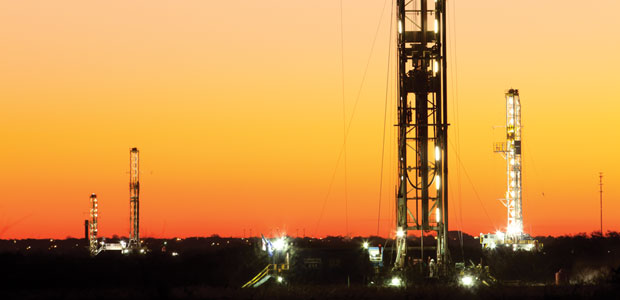
Refracture Optimization
New Wellbore Designs To Incorporate Novel Tools To Boost Recovery Rates
By Kari Johnson, Special Correspondent
Shale wells exhibit very rapid production decline for a number of reasons. Even with a complex fracture network, there is low effective system permeability, and physical deformation can result in excessive loss of fracture conductivity. Early completion and stimulation designs did not optimize reservoir access.
Consequently, thousands of wells in every basin across North America could benefit from refracturing, contends Ibrahim Abou-Sayed, president and owner of i-Stimulation Solutions. Refracturing has the potential to add to both production and reserves, if one of two basic conditions exists, he says. First, some wells were fractured with widely spaced stages, leaving stretches of reservoir untouched.
“Early developments did not have enough perforated intervals,” Abou-Sayed maintains.
Even wells that did have closer spacing may not have opened fractures successfully, he continues. “If insufficient pressure was applied or too many perforations were fractured at once, it is likely that a high percentage of the reservoir was left inaccessible,” he reasons.
In this case, he says, refracturing can be used to connect more reservoir volume to the wellbore.
The second condition for a refrac candidate is a mechanical or geological failure that is causing a loss of connectivity between the well and the reservoir. In this case, Abou Sayed says, refracturing can reconnect the wellbore to the reservoir.
In both cases, he advises, existing production needs to be protected.
Passive Refracturing
One of the interesting effects of downspacing and drilling offset wells is unintentionally stimulating nearby older wells, says Abou-Sayed. Offset well impacts have been seen up to a half mile away, he says, varying by shale play, reservoir quality, and presence of natural fractures. These impacts can both stimulate or damage production.
Operators can improve results if they understand the dynamics within the field and between old and new wells, says Abou-Sayed. “Frac hits are a fact of life for shale plays,” he remarks. “Take advantage of them by putting pressure on existing wells to restimulate rather than taking a negative frac hit.”
He says the resulting uplift can last for a year or more. Hundreds of wells show signs of passive refracturing in the Haynesville and now serve as an analog for refracturing uplift, he adds.
Abou-Sayed says the uplift potential shown through passive refracturing inspired him to study wells for the potential of active refracturing. “It is critical to analyze the potential outcome for each well, both to identify the best candidates and to reduce risk,” he says. “If certain conditions exist and the design is improper, the well can be lost.”
Many factors come into play in evaluating potential refracturing opportunities. Abou-Sayed proposes a disciplined well analysis workflow that reviews in detail the well condition, performance and potential.
During the technical evaluation, Abou-Sayed advises engineers to focus on the weakest link. Sometimes this is the mineralogy. “Clay volume can make a big difference in relative rock hardness, for example,” he mentions.
He says in a strong rock such as the Barnett Shale, the weakest link may be the proppant, which may crush with enough pressure. If the rock is soft, as it is in Haynesville, the weakest link may be rock creep, which accounts for many conductivity issues, he says, adding that rock creep can lead to fracture closure and loss of conductivity.
A thorough risk assessment should be performed. Among the many signs of trouble, Abou-Sayed says, are:
- Scaling;
- Fault proximity;
- Large doglegs;
- Weather induced casing stress;
- Corrosion;
- Carbon dioxide and hydrogen sulfide;
- Pressure on the annuli; and
- Cementing issues.
Well age is another important factor. “There are many cases of new wells that have been stimulated passively, but the effect is small,” Abou-Sayed observes. “Older wells get better results and also present lower risk to existing production.”
Economic Evaluation
Key performance indicators (KPIs) can help identify better refrac candidates, Abou-Sayed says. As shown in Figure 1, the candidate well selection process can be guided by KPIs such as rising cumulative production, initial productivity (IP) and net revenue interest, and falling current rate and present value of estimated net future revenues at an annual discount rate of 10 percent. To these many curves, Abou-Sayed adds the percentage of remaining recoverable hydrocarbons in place. Together, he says, they highlight the subset of wells with the greatest additional production potential.
These wells can be reviewed in light of refracturing cost and an operator’s overall portfolio, Abou-Sayed says. Because they are in production, he adds that it is critical to include delayed production in the calculation. “The goal is to add production and reserves, without risk to existing revenue,” he emphasizes.
He says more monitoring and analysis will contribute to refrac knowledge, enabling engineers to select better candidate wells.
Additional multiwell studies are needed for proof of concept, Abou-Sayed notes. “The potential for refracturing is tremendous, and can be quite rewarding for companies that understand both the forces affecting performance and the relative economic benefit of each well,” he says.
As a case in point, Abou-Sayed offers the Haynesville Shale, where he says he studied 300 wells. “For an independent operator in North Louisiana, we initially selected more than 90 candidate wells, which we slimmed to 60,” he recalls. This was further slimmed, based on economics, safety and potential interference.”
In mid-2014, Abou-Sayed reports, the operator refractured six wells. The first well added 2 billion cubic feet of proved reserves. The operator is evaluating the well performance for further work assessment.
Challenging Conventional Design
Refracs have been performed successfully in every formation type, and in both gas and oil reservoirs, suggests Mike Vincent, an independent consultant who specializes in refrac training.
In his refrac schools, Vincent says he shares the results from refracs in 32 oil-bearing and 28 gas-bearing formations–including sandstones, shales, limestones, diatomites, conglomerates, coals and other rock types–demonstrating that refrac opportunities are not limited to specific formation conditions. However, he cautions, uneconomic refracs also have been performed in almost every reservoir type.
Vincent says his research demonstrates that the reasons to pursue refracs are different in each formation.
“The key to a successful refrac program is to first identify the suspected failure mechanisms and then design a field test structured to confirm and address the problems,” he advises. “Blindly pumping a refrac without trying to learn what was done incorrectly the first time is engineering malpractice.”
Vincent has assessed the results from hundreds of refracs, including more than 300 performed in the Bakken Shale. He reports the Bakken wells have had a wide range of outcomes.
“Some Bakken refracs doubled initial well productivities, while some failed attempts so thoroughly damaged the wells that they subsequently were plugged and abandoned,” Vincent reports. “But there are specific categories of Bakken candidates that have shown more than a 90 percent economic success rate, with every refrac attempt adding in excess of 80,000 barrels of reserves, easily exceeding a 300 percent rate of return on the refrac investment.”
Although calculating incremental reserves shortly after a refrac is challenging, Vincent observes that oil reservoirs provide a unique “tracer” that helps confirm whether new areas of the reservoir are contacted.
“Often, after restimulation, we will see the gas-to-oil ratio drop. This return to the near-original GOR plus pressure data confirms that the refractures reached new areas of the reservoir, and help substantiate the operator’s estimate of incremental reserves” he explains.
Vincent says he also reviewed horizontal refracturing results in the Bakken to identify where economic success was most likely. He says he found that refracturing wells initially fractured with sand had a higher economic success rate than similar wells initially fractured with ceramic proppant. He reasons that durable proppants either have delayed or avoided the need to refrac some wells.
Successful refracs have been performed in a wide range of Bakken well types, including single laterals, multilaterals, cemented, barefoot and uncemented liners. With the enormous range of well configurations in the Bakken, Vincent says he considers it a “refrac playground” with interesting opportunities to learn on each well.
Identify Optimal Treatment
According to Vincent, suspected failure mechanisms should be ranked for candidate wells before designing the refrac treatments. “For example, in some fields there is strong evidence that fractures are ‘salting up,’ or filling with scale or fines,” he reports. “In others, the dominant damage mechanism is the fracture closing near the well. The initial treatment overflushed the sand, and the near-wellbore void has collapsed.”
By understanding the failure mechanism, Vincent says, operators can identify the optimal treatment. “Some wells may be rejuvenated with a tiny refrac because they have a near-wellbore problem,” he attests. “Pumping millions of pounds of proppant would be far more expensive than necessary.”
Vincent illustrates how mechanisms and treatments vary using a series of real-world examples. For one Bakken well completed with millions of pounds of proppant, a refrac containing zero proppant was performed. In this case, the sandless refrac was pumped about 15 months after the well had commenced production. As shown in Figure 2, monthly oil production after refracturing slightly exceeded initial production rates. Few participants in his refrac courses predict that outcome, according to Vincent.
Interestingly, he points out that the production decline rate was virtually the same for both the initial completion and the refrac. Consequently, about 15 months after pumping the refrac (30 months after commencing initial production), the same Bakken well was again refractured using no proppant. The “tri-frac” again improved production, but this time to about 60 percent of IP.
As noted in Figure 2, unusual treatments such as these unpropped jobs can help identify failure mechanisms. Careful evaluation of flowback fluids can determine whether the freshwater injection removed salt or gel residue from the proppant pack, providing key insights that can improve future treatment designs by including salt inhibition or higher concentrations of gel breakers, Vincent says.
Figure 3 shows results after refracturing two Bakken completions that had near-wellbore problems. In both cases, the refracs were performed within the first year of production.
Vincent reports that the refrac treatments pumped less than 10 percent of the proppant mass placed in the original treatments, bull-heading fewer than 100,000 pounds of ceramic proppant into wells originally fractured in 7-10 stages with more than 1 million pounds of sand each.
“These tiny refracs made the wells ‘better than new,’ repairing a near-wellbore issue unrelated to fracture half-length, diversion, or other mechanisms,” he describes.
In a third example, wells initially stimulated with ceramic proppant were restimulated with small sand refracs. Vincent says one refrac was economic, but the other two collapsed within two months of showing encouraging initial production. Even a tri-frac was unable to restore initial productivity, suggesting that bull-heading small-diameter sand into the existing fractures caused permanent damage, he reasons.
“Many curious things have been documented in refracs,” Vincent concludes. “Success depends on careful analysis and testing.”
Failure Mechanisms
In the Bakken, Marcellus, Eagle Ford, Niobrara and other plays where propped fractures have intersected adjacent wells, Vincent reports that pressure communication testing has shown that the created fractures provide insufficient initial conductivity, and progressively collapse or “heal” over time, providing essentially zero hydraulic continuity after six to 24 months.
“The ramifications of fracture collapse are that companies are drilling very closely spaced wells, placing perforation clusters much closer than otherwise needed, and increasingly conducting refracs,” he states.
Vincent says there are myriad conditions that can cause failure, each with its own best resolution. “Determining the failure mechanism is critically important in defining a refracture strategy and ensuring that refracturing is economic,” he says.
He advocates careful analysis and testing prior to beginning a refrac program to determine the best method for each well. “There is no ‘one size fits all’ approach that has yielded the best technical and economic result,” he insists.
“The list of failure mechanisms is long, and cannot be analyzed properly and addressed by a single discipline,” Vincent adds.
Instead, he says he believes multidisciplinary asset teams should analyze candidate wells to hypothesize the key mechanisms, then use field trials to confirm the best approach instead of simply repeating the first successful refrac design.
Although he is adamant that all problems are multidisciplinary, Vincent reluctantly groups fracture collapse mechanisms into three categories: engineering, geology and “unclaimed.” He says each well may suffer from one or more failures in one or more categories. Understanding the failure mechanisms involved in loss of continuity and production decline aids in identifying the best refracturing method. It also can help in predicting the initial and long-term effects of refracturing.
The first category of problems, according to Vincent, arises from the original completion design. It includes proppants, fluids and perforations. These problems are commonly “owned” by the engineering discipline. Proppant-related failures include:
- Insufficient strength and durability, which leads to degradation and fines plugging;
- Thermal degradation of sand-based proppants;
- Overflushing of proppant from the near-wellbore area in transverse fractures;
- Insufficient placement of proppant throughout the network, both lateral and vertical;
- Flowback of proppants from near the wellbore in transverse fracs; and
- Poor contact with pay through losing or wasting proppant out of zone, or poor transport in the first place.
Vincent says cross-linked fluids can lead to occlusion of narrow propped fractures. Gel residue or durable gel filter cakes may completely block narrow fractures. Perforation design also can be the culprit in production decline, Vincent goes on. He says there may be poor alignment with pay zones or too many perforations to allow sufficient diversion. As a result, a high percentage of the lateral may have no associated fractures.
Yet another engineering mechanism for failure is insufficient conductivity for high-velocity hydrocarbon flow, Vincent suggests. He says this results from convergence near the wellbore, especially in liquids-rich formations. The mechanisms cited normally can be identified and addressed solely by an engineering group.
Geology And Responsibility
Sometimes the best explanation for the collapse of propped fractures can be addressed by geology experts, Vincent offers. He says some common problems include:
- Proppant embedment, spalling of the frac face, and rock creep;
- Fluid sensitivity leading to softened formation and clay swelling, which exacerbates embedment and spalling;
- A misplaced lateral that does not land in strata that will accommodate the commonly overflushed completions;
- Precipitation of salt, asphaltenes, barium sulfate and calcium carbonate scales, or migration of formation fines;
- Corrosion, bio-slime, hydrogen sulfide, and carbon dioxide damage;
- Chemical diagenesis of proppant;
- Slippage of frac faces; and
- Pore pressure depletion, subsidence, and compaction that offsets or truncates thin proppant ribbons.
Vincent says the reservoir and surrounding formations must be well understood to diagnose potential problems in the original fracture stimulation, remedy them, and avoid them in the refracturing process. “When engineers design refracs without involving the geology and geophysics team, remediating these issues typically is less than optimal,” he remarks.
The final category of suspected damage mechanisms includes a variety of operational or strategic items that often cannot be attributed to a specific technical “owner.” Vincent says these problems can be more difficult to address because they cross boundaries of responsibility and expertise. Examples include:
- Laterals landed at undesirable depths, or with undulating or undesirable architectures;
- Unrecovered water in portions of the fracture below wellbore elevation;
- Complex fracture geometries that require stronger or more conductive proppant in the turns and pinch points;
- A “factory approach” to completions;
- Aggressive drawdown; and
- A frenetic drilling pace, reducing frac engineers’ role to scheduling without attention to frac durability.
Vincent says these may be the most difficult to avoid in large companies because they are part of “the way things are done.” Investigating and addressing these issues typically requires management involvement, since remedies require compromises among drilling, geology, operations and completions personnel.
Designing The Refrac
“Refracs can improve production and reserves by several mechanisms,” observes Vincent.
He says fracture geometry may be enlarged to increase reservoir contact. Fracture conductivity may be improved by addressing underlying problems such as embedment, cyclic stress, proppant degradation, scaling, salting, and so on.
New fluids and proppants may be used to improve frac-fluid compatibility and re-energize natural fissures, Vincent continues. Stress field alterations may lead to superior containment and reorientation.
In any case, Vincent says, significant engineering effort is required to design the optimal refrac. The approach is not as routine as a daily drilling and completion strategy. Once the potential mechanisms are identified, tests can be performed to narrow the list, he says.
For example, Vincent offers, if a near-wellbore problem is suspected, it can be tested by pumping a very small refrac with a durable, conductive proppant. Success would support the idea that it was a near-wellbore problem. “Otherwise, the results support a diagnosis of problems with the fractures away from the well,” he remarks.
If the problem appears to be a salt mechanism, a hot water wash with freshwater and no new proppant is a good test, Vincent mentions. “Monitoring the salinity of the flowback water will reveal whether salt is, indeed, the problem,” he says, adding that a test process can be devised for every potential damage mechanism.
Although more than 200,000 refracs have been performed over the past 60 years, much remains to be learned about refracturing in unconventional reservoirs, according to Vincent. “The opportunity to increase production and reserves through refracturing is enormous,” he holds.
Figure 4 illustrates how a refrac and subsequent tri-frac incrementally generated higher oil recoveries without adding new stages or perforations. “Although the well produced 400 barrels of oil a day and was highly profitable as initially stimulated, the initial frac job failed to reveal the true potential of the well,” Vincent reveals. “Only after refracturing did the operator recognize that the formation was capable of producing at much higher rates.”
A more conductive refrac design succeeded in doubling daily well productivity to 1,000 barrels of oil. “Most operators would have stopped there and designated this refrac procedure as the new ‘recipe’ and began applying this cookbook to all other wells in the field,” Vincent says. “Luckily, this operator continued experimenting and found an improved design that could again more than double production with a tri-frac, clearly increasing production by more than 1 million barrels of incremental oil. These improved techniques were performed in more than 200 other refracs, tri-, and quad-fracs in the field.”
There also is an opportunity to improve original frac designs by studying refracs, Vincent adds. “In every field we have examined, we know the fractures were not optimized,” he states.
Vincent says he believes the key to improving original fractures is to consider the potential failure mechanisms. “There is something to be learned on each refrac job, and these lessons can be carried back to improve initial frac design,” he concludes. “One key benefit of disciplined refracturing is that it helps us do a better frac job in the first place. Refracs are great, and I love to help clients restimulate old wells. But an even more lucrative outcome is when they discover how to treat the well correctly the first time and avoid the expense of refracturing.”
For other great articles about exploration, drilling, completions and production, subscribe to The American Oil & Gas Reporter and bookmark www.aogr.com.