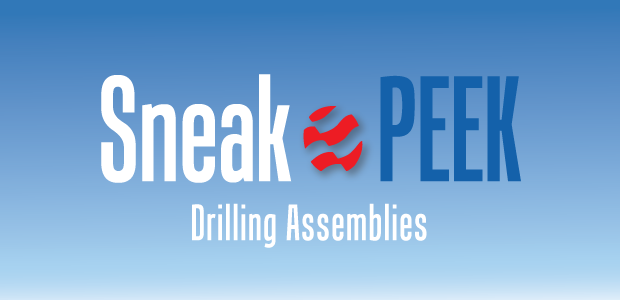
More Detailed Data Accelerates Advances In Drilling Tools, Operations
By Colter Cookson
In the four weeks following Russia’s invasion of Ukraine, Baker Hughes’ U.S. rig count gained 20 rigs. Even before that, the count was trending upward. As of March, it has risen for the past 19 months.
Despite increased activity, drilling remains an extremely competitive business. To stand out, service companies that provide drill bits, downhole tools and software report they are locked in a race to find ways to improve their products.
Historically, directional tool providers have been evaluated primarily on their reliability and cost, says Myles Woloshyn, president and chief executive officer of Turbo Drill® Industries Inc. “In the last few years, we have seen a paradigm shift based on data. The companies that get repeat business collect and analyze data to understand what their tools encounter down hole, then share that data with operators so they can be confident the tools will offer greater reliability and performance,” he reports.
“When it comes to data, volume speaks the loudest. It is no longer enough to put sensors in tools while they are being developed, then remove them to save costs,” Woloshyn stresses. “Instead, we need to collect data from every well.”
Learning from every run is key, concurs Chad Feddema, TDI’s chief technology officer. “In the past, companies often obtained data to troubleshoot problematic or particularly challenging wells,” he recalls. “That is valuable, but if we also study why a particular well went right, we can move faster in the right direction.”
TDI partnered with Sanvean® Technologies to develop sensors small enough to be embedded anywhere in the drill string, including the mud motor and drill bit. “The sensors’ main use is to understand high-frequency dynamics so we can determine why dysfunction occurs and change drilling inputs to reduce it,” outlines Steve Jones, Sanvean’s president and CEO. “Historically, shock and vibration has been measured from the measurement-while-drilling tool. These measurements are useful for seeing how much shock and vibration goes through the MWD tool, but do not give an accurate picture for the whole bottom-hole assembly.
“Placing embedded sensors in the drill bit and above the motor’s power section provides a completely different perspective,” Jones contrasts. “With high-frequency data, we can optimize input parameters, bit selection and motor design to drill wells faster, more consistently and with fewer trips.”
When drill bits experience stick-slip, mud motors may rotate backwards. Because such reverse rotation generates cyclical fatigue that can lead to premature or catastrophic failures, Turbo Drill Industries Inc. has developed a transmission with a patented secondary set of drive keys for mitigating backlash. The company says this transmission has been proven to increase motor reliability and run life.
Improving U-Joints
The sensors above the mud motor have clarified the link between stick slip and u-joint failure, says Sheldon Ritchie, TDI’s chief operating officer. “When the bit stalls, today’s high-power motors often rotate backwards, which is extremely hard on the drive components. In fact, the cyclical fatigue associated with reverse rotation is the most common cause of u-joint failure.”
When motors rotate backwards–an event called backlash–the universal joint can disengage from the driving faces only to re-engage at a high angular velocity, which subjects drive surfaces to severe shock loads. These repeated shocks can cause premature wear or catastrophic failure, Ritchie warns.
In response, the company has developed an articulated universal joint with a second set of drive keys to mitigate backlash. “These high-torque keys reduce backlash in the driveline u-joint at all angles of operation,” Ritchie says. “This is a major improvement over traditional designs, which limit backlash when they are straight but lose effectiveness once they are angled as little as two or three degrees.”
Had TDI relied solely on MWD sensors, it never would have realized the extent of backlash motors were enduring, Woloshyn reflects. “Sensor placement is important,” he says. “During multi-axis drilling dysfunctions, the bit temperature can be 100 degrees F hotter than the top end of the motor. A typical MWD sensor will read lower temperatures, so we should not rely on it to determine whether other BHA components have the right temperature ratings.”
Compound Angle Motor
According to Woloshyn, the embedded sensors also have helped TDI invent a compound angle motor that is able to drill the vertical, curve and lateral with one configuration. “We designed the motor to deliver performance approaching rotary steerable systems at a lower cost and with much greater reliability down hole,” he outlines.
Feddema says the motor achieves that goal by using both an internal and external bend. “When the motor is sliding, the compound angle comes into play and the motor acts like it has a high-bend, which lets us build aggressive curves,” he explains. “Once the motor is rotating, it acts like a low-bend motor because of the low-degree external bend. This lets us rotate much faster than a true high-bend motor without added concerns of fatigue or stress.”
In many applications, the motor has enabled operators to drill the vertical, curve and lateral sections in one run, Feddema reports. He adds that it excels in high-temperature applications that can challenge rotary steerable systems, including Haynesville Shale wells.
Deepening Dull Analysis
For drill bit providers, learning swiftly is the key to gaining market share, says Dustin Lyles, vice president of technology for Taurex™ Drill Bits. “Other drilling system components are advancing at a rapid pace. If bit companies want to fully leverage the torque from modern mud motors, or the hydraulic energy today’s mud pumps deliver, they must rapidly and continuously advance designs to accommodate changes in the drilling system or lithology,” he says.
“We need to look at every bit that comes back from a run and ask what it can tell us about how to do better next time,” Lyles clarifies. “If we had to analyze every bit manually, we could only look at roughly 2%-3% with any depth. So instead, Taurex developed and patented its automated metrology laboratory (AML) that employs a robotic 3-D scanner to quantify diamond loss on every cutter in each bit.”
The scanner captures data with accuracy to three thousandths of an inch, Lyles reports. “As a point of reference, a business card is 16 thousandths of an inch,” he says. “The scanner quantifies wear to less than a sixth of that, which means we can quantify damage invisible to the naked eye and impossible to measure with a micrometer by hand.”
Analyzing a bit and adding it to the company’s composite database takes less than 20 minutes, Lyles reports. He says the robotic scanner’s speed and precision create a digital feedback loop that makes it much easier for bit designers to see how changes in design or drilling parameters affect drilling dysfunction.
“Our composite database can tie the bit’s design attributes with the exact amount of wear on that bit, as well as data from the electronic drilling recorder (EDR) and any information the customer shares about the application, the BHA, the drilling mud, etc.,” Lyles comments. “These links mean it takes only minutes for designers and application engineers to analyze thousands of runs for trends and analogs.
“Historically, engineers who wanted to design a new bit for a specific application would spend weeks combing through dull images and application details to identify similar runs and create a story about why previous designs performed the way they did,” Lyles contrasts. “Three years ago, this research would take 40 days. Today, we can do it in a day or two.”
Actionable Insight
Automation is helping Taurex turn its relational bit performance database into meaningful insights, Lyles shares. “We are using machine learning to build models that couple EDR data with wear on the drill bit to determine what drilling dysfunctions occurred and direct us toward relationships that may explain why,” Lyles describes. “In many cases, the machine learning models see correlations that are difficult for people to notice, then rank the importance of those relationships.
This robotic drill bit scanner allows Taurex™ Drill Bits to measure cutter diamond loss and other wear quickly and precisely. By scanning every bit and combining the detailed dulls with other information, the company says it is accelerating improvements in bit design and drilling parameters.
“These correlations can be insightful,” he remarks. “For example, a bit designer may learn that a specific cutter grade, back rake scheme or profile leads to more wear in a given application.”
The models also help engineers adjust drilling plans, Lyles mentions. As an example, he says they may reveal that sliding through a specific formation correlates strongly with damage to the bit’s lower shoulder. If the operator minimizes sliding in that area, it can increase the bit’s longevity and performance.
“In addition to automating dull analysis, Taurex continuously works to increase the speed of bit design,” Lyles reports. “Instead of manually recreating the hundreds of components that go into each bit, we have developed automated templates that produce a baseline model with the desired attributes. This has shortened design time from two-three weeks in 2017 to two-three days.”
As Taurex continues to gather and analyze data, Lyles says its design accuracy is improving. “We do not have to rely as much on trial and error as we used to,” he reflects. “Because they can draw on so much data, our models are getting much better at evaluating bit designs. In fact, we are on the cusp of being able to tell customers, ‘Based on these changes, we expect a 10%-15% increase in footage drilled and a 5% increase in rate of penetration’ with a high degree of accuracy.”
Real-Time Guidance
When something goes wrong during drilling, drillers want to know immediately so they can correct it, observes Curtis Cheatham, vice president of research and development for Corva. He says the company has developed a cloud-based platform that makes spotting potential problems faster and more reliable. “By analyzing data from EDRs, MWD tools and other on-site equipment in the cloud, the platform’s apps provide situation awareness, and in some cases, make recommendations for improvement,” he explains.
One of Corva’s applications promotes procedural compliance, Cheatham mentions. “It is important that the rig goes to bottom following operator-specified procedures. If the rotary speed is too high, which can cause excessive vibration and damage, our platform can send alerts to the rig, remote centers or any user with internet access, such as drilling engineers or managers,” he describes.
The procedural compliance app also can track whether connections have been made properly and highlight when the bit deviates from the planned trajectory, Cheatham adds.
“When something unusual happens, the cloud makes it easy for the entire team to collaborate in real time,” he says. “A drilling engineer at the office, the company man on the rig and a drilling superintendent in town all can see the same data as they discuss the next step.”
Mo Kamyab, Corva’s senior technical lead for research and development, says other apps can help operators refine drilling parameters. “These apps include the Offset Driller’s Roadmap, which looks at numerous key performance indicators for each formation in offset wells to see which parameters deliver the best performance. That information can be used to optimize parameters during a bit run and plan parameters for future wells,” Kamyab outlines.
Cheatham says the apps automate as much analysis as possible to support real-time decisions. “For example, one app produces heat maps for ROP or mechanical specific energy based on drilling parameters, and color codes performance from red to yellow to green. Optimum drilling parameters are clearly indicated as the target,” he illustrates.
While the impact of the platform’s real-time and post-job insights varies from well to well, it can be substantial, Cheatham assures. “Our customer success team consistently sees a 28% increase in ROP when drillers adopt the platform,” he reports. “It takes time to fully leverage the platform’s capabilities, but many operators quickly get used to tracking connection and trip times so they can compare rigs and try to improve. On average, this process yields a 20% reduction in flat time.”
Data Quality
According to Kamyab, the platform delivers consistent results largely thanks to the effort Corva puts into data quality. “We have a 24/7 operational team that makes sure data is accurate and reaches the platform quickly enough for our real-time apps to guide decisions,” he relates.
Through Corva’s cloud-based platform, drilling teams can access valuable information in real time, including broomstick plots for hook load and torque, as well as drilling parameter recommendations based on offset data. Corva says companies that adopt the platform consistently see 28% increases in their rates of penetration.
In addition to technical issues, such as calibrating drill string weights to provide real-time torque and drag, Kamyab says the quality assurance team identifies and corrects missing or inaccurate data. For example, the team may need to call the rig crew if the hook load sensor gets re-zeroed during a run. Over time, Kamyab says the team has automated routine corrections so it can manage by exception and dive into complex issues as needed.
“One of the most exciting additions to Corva’s platform is our development center that allows users to create their own apps,” Kamyab comments. “Because we take care of importing and checking the data, external developers can focus on creating and testing algorithms.”
According to Cheatham, “Our vision is to create an app store for oil and gas that is comparable to the ones on iPhone or Android devices. Someday, we would like to see a variety of apps for use cases such as optimizing hole cleaning, predicting drilling dynamics or automating directional drilling.”
The apps users create can be restricted to their company or made available to the public at a cost or as free tools or products, Cheatham notes. As of early April, he says the platform hosts more than 80 drilling apps, more than 45 completion apps and about five geoscience apps.
The dev center also has helped Corva improve or introduce in-house apps more quickly, Cheatham adds. “In October 2021, we began developing a suite of well design apps that turn historical data into actionable insight. Using the center doubled the development team’s speed to deployment,” he relates.
“We also have created an app that compares the vibration readings from MWD tools and rotary steerable systems with vendors’ recommended thresholds and limits,” Cheatham continues. “In addition to giving drillers an easy way to consider equipment health as they make decisions, the app constrains recommendations from the drilling guidance app we are testing. If that app knows a certain differential pressure, weight on bit and RPM caused vibration to exceed the thresholds, it will eliminate those parameters from consideration in future recommendations.”
Addressing Flat Time
When engineers look for ways to improve drilling efficiency, they often focus on technical aspects such as drill bit selection, drilling parameters and BHA components, says Todd Blackford, a partner at Partners in Performance. “Getting these technical elements right is only one side of the drilling efficiency puzzle,” he argues. “The other key is speeding up ancillary activities to maximize how much of each day the rig is turning to the right.”
Re-evaluating common tasks to identify unnecessary activity can lead to huge time savings, reports Partners in Performance. For example, operators can shave days off rig moves by standardizing procedures and optimizing the order equipment arrives at the new site.
Trips constitute a common source of flat time, he observes. “As the rig is pulling pipe out of the hole and stacking it, each stand of pipe needs to be disconnected,” Blackford notes. “That process may take only 20 seconds, but on a 10,000 foot well, it adds up. Studying the rig’s tripping processes usually reveals opportunities to disconnect pipe joints faster or less often, which can halve trip times.”
Running in hole also can be accelerated, Blackford continues. As an example, he recalls a rig without a pipe stand. “As it was tripping in, the rig would pull 30 feet of pipe at a time from the catwalk,” he describes. “By adding a second catwalk, we were able to grab 60 feet at once.”
Rig moves frequently involve unnecessary work, Blackford says. “When we film moves, we see the same piece of equipment handled seven or eight times because of sequencing issues. After the crew moves the equipment to the new location, something else arrives, and the equipment is in the way, so it needs to be picked up and pushed to the side,” he illustrates.
“When we show drilling crews the videos, they often say, ‘Are you kidding me? That’s not how the rig is designed to be moved!’” Blackford comments. “No one plans to be inefficient, but it’s hard to master a process the rig only does four times a year. Because rig moves inevitably fall when some people are off tour, each crew member may be involved only once or twice a year. They rediscover parts of the process each time.”
Standardizing processes can lead to much faster rig moves, Blackford reports. “To help crews follow the standard process, we make job aids that include instructions for how to do the work and put them on site,” he says. “Companies with enough active rigs also may form a team that is dedicated to planning moves and helping rig foremen manage them.”
Efficient rig moves require coordination between the drilling contractor, the operator, trucking companies and the community, Blackford stresses. “There is a lot of pre-planning that goes into moves to make sure companies have the right permits to put equipment on the road,” he notes.
Rig components also need to arrive in the right order, Blackford advises. “We have seen trucks bring equipment on site that is not needed for several days when the substructure is still sitting on the old location,” he relates. “Ideally, we want the substructure to arrive first and sequence the other components so the crew can start rigging up while equipment is on the way.
“One common time sink is cleaning the mats on which the rig sits,” Blackford adds. “Historically, trucks would show up and pull all the equipment to the side so the mats could be cleaned and moved to the new site. Exposing and cleaning the mats can take a day, so we suggest using two sets of mats that leapfrog each other. One set would be cleaned and installed at the new site ahead of the move, while the current set would be cleaned afterward.”
Optimizing moves can save huge amounts of time, Blackford assures. “For a recent client, we were able to cut the number of days required for each move from five to two and a half,” he says. “Across an entire year, that was enough for the rig to drill an extra well.”
Frontline Power
If companies want to continuously improve rig performance, they should try to keep crews together, Blackford recommends. “So much efficiency comes from crews knowing how to work together and learning from each other,” he explains.
When competition for employees is steep, sustaining crews can be a challenge, Blackford acknowledges. “Equitable pay is just the start,” he says. “If a company wants people to show up ready to work hard and grow, they need to treat workers like people and give them incentives to improve.”
Making metrics more visible to rig crews is vital, Blackford suggests. “For example, at one of the operators I worked for, we added a performance metric board to the site. During the shift change, the crew would discuss how far the well had progressed during the last shift, any issues that shift encountered and what the company would like to accomplish during the coming shift.
“The more crews saw their performance, the more they began taking ownership of it,” Blackford relates. “It’s also important to train crews to spot wasteful activity, encourage them to make suggestions and include them in problem-solving. When crew members know their superiors consider their knowledge and ideas important as the company man’s or the drilling engineer’s, rig performance increases significantly.”
For other great articles about exploration, drilling, completions and production, subscribe to The American Oil & Gas Reporter and bookmark www.aogr.com.