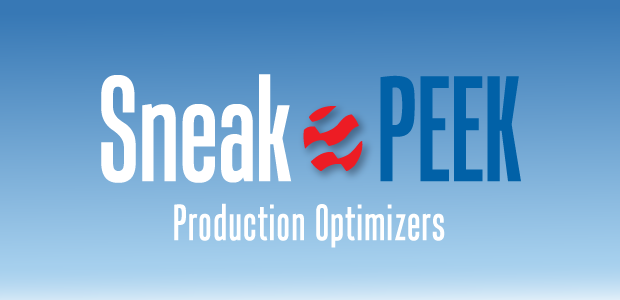
Powerful Automation And Robust Inventions Boost Artificial Lift’s Impact
By Colter Cookson
The right artificial lift system can turn an unremarkable well into a stellar performer or revive a well that would otherwise need to be plugged. For most wells, optimizing lift will deliver significant production increases and cost savings. Extend those improvements across hundreds or thousands of wells, and the cumulative effect can be enormous.
Maximizing each well’s potential is getting easier thanks to innovations that let engineers and pumpers accomplish more with available time, capital and equipment. These innovations range from longer-lasting pumps for high-volume unconventional wells to new concepts that will extend the life of marginal wells.
One of the latest innovations is a multi-well controller. “Flowco Production Solutions has developed a more precise monitoring and control system for gas lift, plunger lift and hybrid-lift methods, capable of overseeing up to 16 wells,” reports Dean Lehner, the company’s director of digital solutions. “Our new single-platform controller brings enhanced computing power, production possibilities and optimization capabilities to either an individual well or a pad of connected assets.
“Optimal control and production of the well is automated and remote,” Lehner continues. “Whether set points are manually specified by the operator or automated with AI algorithms in the controller, the operator has the flexibility to tune each artificial lift platform for peak performance.”
To guide its decisions, Lehner says the controller applies either a patented GAPL (Gas-Assisted Plunger Lift) algorithm or advanced gas lift optimization software. This new gas lift optimization protocol allows the operator to control the gas lift injection rate autonomously based on a user-selected critical rate or based on live data from a downhole gauge, Lehner describes.
Lehner adds that the controller’s algorithms for GAPL/PAGL include cycle skip technology. He says this capability helps them manage both gas injection and plunger cycles to get the best performance out of independent plunger or gas lift systems—or both systems simultaneously.
“The system has the capability to optimize each well regardless of lift platform,” Lehner emphasizes. “For example, the controller can optimize gas injection on a GAPL well based on plunger velocity and simultaneously optimize a second gas lift well based on critical velocity of production on the same pad.”
He adds, “The software optimizes gas injection volume and plunger cycle settings. The provided automation frees up a significant amount of productive time for the engineer or field tech to attend to other critical tasks.”
The algorithm’s results can be impressive, Lehner says. “We cannot create production in reservoirs with little to give, but we can help a well deliver the available production at the optimum rate,” he explains. “The uplift varies, but for an operator who goes from manual control to automation, it’s realistic to see a 20%-30% increase in production and a 20% decrease in injected gas volume.”
CAPEX Savings
Lehner points out that many production engineers prefer to manage wells manually until they become comfortable with the controller’s recommendations. “The controller supports everything from completely manual operation—where it merely takes input variables, does calculations, and then outputs the numbers for somebody to look at—to fully automated control where all the user needs to do is set the target rate. At that point, the controller will find the rate quickly by making changes without any user input.
“The system not only saves time but can provide significant savings in CAPEX. Multi-well pads would normally require putting a controller on each wellhead,” he says. “Instead, we install the new controller on one well and install expanders on the other wells. These expanders are smaller scale devices that take all the information needed to control the well and transmit it to the master.”
Flowco Production Solutions’ new multi-well controller has the computing power to manage as many as 16 wells that are on gas lift, gas-assisted plunger lift or plunger-assisted gas lift. According to the company, the controller’s proprietary algorithms optimize gas injection rates, plunger cycles and other variables to maximize each well’s performance.
The capital savings this approach provides can be significant, Lehner reports. “On a four-well pad, going from one controller for each well to one controller and three expanders can save around 30% on hardware alone,” he illustrates. “The expanders are less expensive because they only need the processing power and inputs to take care of a single well. The master has a stronger processor, more robust inputs and a user-friendly display.”
The expanders can connect to the master through serialized wires, but Lehner says he usually recommends going wireless. “With fewer wires to install, less crimping, and fewer cable trays, we can minimize the amount of work required to get the system up and running,” he explains. “If communication with the master is interrupted, the expanders operate their wells independently until communication resumes, at which point they update the master. There is no loss of automation or production optimization.”
Even in its fully automated mode, the device can prompt users to intervene if parameters fall outside a specified band, Lehner mentions. “As the controller proves itself, most companies move to automation because they can see the benefits of better production, lower injection gas rates, and ability to track the reservoir performance as well as the current fluid-level,” he remarks.
The multi-well controller works with most major proprietary and retail SCADA packages, Lehner assures. He says the computing capabilities it brings to the well site deliver value throughout the well life cycle.
According to Lehner, the controller’s benefits can be magnified by pairing it with downhole temperature and pressure gauges. “Having that downhole information lets the controller see exactly what is happening at the various points where gas enters the well and track the reservoir performance as well as the current fluid level precisely,” he explains. “This gives it faster and more detailed feedback on how the well is responding to changes at the surface, as well as the potential to react to leakage, skin damage and other problems before they show up in surface data.”
Noting that Flowco develops the associated technology in house, Lehner says the gauges have become extremely robust. “We have installed thousands of gauges with a success rate of 98.75%, meaning the gauges operate continuously with no loss of data,” he details. “That exceptional reliability is giving more people the comfort to invest in real-time downhole data that will help them optimize their wells’ production and costs.”
Versatile ESPs
Electric submersible pumps have come a long way in a short time, observes Juan Fernandez, who oversees application engineering in the Permian Basin for UNBRIDLED® ESP Systems, ChampionX’s ESP business unit. “In 2010, most Permian Basin operators would pull ESPs and move to another form of artificial lift once the flow rate dropped to 400 or 500 barrels,” he recalls. “Today, many operators continue running ESPs down to 200 or 300 barrels a day.”
To improve electric submersible pumps’ longevity and versatility, ChampionX reports it has developed a pump design that reduces the pressure drop from one stage to another. In addition to helping with gas handling, an especially important benefit at low flow rates, the lower pressure drop frequently allows ESPs to deliver the necessary lift with fewer sections.
Fernandez and Michael Rumbaugh, the company’s ESP product line manager, attribute that shift largely to technological advances that aim to mitigate challenges ESPs encounter in unconventional plays. These advances include a 4.20-inch motor that can produce as much power as one with an outer diameter of 4.56 inches.
“Because of the high pressures in the lateral during hydraulic fracturing, many operators have moved to 20- and 23-pound casing with an outer diameter of 5½-inches. A traditional 4.56 motor needs to be modified to fit inside the casing, and even then, it can get stuck,” Rumbaugh says. “Operators can mitigate that risk by running three or four 3.75-inch motors, but that involves so many connections it makes the motors notoriously unreliable.
“To power the ESP with a smaller footprint, we started with a blank slate and asked how we could design a motor for tight casing in unconventional plays,” he relates. “Using finite element analysis and modern computing power, we came up with a single-motor package that can deliver the necessary lift without getting stuck.”
The compact motor proved so successful that Fernandez says it now accounts for more than half of the company’s Permian Basin installations. “The motor’s smaller OD means there is more annular space. This slows the fluid speed, which improves gas handling and reduces erosion,” he says.
Noting that gas tends to become more problematic as the flow rate drops, Fernandez says ChampionX has extended pumps’ operating ranges by redesigning their stages. “In all ESPs, each stage has a diffuser, which is stationary, and an impeller, which rotates with the shaft,” he notes. “In a normal pump, as the fluid transitions from the diffuser to the impeller, it enters a dead zone that causes pressure to drop and allows gas to escape from the liquid.
“The new design eliminates or minimizes the dead zone by optimizing the vane’s placement and shape,” Fernandez describes. “This shrinks the pressure drop between stages, which keeps gas in the fluid and allows each stage to lift more fluid.”
“The improvement in gas handling can be significant,” Rumbaugh says. “In fact, one of our pumps has centrifugal stages that can handle up to 52% free gas.”
The new design’s extra lift means the pump needs fewer stages, Fernandez reports. As a rule of thumb, he says it only takes three to handle the work traditionally done by four. “That makes the ESP shorter, which could let the operator land the pump in the tangent section, where it is closer to the production,” he says.
Rumbaugh adds that in some applications, the lower stage count can reduce horsepower requirements and power consumption. He mentions that ESPs can introduce harmonics into the power grid that reduce its capacity, overheat equipment and create other headaches for utility companies. If harmonics get too extreme, utilities can issue fines or cut off power.
“We have developed a harmonic halter to purify the power the variable frequency drive sends back into the grid. It works so well that the power meets the Institute of Electric and Electronics Engineers’ harmonics standard, IEEE 519,” he says. “We designed it for unconventional plays, so unlike traditional harmonic systems, which work best at particular loads, the halter stays effective even when loads fall to 15%. This lets the operator manage harmonics as production declines without changing equipment.”
Electricity-Free Automation
Optimizing rod pumps using a pump-off controller and a VFD has proven time and again to increase production, extend rod life and reduce workover costs, observes Gord Abram, co-founder of Variable Speed Hydraulics Inc. Because VFDs require electricity, he continues, these benefits have been available only at sites with access to electricity from the grid or enough power consumption to justify running a generator.
With a hydraulic variable speed drive, operators can use pump-off controllers on sites that lack the electricity required to power a variable frequency drive. Variable Speed Hydraulics says the production gains and cost savings from the pump-off controller can be augmented by using the same drive to run a casing gas compressor.
Through a happy accident, Abram says he and VSH co-founder Everett Haarstad developed a hydraulic variable speed drive that could bring pump-off controllers to all sites. After years of working as a pumper and production foreman, Abram was searching for a more reliable belt guard when Haarstad, a farmer with extensive experience with hydraulic equipment, suggested replacing the belt with a hydraulically-powered chain.
“We never managed to make the chain work, but we realized that in the process of trying, we had created a variable speed drive for natural gas engines,” Abram recounts. “That is so much bigger, because it means pump-off controllers can manage the pump even in areas with no electricity. All they need is an engine and field gas.”
In most applications, Abram says there is excess gas in the annulus that can be optimized with a casing gas compressor. “As the compressor runs, it relieves pressure on the formation, allowing more emulsions to flow into the pump,” he points out. “That will cause the pump-off controller to accelerate the jack and bring more production to surface.”
By itself, a casing gas compressor has the potential to increase production up to 60%, Abram reports. Enabling pump-off control will not affect production as dramatically, but reducing fluid pound and other wear and tear on equipment can deliver substantial savings. Add those benefits together, and the system generally will pay for itself in less than a year, he estimates.
Abram emphasizes that the hydraulic drive differs from past attempts to run pumpjacks with hydraulics. “Most of those involved replacing a traditional pumpjack with a hydraulic system that could lift the rod out of the well, which can require 15,000 or 20,000 pounds of pressure and a huge oil reservoir,” he says. “To turn an existing pumpjack, we only need 1,800-2,500 psi.”
According to Abram, that approach translates into safe and reliable operations. “The system comes with a small maintenance manual, but other than changing the hydraulic filter and lubricating oil after the initial break-in, little needs to be done. The tank that holds the oil is sealed, so it should be able to circulate forever without contamination.”
In recent field testing, the system ran for 625 days without any issues, he reports. So far, 12 systems have been deployed in Canada and Texas. “We have had the odd oil-cooling fan failure, but that is an easy fix. All the operator needs to do is pop a clip out to remove the old fan and plug the new one in,” he says.
For wells with easy access to power, Abram recommends using a VFD because electric motors require less maintenance than natural gas engines. However, the hydraulic drive excels in locations where running power is impossible or impractical, he advises. “Bringing out a natural gas engine and our hydraulic drive is much more convenient and environmentally friendly than negotiating with landowners and clear-cutting brush to run power polls,” he comments.
“Not every well needs a VSH system, but every producer has at least one remote or otherwise inaccessible well in their inventory that would benefit from one,” he assesses.
Pneumatic Pump
When Gary J. Sommese was asked to lead development of an air-powered pump for water wells in Bangladesh, he recalls jumping at the opportunity. The team created a low-cost pump that could bring water to the surface or move it over a mountain, as well as an air-generating windmill. “The windmill worked at speeds as low as seven miles an hour, and we envisioned storing air in propane tanks to pump water even on windless days,” he says.
After the project stalled, Sommese began selling the pump for other uses. A few years after its invention, he had the good fortune to meet someone in Morris, Ok., who asked if the pump could be repurposed to lift oil.
Air Lift Technology describes its pneumatic pump as a low-cost way to boost production from stripper wells, including ones with holes in the casing or crooked sections. Since it is made from stainless steel, only contains one moving part, and automatically adjusts to the well’s production, the pump requires almost no maintenance or attention.
“My company, Air Lift Technology, recently received a letter from an operator in Texas who has been using the pump on 65 oil wells,” he reports. “Before adopting the pump, the operator had to shut in the wells an average of every 10 months because of tubing holes. Today, those wells have gone four years without any maintenance.”
To explain the pump’s reliability, Sommese points out that it is made from 316 stainless steel and has only one moving part, a float switch inside the pump. “When the pump is full of fluid, this float switch rises, shutting the exhaust port and opening the air-in pin. As air enters the pump, it pushes the fluid to the bottom into a pick-up tube, which takes the fluid through a check valve to the next pump, or if the well is shallow, the surface.”
Three stands of polyethylene pipe connect each stage: a red pipe that brings in air, a blue pipe that allows air to return to the surface, and a black pipe that transports the fluid, Sommese describes. “All the air that goes into the pump to displace the fluid vents back out, so none gets mixed with the formation,” he assures. “Because everything is self-contained, the system does not care if the casing has holes or the well is crooked.
“One of the best things about the pump is that it is self-regulating,” he continues. “Until the bottom stage is completely full of fluid, the pump is in standby mode and does not waste any air. Since the pump only moves fluid when it needs to, there is no need to install a time clock or try to guess how frequently a pumpjack should turn on. Almost every operator who installs the pump sees production increase 10%-30%.”
How much fluid the system can move depends on depth. “In our deepest well, which is at 1,850 feet, we move 125 barrels a day. In Oil City, La., we have a shallower pump moving 300 barrels of fluid,” he illustrates.
Sommese describes pump installation as easy. An oil field winch truck with a quarter-inch stainless steel cable lowers the stages into the well, with each stage about 250 feet apart. The air compressors can be powered by electric motors, or if the well is off grid, natural gas. The pump runs at 125 psi, low enough that Sommese says one of his Texas customers manages 30 wells with a single compressor.
The payback period varies with production, Sommese notes. “For customers in Pennsylvania who make six barrels a day of straight oil, the system pays for itself in a few months. For the ones in Oil City, La., that move 300 barrels a day to get a half a barrel of oil, it’s 16-18 months.”
Addressing Methane
Instead of mobilizing the fluid with air, the pump can be set up to use methane, Sommese reports. “We are doing that on federal land in Osage County, Ok.,” he says. “The system reuses the same gas over and over, so once it is charged, it does not take any production.”
As a closed-loop system, the pump does not allow any methane to escape at the well site, Sommese says. “When we mentioned that we had achieved zero emissions at a meeting with the Osage Mineral Council, some professors from the University of Tulsa’s petroleum engineering department asked if they could get involved. We love working with them,” he says.
“They have set up a test tower and are studying how to increase the pump’s depth,” he shares. “In applications where we use gas from the well rather than air, we plan to periodically inject gas into the fluid pipe to provide extra lift. We think that will let us double the space between stages to 500 feet, which should reduce costs, and increase the system’s maximum depth to 4,000 feet.”
The pump already is sufficiently economic that Sommese says a few customers are taking ownership of abandoned wells and installing the pump to revive them. For example, NovaTech Energy (which he helped found and serves as chief technology officer) has brought several wells back on line in Louisiana. Another operator is partnering with NovaTech to do so in Texas, Sommese relates.
“It takes research to make sure the abandoned well can still produce,” he allows. “When it can, installing the pump is a true win. For a cost comparable to a plugging operation, we can stop the well from venting methane into the atmosphere while bringing it back into service.”
For other great articles about exploration, drilling, completions and production, subscribe to The American Oil & Gas Reporter and bookmark www.aogr.com.