Reporter and bookmark www.aogr.com.